Microvia Substrates Manufacturing
Microvia Substrates Manufacturing,The cost of microvia substrates varies depending on factors such as substrate material, design complexity, number of layers, and production volume. Generally, microvia substrates tend to be more expensive than traditional PCBs due to their higher precision and specialized manufacturing techniques. Factors such as the choice of substrate material, including high-performance materials or those with special properties, can significantly impact costs. Additionally, designs with intricate layouts, dense routing, or smaller microvias may require more sophisticated manufacturing processes, contributing to higher production costs. Production volume also plays a role, with higher volumes often leading to lower unit costs due to economies of scale. However, special features like blind or buried vias, controlled impedance, or specific surface finishes may incur additional expenses. Overall, while microvia substrates offer numerous benefits such as high-density interconnections and improved signal integrity, it’s essential to consider the associated costs and explore strategies for cost optimization without compromising quality or performance.
What is a Microvia Substrate?
A microvia substrate is a type of substrate used in electronic packaging, particularly in the manufacturing of printed circuit boards (PCBs). Microvia substrates are characterized by their small diameter vias, which are used to connect different layers of the PCB. These vias are typically less than 150 micrometers (µm) in diameter.
Microvia substrates offer several advantages over traditional PCB substrates, including:
- High density: Microvia substrates allow for a higher density of interconnections between components, leading to smaller and more compact electronic devices.
- Improved signal integrity: The smaller size of microvias reduces signal loss and impedance mismatch, improving the overall signal integrity of the PCB.
- Enhanced thermal performance: Microvia substrates can dissipate heat more effectively than traditional substrates, making them suitable for high-performance applications.
- Better reliability: Microvia technology enables the creation of more reliable and robust PCBs with fewer defects and failures.
Microvia substrates are commonly used in applications where space constraints, high-speed signal transmission, and reliability are critical, such as in mobile devices, automotive electronics, and high-performance computing systems.
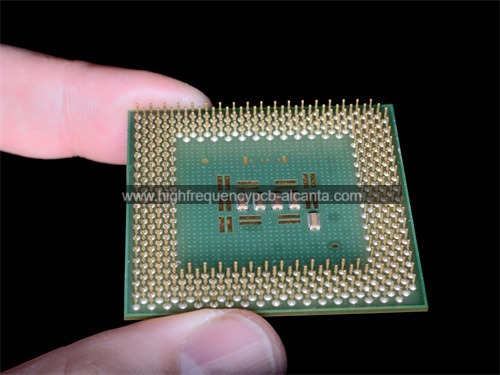
Microvia Substrates Manufacturing
What are the Microvia Substrate Design Guidelines?
Microvia substrate design guidelines are a set of recommendations and best practices used by PCB designers to ensure the successful implementation of microvia technology in PCB layouts. These guidelines aim to optimize signal integrity, reliability, manufacturability, and overall performance of the PCB. Some common microvia substrate design guidelines include:
- Minimum feature size: Ensure that the minimum feature size, including the diameter of microvias and the spacing between them, adheres to the capabilities of the fabrication process.
- Aspect ratio: Maintain an appropriate aspect ratio for microvias (the ratio of their depth to diameter) to facilitate reliable plating and minimize the risk of defects such as voids or cracks.
- Layer stackup: Design the layer stackup of the PCB considering the number of layers, signal integrity requirements, and thermal management needs. Proper layer arrangement can optimize signal transmission and minimize signal interference.
- Signal routing: Carefully plan the routing of high-speed signals to minimize impedance mismatches, crosstalk, and signal reflections. Use microvias for vias-in-pad configurations to reduce signal path length and improve signal integrity.
- Via placement: Strategically place microvias to optimize signal paths, minimize signal distortion, and ensure adequate clearance from other components and traces.
- Thermal management: Consider thermal management techniques such as the placement of thermal vias or copper fills to dissipate heat efficiently and prevent overheating of components.
- Design for manufacturability (DFM): Follow DFM guidelines to ensure that the design can be manufactured reliably and cost-effectively. This includes considering the capabilities of the chosen fabrication process and any specific requirements or limitations associated with microvia technology.
- Material selection: Choose appropriate substrate materials with suitable dielectric properties, thermal conductivity, and reliability characteristics to meet the performance requirements of the PCB.
- Testing and validation: Implement testing and validation procedures to verify the performance and reliability of the microvia substrate design, both during prototyping and mass production stages.
By adhering to these design guidelines, PCB designers can effectively leverage microvia technology to achieve high-density interconnections, improved signal integrity, and overall enhanced performance in electronic devices.
What is the Microvia Substrate Fabrication Process?
The fabrication process of microvia substrates involves several steps to create the intricate interconnection structure required for high-density electronic packaging. Here’s an overview of the typical microvia substrate fabrication process:
- Substrate Preparation: The process begins with the preparation of the substrate material, usually a laminate composed of layers of copper and insulating material (such as epoxy resin or polyimide). The substrate material is typically in the form of large panels or sheets.
- Circuit Patterning: A layer of copper foil is bonded onto the substrate material. The desired circuit patterns are then transferred onto the copper foil layer using photolithography or direct imaging techniques. This involves applying a photoresist layer onto the copper foil, exposing it to UV light through a mask with the circuit pattern, and then developing the exposed resist to leave behind the desired copper traces.
- Via Drilling: Small-diameter holes, known as microvias, are drilled through the substrate material at locations where interconnections are required between different layers of the PCB. Microvias are typically created using laser drilling or mechanical drilling processes, depending on the substrate material and design requirements.
- Via Cleaning and Surface Treatment: After drilling, the microvias are cleaned to remove any debris or contaminants that may have accumulated during the drilling process. The surfaces of the microvias are then treated to promote adhesion and facilitate subsequent plating processes.
- Via Plating: A thin layer of conductive material, such as copper or electroless nickel, is deposited onto the walls of the microvias through an electroplating or electroless plating process. This forms the conductive pathways that establish electrical connections between different layers of the PCB.
- Circuit Lamination: Additional layers of substrate material and copper foil may be laminated onto the previously patterned layers to build up the required number of PCB layers. Each additional layer may undergo the same circuit patterning, via drilling, cleaning, surface treatment, and plating processes as described above.
- Final Processing: Once all layers and interconnections are formed, the fabricated panel undergoes final processing steps, including etching, solder mask application, legend printing, and surface finish application (such as immersion gold or HASL) to protect the exposed copper traces, provide insulation between conductive traces, and improve solderability.
- Quality Control and Testing: Throughout the fabrication process, various quality control measures and testing procedures are implemented to ensure that the microvia substrate meets the required specifications for dimensional accuracy, electrical performance, reliability, and overall quality.
By following these steps, manufacturers can produce microvia substrates with precise interconnections and high-density packaging capabilities suitable for advanced electronic applications.
How do you manufacture a Microvia Substrate?
Manufacturing a Microvia Substrate involves several specialized steps to create small-diameter holes (microvias) that connect different layers of the substrate. Here’s an overview of the process:
- Substrate Preparation:
– Begin with a base material, often a high-performance substrate such as FR-4, FR-408, or a specialized material like polyimide or ceramic.
– Clean the substrate to remove any contaminants that could affect the manufacturing process.
- Lamination:
– Stack multiple layers of substrate material according to the design requirements.
– Apply heat and pressure to bond the layers together, forming a solid composite structure.
- Drilling:
– Use a laser drilling or mechanical drilling process to create small-diameter holes, typically less than 150 microns in diameter, through the substrate material.
– Ensure precise alignment and depth control to achieve accurate placement of the microvias.
- Desmear and Surface Preparation:
– After drilling, the substrate surface may contain residues or burrs from the drilling process.
– Desmear the substrate to remove any debris and clean the surface for subsequent processing.
- Microvia Plating:
– Plate the microvias with a thin layer of conductive material, typically copper, to provide electrical connections between different layers of the substrate.
– Use electroplating or electroless plating processes to deposit the copper onto the walls of the microvias.
- Conductor Patterning:
– Apply a photoresist material to the substrate surface and expose it to UV light through a photomask, defining the desired conductor patterns.
– Develop the photoresist to remove the unexposed areas, leaving behind the patterned resist.
- Copper Etching:
– Use chemical etchants to selectively remove the exposed copper, leaving behind the desired conductor traces on the substrate surface.
– Rinse and clean the substrate to remove any remaining etchant residues.
- Surface Finish:
– Apply a surface finish to the substrate, such as immersion gold, HASL (Hot Air Solder Leveling), or OSP (Organic Solderability Preservatives), to protect the copper traces and provide solderability.
- Final Inspection:
– Conduct visual inspection and electrical testing to ensure that the microvia substrate meets the required specifications for quality and performance.
- Packaging and Shipping:
– Package the finished microvia substrates and prepare them for shipping to the customer or assembly facility.
Throughout the manufacturing process, quality control measures are implemented to ensure that the microvia substrates meet the required specifications for performance, reliability, and manufacturability. Collaboration between the substrate manufacturer and the customer is essential to address any specific design requirements and ensure the successful production of the microvia substrate.
How much should a Microvia Substrate cost?
The cost of a microvia substrate can vary significantly depending on several factors such as the size and complexity of the PCB, the number of layers, the substrate material, the manufacturing process used, and the desired quality and performance specifications. Generally, microvia substrates tend to be more expensive than traditional PCBs due to their higher precision and specialized manufacturing techniques.
On average, the cost of a microvia substrate can range from a few dollars to several hundred dollars per square foot or per unit, with more complex and advanced designs typically commanding higher prices. For large-volume orders, manufacturers may offer discounts based on economies of scale.
It’s essential for PCB designers and manufacturers to carefully consider cost implications during the design phase and to work closely with suppliers to optimize the design for cost-effectiveness without compromising quality and performance.
Additionally, factors such as material availability, market demand, and technological advancements can also influence the cost of microvia substrates over time. Therefore, it’s advisable to obtain quotes from multiple suppliers and evaluate the cost-effectiveness of different options based on the specific requirements of the project.
What is Microvia Substrate base material?
The base material used for microvia substrates can vary depending on the specific requirements of the application, but it typically consists of a laminate composed of layers of copper and insulating material. The choice of base material is crucial for achieving desired electrical, mechanical, and thermal properties in the final PCB.
Common base materials for microvia substrates include:
- FR-4 Epoxy: FR-4 (Flame Retardant 4) is a widely used substrate material composed of woven fiberglass impregnated with epoxy resin. It offers good electrical insulation properties, mechanical strength, and affordability, making it suitable for many general-purpose applications.
- High-Frequency Laminates: For applications requiring enhanced signal integrity at high frequencies, high-frequency laminates such as polytetrafluoroethylene (PTFE) or polyimide-based materials may be used. These materials have low dielectric constants and low loss tangents, enabling better signal transmission performance.
- Rogers® Materials: Rogers Corporation produces a range of specialty laminates designed specifically for high-frequency and high-performance applications. These materials offer excellent electrical properties, dimensional stability, and reliability, making them suitable for demanding RF/microwave, automotive, and aerospace applications.
- BT Epoxy: BT (Bismaleimide Triazine) epoxy is another type of substrate material known for its high thermal stability and low coefficient of thermal expansion (CTE). BT epoxy laminates are commonly used in applications requiring reliable thermal performance, such as in high-power electronics or harsh operating environments.
- Flexible Substrates: In some cases, flexible substrates made of polyimide or polyester film may be used for microvia applications where flexibility or conformal shapes are required, such as in wearable electronics or flexible displays.
The selection of the base material depends on various factors including electrical performance requirements, thermal management needs, cost considerations, and environmental factors. PCB designers and engineers carefully evaluate these factors to choose the most appropriate base material for their specific application.
Which company makes Microvia Substrates?
There are many companies currently specializing in the manufacturing of microvia substrates, including well-known companies such as TTM Technologies in the United States, Hitachi Chemical in Japan, Unimicron in Taiwan, and CTEC in China. These companies have extensive experience and advanced manufacturing technologies in the field of microvia substrates, capable of meeting various needs of different customers.
As a professional electronic manufacturing service provider, our company also has the capability to produce microvia substrates. We possess advanced production equipment and a skilled technical team to design and manufacture high-quality microvia substrates according to customer requirements. Our production processes strictly adhere to industry standards, ensuring stable and reliable product quality.
Regarding the cost of microvia substrates, our company can provide customized quotations based on the specific needs and project scale of customers. The cost of microvia substrates is influenced by various factors, including substrate material, number of layers, design complexity, and manufacturing processes. Generally, microvia substrates tend to have higher costs due to the need for higher precision and specialized technologies during manufacturing. However, through the expertise of our professional team and efficient management, we can offer competitive prices to provide customers with cost-effective solutions for microvia substrates.
We are committed to providing customers with high-quality products and services to meet their needs and achieve mutual success. Customers are welcome to contact us for more information about microvia substrate manufacturing and customized quotations.
Qualities of Good Customer Service:
Good customer service is characterized by several key qualities that contribute to positive interactions between a company and its customers. Here are some of the qualities of good customer service:
- Promptness: Good customer service involves responding to customer inquiries, concerns, or issues in a timely manner. This includes acknowledging messages or calls promptly and providing timely resolutions to problems.
- Empathy: Empathy involves understanding and acknowledging the customer’s feelings, concerns, and perspectives. Customer service representatives should listen actively, show genuine concern, and demonstrate empathy towards customers’ needs and situations.
- Clarity and Transparency: Providing clear and transparent communication is essential in good customer service. Customers should be given accurate and understandable information regarding products, services, pricing, policies, and procedures.
- Professionalism: Good customer service requires professionalism in interactions with customers. This includes being courteous, respectful, and maintaining a positive attitude, even in challenging situations.
- Knowledge and Expertise: Customer service representatives should possess sufficient knowledge and expertise about the company’s products, services, and policies to assist customers effectively. They should be able to answer questions, provide guidance, and offer solutions to customer issues competently.
- Problem-solving Skills: Good customer service involves effectively addressing customer concerns and resolving problems in a satisfactory manner. This may require critical thinking, creativity, and the ability to find appropriate solutions tailored to each customer’s situation.
- Consistency: Consistency in service delivery is important for building trust and reliability with customers. Good customer service should be consistent across all channels and interactions, ensuring that customers receive the same level of quality service every time.
- Personalization: Tailoring interactions and solutions to meet the individual needs and preferences of each customer can enhance the customer experience. Personalization involves recognizing and acknowledging customers as individuals and treating them accordingly.
- Follow-up and Feedback: Following up with customers after resolving their issues or completing a transaction shows that their satisfaction is important. Good customer service also involves actively seeking feedback from customers to identify areas for improvement and make necessary adjustments.
- Going the Extra Mile: Going above and beyond to exceed customer expectations can leave a lasting positive impression. Whether it’s offering additional assistance, providing special accommodations, or showing appreciation for customer loyalty, going the extra mile demonstrates a commitment to customer satisfaction.
Overall, good customer service is about building strong relationships with customers by delivering exceptional experiences that meet or exceed their expectations, ultimately fostering customer loyalty and advocacy for the brand.
FAQs
What factors influence the cost of microvia substrates?
Several factors can affect the cost of microvia substrates, including the substrate material, number of layers, design complexity, dimensions, surface finish, and production volume.
How does the substrate material affect the cost?
The choice of substrate material can significantly impact the cost of microvia substrates. Materials with higher performance characteristics or special properties may be more expensive than standard materials.
Does the number of layers affect the cost?
Yes, the number of layers in the microvia substrate directly affects the cost. More layers typically mean more complex manufacturing processes and increased material costs.
What role does design complexity play in cost?
Designs with intricate layouts, dense routing, and smaller microvias may require more sophisticated manufacturing techniques, which can increase production costs.
How does production volume affect the cost?
Generally, higher production volumes can lead to economies of scale, resulting in lower unit costs. Conversely, lower volumes may incur higher costs per unit due to setup and tooling expenses.
Are there additional costs for special features or finishes?
Yes, special features such as blind or buried vias, controlled impedance, and specific surface finishes (e.g., immersion gold) may incur additional costs due to their complexity or specialized processes.
Do expedited lead times affect the cost?
Expedited lead times often require prioritized production schedules and additional resources, which may result in higher costs compared to standard lead times.
Can I request a quote for microvia substrate cost?
Yes, most manufacturers offer quoting services where customers can provide specifications and receive estimates tailored to their project requirements.
Are there any cost-saving strategies for microvia substrates?
Opting for standard materials and surface finishes, designing for manufacturability, consolidating layers where possible, and optimizing panelization can help reduce costs without compromising quality.