Microvias | Blind Vias PCB Manufacturing
Microvias | Blind Vias PCB Manufacturing,Microvias and Blind Vias PCBs represent cutting-edge technology in printed circuit board design, revolutionizing the landscape of electronic devices. These PCBs feature intricate networks of tiny plated-through holes, known as microvias, and vias that connect the outer layers to inner layers without traversing the entire board, termed blind vias. Their compact size and high routing densities enable the creation of smaller, lighter, and more sophisticated electronic products, meeting the demands of today’s tech-savvy consumers.
Microvias and Blind Vias PCBs offer numerous advantages, including enhanced signal integrity, reduced signal distortion, and improved thermal management. They are particularly vital for high-performance applications in industries such as telecommunications, aerospace, and medical devices, where space constraints and reliability are paramount. By leveraging advanced fabrication techniques and high-quality materials, these PCBs empower engineers to push the boundaries of innovation, delivering products that are smaller, faster, and more efficient than ever before. In essence, Microvias | Blind Vias PCBs embody the convergence of precision engineering and cutting-edge technology, driving the next wave of electronic advancements.
What is a Microvias | Blind Vias PCB?
Microvias and blind vias are two features commonly found in modern printed circuit boards (PCBs) used in electronic devices.
- Microvias: Microvias are small plated-through holes used to establish connections between different layers of a PCB. They are typically very small in diameter, often less than 150 micrometers, and are used in high-density interconnect (HDI) PCB designs to save space and improve signal integrity. Microvias allow for more routing channels and higher interconnect densities compared to traditional through-hole vias.
- Blind Vias: Blind vias are a type of via that connects the outer layer(s) of a PCB to one or more inner layers, but does not penetrate through the entire board. Instead, they only extend to a specific depth, terminating at one of the inner layers. Blind vias are used when you need to make connections between specific layers without affecting the entire thickness of the PCB. They are often employed in multilayer PCBs to increase routing density and reduce signal distortion.
When these two features are combined, you get a Microvias Blind Vias PCB, which is a PCB that utilizes both microvias and blind vias in its design. This type of PCB is commonly used in high-density and high-performance electronic applications where space constraints are ritical, and signal integrity is essential.
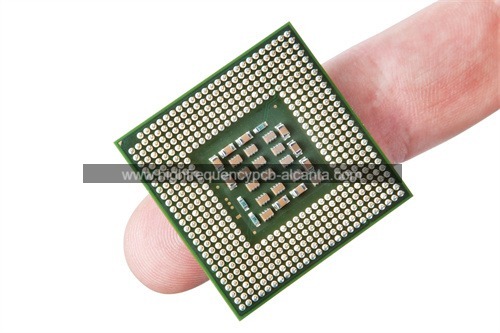
Microvias | Blind Vias PCB Manufacturing
What are the Microvias | Blind Vias PCB Design Guidelines?
Microvias and blind vias PCB design guidelines help ensure the successful implementation of these features in a printed circuit board design. Here are some general guidelines:
- Aspect Ratio: The aspect ratio of microvias and blind vias should be kept within acceptable limits. Aspect ratio is the ratio of the depth of the hole to its diameter. Higher aspect ratios can lead to manufacturing challenges such as plating issues and drilling difficulties. Typically, aspect ratios for microvias and blind vias should be limited to around 1:1 to 1.5:1.
- Minimum Sizes: Define minimum sizes for microvias and blind vias based on manufacturing capabilities and reliability requirements. Microvias are typically smaller than traditional vias, often ranging from 75 to 150 micrometers in diameter. Blind vias may have larger diameters due to the need for higher aspect ratios.
- Layer Stacking: Consider the layer stacking and placement of blind vias carefully to ensure proper connectivity between the desired layers without interference with adjacent traces or vias. Properly aligning blind vias with microvias and signal traces can help maintain signal integrity and reduce crosstalk.
- Annular Ring and Pad Sizes: Maintain adequate annular ring sizes and pad sizes around microvias and blind vias to ensure reliable connections during fabrication and assembly processes. Adequate spacing between vias and other circuit elements should also be maintained to prevent electrical shorting.
- Plating Thickness: Specify appropriate plating thickness for microvias and blind vias to ensure good electrical conductivity and reliability. Insufficient plating thickness can lead to signal attenuation and reliability issues, while excessive plating thickness can cause manufacturing defects.
- Materials Selection: Choose suitable materials for the substrate and conductive layers of the PCB to accommodate microvias and blind vias. Substrate materials with good dimensional stability and thermal properties are essential for maintaining the integrity of microvias and blind vias during fabrication and operation.
- Manufacturing Tolerances: Consider manufacturing tolerances and capabilities when designing microvias and blind vias to ensure that the final PCB meets specifications and can be reliably manufactured within cost-effective limits.
- Signal Integrity Analysis: Perform signal integrity analysis, including impedance calculations and crosstalk simulations, to evaluate the impact of microvias and blind vias on signal performance and mitigate any potential issues early in the design process.
By following these guidelines, designers can optimize the implementation of microvias and blind vias in PCB designs to achieve high performance, reliability, and manufacturability.
What is the Microvias | Blind Vias PCB Fabrication Process?
The fabrication process for Microvias and Blind Vias PCBs involves several steps, each crucial for achieving high-quality boards with these advanced features. Here’s a general outline of the process:
- Design Stage:
– PCB designers create the circuit schematic and layout, incorporating microvias and blind vias where necessary.
– Design guidelines specific to microvias and blind vias are followed to ensure manufacturability and reliability.
- Material Selection:
– High-quality laminate materials suitable for microvia fabrication are chosen. These materials typically have a low dielectric constant and are compatible with advanced fabrication techniques.
– Copper foils of appropriate thicknesses are selected for the PCB layers.
- Preparation:
– The chosen substrate material is cleaned thoroughly to remove any contaminants.
– Copper foils are laminated onto the substrate material.
- Drilling:
– Laser drilling or mechanical drilling processes are used to create the microvias and blind vias. Laser drilling is often preferred for its precision and ability to create very small holes.
– Advanced control systems ensure accurate drilling depths for blind vias.
- Plating:
– After drilling, the vias are plated with a conductive material, typically copper, to establish electrical connections between layers.
– The plating process ensures that the vias are properly filled and have good conductivity.
- Lamination:
– Multiple layers of the PCB are laminated together, including the layers containing microvias and blind vias.
– Pressure and heat are applied during lamination to bond the layers together securely.
- Etching:
– The outer layers of the PCB are etched to remove excess copper and define the circuit traces.
– Etching is done using chemical processes or by using a CNC milling machine for precision.
- 8. Surface Finish:
– Surface finish processes such as HASL (Hot Air Solder Leveling), ENIG (Electroless Nickel Immersion Gold), or immersion silver are applied to protect exposed copper and provide solderability.
- Quality Control:
– The finished PCBs undergo rigorous quality control inspections to ensure they meet design specifications and industry standards.
– Tests may include electrical continuity testing, dimensional inspections, and thermal cycling tests.
- Final Inspection and Packaging:
– Once quality control checks are completed and the PCBs are deemed acceptable, they are prepared for shipping by packaging them appropriately for protection during transit.
By following these steps carefully and employing advanced manufacturing techniques, PCB fabricators can produce high-quality Microvias and Blind Vias PCBs that meet the demanding requirements of modern electronic devices.
How do you manufacture a Microvias | Blind Vias PCB?
Manufacturing a Microvias | Blind Vias PCB involves several specialized processes to create the intricate vias and ensure the integrity of the circuitry. Here’s a step-by-step guide to the manufacturing process:
- Design and Layout:
– PCB designers create the circuit schematic and layout, incorporating Microvias and Blind Vias as needed.
– Design guidelines specific to Microvias and Blind Vias are followed to ensure manufacturability and reliability.
- Material Selection:
– High-quality laminate materials suitable for Microvias fabrication are chosen. These materials typically have a low dielectric constant and are compatible with advanced fabrication techniques.
– Copper foils of appropriate thicknesses are selected for the PCB layers.
- Preparation:
– The chosen substrate material is cleaned thoroughly to remove any contaminants.
– Copper foils are laminated onto the substrate material.
- Drilling:
– Advanced laser drilling or mechanical drilling processes are used to create the Microvias and Blind Vias. Laser drilling is often preferred for its precision and ability to create very small holes.
– Computer-controlled drilling machines ensure accurate positioning and depth control for Microvias and Blind Vias.
- Desmear and Plating:
– After drilling, the vias are desmeared to remove any debris or residues left from the drilling process.
– The vias are then plated with a conductive material, typically copper, to establish electrical connections between layers.
– The plating process ensures that the vias are properly filled and have good conductivity.
- Lamination:
– Multiple layers of the PCB are laminated together, including the layers containing Microvias and Blind Vias.
– Pressure and heat are applied during lamination to bond the layers together securely.
- Etching:
– The outer layers of the PCB are etched to remove excess copper and define the circuit traces.
– Etching is done using chemical processes or by using a CNC milling machine for precision.
- Surface Finish:
– Surface finish processes such as HASL (Hot Air Solder Leveling), ENIG (Electroless Nickel Immersion Gold), or immersion silver are applied to protect exposed copper and provide solderability.
- Quality Control:
– The finished PCBs undergo rigorous quality control inspections to ensure they meet design specifications and industry standards.
– Tests may include electrical continuity testing, dimensional inspections, and thermal cycling tests.
- Final Inspection and Packaging:
– Once quality control checks are completed and the PCBs are deemed acceptable, they are prepared for shipping by packaging them appropriately for protection during transit.
By following these steps carefully and employing advanced manufacturing techniques, PCB manufacturers can produce high-quality Microvias | Blind Vias PCBs that meet the demanding requirements of modern electronic devices.
How much should a Microvias | Blind Vias PCB cost?
The cost of manufacturing a Microvias | Blind Vias PCB can vary significantly depending on various factors such as the complexity of the design, the number of layers, the size of the board, the choice of materials, the quantity ordered, and the manufacturing technology used. However, due to the specialized nature of these PCBs, they typically incur higher manufacturing costs compared to standard PCBs without microvias or blind vias.
Here are some factors that can influence the cost:
- Design Complexity: PCBs with intricate designs containing numerous microvias and blind vias may require more time and resources for fabrication, leading to higher costs.
- Number of Layers: Multi-layer PCBs with microvias and blind vias tend to be more expensive than single or double-layer boards due to increased fabrication complexity.
- Material Selection: High-quality laminate materials suitable for microvia fabrication may be more expensive than standard PCB materials. Additionally, the cost of copper foils and plating materials can impact overall costs.
- Manufacturing Technology: Advanced drilling and plating technologies required for microvias and blind vias fabrication may involve higher setup costs and specialized equipment, contributing to increased manufacturing expenses.
- Order Quantity: Larger production runs often result in lower per-unit costs due to economies of scale. However, prototype or small-batch orders may incur higher costs per unit.
- Lead Time: Expedited production schedules or quick-turn services typically incur additional fees, affecting the overall cost of the PCBs.
- Additional Services: Surface finish options, such as ENIG (Electroless Nickel Immersion Gold) or immersion silver, may add to the cost. Similarly, additional testing, such as impedance testing or thermal cycling, can increase the overall cost of the PCBs.
- Supplier and Location: PCB fabrication costs can vary among different manufacturers and regions due to factors such as labor costs, overhead expenses, and shipping fees.
Given these variables, it’s challenging to provide an exact cost without specific details about the PCB requirements. Generally, it’s recommended to obtain quotes from multiple PCB manufacturers to compare prices and ensure the best value for your specific project needs.
What is Microvias | Blind Vias PCB base material?
The base material used for Microvias | Blind Vias PCBs typically consists of high-quality laminate materials that offer excellent electrical performance, mechanical strength, and thermal stability. These materials are selected based on the specific requirements of the PCB design and fabrication process. Some commonly used base materials include:
- FR-4 (Flame Retardant-4): FR-4 is a widely used epoxy-based laminate material reinforced with glass fibers. It offers good mechanical strength, dimensional stability, and electrical insulation properties. FR-4 is commonly used for standard PCBs as well as those with microvias and blind vias.
- High-Speed/High-Frequency Materials: For applications requiring high-speed signal transmission or high-frequency operation, specialized laminate materials with lower dielectric constants and controlled impedance properties may be used. Examples include materials like Rogers RO4000 series, Isola FR408, and Nelco N4000-13.
- Polyimide (PI): Polyimide-based materials, such as Kapton, offer exceptional thermal stability and are well-suited for applications involving high-temperature environments. Polyimide-based materials are often used in flexible PCBs that incorporate microvias and blind vias.
- PTFE (Polytetrafluoroethylene): PTFE-based materials, such as Teflon, provide excellent electrical properties, low dielectric loss, and high-temperature stability. These materials are commonly used in high-frequency and microwave applications where superior signal integrity is critical.
- Composite Materials: Some advanced PCB designs may require composite materials that combine different substrate materials to achieve specific performance characteristics, such as enhanced thermal conductivity or reduced signal loss.
The selection of the base material depends on factors such as the desired electrical performance, thermal requirements, mechanical properties, and cost considerations. PCB designers and manufacturers carefully evaluate these factors to choose the most suitable base material for each Microvias | Blind Vias PCB project.
Which company makes Microvias | Blind Vias PCB?
Microvias and blind vias PCBs are essential components in modern electronic devices, enabling high-density wiring and signal transmission. Currently, many companies are capable of manufacturing microvias and blind vias PCBs, including Foxconn, Semco, Jiangsu Zhongyuan Electronics, and Fuhua Hua. These companies possess advanced technology and equipment to meet the demands of various complex PCB designs.
Our company is also a professional PCB manufacturer with years of experience and rich technical strength. Our production processes and equipment meet the requirements for manufacturing microvias and blind vias PCBs. We have advanced laser drilling equipment and high-precision control systems to produce tiny apertures and intricate wiring accurately. Furthermore, our production procedures strictly adhere to international standards to ensure reliable product quality.
Our team consists of experienced engineers and technical personnel capable of providing professional design advice and technical support. Whether it’s a simple double-layer PCB or a complex multi-layer PCB, we can provide customized solutions tailored to our customers’ needs. We prioritize communication with our customers, striving to meet their requirements and ensure timely delivery of high-quality products.
As a trusted PCB manufacturer, we are committed to providing customers with excellent products and services. If you are seeking a reliable partner for manufacturing microvias and blind vias PCBs, please contact us, and we will be dedicated to offering you support and assistance.
What are the 7 qualities of good customer service?
Good customer service is characterized by several key qualities that contribute to positive experiences for customers. These qualities include:
- Responsiveness: Good customer service involves promptly addressing customer inquiries, concerns, or issues. Being responsive demonstrates attentiveness to customers’ needs and helps build trust and satisfaction.
- Empathy: Empathy involves understanding and acknowledging customers’ emotions, concerns, and perspectives. Showing empathy helps create a connection with customers and makes them feel valued and understood.
- Clear Communication: Effective communication is essential in providing good customer service. Clear and concise communication helps ensure that customers understand information, instructions, or solutions provided, leading to smoother interactions and resolutions.
- Problem-solving Skills: Good customer service representatives possess strong problem-solving skills to effectively address customer issues or complaints. They identify root causes, explore solutions, and resolve problems in a timely and satisfactory manner.
- Product Knowledge: Having comprehensive knowledge about products or services allows customer service representatives to provide accurate information, answer questions, and offer helpful recommendations. A thorough understanding of offerings enhances credibility and builds customer confidence.
- Professionalism: Professionalism involves maintaining a courteous, respectful, and professional demeanor in all customer interactions. Treating customers with respect and courtesy, regardless of the situation, fosters positive relationships and reflects well on the company.
- Follow-up and Follow-through: Good customer service includes following up with customers to ensure that their issues have been resolved satisfactorily. Additionally, following through on commitments, promises, or resolutions demonstrates reliability and commitment to customer satisfaction.
By embodying these qualities, organizations can deliver exceptional customer service experiences that foster loyalty, positive word-of-mouth, and long-term success.
FAQs
What are Microvias and Blind Vias in PCBs?
Microvias are small plated-through holes used for establishing connections between different layers of a PCB. Blind vias, on the other hand, are vias that connect the outer layer(s) of a PCB to one or more inner layers without penetrating the entire board.
What are the benefits of using Microvias and Blind Vias in PCBs?
Microvias and blind vias enable higher routing densities, improved signal integrity, and reduced PCB size. They are particularly beneficial for high-density interconnect (HDI) PCB designs and applications where space constraints are critical.
What are the design considerations for Microvias | Blind Vias PCBs?
Design considerations include the size and placement of microvias, routing constraints, layer stackup, via aspect ratio, and manufacturing tolerances. It’s essential to adhere to design guidelines to ensure manufacturability and reliability.
What materials are suitable for Microvias | Blind Vias PCB fabrication?
High-quality laminate materials, such as FR-4, high-speed materials, polyimide, and PTFE-based materials, are commonly used for Microvias | Blind Vias PCB fabrication. The choice of material depends on specific requirements such as electrical performance and thermal stability.
What fabrication processes are involved in manufacturing Microvias | Blind Vias PCBs?
Fabrication processes include drilling, plating, lamination, etching, surface finish, and quality control. Advanced drilling techniques, such as laser drilling, are often used for creating microvias, while blind vias require precise depth control during drilling.
What are the typical applications of Microvias | Blind Vias PCBs?
Microvias | Blind Vias PCBs find applications in various industries, including telecommunications, aerospace, medical devices, consumer electronics, and automotive electronics, where compact size, high performance, and reliability are essential.
How can I ensure the reliability and quality of Microvias | Blind Vias PCBs?
To ensure reliability and quality, it’s crucial to work with experienced PCB manufacturers who have the expertise, advanced technology, and quality control processes specific to Microvias | Blind Vias PCB fabrication. Additionally, adhering to design guidelines and conducting thorough testing can help ensure the desired performance and reliability.