Microwave Substrate Manufacturer
Microwave Substrate Manufacturer,Microwave substrates are specialized materials crucial for the construction of high-frequency electronic circuits. These substrates serve as the foundation upon which various electronic components, such as transistors and capacitors, are mounted and interconnected. Engineered to exhibit specific electrical properties, microwave substrates facilitate efficient transmission of microwave signals with minimal loss or distortion. Typically made from materials like ceramics (e.g., alumina, aluminum nitride) or high-frequency laminates (e.g., PTFE-based materials), microwave substrates boast characteristics such as low dielectric loss, high thermal conductivity, and controlled impedance. Their applications span across diverse industries, including telecommunications, radar systems, satellite communications, and microwave ovens. The manufacturing process for microwave substrates involves precise techniques such as material selection, deposition of conductive layers, photolithography, etching, and surface treatment. These substrates play a fundamental role in enabling the functionality and performance of various high-frequency electronic devices and systems, contributing to advancements in modern technology and communication.
What is a Microwave Substrate?
A microwave substrate is a material used in the construction of electronic circuits, particularly those operating at microwave frequencies. These substrates provide a stable and reliable platform for mounting and interconnecting various electronic components such as transistors, diodes, and capacitors.
Microwave substrates are designed to have specific electrical properties, such as low dielectric loss, high thermal conductivity, and controlled impedance, to ensure efficient transmission of microwave signals without significant loss or distortion. Common materials used as microwave substrates include ceramics like alumina (Al2O3), aluminum nitride (AlN), and various types of high-frequency laminates.
These substrates are essential for the development of microwave circuits used in applications such as telecommunications, radar systems, satellite communications, and microwave ovens, where high-frequency signals need to be transmitted and processed efficiently.
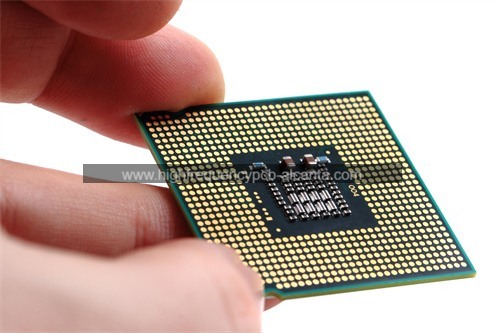
Microwave Substrate Manufacturer
What are the Microwave Substrate Design Guidelines?
Designing with microwave substrates requires careful consideration of various factors to ensure optimal performance of the electronic circuitry. Here are some general design guidelines:
- Dielectric Constant (ε_r): Choose a substrate material with a dielectric constant appropriate for the desired circuit performance. Higher dielectric constants allow for smaller circuit dimensions but can also increase signal dispersion and loss.
- Dielectric Loss (tanδ): Minimize dielectric loss to maintain signal integrity and prevent excessive heating of the substrate. Low-loss materials such as high-frequency laminates are often preferred for microwave applications.
- Thermal Conductivity: Select a substrate with adequate thermal conductivity to dissipate heat generated by active components such as transistors. Effective thermal management helps maintain circuit stability and reliability, especially in high-power applications.
- Substrate Thickness: The substrate thickness affects the characteristic impedance of transmission lines on the substrate. Thinner substrates generally result in lower characteristic impedance, while thicker substrates lead to higher characteristic impedance. Choose the appropriate thickness based on the desired impedance and mechanical considerations.
- Surface Roughness: Maintain smooth substrate surfaces to minimize signal losses due to surface roughness effects. Surface roughness can lead to increased insertion loss and impedance mismatch in microwave circuits.
- Impedance Matching: Use transmission line techniques such as microstrip or stripline to achieve impedance matching between circuit components and the transmission lines on the substrate. Proper impedance matching maximizes power transfer and minimizes signal reflections.
- Grounding:Implement effective grounding techniques to minimize ground loops and ensure proper signal return paths. Ground planes on the substrate provide low-impedance paths for return currents, reducing electromagnetic interference (EMI) and signal distortion.
- Component Placement: Carefully layout components on the substrate to minimize signal coupling, crosstalk, and parasitic effects. Considerations such as component spacing, orientation, and routing of signal traces can significantly impact circuit performance.
- Environmental Considerations:Consider the operating environment, including temperature, humidity, and vibration, when selecting substrate materials and designing the circuit layout. Ensure that the chosen substrate can withstand the environmental conditions encountered during operation.
- Simulation and Testing: Use computer-aided design (CAD) tools and electromagnetic simulation software to model and analyze circuit performance before fabrication. Additionally, perform thorough testing and characterization of fabricated circuits to validate design assumptions and optimize performance.
By following these design guidelines, engineers can develop microwave circuits with improved performance, reliability, and manufacturability for various applications.
What is the Microwave Substrate Fabrication Process?
The fabrication of microwave substrates involves a series of precise and carefully controlled processes to ensure that the final product meets the stringent requirements of microwave applications. The process generally includes the following key steps:
- Material Selection: The first step is selecting the appropriate substrate material based on the application’s requirements, such as dielectric constant, loss tangent, thermal conductivity, and mechanical strength. Common materials include ceramics like alumina and aluminum nitride, as well as specialized laminates like Rogers or Teflon-based substrates.
- Substrate Preparation:The selected material is processed into the desired thickness and surface quality. This may involve mechanical processes like cutting and grinding, as well as chemical processes to clean and prepare the surface for further processing.
- Deposition of Conductive Layers: Conductive layers, typically made of metals such as copper, are deposited on the substrate. This can be done through various methods such as sputtering, electroplating, or evaporating. The choice of method depends on the desired thickness and uniformity of the metal layers.
- Photolithography: This step involves transferring the circuit pattern onto the substrate. A light-sensitive chemical (photoresist) is applied to the conductive layer, and then a mask with the circuit pattern is used to expose areas of the photoresist to light. The exposed or unexposed photoresist, depending on the type used (positive or negative), is then developed to reveal the underlying metal layer.
- Etching: The exposed metal areas are then etched away using a chemical etchant, leaving behind the desired circuit pattern. This step requires precise control to ensure that the etching process does not underetch or overetch the desired pattern.
- Drilling and Cutting: For substrates that require vias or need to be fit into specific assemblies, mechanical drilling and cutting are performed. This step must be done carefully to avoid damaging the substrate or the circuitry.
- Surface Finishing: After etching, the substrate may undergo surface finishing processes to improve conductivity, solderability, or resistance to oxidation. Common surface finishes include gold plating, tin-lead plating, or organic coatings.
- Testing and Inspection: Throughout the fabrication process, various testing and inspection techniques are employed to ensure quality and functionality. This includes visual inspection, electrical testing to measure impedance and continuity, as well as more advanced methods like microwave performance testing using network analyzers.
- Assembly: Finally, components such as chips, resistors, and capacitors are mounted on the substrate. This can be done using surface-mount technology (SMT), through-hole technology, or other hybrid methods. This step also involves soldering or bonding components to the substrate, followed by final testing to ensure operational functionality.
- Packaging: Once assembled and tested, the substrates are packaged for delivery. This includes protective measures to prevent damage during transport and handling.
This entire process requires a high degree of precision and control to ensure that the microwave substrates perform as expected in their respective applications, whether in communications, radar systems, or other high-frequency electronic environments.
How do you manufacture a Microwave Substrate?
Manufacturing microwave substrates involves several precise steps to create a material with specific electrical properties suitable for high-frequency electronic applications. Here’s an overview of the typical manufacturing process:
- Material Selection:The process begins with selecting the appropriate substrate material based on the desired electrical characteristics and mechanical properties. Common materials include ceramics such as alumina (Al2O3), aluminum nitride (AlN), or specialized high-frequency laminates.
- Powder Preparation (for Ceramic Substrates): If ceramic substrates are chosen, the raw materials are carefully selected and blended to achieve the desired composition and purity. This mixture is then milled into a fine powder to ensure uniformity.
- Forming: The substrate material is formed into the desired shape using techniques such as dry pressing, tape casting, or injection molding. This step may involve pressing the powder into a green body or casting it into a tape or sheet form.
- Drying: After forming, the green bodies or tapes are dried to remove any excess moisture. Proper drying is crucial to prevent defects and ensure dimensional stability during subsequent processing steps.
- Sintering: The dried green bodies or tapes are subjected to high temperatures in a furnace in a process called sintering. This step causes the particles to bond together, forming a dense and solid ceramic structure. Sintering also influences the final microstructure and electrical properties of the substrate.
- Lamination (for High-Frequency Laminates): If high-frequency laminates are used, the manufacturing process involves laminating layers of dielectric material with reinforcing fibers and resin binders. This creates a composite material with excellent electrical properties and mechanical strength.
- Curing and Prepreg Processing (for Laminates): After lamination, the composite material is cured under heat and pressure to ensure proper bonding and resin impregnation. Additional prepreg processing steps may be performed to adjust the material’s thickness and surface finish.
- Copper Cladding: For both ceramic substrates and laminates, copper foil is typically bonded to one or both sides of the material to create conductive layers. This is often done using an adhesive or bonding agent followed by lamination under heat and pressure.
- Etching: The copper-clad substrate is then coated with a photoresist and exposed to UV light through a photomask, defining the desired circuit pattern. The exposed areas are then etched away using chemical etchants, leaving behind the conductive traces.
- Surface Treatment: After etching, the substrate may undergo surface treatment processes such as chemical cleaning, surface roughening, or application of protective coatings to improve solderability and prevent oxidation.
- Inspection and Testing: Throughout the manufacturing process, the substrates undergo rigorous inspection and testing to ensure quality and compliance with specifications. This includes dimensional measurements, visual inspection, electrical testing for impedance and dielectric properties, and microstructural analysis.
- Final Finishing and Packaging: Once the substrates pass inspection, they undergo final finishing processes such as edge trimming, surface polishing, and marking. They are then packaged and prepared for shipment to customers or further assembly into electronic components and systems.
Each of these manufacturing steps requires careful control of process parameters and quality assurance measures to produce microwave substrates with consistent performance and reliability for use in high-frequency electronic applications.
How much should a Microwave Substrate cost?
The cost of a microwave substrate can vary significantly depending on several factors, including the material used, the manufacturing process, the size and thickness of the substrate, and the required electrical and mechanical specifications. Here are some factors that can influence the cost:
- Material: Different substrate materials have varying costs. For example, ceramic substrates like alumina or aluminum nitride may be more expensive than high-frequency laminates due to the raw material costs and the complexity of the manufacturing process.
- Manufacturing Process: The complexity and precision required in the manufacturing process can impact the cost. Processes like sintering for ceramic substrates or lamination for high-frequency laminates may require specialized equipment and skilled labor, contributing to higher production costs.
- Size and Thickness:Larger and thicker substrates generally require more material and may involve additional processing steps, which can increase the cost. Additionally, substrates with tighter dimensional tolerances or specific thickness requirements may incur higher manufacturing costs.
- Electrical Specifications: Substrates with stringent electrical properties, such as low dielectric loss, controlled impedance, or high thermal conductivity, may require more precise manufacturing techniques or higher quality materials, resulting in higher costs.
- Volume and Order Quantity: Economies of scale can play a significant role in determining the cost of microwave substrates. Larger production volumes typically lead to lower per-unit costs due to efficiencies in material procurement, manufacturing processes, and overhead expenses.
- Customization: If the substrate requires customization, such as specific circuit patterns, surface finishes, or additional features like vias or edge connectors, the cost may increase to accommodate the extra design and manufacturing efforts.
- Supplier and Market Dynamics: The pricing of microwave substrates can also be influenced by factors such as supplier competition, market demand, and fluctuations in raw material costs.
Given these factors, it’s challenging to provide a specific cost without knowing the detailed requirements of the microwave substrate in question. Typically, customers can request quotes from substrate manufacturers or suppliers based on their specific needs and volume requirements.
What is Microwave Substrate base material?
Microwave substrates can be made from various materials, each offering different properties and suitability for different applications. Some common base materials used for microwave substrates include:
- Ceramics: Ceramic materials such as alumina (Al2O3) and aluminum nitride (AlN) are commonly used as base materials for microwave substrates. These ceramics offer excellent thermal conductivity, high dielectric strength, and stability over a wide range of temperatures. Alumina substrates are widely used in microwave applications due to their relatively low cost and good electrical properties, while aluminum nitride substrates offer higher thermal conductivity and are preferred for applications requiring superior heat dissipation.
- High-Frequency Laminates: High-frequency laminates are composite materials made from layers of dielectric material, reinforced with fibers (such as glass or aramid) and impregnated with resin binders. These laminates offer excellent electrical properties, including low dielectric loss and controlled impedance. Examples of high-frequency laminate materials include polytetrafluoroethylene (PTFE) based materials like Rogers RO4000 series, Arlon, and Taconic substrates.
- Semiconductors: In certain specialized applications, semiconductor materials such as silicon (Si) or gallium arsenide (GaAs) may be used as base materials for microwave substrates. These materials offer unique electrical properties suited for specific high-frequency and high-power applications, such as microwave integrated circuits (MICs) and monolithic microwave integrated circuits (MMICs).
The choice of base material depends on factors such as the desired electrical properties (dielectric constant, loss tangent, impedance), thermal conductivity, mechanical strength, and cost considerations. Each material has its advantages and limitations, and the selection is based on the requirements of the particular microwave circuit or system being designed.
Which company makes Microwave Substrates?
Many companies produce microwave substrates, and some major ones include Rogers Corporation, Arlon Electronic Materials, Taconic Advanced Dielectric Division in the United States, as well as Murata Manufacturing Co., Ltd. and Kyocera Corporation in Japan. These companies have rich experience and advanced technology in the field of microwave substrates, offering various types of substrates to meet the needs of different applications.
Our company is also a professional microwave substrate manufacturer. We have advanced production equipment and a skilled technical team capable of producing various types of microwave substrates, including:
- Ceramic Substrates: We can produce high-purity alumina (Al2O3) and aluminum nitride (AlN) substrates with excellent electrical performance and thermal conductivity, suitable for high-frequency and high-temperature environments.
- High-Frequency Laminates: We can manufacture various types of high-frequency laminates, including PTFE-based materials such as Teflon, FR-4, and special composite materials, characterized by low dielectric loss and controlled impedance.
- Semiconductor Substrates: We can also produce semiconductor materials such as silicon (Si) and gallium arsenide (GaAs) substrates, suitable for specific high-frequency and high-power microwave integrated circuit applications.
Our manufacturing process strictly adheres to international standards to ensure stable and reliable product quality. With a professional R&D team, we can provide customized solutions according to customer requirements and offer technical support and after-sales service. We are committed to providing high-quality microwave substrate products to meet the needs of different application fields.
What are the 7 qualities of good customer service?
Good customer service is characterized by several key qualities that contribute to positive interactions and relationships with customers. Here are seven qualities of good customer service:
- Responsiveness: Good customer service involves promptly addressing customer inquiries, concerns, and requests. Responding to customers in a timely manner demonstrates attentiveness and shows that their needs are valued.
- Empathy: Empathy is the ability to understand and share the feelings of others. Good customer service representatives empathize with customers’ situations and concerns, showing genuine care and concern for their well-being.
- Communication Skills: Effective communication is essential for delivering good customer service. Customer service representatives should possess strong verbal and written communication skills to convey information clearly, listen actively to customers’ needs, and provide helpful explanations or solutions.
- Problem-Solving Abilities: Good customer service involves effectively resolving customer problems and addressing their concerns. Customer service representatives should possess strong problem-solving abilities, including the capacity to analyze issues, identify root causes, and implement appropriate solutions.
- Professionalism: Professionalism entails maintaining a courteous and respectful demeanor when interacting with customers. Good customer service representatives conduct themselves professionally, demonstrating integrity, reliability, and a commitment to upholding company values and standards.
- Product Knowledge: Good customer service requires a thorough understanding of the products or services being offered. Customer service representatives should possess comprehensive product knowledge to accurately answer customer questions, provide relevant information, and offer appropriate recommendations.
- Follow-Up and Follow-Through: Following up with customers after their interactions and ensuring that any promises or commitments made are fulfilled demonstrates accountability and reliability. Good customer service representatives follow through on their commitments and take proactive steps to ensure customer satisfaction.
By embodying these qualities, organizations can deliver exceptional customer service experiences that foster customer loyalty, satisfaction, and trust.
FAQs
What is a microwave substrate?
A microwave substrate is a material used in the construction of electronic circuits, particularly those operating at microwave frequencies. These substrates provide a stable platform for mounting and interconnecting electronic components such as transistors, diodes, and capacitors.
What are microwave substrates made of?
Microwave substrates can be made from various materials, including ceramics such as alumina (Al2O3) and aluminum nitride (AlN), as well as high-frequency laminates like polytetrafluoroethylene (PTFE) based materials such as Rogers RO4000 series and Arlon substrates.
What are the key properties of microwave substrates?
Key properties of microwave substrates include low dielectric loss, high thermal conductivity, controlled impedance, and mechanical stability. These properties ensure efficient transmission of microwave signals and reliable performance in high-frequency applications.
What are microwave substrates used for?
Microwave substrates are used in various applications, including telecommunications, radar systems, satellite communications, microwave ovens, wireless networks, and high-frequency electronic devices.
How are microwave substrates manufactured?
The manufacturing process for microwave substrates involves steps such as material selection, substrate preparation, deposition of conductive layers, photolithography, etching, surface treatment, and testing. Different materials may undergo specific processes tailored to their properties and intended applications.
What factors should be considered when selecting a microwave substrate?
When selecting a microwave substrate, factors such as dielectric constant, dielectric loss, thermal conductivity, mechanical strength, cost, and specific application requirements should be considered to ensure optimal performance and reliability.
Where can microwave substrates be purchased?
Microwave substrates can be purchased from specialized manufacturers, distributors, or suppliers of electronic components and materials. Companies specializing in microwave substrates include Rogers Corporation, Arlon Electronic Materials, Taconic Advanced Dielectric Division, and others.