Military PCB Manufacturer
Military PCB Manufacturer,Military PCBs, or Military-Grade Printed Circuit Boards, are engineered to meet the rigorous demands of military applications. Designed with a focus on reliability, durability, and performance, these specialized circuit boards are built to withstand harsh environmental conditions encountered in military operations. Constructed using high-quality materials such as high-grade epoxy laminates, ceramic substrates, and high-temperature laminates, military PCBs offer superior mechanical strength and thermal stability. Advanced manufacturing processes and stringent quality control measures ensure that each PCB meets the exacting standards of military specifications and standards. From communication systems and radar systems to weapons systems and unmanned vehicles, military PCBs play a critical role in the development of robust and resilient electronic systems used in defense and aerospace applications. With features like high reliability, rugged construction, and compatibility with military standards, military PCBs provide the foundation for mission-critical equipment designed to operate flawlessly in challenging environments.
What is a Military PCB?
A Military PCB (Printed Circuit Board) refers to a circuit board specifically designed and manufactured to meet the stringent requirements of military applications. These PCBs are constructed with materials and processes that ensure high reliability, durability, and performance in harsh environments typically encountered in military operations.
Key features of military PCBs include:
- High Reliability:Military PCBs are built to withstand extreme temperatures, humidity, shock, and vibration, ensuring reliable operation in challenging conditions.
- Rugged Construction:They often use materials such as high-grade epoxy laminates or ceramic substrates that offer superior mechanical strength and resistance to environmental stressors.
- Stringent Quality Standards:Military PCBs undergo rigorous testing and adhere to strict quality standards to ensure consistent performance and reliability under demanding circumstances.
- Advanced Technology:Military PCBs may incorporate advanced technologies such as multilayer construction, high-density interconnects, and embedded components to optimize performance while minimizing size and weight.
- Security: Military PCBs may incorporate features to enhance security, such as tamper-proof designs, encryption capabilities, and protection against electromagnetic interference (EMI) and radio frequency interference (RFI).
Overall, military PCBs play a crucial role in the development of robust and resilient electronic systems used in military equipment, including communication systems, radar systems, weapons systems, and unmanned vehicles.
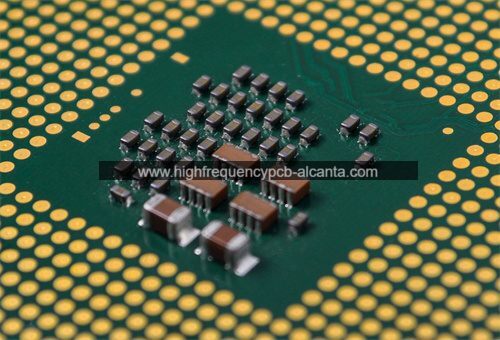
Military PCB Manufacturer
What are Military PCB Design Guidelines?
Military PCB design guidelines are specific recommendations and requirements for designing printed circuit boards (PCBs) intended for military applications. These guidelines aim to ensure that the PCBs meet the high standards of reliability, durability, and performance necessary for use in military equipment. Some common military PCB design guidelines include:
- Reliability and Durability:Military PCBs must be designed to withstand harsh environmental conditions, including extreme temperatures, humidity, shock, and vibration. Designers should select materials and components with proven reliability and durability ratings.
- Component Selection:Use components that meet military-grade specifications and have undergone rigorous testing for reliability and performance. Components should have wide operating temperature ranges and be resistant to environmental factors such as moisture and corrosion.
- Signal Integrity:Ensure proper signal integrity by minimizing signal distortion, noise, and crosstalk. Use controlled impedance traces for high-speed signal paths to maintain signal integrity and reduce electromagnetic interference (EMI).
- Power Distribution:Design robust power distribution networks to ensure stable and reliable power supply to all components, even under varying loads and environmental conditions. Employ techniques such as power plane design, bypass capacitors, and voltage regulation to minimize voltage fluctuations and noise.
- Thermal Management:Implement effective thermal management techniques to dissipate heat generated by components and ensure proper operating temperatures. Use thermal vias, heat sinks, and strategically placed components to facilitate heat transfer and prevent overheating.
- Mechanical Considerations:Consider mechanical factors such as board size, shape, and mounting requirements to ensure compatibility with the intended enclosure and mechanical assembly. Design the PCB to withstand mechanical stress and facilitate ease of assembly and maintenance.
- EMI/RFI Shielding:Incorporate shielding techniques to mitigate electromagnetic interference (EMI) and radio frequency interference (RFI) that could degrade performance or compromise security. Use shielding materials and techniques to contain emissions and protect sensitive components from external interference.
- Testing and Verification:Implement comprehensive testing and verification procedures throughout the design process to ensure that the PCB meets all performance and reliability requirements. Conduct environmental testing, reliability testing, and functional testing to validate the design under simulated operating conditions.
By adhering to these military PCB design guidelines, designers can develop PCBs that meet the stringent requirements of military applications, ensuring reliable performance in demanding environments.
What is the Military PCB Fabrication Process?
The military PCB fabrication process is similar to standard PCB fabrication but with additional steps and considerations to meet the stringent requirements of military applications. Here is an overview of the typical military PCB fabrication process:
- Design:The process begins with the design of the PCB using specialized software. Designers follow military PCB design guidelines to ensure the PCB meets the required specifications for reliability, durability, and performance.
- Material Selection:Military PCBs require high-quality materials that can withstand harsh environmental conditions. Common materials include high-grade epoxy laminates, ceramic substrates, and high-temperature laminates. These materials offer superior mechanical strength, thermal conductivity, and resistance to moisture and corrosion.
- Preparation of Substrates:The chosen substrate material is prepared by cutting it to the required size and shape. For multilayer PCBs, multiple substrate layers may be prepared and stacked together.
- Layer Preparation: The PCB design is divided into individual layers, each containing traces, pads, and vias. Copper foil is bonded to each substrate layer, and a photoresist layer is applied on top.
- Photo Imaging:A photomask, which contains the pattern of the circuit traces and features, is placed over the photoresist layer. The PCB is then exposed to UV light, which transfers the pattern onto the photoresist.
- Etching:The exposed areas of the copper foil are chemically etched away, leaving behind the desired circuit traces and features on each layer.
- Drilling:Holes for through-hole components and vias are drilled into the substrate layers using precision drilling machines. Laser drilling may be used for high-density PCBs.
- Plating:A thin layer of metal, typically copper, is plated onto the walls of the drilled holes to create electrical connections between layers.
- Lamination:The individual substrate layers are stacked together and laminated under heat and pressure to form a multilayer PCB. Adhesive layers may be used to bond the layers together.
- Surface Finishing:Surface finishing processes such as HASL (Hot Air Solder Leveling), ENIG (Electroless Nickel Immersion Gold), or immersion silver are applied to protect the exposed copper surfaces and facilitate soldering.
- Solder Mask Application:A solder mask is applied over the entire PCB surface, leaving only the pads and vias exposed for soldering. The solder mask provides insulation and protects the copper traces from environmental damage.
- Silkscreen Printing: Component designators, logos, and other identifying information are printed onto the PCB surface using a silkscreen printing process.
- Testing: The finished PCB undergoes comprehensive testing to ensure it meets all performance and reliability requirements. This may include electrical testing, impedance testing, and environmental testing.
- Quality Assurance:The PCB is inspected for defects and inconsistencies, and any necessary corrections are made before final approval.
- Packaging and Shipping:Once the PCB passes all inspections and testing, it is packaged according to military standards and shipped to the customer for use in military equipment.
Throughout the entire military PCB fabrication process, strict quality control measures are implemented to ensure the final product meets the high standards of reliability, durability, and performance required for military applications. Additionally, documentation and traceability are maintained to comply with military regulations and standards.
How do you manufacture a Military PCB?
Manufacturing a military PCB involves a series of steps tailored to meet the stringent requirements of military applications. Here’s an overview of the manufacturing process:
- Design Verification and Validation:Before manufacturing begins, the PCB design undergoes thorough verification and validation to ensure it meets the specifications and requirements of the military application. This includes design reviews, simulations, and prototyping.
- Material Selection:High-quality materials are crucial for military PCBs. The selection process involves choosing substrates, copper foils, solder masks, and surface finishes that offer superior reliability, durability, and performance in harsh environments. Materials must meet military standards and specifications.
- Panelization:PCB layouts are arranged in panels to optimize material usage and manufacturing efficiency. Panelization involves arranging multiple PCBs on a larger panel, allowing them to be processed simultaneously during fabrication.
- Lamination:For multilayer PCBs, individual substrate layers are stacked together with prepreg layers and bonded using heat and pressure in a lamination press. This process creates a single, solid structure with alternating layers of copper and substrate.
- Drilling: Precision drilling machines are used to drill holes for through-hole components and vias. Laser drilling may be employed for high-density PCBs or microvias.
- Plating:After drilling, the holes are plated with a thin layer of conductive metal, typically copper, to establish electrical connections between layers. Plating also reinforces the hole walls, ensuring mechanical strength and reliability.
- Etching:Copper foils on outer layers are etched to define the circuit traces and features using chemical etchants. Photolithography techniques are employed to transfer the PCB design onto the copper surface accurately.
- Surface Finishing:Surface finishing processes are applied to protect exposed copper surfaces, enhance solderability, and improve reliability. Common surface finishes for military PCBs include HASL (Hot Air Solder Leveling), ENIG (Electroless Nickel Immersion Gold), and immersion silver.
- Solder Mask Application:A solder mask is applied over the entire PCB surface, leaving only the pads and vias exposed for soldering. The solder mask provides insulation, protection against environmental factors, and facilitates soldering during assembly.
- Silkscreen Printing:Component designators, logos, and other identifying information are printed onto the PCB surface using silkscreen printing. This information aids in component placement and assembly.
- Testing and Inspection:The manufactured PCBs undergo rigorous testing and inspection to ensure they meet all performance and reliability requirements. This includes electrical testing, impedance testing, solderability testing, and visual inspection for defects.
- Quality Assurance:Throughout the manufacturing process, strict quality control measures are implemented to identify and address any issues promptly. Quality assurance procedures ensure that the final product meets the high standards of reliability and performance required for military applications.
- Packaging and Shipping:Once the PCBs pass all inspections and testing, they are packaged according to military standards and shipped to the customer for integration into military equipment.
By following these manufacturing steps and adhering to military standards and specifications, manufacturers can produce high-quality PCBs suitable for use in military applications, ensuring reliability, durability, and performance in demanding environments.
How much should a Military PCB cost?
The cost of a military PCB can vary significantly depending on various factors such as complexity, size, materials used, quantity ordered, and the specific requirements of the military application. Military-grade PCBs typically have higher costs compared to commercial-grade PCBs due to the need for superior reliability, durability, and performance in harsh environments.
Here are some factors that can influence the cost of a military PCB:
- Complexity:PCBs with intricate designs, high component density, and advanced features such as multilayer construction, high-speed signaling, and embedded components will typically cost more to manufacture.
- Materials:Military PCBs require high-quality materials that meet stringent military standards and specifications. Specialized materials such as high-grade epoxy laminates, ceramic substrates, and high-temperature laminates can increase manufacturing costs.
- Manufacturing Processes:Certain manufacturing processes, such as laser drilling, controlled impedance routing, and surface finishing techniques like ENIG (Electroless Nickel Immersion Gold), can add to the overall cost of production.
- Testing and Certification:Military PCBs undergo rigorous testing and certification processes to ensure compliance with military standards and specifications. Testing procedures such as environmental testing, reliability testing, and functional testing can contribute to the cost.
- Volume:The quantity of PCBs ordered can impact the unit cost. Larger production runs typically result in lower unit costs due to economies of scale, whereas smaller quantities may incur higher per-unit costs.
- Lead Time:Expedited manufacturing or delivery timelines may come with additional costs to prioritize production and meet tight deadlines.
- Supplier Selection: The choice of PCB manufacturer or supplier can also affect the cost. Suppliers with specialized expertise in military-grade PCBs may charge higher prices for their services.
Given the wide range of factors influencing the cost of military PCBs, it’s challenging to provide a specific price without detailed information about the PCB specifications and manufacturing requirements. For accurate pricing, it’s advisable to consult with reputable PCB manufacturers or suppliers who specialize in military-grade PCBs and provide quotes based on the specific project needs. Additionally, factors such as long-term reliability, performance, and compliance with military standards should be prioritized over cost considerations when sourcing military PCBs.
What is Military PCB base material?
The choice of base material for military PCBs is critical for ensuring reliability, durability, and performance in harsh environments typical of military applications. Several materials are commonly used as the base substrate for military PCBs, each offering unique properties suited to specific requirements. Some of the primary materials include:
- FR-4 (Flame Retardant 4):FR-4 is a widely used epoxy-based laminate material composed of woven fiberglass cloth impregnated with epoxy resin. It offers good mechanical strength, dimensional stability, and electrical insulation properties. FR-4 is cost-effective and suitable for many military applications.
- High-Temperature Laminates:Military PCBs operating in high-temperature environments may require specialized laminates capable of withstanding elevated temperatures without degrading. High-temperature laminates, such as polyimide (PI) or PTFE (polytetrafluoroethylene), offer excellent thermal stability and reliability.
- Ceramic Substrates:Ceramic substrates, such as aluminum oxide (Al2O3) or aluminum nitride (AlN), are ideal for military PCBs requiring superior thermal conductivity, high-frequency performance, and resistance to thermal cycling. Ceramic substrates are commonly used in high-power and RF/microwave applications.
- Metal Core PCBs (MCPCBs):Metal core PCBs feature a metal base layer, typically aluminum or copper, with a dielectric layer and copper circuit layers bonded on top. MCPCBs offer enhanced thermal management capabilities, making them suitable for military applications requiring efficient heat dissipation.
- Flex and Rigid-Flex PCBs:Flex and rigid-flex PCBs are used in military applications where flexibility, space-saving, and reliability are essential. They feature flexible substrates composed of polyimide or polyester materials, providing durability and resistance to bending and vibration.
When selecting the base material for military PCBs, considerations such as operating environment, temperature range, electrical performance, mechanical requirements, and cost must be taken into account. Additionally, military specifications and standards may dictate specific material requirements to ensure compliance and reliability. Overall, choosing the appropriate base material is crucial for achieving the desired performance and longevity of military PCBs in demanding applications.
Which company makes Military PCB?
There are many companies specializing in the production of military PCBs (Printed Circuit Boards), some of which offer high-quality and reliable products to meet the stringent requirements of military applications. Some well-known companies include DuPont, Rogers Corporation, TTM Technologies in North America, as well as Epec Engineered Technologies, AT&S in Europe. These companies typically have advanced manufacturing equipment, extensive experience, and professional teams to provide high-performance PCB products that meet military standards.
At our company, we also have the capability to manufacture military PCBs. We employ advanced manufacturing technologies and strict quality control processes to ensure that our products meet the requirements of military applications. With a professional engineering team, we can design and manufacture PCBs that meet military standards according to customer requirements. Our production facilities are equipped with advanced equipment, including automated production lines, precision drilling machines, plating lines, automated testing equipment, etc., to meet the high-quality and high-demand requirements of PCB manufacturing.
Our military PCB products have the following features and advantages:
- Reliability and Stability:We use high-quality base materials and components to ensure the reliability and stability of our products in harsh environments, capable of withstanding extreme temperatures, humidity, vibrations, and other conditions.
- High Performance:We employ advanced manufacturing processes and technologies to provide high-performance PCB products that meet the requirements of military equipment for signal transmission, power management, thermal management, etc.
- Compliance with Military Standards:Our products comply with international military standards and specifications, such as IPC-A-600, IPC-6012, MIL-PRF-31032, etc., ensuring product quality and reliability.
- Customized Services:We can customize PCB products according to customer’s specific requirements, including design, manufacturing, testing, etc., providing customers with comprehensive solutions.
- Fast Delivery:With efficient production capacity and flexible production scheduling, we can deliver customer orders promptly to meet urgent customer needs.
As a professional PCB manufacturer, we are committed to providing customers with high-quality, reliable products and services to meet their needs in military applications. We will continue to improve and enhance our production capacity and technical level to provide better support and services to our customers.
What are the qualities of good customer service?
Good customer service is characterized by several qualities that contribute to positive experiences for customers and foster long-term relationships. Some key qualities of good customer service include:
- Empathy:Empathizing with customers and understanding their needs, concerns, and emotions is crucial for providing personalized and effective assistance. Empathetic customer service representatives listen actively, show genuine concern, and strive to address customers’ issues with sensitivity.
- Responsiveness:Promptly addressing customer inquiries, requests, and issues demonstrates a commitment to providing timely assistance. Quick response times, whether through phone, email, chat, or social media, help customers feel valued and respected.
- Clarity and Communication:Communicating clearly and effectively is essential for ensuring customers understand the information, instructions, or solutions provided. Using simple language, avoiding jargon, and providing relevant details help prevent misunderstandings and confusion.
- Knowledge and Expertise:Having a deep understanding of products, services, policies, and procedures enables customer service representatives to provide accurate information and guidance. Knowledgeable staff can answer questions, troubleshoot problems, and offer solutions efficiently, building trust and confidence with customers.
- Professionalism:Maintaining professionalism in interactions with customers involves being courteous, respectful, and patient, even in challenging situations. Professional behavior instills confidence in customers and reflects positively on the company’s reputation.
- Problem-Solving Skills:Effective problem-solving skills enable customer service representatives to identify issues, analyze root causes, and propose solutions that meet customers’ needs. Being proactive, resourceful, and creative in resolving problems fosters customer satisfaction and loyalty.
- Flexibility and Adaptability: Adapting to customers’ preferences, changing circumstances, and unexpected challenges demonstrates flexibility and a commitment to meeting customer needs. Being adaptable allows for personalized service and customized solutions tailored to individual situations.
- Follow-Up and Accountability:Following up with customers to ensure their issues have been resolved and their needs have been met shows attentiveness and accountability. Following through on commitments and taking ownership of customer concerns reinforces trust and reliability.
- Positive Attitude:Maintaining a positive and upbeat attitude during interactions with customers helps create a welcoming and enjoyable experience. A positive attitude can uplift customers, diffuse tense situations, and leave a lasting impression.
- Continuous Improvement:Striving for continuous improvement in customer service processes, policies, and practices demonstrates a commitment to delivering excellence. Soliciting feedback from customers, monitoring performance metrics, and implementing changes based on insights contribute to ongoing enhancement of the customer experience.
By embodying these qualities, organizations can cultivate a customer-centric culture and build strong relationships with customers, leading to increased satisfaction, loyalty, and advocacy.
FAQs
What are military PCBs?
Military PCBs, or Military-Grade Printed Circuit Boards, are circuit boards specifically designed and manufactured to meet the stringent requirements of military applications. They are built to withstand extreme conditions such as temperature variations, humidity, shock, and vibration, while maintaining high reliability and performance.
What makes military PCBs different from commercial PCBs?
Military PCBs are designed and manufactured to higher standards of reliability, durability, and performance compared to commercial PCBs. They undergo rigorous testing and adhere to strict military specifications and standards to ensure suitability for use in military equipment and systems.
What are the key features of military PCBs?
Key features of military PCBs include high reliability, rugged construction, stringent quality standards, advanced technology, security features, and compatibility with military specifications and standards.
What are some common applications of military PCBs?
Military PCBs are used in various military equipment and systems, including communication systems, radar systems, weapons systems, navigation systems, surveillance systems, unmanned vehicles, and electronic warfare systems.
What materials are used in military PCBs?
Military PCBs are typically constructed using high-quality materials such as high-grade epoxy laminates, ceramic substrates, and high-temperature laminates. These materials offer superior mechanical strength, thermal stability, and resistance to environmental stressors.
What are the design guidelines for military PCBs?
Military PCB design guidelines include considerations for reliability, durability, signal integrity, power distribution, thermal management, mechanical considerations, EMI/RFI shielding, testing, and verification. These guidelines ensure that the PCBs meet the high standards required for military applications.
How are military PCBs manufactured?
The manufacturing process for military PCBs involves steps such as design verification, material selection, panelization, lamination, drilling, plating, etching, surface finishing, solder mask application, silkscreen printing, testing, inspection, quality assurance, packaging, and shipping. Specialized equipment and processes are used to meet military specifications and standards.
What are the benefits of using military PCBs?
The benefits of using military PCBs include high reliability, durability, and performance in harsh environments, compatibility with military standards and specifications, long-term reliability and stability, and enhanced security features.