Microwave/Microtrace PCB Manufacturer
Microwave/Microtrace PCB Manufacturer,Microwave PCBs, also known as Microtrace PCBs, are specialized printed circuit boards engineered to handle high-frequency signals, typically ranging in the microwave frequency spectrum, often in the GHz range. These PCBs are meticulously designed to ensure precise signal transmission, minimal signal loss, and optimal performance in demanding applications. They feature carefully controlled trace geometry, impedance matching, and substrate material selection to meet the stringent requirements of high-frequency circuits. Microwave PCBs utilize advanced substrate materials such as Rogers, Teflon (PTFE), or high-frequency grade FR-4, chosen for their low dielectric loss and consistent electrical properties over a wide frequency range. They find extensive use in various industries, including aerospace, defense, telecommunications, automotive radar systems, medical devices, and consumer electronics, where high-frequency signal integrity and reliability are paramount. With their specialized design and manufacturing processes, Microwave PCBs play a crucial role in enabling the functionality of advanced electronic systems operating in the microwave frequency domain.
What is a Microwave PCB (Microtrace PCB)?
A Microwave PCB, often referred to as a Microstrip PCB or Microtrace PCB, is a type of printed circuit board specifically designed to handle microwave frequencies. These PCBs are used in various high-frequency applications such as radar systems, telecommunications equipment, satellite communication systems, and microwave ovens.
The design of Microwave PCBs involves careful consideration of the transmission lines, signal integrity, impedance matching, and electromagnetic interference (EMI) issues. Microstrip PCBs typically consist of a dielectric substrate material with conductive traces on one or both sides. These traces are often made of copper and are carefully laid out to control the impedance and propagation of microwave signals.
Microstrip PCBs offer several advantages for high-frequency applications:
- Low Losses:Microstrip PCBs can be designed to minimize signal loss, allowing efficient transmission of microwave signals.
- High Frequency Performance:These PCBs are optimized for high-frequency operation, allowing them to handle signals in the GHz range commonly used in microwave applications.
- Compact Design:Microstrip PCBs can be designed with a compact form factor, making them suitable for space-constrained applications.
- Customization:Designers can tailor Microstrip PCBs to meet specific impedance and performance requirements, ensuring optimal signal integrity.
Overall, Microwave PCBs play a crucial role in enabling the functionality of high-frequency electronic devices and systems by providing reliable signal transmission at microwave frequencies.
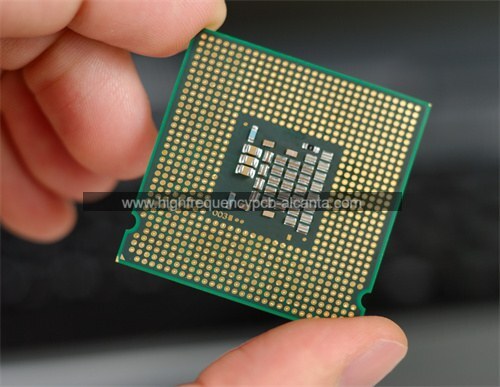
Microwave/Microtrace PCB Manufacturer
What are the Microwave PCB Design Guidelines?
Designing Microwave PCBs requires adherence to specific guidelines to ensure optimal performance at high frequencies. Here are some key guidelines:
- Substrate Selection:Choose a substrate material with low dielectric loss and consistent electrical properties over a wide frequency range. Common substrate materials include FR-4, Rogers, and PTFE-based materials like Teflon.
- Trace Width and Spacing:Calculate the trace width and spacing to achieve the desired characteristic impedance. Use tools or formulas specific to microstrip or stripline transmission line configurations.
- Ground Plane:Ensure a solid ground plane beneath the signal traces to provide shielding and reduce interference. A continuous ground plane helps maintain signal integrity by minimizing electromagnetic interference.
- Impedance Matching:Design traces and components to match the characteristic impedance of the transmission lines to minimize reflections and signal loss. Use impedance-controlled manufacturing processes to maintain consistency.
- Via Placement:Place vias strategically to maintain signal integrity and minimize signal distortion. Consider via stubs and their effects on signal quality, especially at high frequencies.
- Component Placement:Arrange components to minimize signal path lengths and reduce parasitic effects. Place critical components closer to each other and optimize the layout for signal integrity and EMI reduction.
- Edge Coupling:Minimize edge coupling between traces by maintaining sufficient distance between adjacent traces and by using guard traces or ground-signal-ground (GSG) configurations.
- High-Frequency Connectors:Choose connectors and interconnects designed for high-frequency applications with low insertion loss and impedance matching capabilities.
- Thermal Management:Consider thermal management strategies to dissipate heat generated by high-frequency components, as excessive heat can degrade performance.
- EMI Shielding:Incorporate EMI shielding techniques such as shielding cans, grounded copper pours, and ferrite beads to minimize electromagnetic interference and ensure compliance with regulatory standards.
- Simulation and Testing:Use electromagnetic simulation software to validate the design and predict the behavior of the PCB at high frequencies. Perform signal integrity analysis and physical testing to verify performance.
By following these guidelines, designers can create Microwave PCBs optimized for high-frequency applications with reliable signal transmission and minimal signal degradation.
What is the Microwave PCB Fabrication Process?
The fabrication process for Microwave PCBs involves several steps to ensure the precise creation of high-frequency circuits. Here’s an overview of the typical process:
- Design:The process begins with the creation of a detailed PCB design using specialized software. Designers consider factors such as trace width, spacing, substrate material, impedance matching, and component placement to optimize the PCB for high-frequency operation.
- Substrate Preparation:Select a substrate material suitable for high-frequency applications, such as Rogers, Teflon (PTFE), or FR-4 with a high-frequency grade. The substrate is typically supplied as sheets or panels and is cut to the desired size for the PCB.
- Preparation of Copper Foil:Copper foil is laminated onto one or both sides of the substrate material. The thickness and quality of the copper foil are critical for maintaining signal integrity and minimizing losses at high frequencies.
- Etching:Using photolithography techniques, a photoresist is applied to the copper foil, and the PCB design is transferred onto the photoresist using a mask or photomask. The PCB is then exposed to ultraviolet (UV) light, which hardens the exposed areas of the photoresist.
- Developing:The PCB is immersed in a developer solution that removes the unexposed areas of the photoresist, leaving behind the desired pattern of copper traces on the substrate.
- Etching: The PCB is submerged in an etchant solution, typically an acidic or alkaline solution, which selectively removes the exposed copper, leaving behind the desired circuit traces.
- Stripping: After etching, the remaining photoresist is removed from the PCB using a stripping solution, leaving clean copper traces on the substrate.
- Drilling:Holes are drilled into the PCB for component mounting and vias. High-precision drilling equipment is used to ensure accurate hole placement and dimensions.
- Plating:Through-hole vias and pads are plated with copper to provide conductivity and ensure reliable electrical connections between layers.
- Surface Finish:Surface finish processes such as HASL (Hot Air Solder Leveling), ENIG (Electroless Nickel Immersion Gold), or OSP (Organic Solderability Preservative) are applied to protect the exposed copper surfaces and facilitate soldering during assembly.
- Final Inspection: The finished PCB undergoes thorough inspection to verify dimensional accuracy, trace integrity, and overall quality. Automated optical inspection (AOI) and electrical testing may be performed to ensure compliance with design specifications.
- Assembly:Once the PCBs pass inspection, they are ready for component assembly, where electronic components are soldered onto the board using surface mount technology (SMT) or through-hole mounting techniques.
- Testing:The assembled PCBs undergo functional testing to verify proper operation and performance at high frequencies. This may include testing for signal integrity, impedance matching, and EMI compliance.
By following these fabrication steps carefully, manufacturers can produce Microwave PCBs optimized for high-frequency applications with precise signal transmission and minimal signal loss.
How do you manufacture a Microwave PCB (Microtrace PCB)?
Manufacturing a Microwave PCB, also known as a Microtrace PCB, involves several specialized processes to ensure precise fabrication and optimal performance at high frequencies. Here’s a step-by-step overview of the manufacturing process:
- Design Preparation:The process begins with the creation of a detailed PCB design using specialized software capable of handling high-frequency requirements. Designers consider factors such as trace width, spacing, substrate material, impedance matching, and component placement to optimize the PCB layout for microwave frequencies.
- Substrate Selection:Choose a substrate material suitable for high-frequency applications, such as Rogers, Teflon (PTFE), or FR-4 with a high-frequency grade. The substrate material should have low dielectric loss, consistent electrical properties, and good dimensional stability over a wide temperature range.
- Copper Foil Preparation:Copper foil is laminated onto one or both sides of the substrate material. The thickness and quality of the copper foil are critical for maintaining signal integrity and minimizing losses at high frequencies.
- Circuit Patterning:Using photolithography techniques, a photoresist is applied to the copper foil, and the PCB design is transferred onto the photoresist using a mask or photomask. The PCB is then exposed to ultraviolet (UV) light, which hardens the exposed areas of the photoresist.
- Etching:The PCB is submerged in an etchant solution, typically an acidic or alkaline solution, which selectively removes the exposed copper, leaving behind the desired circuit traces. Etching is carefully controlled to achieve precise trace dimensions and maintain signal integrity.
- Strip and Clean:After etching, the remaining photoresist is removed from the PCB using a stripping solution, leaving clean copper traces on the substrate. The PCB is then thoroughly cleaned to remove any residues or contaminants.
- Drilling:Precision drilling equipment is used to drill holes into the PCB for component mounting and vias. The drill holes must be accurately positioned and sized according to the PCB design specifications.
- Plating:Through-hole vias and pads are plated with copper to provide conductivity and ensure reliable electrical connections between layers. Plating is typically performed using electroplating or electroless plating processes.
- Surface Finish:Surface finish processes such as HASL (Hot Air Solder Leveling), ENIG (Electroless Nickel Immersion Gold), or OSP (Organic Solderability Preservative) are applied to protect the exposed copper surfaces and facilitate soldering during assembly.
- Final Inspection:The finished PCB undergoes thorough inspection to verify dimensional accuracy, trace integrity, and overall quality. Automated optical inspection (AOI) and electrical testing may be performed to ensure compliance with design specifications.
- Component Assembly:Once the PCBs pass inspection, they are ready for component assembly, where electronic components are soldered onto the board using surface mount technology (SMT) or through-hole mounting techniques.
- Testing:The assembled PCBs undergo functional testing to verify proper operation and performance at high frequencies. This may include testing for signal integrity, impedance matching, and EMI compliance.
By following these manufacturing processes carefully and using specialized equipment and materials, manufacturers can produce Microwave PCBs optimized for high-frequency applications with precise signal transmission and minimal signal loss.
How much should a Microwave PCB (Microtrace PCB) cost?
The cost of a Microwave PCB, or Microtrace PCB, can vary significantly depending on several factors, including the complexity of the design, the substrate material used, the number of layers, the size of the PCB, and the manufacturing volume. Here are some factors that influence the cost:
- Design Complexity:PCBs with intricate designs, high-density routing, and fine pitch components may require more advanced manufacturing processes and thus incur higher costs.
- Substrate Material:High-frequency substrate materials such as Rogers or Teflon (PTFE) tend to be more expensive than standard FR-4. The choice of substrate material depends on the specific requirements of the application.
- Number of Layers:Microwave PCBs may have multiple layers to accommodate complex routing and impedance control. Each additional layer adds to the manufacturing cost.
- Size of the PCB:Larger PCBs require more material and may also require specialized handling during manufacturing, leading to higher costs.
- Manufacturing Volume:Economies of scale apply in PCB manufacturing. Larger production volumes typically result in lower per-unit costs due to efficiencies in material utilization and manufacturing processes.
- Lead Time:Rush orders or expedited manufacturing may incur additional charges.
As a rough estimate, the cost of a Microwave PCB can range from tens to hundreds or even thousands of dollars per unit, depending on the factors mentioned above. For a more accurate cost estimate, it’s recommended to consult with PCB manufacturers and provide them with detailed specifications of your PCB design and manufacturing requirements. Many PCB manufacturers offer online quotation tools where you can input your design parameters to receive a cost estimate.
What is the Microwave PCB (Microtrace PCB) base material?
The base material for Microwave PCBs, including Microtrace PCBs, is typically chosen based on its electrical properties, dimensional stability, and suitability for high-frequency applications. Some common substrate materials used for Microwave PCBs include:
- Rogers Materials:Rogers Corporation produces a range of high-performance substrate materials specifically designed for high-frequency applications. These materials offer low dielectric loss, consistent electrical properties over a wide frequency range, and excellent dimensional stability.
- Teflon (PTFE)-Based Materials:Polytetrafluoroethylene (PTFE) substrates, commonly known by the brand name Teflon, are widely used for Microwave PCBs due to their low dielectric constant, low loss tangent, and excellent electrical properties at high frequencies.
- FR-4 with High-Frequency Grade:While FR-4 is a standard substrate material for PCBs, versions with a high-frequency grade are available to meet the requirements of Microwave PCBs. High-frequency FR-4 materials offer improved dielectric properties and are suitable for lower-frequency microwave applications.
- Ceramic Substrates: Certain types of ceramic materials, such as alumina (Al2O3) or aluminum nitride (AlN), are used for Microwave PCBs in applications requiring very high frequencies or stringent thermal management.
The choice of base material depends on the specific requirements of the application, including frequency range, signal integrity requirements, thermal considerations, and cost constraints. Designers select the substrate material that best balances these factors to achieve optimal performance in the final PCB design.
Which company makes Microwave PCBs (Microtrace PCBs)?
There are many companies specializing in the production of Microwave PCBs (Microtrace PCBs), some of which include Rogers Corporation, Isola Group, Taconic Advanced Dielectric Division, DuPont, and Arlon Electronic Materials. These companies offer a variety of high-performance substrate materials designed specifically for high-frequency applications such as radar systems, communication equipment, satellite communication systems, and more.
Our company is also a professional PCB manufacturer with extensive experience and advanced production equipment capable of producing Microwave PCBs (Microtrace PCBs). Our manufacturing processes adhere to international standards, and our engineering team provides professional design support and technical consultation to ensure that customers’ needs are met.
Our manufacturing process covers all aspects of PCB production, including design, material selection, process control, production, quality inspection, and more. We use advanced techniques and equipment to ensure that the quality and performance of the PCBs meet our customers’ requirements.
Our Microtrace PCBs use high-quality substrate materials such as Rogers or Teflon (PTFE), which exhibit excellent electrical performance and stability. With our experienced production team, we can precisely control the manufacturing process to ensure the quality and reliability of our products.
Regardless of our customers’ needs, we are committed to providing high-quality products and services. We are willing to collaborate with customers to develop customized Microwave PCB solutions to meet their specific application requirements.
What are the 7 qualities of good customer service?
Good customer service is characterized by several key qualities that help build positive relationships with customers and enhance their overall experience. Here are seven qualities of good customer service:
- Responsiveness:Good customer service involves promptly addressing customer inquiries, concerns, and requests. Responsiveness demonstrates attentiveness and a willingness to assist customers in a timely manner, which helps build trust and satisfaction.
- Empathy:Empathy involves understanding and empathizing with customers’ perspectives, feelings, and needs. Good customer service representatives listen actively, acknowledge customers’ emotions, and demonstrate compassion, which fosters rapport and loyalty.
- Clarity:Providing clear and concise communication is essential for good customer service. Clear communication ensures that customers understand information, instructions, and solutions effectively, reducing confusion and misunderstandings.
- Professionalism:Professionalism entails maintaining a courteous, respectful, and professional demeanor at all times when interacting with customers. Professional behavior instills confidence in customers and reflects positively on the company’s image and reputation.
- Knowledgeability: Good customer service representatives possess in-depth knowledge about the company’s products, services, policies, and procedures. Being knowledgeable enables representatives to provide accurate information, answer questions effectively, and offer valuable assistance to customers.
- Problem-solving:Effective problem-solving skills are crucial for resolving customer issues and concerns satisfactorily. Good customer service involves identifying root causes, exploring solutions, and taking proactive steps to address problems promptly and effectively.
- Follow-up:Following up with customers after resolving their issues or inquiries demonstrates a commitment to their satisfaction and reinforces a positive customer experience. Follow-up communication can involve checking in on customers’ satisfaction, providing additional assistance if needed, or seeking feedback for continuous improvement.
By embodying these qualities, businesses can deliver exceptional customer service experiences that foster customer loyalty, retention, and advocacy.
FAQs
What are Microwave PCBs?
Microwave PCBs, also known as Microtrace PCBs, are specialized printed circuit boards designed to handle high-frequency signals, typically in the microwave range (GHz). They are used in applications such as radar systems, telecommunications equipment, satellite communication systems, and microwave ovens.
What makes Microwave PCBs different from standard PCBs?
Microwave PCBs are optimized for high-frequency operation, with careful attention to factors such as trace geometry, impedance control, and substrate material selection. They often use specialized substrate materials with low dielectric loss and consistent electrical properties over a wide frequency range.
What are the key considerations in designing Microwave PCBs?
Designing Microwave PCBs involves considerations such as impedance matching, transmission line design, substrate material selection, signal integrity, and electromagnetic interference (EMI) management. Achieving precise impedance control and minimizing signal loss are critical for optimal performance.
What substrate materials are commonly used in Microwave PCBs?
Common substrate materials for Microwave PCBs include Rogers materials, Teflon (PTFE)-based materials, high-frequency grade FR-4, and certain ceramic materials. These materials offer low dielectric loss, consistent electrical properties, and excellent performance at high frequencies.
What are some applications of Microwave PCBs?
Microwave PCBs find applications in various industries, including aerospace, defense, telecommunications, automotive radar systems, medical devices, and consumer electronics. They are used wherever high-frequency signal transmission and precise control are required.
How do I choose the right manufacturer for Microwave PCBs?
When selecting a manufacturer for Microwave PCBs, consider factors such as their experience in high-frequency PCB fabrication, the quality of their materials and processes, adherence to industry standards, customization capabilities, and customer support services.
What are the typical lead times for manufacturing Microwave PCBs?
Lead times for manufacturing Microwave PCBs depend on factors such as the complexity of the design, substrate material availability, manufacturing volume, and the manufacturer’s production capacity. Lead times can range from a few days to several weeks, so it’s advisable to plan ahead.