Military Circuit Board Manufacturer
Military Circuit Board Manufacturer,Military Circuit Boards (MCBs) are specialized electronic components engineered to withstand the extreme conditions and demanding environments encountered in military operations. These circuit boards are meticulously designed and manufactured to meet stringent military standards, ensuring unparalleled reliability and performance.
MCBs are constructed using high-quality materials and advanced manufacturing techniques to endure harsh temperatures, vibrations, humidity, and electromagnetic interference (EMI). They are engineered to provide robust electrical connections, precise signal transmission, and optimal thermal management, critical for the operation of military equipment such as aircraft, vehicles, communication systems, radar systems, and weapons platforms.
Each MCB undergoes rigorous testing and qualification processes to ensure adherence to military specifications and standards, including MIL-STD-810 and MIL-STD-461. These tests evaluate the MCB’s ability to withstand environmental stressors, maintain functionality under extreme conditions, and comply with electromagnetic compatibility requirements.
With their unparalleled durability, reliability, and performance, Military Circuit Boards play a vital role in enhancing the effectiveness, safety, and mission success of military operations around the world.
What is a Military Circuit Board (MCB)?
A Military Circuit Board (MCB) is a type of circuit board specifically designed and manufactured to meet the stringent requirements of military applications. These circuit boards are built to withstand harsh environmental conditions, extreme temperatures, high levels of vibration, and electromagnetic interference (EMI), which are common in military operations.
MCBs typically undergo rigorous testing and adhere to strict quality standards to ensure reliability and durability in demanding situations. They may incorporate specialized materials, coatings, and construction techniques to enhance their ruggedness and resistance to environmental stressors.
In addition to their robust construction, Military Circuit Boards often feature advanced technologies and components optimized for military use, such as high-performance processors, memory modules, and communication interfaces. These boards are utilized in various military equipment, including aircraft, vehicles, communication systems, and weapons platforms, where reliability and performance are critical.
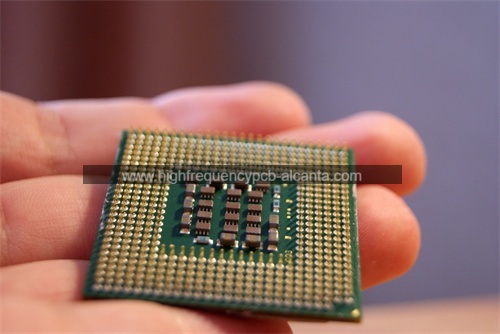
Military Circuit Board Manufacturer
What are the Military Circuit Board (MCB) Design Guidelines?
Designing Military Circuit Boards (MCBs) involves adhering to specific guidelines and standards to ensure they meet the stringent requirements of military applications. Some key design guidelines for MCBs include:
- Reliability: MCBs must be highly reliable to withstand harsh environmental conditions and operate in critical military systems without failure. Designers must select components and materials known for their reliability and durability.
- Ruggedness: MCBs should be ruggedized to withstand shock, vibration, temperature extremes, humidity, and other environmental factors encountered in military operations. This may involve using reinforced substrates, conformal coatings, and robust component mounting techniques.
- EMI/EMC Compliance: MCBs must comply with electromagnetic interference (EMI) and electromagnetic compatibility (EMC) standards to ensure they do not interfere with other electronic equipment and are not susceptible to interference from external sources. Proper grounding, shielding, and layout techniques are essential for achieving EMI/EMC compliance.
- Size, Weight, and Power (SWaP) Optimization: Military systems often have stringent size, weight, and power requirements. MCBs should be designed to minimize their footprint, weight, and power consumption while still meeting performance specifications.
- High-Speed Design Considerations: Many military applications require high-speed data processing and communication capabilities. MCBs must be designed with proper signal integrity, impedance matching, and routing techniques to ensure reliable high-speed operation.
- Component Selection: Selecting components rated for extended temperature ranges, high reliability, and long-term availability is critical for MCBs. Components should be sourced from trusted suppliers and undergo rigorous qualification testing.
- Thermal Management: MCBs operating in extreme temperature environments must incorporate effective thermal management techniques to prevent overheating and ensure reliable operation. This may involve using heat sinks, thermal vias, and strategically placed airflow channels.
- Security: Military systems often require stringent security measures to protect sensitive data and prevent unauthorized access. MCBs may incorporate hardware security features such as tamper detection, encryption, and secure boot mechanisms.
- Testing and Qualification: MCBs must undergo thorough testing and qualification processes to ensure they meet all performance, reliability, and compliance requirements. This may include environmental testing, functional testing, and compliance testing to military standards such as MIL-STD-810 and MIL-STD-461.
By following these design guidelines, engineers can develop Military Circuit Boards that meet the demanding requirements of military applications while ensuring reliability, durability, and performance in the field.
What is the Military Circuit Board (MCB) Fabrication Process?
The fabrication process for Military Circuit Boards (MCBs) is similar to that of standard circuit boards but often involves additional steps and considerations to meet the rigorous requirements of military applications. Here’s an overview of the typical MCB fabrication process:
- Design and Layout: The fabrication process begins with the design and layout of the MCB. Engineers use specialized software to create the circuit board layout, incorporating all the necessary components, traces, and connections according to the design requirements and guidelines.
- Material Selection: Military-grade circuit boards require materials capable of withstanding harsh environmental conditions and providing high reliability. Common materials used include high-temperature laminates, rigid and flexible substrates, and specialized coatings for enhanced durability and resistance to moisture, corrosion, and thermal stress.
- Layer Stackup Design: MCBs often have multiple layers to accommodate complex circuits and high-density components. Engineers design the layer stackup considering factors such as signal integrity, impedance control, and thermal management. Special attention is paid to minimizing signal interference and ensuring reliable high-speed performance.
- Photoresist Application and Imaging: Once the design is finalized, the circuit board substrate is coated with a layer of photoresist. The circuit pattern is then transferred onto the substrate using photolithography techniques, which involve exposing the photoresist to UV light through a photomask, followed by developing to remove the unexposed areas.
- Etching: After imaging, the substrate undergoes etching to remove the exposed copper and create the desired circuit traces and patterns. Chemical etchants are commonly used to dissolve the unwanted copper while leaving the protected areas intact.
- Drilling: Holes for component mounting and vias are drilled into the circuit board using precision drilling machines. Laser drilling may be employed for high-density boards or specialized applications requiring very small holes.
- Plating and Surface Finishing: After drilling, the holes are plated with conductive material to provide electrical connections between layers. Common plating materials include copper and tin-lead alloys. Surface finishing processes such as immersion gold, electroless nickel immersion gold (ENIG), or tin-lead solder may be applied to improve solderability, corrosion resistance, and wire bonding capability.
- Component Assembly: Once the fabrication of the bare circuit board is complete, electronic components are assembled onto the board using surface mount technology (SMT) or through-hole technology (THT). Automated pick-and-place machines accurately place the components onto the board, and solder paste is applied to facilitate soldering.
- Soldering: The assembled board undergoes reflow soldering or wave soldering to permanently attach the components to the board and create reliable electrical connections. Solder joints are inspected for quality, and any defects are repaired.
- Testing and Inspection: The finished MCB undergoes comprehensive testing and inspection to ensure it meets all performance, reliability, and quality standards. This may include electrical testing, functional testing, visual inspection, and automated optical inspection (AOI) to detect any defects or anomalies.
- Conformal Coating and Encapsulation: In some cases, MCBs may be coated with a protective conformal coating to enhance durability and resistance to environmental stressors such as moisture, dust, and chemicals. Potting or encapsulation may also be used to further protect the board and its components from mechanical shock and vibration.
- Packaging and Shipping: Once the MCB has passed all tests and inspections, it is packaged according to customer specifications and shipped to its final destination, where it will be integrated into military equipment or systems.
Throughout the fabrication process, strict quality control measures are implemented to ensure the MCB meets the stringent requirements of military applications for reliability, durability, performance, and compliance with relevant standards and specifications.
How do you manufacture a Military Circuit Board (MCB)?
Manufacturing a Military Circuit Board (MCB) involves several steps, from design and material selection to fabrication, assembly, and testing. Here’s a detailed overview of the manufacturing process:
- Design and Layout: Engineers design the MCB layout using specialized software, considering the circuit’s functionality, size, and other requirements. The layout includes the placement of components, routing of traces, and layer stackup design.
- Material Selection: High-quality materials are selected for MCB fabrication, including substrates, copper foils, and coatings. Military-grade materials are chosen for their reliability, durability, and ability to withstand harsh environmental conditions.
- Layer Stackup Design: MCBs often have multiple layers to accommodate complex circuits and high-density components. Engineers design the layer stackup to optimize signal integrity, impedance control, and thermal management.
- Photoresist Application and Imaging: The substrate is coated with a layer of photoresist, and the circuit pattern is transferred onto it using photolithography techniques. UV light exposure through a photomask defines the circuit traces, and unexposed areas are removed during development.
- Etching: Chemical etchants are used to remove the exposed copper and create the desired circuit patterns. This process defines the conductive traces on the MCB.
- Drilling: Precision drilling machines are used to create holes for component mounting and vias, which provide electrical connections between layers in multilayer boards. Laser drilling may be employed for high-density boards.
- Plating and Surface Finishing: The drilled holes are plated with conductive material to facilitate electrical connections. Surface finishing processes such as immersion gold, ENIG, or tin-lead solder are applied to improve solderability and corrosion resistance.
- Component Assembly: Electronic components are assembled onto the board using SMT or THT methods. Automated pick-and-place machines accurately place components, and solder paste is applied before reflow or wave soldering to create permanent connections.
- Soldering: The assembled board undergoes reflow soldering or wave soldering to attach components and create reliable electrical connections. Solder joints are inspected for quality, and any defects are repaired.
- Testing and Inspection: The finished MCB undergoes comprehensive testing and inspection to ensure it meets all performance, reliability, and quality standards. Electrical testing, functional testing, visual inspection, and AOI are performed to detect defects or anomalies.
- Conformal Coating and Encapsulation: MCBs may be coated with a conformal coating to enhance durability and protect against environmental stressors. Potting or encapsulation may also be used for additional protection.
- Packaging and Shipping: Once the MCB passes all tests and inspections, it is packaged according to customer specifications and shipped to its final destination for integration into military equipment or systems
Throughout the manufacturing process, strict quality control measures are implemented to ensure the MCB meets the stringent requirements of military applications for reliability, durability, performance, and compliance with relevant standards and specifications. Additionally, security measures may be incorporated to protect sensitive data and prevent unauthorized access.
How much should a Military Circuit Board (MCB) cost?
The cost of a Military Circuit Board (MCB) can vary significantly depending on various factors such as:
- Complexity: The complexity of the circuit design and the number of layers in the board can impact the cost. More complex designs with higher layer counts generally require more materials and labor, resulting in higher costs.
- Material Quality: Military-grade materials used in MCBs are typically more expensive than standard materials due to their higher reliability and durability. The cost of materials can vary based on factors such as substrate type, copper thickness, and surface finish.
- Manufacturing Processes: The fabrication and assembly processes used to manufacture the MCB can affect the cost. Advanced techniques such as laser drilling, high-precision imaging, and conformal coating may increase manufacturing costs.
- Volume: The volume of MCBs being produced can impact the unit cost. Larger production runs often benefit from economies of scale, leading to lower per-unit costs. However, smaller quantities may incur higher setup and overhead costs.
- Testing and Certification: Military-grade MCBs undergo rigorous testing and certification processes to ensure they meet stringent performance and reliability requirements. The cost of testing and certification can contribute to the overall cost of the MCB.
- Customization: Customized features or specifications requested by the customer may increase the cost of the MCB. This could include specialized coatings, additional testing requirements, or unique design considerations.
Due to these factors, it’s challenging to provide a specific cost for a Military Circuit Board without knowing the exact specifications and requirements of the project. However, military-grade circuit boards typically command a higher price compared to commercial or industrial-grade boards due to their specialized nature and stringent quality standards. It’s essential for customers to work closely with manufacturers to determine the most cost-effective solution that meets their specific needs while ensuring reliability and performance in military applications.
What is Military Circuit Board (MCB) base material?
Military Circuit Boards (MCBs) use a variety of base materials, each selected for its specific properties and suitability for military applications. Some common base materials used in MCBs include:
- FR-4: FR-4 is a widely used epoxy-based laminate material with woven glass reinforcement. It provides good electrical insulation, mechanical strength, and dimensional stability. FR-4 is commonly used in commercial and industrial applications but can also be suitable for certain military applications.
- Polyimide (PI): Polyimide is a high-performance polymer with excellent thermal stability, chemical resistance, and mechanical properties. It is commonly used in MCBs for its ability to withstand high temperatures and harsh environmental conditions. Polyimide-based substrates are often used in flexible and rigid-flex MCBs.
- Rogers PCB Materials: Rogers Corporation produces a range of high-frequency laminates specifically designed for RF and microwave applications. These materials offer low dielectric loss, excellent signal integrity, and high-frequency performance, making them suitable for military communication systems and radar applications.
- Aramid-Based Laminates: Aramid-based laminates, such as Arlon and Isola, offer high thermal conductivity, excellent dimensional stability, and good mechanical properties. These materials are often used in MCBs for their ability to withstand high temperatures and mechanical stress.
- Metal-Core PCBs: Metal-core PCBs feature a metal core layer, typically aluminum or copper, sandwiched between layers of dielectric material. These boards offer superior thermal conductivity and heat dissipation, making them suitable for high-power military applications where thermal management is critical.
- Ceramic PCBs: Ceramic-based substrates offer excellent thermal conductivity, high electrical insulation, and mechanical stability. They are often used in MCBs for high-power and high-frequency applications where thermal management and signal integrity are essential.
The choice of base material for an MCB depends on factors such as the operating environment, required electrical and mechanical properties, thermal management requirements, and cost considerations. Military-grade circuit boards often use specialized materials that can withstand harsh environmental conditions, extreme temperatures, and high levels of vibration while maintaining reliability and performance in demanding military applications.
Which company makes Military Circuit Boards (MCBs)?
Many companies specialize in manufacturing Military Circuit Boards (MCBs), with some focusing on providing military-grade circuit boards and related services. For example, companies like Mercury Systems, Northrop Grumman, and Raytheon in the United States, as well as China Aerospace Science and Technology Corporation, AVIC Optoelectronics, and North Huachuang in China, are involved in producing military circuit boards.
Our company also has the capability to manufacture Military Circuit Boards (MCBs). We have advanced production equipment and technology and are dedicated to meeting the unique requirements of our customers in the military sector. Our production processes adhere strictly to military standards and specifications to ensure products have high reliability, durability, and performance. With a team of experienced professionals, we excel in designing, manufacturing, and testing military circuit boards.
Our military circuit boards can be applied in various military systems and equipment, including aircraft, ships, vehicles, communication devices, radar systems, and more. We can provide customized solutions, designing and manufacturing military circuit boards that meet specific requirements of our customers.
We are committed to providing high-quality, reliable, and high-performance products to our customers and work closely with them to ensure their needs are met and expectations exceeded. Whether it’s in terms of product quality or delivery time, we strive for excellence and aim to be a trusted partner for our customers.
What are the 7 qualities of good customer service?
Good customer service is essential for building positive relationships with customers and fostering loyalty. Seven qualities of good customer service include:
- Responsiveness: Responding promptly to customer inquiries, questions, and concerns demonstrates attentiveness and shows that their needs are valued. Whether it’s through phone, email, live chat, or in person, being responsive helps to address issues in a timely manner.
- Empathy:Empathizing with customers and understanding their perspective allows customer service representatives to connect on a deeper level. Showing empathy involves actively listening to customers, acknowledging their feelings, and expressing understanding and concern.
- Professionalism: Maintaining professionalism in all interactions with customers is crucial for building trust and credibility. This includes being polite, respectful, and courteous, regardless of the situation or the customer’s demeanor.
- Knowledgeability:Having in-depth knowledge about products, services, policies, and procedures enables customer service representatives to provide accurate and helpful information to customers. Being knowledgeable instills confidence in customers and helps to resolve issues effectively.
- Problem-solving skills: Good customer service involves being proactive in resolving customer issues and finding solutions to their problems. Customer service representatives should be resourceful, creative, and willing to go the extra mile to address customer concerns and ensure satisfaction.
- Flexibility: Being adaptable and flexible allows customer service representatives to accommodate the diverse needs and preferences of customers. This may involve customizing solutions, offering alternatives, or adjusting policies within reason to meet customer expectations.
- Consistency: Consistency in delivering high-quality customer service across all touchpoints and interactions is key to building a positive reputation and fostering long-term relationships with customers. Consistency ensures that customers receive the same level of service regardless of when, where, or how they interact with the company.
By embodying these qualities, businesses can create positive experiences for their customers and differentiate themselves from competitors in a competitive marketplace.
FAQs (Frequently Asked Questions)
What are Military Circuit Boards (MCBs)?
Military Circuit Boards (MCBs) are specialized electronic boards designed and manufactured to meet the stringent requirements of military applications. They are built to withstand harsh environmental conditions, extreme temperatures, high levels of vibration, and electromagnetic interference (EMI).
What makes MCBs different from commercial circuit boards?
MCBs are designed and built to much higher standards compared to commercial circuit boards. They undergo rigorous testing and adhere to strict quality standards to ensure reliability and durability in demanding military environments.
What are some common applications of MCBs?
MCBs are used in various military equipment and systems, including aircraft, vehicles, communication systems, radar systems, weapons platforms, and more. They play a critical role in ensuring the reliability and performance of these military technologies.
What are the key design considerations for MCBs?
Key design considerations for MCBs include reliability, ruggedness, EMI/EMC compliance, size, weight, and power optimization, high-speed design considerations, component selection, thermal management, security, and testing/qualification.
What materials are commonly used in MCBs?
Common materials used in MCBs include high-temperature laminates, polyimide (PI), metal-core laminates, ceramic substrates, and specialized coatings. These materials are chosen for their ability to withstand harsh environmental conditions and provide high reliability.
How are MCBs tested and qualified for military use?
MCBs undergo thorough testing and qualification processes to ensure they meet all performance, reliability, and compliance requirements. This may include environmental testing, functional testing, EMI/EMC testing, and compliance testing to military standards such as MIL-STD-810 and MIL-STD-461.
Can MCBs be customized for specific military applications?
Yes, MCBs can be customized to meet the specific requirements of different military applications. This may involve customizing the design, materials, coatings, and specifications to ensure optimal performance and reliability in the intended use case.