Microwave PCB Manufacturer
Microwave PCB Manufacturer,Microwave PCBs, designed for high-frequency applications, boast specialized materials and meticulous engineering. These boards, crafted with low-loss substrates like PTFE or ceramic-filled composites, ensure minimal signal degradation, vital for telecommunications, radar, and satellite systems. With controlled impedance routing and precise manufacturing, Microwave PCBs maintain signal integrity at frequencies surpassing 1 GHz. Their design prioritizes reduced electromagnetic interference and optimized thermal management, guaranteeing reliable performance in critical environments. From RF transmitters to medical devices, Microwave PCBs empower cutting-edge technologies with precision, stability, and unmatched high-frequency capabilities.
What is a Microwave PCB?
A Microwave PCB (Printed Circuit Board) is a specialized type of PCB designed to operate at microwave frequencies, typically above 1 GHz. These PCBs are essential in applications involving high-frequency signals such as telecommunications, radar systems, satellite communications, and medical devices.
Microwave PCBs are distinct due to their specific requirements for materials and design. The substrate material is crucial; it must have a low dielectric constant and low loss tangent to minimize signal loss and ensure signal integrity. Common materials include PTFE (polytetrafluoroethylene), ceramic-filled PTFE composites, and high-performance laminates like Rogers materials. These substrates provide stable electrical properties over a wide frequency range and various environmental conditions.
The design of Microwave PCBs involves meticulous considerations to manage electromagnetic interference (EMI) and signal integrity. Techniques like controlled impedance routing, the use of microstrip or stripline transmission lines, and careful layer stack-up are employed to maintain signal fidelity. Additionally, attention to detail in the layout, such as minimizing discontinuities and ensuring proper grounding, is critical to prevent signal degradation.
Furthermore, Microwave PCBs often incorporate advanced features like plated through holes (PTH) and via-in-pad to optimize the signal path and reduce parasitic inductance and capacitance. Manufacturing these boards requires precision in etching and plating processes to achieve the fine geometries needed for high-frequency operation.
Overall, Microwave PCBs are pivotal in enabling modern high-frequency electronic applications, where performance and reliability are paramount. Their design and fabrication are more complex than standard PCBs, necessitating expertise in both materials science and high-frequency circuit design.
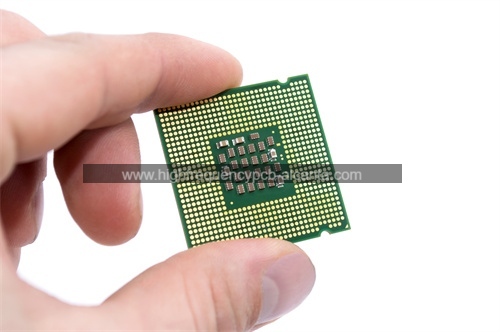
Microwave PCB Manufacturer
What are the Microwave PCB Design Guidelines?
Microwave PCB design requires adherence to specific guidelines to ensure optimal performance at high frequencies. Here are some key guidelines:
- Substrate Selection: Choose a substrate material with low dielectric constant (Dk) and low loss tangent (Df) to minimize signal loss and maintain signal integrity. Common materials include PTFE-based laminates like FR-4, Rogers materials, and ceramic-filled PTFE composites.
- Controlled Impedance: Maintain controlled impedance for transmission lines by carefully selecting trace widths, heights, and spacing. Use impedance calculation tools to ensure consistent impedance throughout the board.
- Transmission Line Routing: Use microstrip or stripline transmission lines to guide high-frequency signals. Keep traces short and direct to minimize signal loss and impedance mismatch.
- Grounding: Implement a solid ground plane beneath signal traces to reduce electromagnetic interference (EMI) and provide a low-impedance return path. Avoid routing high-frequency signals over splits or gaps in the ground plane.
- Via Design: Minimize the number of vias in high-frequency signal paths to reduce parasitic capacitance and inductance. Use via stitching to connect ground planes and improve signal return paths.
- Component Placement: Place high-frequency components close together to minimize trace length and reduce parasitic capacitance and inductance. Position critical components symmetrically to maintain signal symmetry and minimize electromagnetic coupling.
- Avoid Sharp Corners: Round or chamfer sharp corners to reduce reflections and impedance mismatches that can degrade signal integrity.
- Crosstalk Mitigation: Maintain adequate spacing between adjacent signal traces to minimize crosstalk. Use shielding techniques like ground planes or shielded enclosures for sensitive traces.
- Thermal Management: Consider thermal management techniques to dissipate heat generated by high-frequency components. Ensure proper airflow and heat sinking to prevent thermal issues that can affect performance.
- EMI/EMC Considerations: Design the PCB with EMI/EMC compliance in mind. Employ techniques such as shielding, filtering, and grounding to reduce electromagnetic interference and ensure electromagnetic compatibility.
- Testing and Validation: Perform thorough testing and validation of the PCB design using high-frequency measurement equipment. Verify signal integrity, impedance matching, and EMI/EMC compliance through simulation and physical testing.
By following these guidelines, designers can create Microwave PCBs that meet the stringent requirements of high-frequency applications, ensuring reliable performance and signal integrity.
What is the Microwave PCB Fabrication Process?
The fabrication process for Microwave PCBs involves several steps, each crucial for ensuring high-quality boards capable of operating at high frequencies. Here’s an overview of the typical process:
- Design: The process begins with the design of the PCB layout using specialized CAD software. Designers adhere to strict guidelines for high-frequency applications, considering factors like controlled impedance, transmission line routing, and grounding.
- Material Selection: Choose appropriate substrate materials based on the specific requirements of the application. Common materials include PTFE-based laminates (e.g., Rogers materials), ceramic-filled PTFE composites, and high-performance FR-4 variants.
- Preparation: Clean the substrate material to remove any contaminants that could affect the adhesion of copper during the next steps.
- Copper Cladding: Apply a thin layer of copper to one or both sides of the substrate material through processes like electroless plating or lamination with copper foil. This copper layer will form the conductive traces and ground planes of the PCB.
- Photoresist Application: Apply a layer of photoresist material onto the copper-clad substrate. This photoresist layer will be selectively exposed to UV light during the next step.
- Exposure and Development: Use a photomask to selectively expose the photoresist layer to UV light, transferring the PCB layout pattern onto the photoresist. Then, develop the photoresist to remove the unexposed areas, leaving behind the pattern of traces and pads.
- Etching: Submerge the substrate in an etchant solution (e.g., ferric chloride) to remove the exposed copper, leaving only the desired traces and pads on the substrate. Careful control of the etching process is crucial to achieve precise trace geometries and maintain signal integrity.
- Stripping: Remove the remaining photoresist and any etchant residues from the substrate using a stripping solution or mechanical methods.
- Drilling: Use precision drilling equipment to create holes for through-hole components and vias. The holes are plated with copper to provide electrical connections between different layers of the PCB.
- Plating and Surface Finish: Plate the exposed copper surfaces with a protective layer (e.g., gold, tin, or ENIG) to prevent oxidation and improve solderability. Apply any additional surface finishes required for the application.
- Quality Control: Inspect the fabricated PCBs for defects such as shorts, opens, and dimensional inaccuracies. Electrical testing, including impedance measurements, may also be performed to verify the integrity of the traces.
- Routing and Profiling: Cut the PCB panel into individual boards using routing or milling equipment. Optionally, apply silkscreen legends and component markings.
- Final Inspection: Conduct a final inspection to ensure that the fabricated PCBs meet the specified requirements and quality standards.
Following these steps meticulously ensures the production of high-quality Microwave PCBs capable of meeting the stringent demands of high-frequency applications.
How do you manufacture a Microwave PCB?
Manufacturing a Microwave PCB involves several specialized steps to ensure optimal performance at high frequencies. Here’s a detailed overview of the manufacturing process:
- Material Selection: Choose substrate materials with low dielectric constant (Dk) and low loss tangent (Df), such as PTFE-based laminates (e.g., Rogers materials), ceramic-filled PTFE composites, or high-performance FR-4 variants. Select materials based on the specific requirements of the application.
- Preparation: Clean the substrate material thoroughly to remove any contaminants that could affect adhesion and processing.
- Copper Cladding: Apply a thin layer of copper to one or both sides of the substrate material using processes like electroless plating or lamination with copper foil. Ensure uniform copper coverage for consistent electrical properties.
- Photoresist Application: Apply a layer of photoresist material onto the copper-clad substrate. The photoresist layer will be selectively exposed to UV light in the next step.
- Exposure and Development: Use a photomask to selectively expose the photoresist layer to UV light, transferring the PCB layout pattern onto the photoresist. Develop the photoresist to remove the unexposed areas, leaving behind the pattern of traces and pads.
- Etching: Submerge the substrate in an etchant solution (e.g., ferric chloride) to remove the exposed copper, leaving only the desired traces and pads on the substrate. Control the etching process carefully to achieve precise trace geometries and maintain signal integrity.
- Stripping: Remove the remaining photoresist and any etchant residues from the substrate using a stripping solution or mechanical methods.
- Drilling: Use precision drilling equipment to create holes for through-hole components and vias. The holes are plated with copper to provide electrical connections between different layers of the PCB.
- Plating and Surface Finish:Plate the exposed copper surfaces with a protective layer (e.g., gold, tin, or ENIG) to prevent oxidation and improve solderability. Apply any additional surface finishes required for the application.
- Quality Control:Inspect the fabricated PCBs for defects such as shorts, opens, and dimensional inaccuracies. Perform electrical testing, including impedance measurements, to verify the integrity of the traces.
- Routing and Profiling: Cut the PCB panel into individual boards using routing or milling equipment. Optionally, apply silkscreen legends and component markings.
- Final Inspection: Conduct a final inspection to ensure that the fabricated PCBs meet the specified requirements and quality standards for high-frequency operation.
By following these steps meticulously and employing specialized techniques and materials, manufacturers can produce Microwave PCBs capable of meeting the stringent demands of high-frequency applications.
How much should a Microwave PCB cost?
The cost of a Microwave PCB can vary widely depending on several factors, including:
- Size and Complexity: Larger and more complex PCBs with intricate designs, multiple layers, and high component density will generally cost more to manufacture.
- Materials: The choice of substrate material and surface finish significantly impacts the cost. High-performance materials like Rogers materials or ceramic-filled PTFE composites tend to be more expensive than standard FR-4.
- Layer Count: PCBs with multiple layers require more complex fabrication processes and materials, leading to higher costs.
- Feature Requirements: Additional features such as controlled impedance, blind/buried vias, and fine-pitch components can increase manufacturing costs.
- Quantity: Economies of scale apply, meaning that larger production runs typically result in lower per-unit costs. Ordering in bulk can reduce the cost per board.
- Lead Time: Expedited production schedules may incur higher costs due to rush fees or expedited shipping charges.
- Supplier: Different PCB manufacturers may offer varying pricing structures and capabilities. It’s essential to obtain quotes from multiple suppliers to compare costs and services.
As a rough estimate, Microwave PCBs can range from a few dollars for simple designs to several hundred dollars for complex, high-performance boards. It’s advisable to work closely with a reputable PCB manufacturer to determine the most cost-effective solution that meets your specific requirements for performance, quality, and budget.
What is Microwave PCB base material?
The base material used for Microwave PCBs is critical for achieving high-performance at microwave frequencies. Several materials are commonly used:
- PTFE (Polytetrafluoroethylene): PTFE-based materials, such as Teflon, offer excellent electrical properties, including low dielectric constant (Dk) and low dissipation factor (Df). These materials provide stable electrical characteristics over a wide range of frequencies and temperatures, making them ideal for microwave applications.
- Rogers Materials: Rogers Corporation produces a range of high-performance laminates specifically designed for microwave and RF applications. These materials typically consist of PTFE or ceramic-filled PTFE composites, offering superior electrical performance, thermal stability, and reliability.
- Ceramic-filled PTFE Composites: These materials combine the low-loss properties of PTFE with the enhanced mechanical strength and thermal conductivity of ceramic fillers. Ceramic-filled PTFE composites are suitable for high-frequency applications requiring excellent electrical performance and reliability.
- High-Performance FR-4: While standard FR-4 is not typically recommended for microwave applications due to its higher dielectric constant and loss tangent, some high-performance FR-4 variants are available with improved electrical properties. These materials may be suitable for lower-frequency microwave applications or when cost considerations outweigh the need for optimal performance.
The choice of base material depends on factors such as frequency of operation, required electrical performance, thermal considerations, and cost constraints. Microwave PCB designers carefully select the base material to ensure that the PCB meets the specific requirements of the application while maintaining signal integrity and reliability at microwave frequencies.
Which company makes Microwave PCBs?
Several companies produce Microwave PCBs, including Rogers Corporation, Taconic Advanced Dielectric Division, Isola Group, and more. These companies specialize in providing high-performance materials and solutions for Microwave PCBs, catering to various industries such as telecommunications, radar, satellite communications, and others.
As a PCB manufacturing company, we have the capability to produce Microwave PCBs to meet the high-frequency application needs of our customers. We have advanced equipment and technology, and we possess the following capabilities:
- Material Selection and Procurement:We can provide a variety of materials suitable for Microwave PCBs, including Rogers materials, PTFE-based substrates, ceramic-filled PTFE composites, and more. We have established partnerships with multiple material suppliers to select the appropriate materials based on customer requirements.
- Design Support: Our experienced PCB design team can provide design support for Microwave PCBs. We are familiar with the principles and technical requirements of high-frequency PCB design and can optimize PCB layout, transmission line design, and more to ensure signal integrity and reliability.
- Manufacturing Process: We employ advanced manufacturing processes and equipment to precisely control the manufacturing process of PCBs. From material preparation, copper foil processing, imaging, etching, drilling, to surface treatment, each step follows strict standard operating procedures to ensure the quality and performance of the PCB.
- Quality Control:We strictly adhere to quality management systems to ensure the production of high-quality PCBs that meet customer requirements. Multiple quality inspections and tests are conducted during the manufacturing process, including visual inspection, dimension measurement, electrical testing, and more, to ensure stable and reliable product quality.
- Flexible Production Capacity: We have flexible production capabilities to meet the needs of different batch sizes and delivery schedules. Whether it’s small-batch customization or large-scale production, we can provide efficient solutions and ensure timely delivery.
With our company’s professional expertise and rich experience, we can provide customers with high-quality Microwave PCB solutions to meet their high-frequency application needs. We are committed to providing customers with the best products and services and working together to achieve business success.
What are the 7 qualities of good customer service?
Good customer service is characterized by several key qualities that contribute to a positive experience for customers. Here are seven qualities:
- Responsiveness: A good customer service team responds promptly to customer inquiries, questions, and concerns. This includes providing timely assistance and solutions to address customer needs, whether it’s through phone, email, live chat, or in-person interaction.
- Empathy: Empathy involves understanding and acknowledging the customer’s emotions, feelings, and perspective. Good customer service representatives show empathy by listening attentively, expressing understanding, and showing genuine concern for the customer’s situation or issue.
- Clear Communication:Effective communication is essential for good customer service. This includes using clear and concise language, actively listening to customers to understand their needs, and providing information or instructions in a way that is easy to understand.
- Problem-solving Skills: Good customer service representatives possess strong problem-solving skills to address customer issues and resolve conflicts effectively. They analyze situations, identify solutions, and take proactive steps to resolve problems to the customer’s satisfaction.
- Professionalism:Professionalism encompasses various aspects, including politeness, respectfulness, and maintaining a positive attitude when interacting with customers. Good customer service representatives conduct themselves professionally at all times, regardless of the situation or customer behavior.
- Product Knowledge: Having a deep understanding of the products or services offered allows customer service representatives to provide accurate information, answer questions, and offer relevant recommendations to customers. They stay informed about product updates, features, and benefits to better assist customers.
- Follow-up and Feedback: Good customer service involves following up with customers to ensure that their needs have been met and to gather feedback on their experience. This may include sending satisfaction surveys, asking for reviews or testimonials, and addressing any remaining concerns or issues.
By embodying these qualities, businesses can deliver exceptional customer service experiences that foster customer satisfaction, loyalty, and positive word-of-mouth recommendations.
FAQs (Frequently Asked Questions)
What are Microwave PCBs?
Microwave PCBs, also known as high-frequency PCBs, are specialized printed circuit boards designed to operate at microwave frequencies, typically above 1 GHz. They are used in applications such as telecommunications, radar systems, satellite communications, and medical devices.
What makes Microwave PCBs different from standard PCBs?
Microwave PCBs are designed with specific materials and techniques to ensure optimal performance at high frequencies. They typically use low-loss substrate materials, controlled impedance traces, and careful layout to minimize signal loss and maintain signal integrity.
What are the key considerations in designing Microwave PCBs?
Designing Microwave PCBs requires attention to factors such as substrate material selection, controlled impedance routing, transmission line design, grounding, and thermal management. These considerations are crucial for ensuring reliable performance at high frequencies.
What are common substrate materials used in Microwave PCBs?
Common substrate materials for Microwave PCBs include PTFE (polytetrafluoroethylene), ceramic-filled PTFE composites, and high-performance laminates like Rogers materials. These materials offer low dielectric constant (Dk) and low loss tangent (Df) to minimize signal loss.
How are Microwave PCBs manufactured?
The manufacturing process for Microwave PCBs involves steps such as material selection, copper cladding, photoresist application, exposure and development, etching, drilling, plating, surface finishing, quality control, and final inspection. Specialized techniques and equipment are used to ensure precise fabrication.
What are the applications of Microwave PCBs?
Microwave PCBs are used in a wide range of applications that require high-frequency operation, including telecommunications infrastructure, RF/microwave transmitters and receivers, radar systems, satellite communications, medical devices, aerospace, and defense systems.
What are the advantages of using Microwave PCBs?
The advantages of Microwave PCBs include high performance at high frequencies, low signal loss, excellent signal integrity, reliability, and suitability for demanding applications where precision and consistency are critical.
How can I ensure the quality of Microwave PCBs?
Ensuring the quality of Microwave PCBs involves working with reputable suppliers, specifying high-quality materials, adhering to industry standards and guidelines, conducting thorough testing and inspection, and partnering with experienced PCB manufacturers with expertise in high-frequency applications.