Microvia Package Substrate Manufacturer
Microvia Package Substrate Manufacturer,Microvia Package Substrates are advanced circuit boards designed with microvias, tiny holes drilled with lasers to create interconnections between different layers. These substrates enable high-density packaging of semiconductor chips and other components, optimizing space utilization and enhancing electrical performance. Microvia technology supports fine-pitch designs and facilitates shorter signal paths, reducing signal loss and improving signal integrity. They are crucial in applications requiring miniaturization and high-speed performance, such as mobile devices, computing systems, and high-frequency communication equipment. Microvia Package Substrates are engineered with precision to meet stringent reliability standards, ensuring stable operation in challenging operating conditions.
What is a Microvia Package Substrate?
A Microvia Package Substrate refers to a type of printed circuit board (PCB) substrate that utilizes microvia technology. Microvias are small, laser-drilled holes with diameters typically less than 150 micrometers, used to create interconnections between different layers of the PCB. These substrates are crucial in modern electronics, especially in densely packed and high-performance applications like mobile devices and advanced semiconductor packaging.
The key advantages of Microvia Package Substrates include their ability to support higher interconnect densities, reduced signal loss at high frequencies, and improved thermal management. They contribute to miniaturization efforts in electronics by enabling finer pitch designs and more complex circuitry layouts. Manufacturers use advanced materials like high-frequency laminates and thermally conductive substrates to optimize performance for specific applications.
In summary, Microvia Package Substrates represent a significant advancement in PCB technology, offering enhanced reliability, performance, and efficiency in electronic devices demanding compact and high-speed designs.
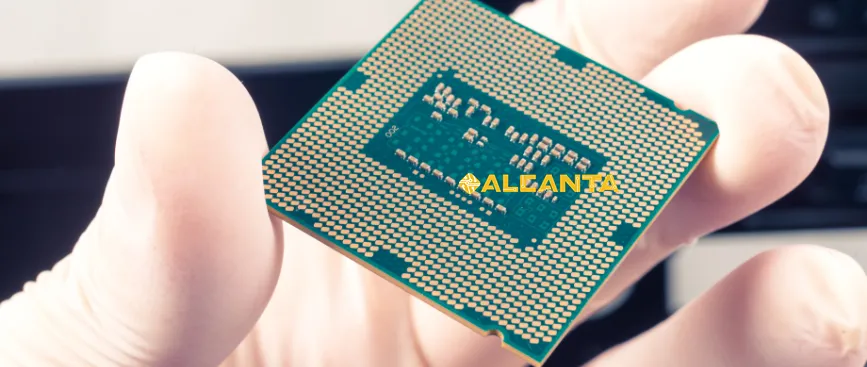
Microvia Package Substrate Manufacturer
What are the Microvia Package Substrate Design Guidelines?
The design guidelines for Microvia Package Substrates focus on ensuring reliable performance and manufacturability. Here are some key aspects typically considered:
- Microvia Size and Pitch: Specify the minimum via size and pitch requirements based on the density and complexity of the circuit design. This includes guidelines for aspect ratios to ensure proper plating and reliability.
- Layer Stackup: Define the layer stackup configuration, including the number of layers, material types, and thicknesses. Ensure compatibility with the intended electrical and thermal performance requirements.
- Material Selection: Choose appropriate substrate materials based on thermal management needs, signal integrity considerations, and compatibility with manufacturing processes.
- Via Placement and Routing: Optimize the placement of microvias to minimize signal interference and crosstalk. Follow guidelines for routing signal traces and power planes to maintain signal integrity and reduce noise.
- Annular Ring and Pad Design: Specify the dimensions of annular rings and pads around microvias to ensure robust electrical connections and reliability during assembly and operation.
- Plating and Surface Finish: Define plating requirements for microvias to ensure good electrical conductivity and reliability. Choose suitable surface finishes to protect against oxidation and facilitate soldering.
- Thermal Management: Incorporate design features such as thermal vias or heat sinks as needed to manage heat dissipation effectively, especially for high-power applications.
- Manufacturing Tolerances: Consider manufacturing tolerances for drilling, plating, and layer registration to ensure consistent quality and reliability across production batches.
- Testing and Inspection:Establish guidelines for testing and inspection procedures to verify the integrity and functionality of microvias and overall substrate performance.
- Compliance and Standards: Ensure compliance with industry standards and regulations related to PCB design, materials, and manufacturing processes.
By adhering to these design guidelines, engineers can optimize the performance, reliability, and manufacturability of Microvia Package Substrates for various advanced electronic applications.
What is the Microvia Package Substrate Fabrication Process?
The fabrication process of Microvia Package Substrates involves several key steps to achieve precise interconnection and high reliability. Here’s a generalized outline of the process:
- Material Selection:Choose appropriate substrate materials based on the specific application requirements, such as high-frequency laminates or thermally conductive substrates.
- Design Layout: Create a detailed design layout that includes microvia placement, routing of signal traces, power planes, and thermal management features. Ensure adherence to design guidelines for microvia size, pitch, and layer stackup.
- Drilling: Utilize laser drilling technology to create microvias with diameters typically less than 150 micrometers. Laser drilling offers high precision and control over via size and placement.
- Desmear and Clean: After drilling, remove any residues and contaminants from the drilled holes through desmear and cleaning processes. This step is crucial to ensure good adhesion of subsequent layers and plating.
- Electroless Copper Deposition: Initiate the process of metallization by depositing a thin layer of electroless copper on the inner walls of the microvias. This layer acts as a seed layer for subsequent plating.
- Electroplating: Plate additional layers of copper through electroplating processes to build up the conductive paths within the microvias and across the substrate layers. Control plating thickness carefully to meet design specifications.
- Surface Finish: Apply a suitable surface finish, such as immersion gold, OSP (Organic Solderability Preservatives), or HASL (Hot Air Solder Leveling), to protect exposed copper surfaces, ensure solderability, and prevent oxidation.
- Etching and Lamination: Etch away excess copper from non-circuit areas using chemical etching processes. Then, laminate multiple layers of substrate materials together under heat and pressure to form the final PCB substrate.
- Routing and Final Inspection: Rout the substrate to its final dimensions and conduct rigorous inspections and tests to verify the integrity of microvias, layer registration, and overall substrate quality.
- Quality Assurance: Implement quality control measures throughout the fabrication process to ensure compliance with design specifications, industry standards, and customer requirements.
Microvia Package Substrate fabrication requires precision, expertise in material handling, and advanced manufacturing technologies to achieve high-density interconnects and reliable performance suitable for modern electronic applications.
How do you manufacture a Microvia Package Substrate?
Manufacturing a Microvia Package Substrate involves a detailed process that integrates advanced technologies and precise handling of materials. Here’s a step-by-step overview of how Microvia Package Substrates are typically manufactured:
- Material Selection: Choose substrate materials based on the application requirements, such as high-frequency laminates for RF applications or thermally conductive materials for high-power devices.
- Design and Layout: Create a detailed design layout using CAD software. This includes determining the number of layers, microvia placements, routing of signal traces, and consideration of thermal management features.
- Laser Drilling: Use laser drilling technology to create microvias in the substrate. Laser drilling offers high precision and control over via size and placement. The diameters of microvias are typically less than 150 micrometers.
- Desmear and Cleaning: After drilling, remove any residues and contaminants from the drilled holes through desmear and cleaning processes. This step is critical to ensure good adhesion of subsequent layers and proper plating.
- Metallization:Initiate metallization by depositing a thin layer of electroless copper on the inner walls of the microvias. This layer acts as a seed layer for subsequent plating processes.
- Electroplating: Plate additional layers of copper through electroplating processes to build up the conductive paths within the microvias and across the substrate layers. Control plating thickness carefully to meet design specifications.
- Layer Lamination: Laminate multiple layers of substrate materials together under heat and pressure. This step integrates the microvias and builds the multi-layered structure of the substrate.
- Etching and Surface Finishing: Etch away excess copper from non-circuit areas using chemical etching processes. Apply a suitable surface finish, such as immersion gold, OSP (Organic Solderability Preservatives), or HASL (Hot Air Solder Leveling), to protect exposed copper surfaces and ensure solderability.
- Final Inspection and Testing: Conduct thorough inspections and tests to verify the integrity of microvias, layer registration, and overall substrate quality. This includes checks for dimensional accuracy, electrical continuity, and reliability under various environmental conditions.
- Quality Assurance: Implement quality control measures throughout the manufacturing process to ensure compliance with design specifications, industry standards, and customer requirements.
- Packaging and Delivery: Package the finished Microvia Package Substrates according to customer specifications and deliver them to assembly facilities for integration into electronic devices.
Manufacturing Microvia Package Substrates requires expertise in PCB fabrication processes, advanced equipment for laser drilling and metallization, and strict adherence to design guidelines and quality standards to achieve high-density interconnects and reliable performance essential for modern electronic applications.
How much should a Microvia Package Substrate cost?
The cost of a Microvia Package Substrate can vary significantly depending on several factors:
- Complexity of Design: The number of layers, density of microvias, and complexity of the layout impact manufacturing costs. More intricate designs requiring higher precision and tighter tolerances will generally increase costs.
- Materials Used: The type and quality of substrate materials (such as high-frequency laminates or thermally conductive substrates) affect costs. Specialized materials designed for specific performance characteristics can be more expensive.
- Manufacturing Process: Advanced processes such as laser drilling for microvias, precise metallization techniques, and stringent quality control measures contribute to manufacturing costs.
- Quantities Ordered: Economies of scale apply, meaning larger production runs typically lower per-unit costs due to efficiencies in material usage, setup, and production.
- Additional Features: Surface finishes (like immersion gold or OSP), special treatments (such as thermal management solutions), and compliance testing may add to the overall cost.
- Supplier and Location: Costs can vary between different suppliers and regions based on labor costs, overheads, and market conditions.
As a rough estimate, prices for Microvia Package Substrates can range from a few dollars to tens of dollars per square inch, depending on the above factors. For a precise quote, it’s advisable to consult with PCB manufacturers or suppliers who can provide tailored pricing based on your specific design requirements and production volume.
What is Microvia Package Substrate base material?
The base material used for Microvia Package Substrates can vary depending on the specific requirements of the application. Typically, these substrates are made from advanced materials tailored to meet high-performance electronic needs. Some common base materials include:
- High-Frequency Laminates: These are designed to minimize signal loss and maintain signal integrity at high frequencies. They often have low dielectric constants and low loss tangents, making them suitable for RF/microwave applications.
- Thermally Conductive Substrates: Used in applications requiring efficient heat dissipation, such as power electronics and LED lighting. These substrates typically have high thermal conductivity and can include metal-backed options for improved thermal management.
- FR-4 and Similar Materials: Although less common for Microvia Package Substrates due to their lower performance characteristics compared to specialized laminates, standard FR-4 materials can still be used for less demanding applications where cost-effectiveness is prioritized over high performance.
- High-Density Interconnect (HDI) Materials: HDI materials are optimized for dense interconnects and microvia structures. They offer good electrical performance and reliability, making them suitable for advanced semiconductor packaging and mobile devices.
- Ceramic Substrates: In certain high-temperature and high-frequency applications, ceramic substrates like LTCC (Low Temperature Co-Fired Ceramic) or HTCC (High Temperature Co-Fired Ceramic) may be used. These offer excellent thermal stability and mechanical strength.
The choice of base material depends on factors such as electrical performance requirements (signal integrity, impedance control), thermal management needs, mechanical properties, and environmental considerations. Manufacturers select the most appropriate material based on the specific design parameters and performance specifications of the Microvia Package Substrate.
Which company makes Microvia Package Substrates?
Microvia Package Substrates (微孔封装基板) are produced by many professional PCB manufacturing companies, which typically possess advanced technologies and equipment to meet the demands of high-performance electronic products. For instance, companies like Rogers Corporation, Isola Group, Park Electrochemical Corp., and Shengyi Technology have extensive experience and technological expertise in the field of Microvia Package Substrates.
As for our company, we are also capable of producing high-quality Microvia Package Substrates. We have advanced PCB manufacturing equipment and a skilled technical team capable of meeting various customer requirements for Microvia Package Substrates. Our manufacturing process includes advanced laser drilling technology, precise metallization processes, and rigorous quality control procedures to ensure consistency and reliability in every production batch.
In terms of material selection, we can offer a variety of options based on customer application needs, such as high-frequency laminates, thermally conductive substrates, etc., to ensure optimal performance in signal transmission, thermal management, and reliability. Moreover, we emphasize cost-effectiveness and production efficiency, providing competitive pricing based on customer order volumes.
Our team not only serves as a manufacturer but also as a provider of technical expertise and solutions. We are committed to collaborating with customers to customize Microvia Package Substrates according to their design specifications and performance requirements, providing essential foundational support for their electronic products.
Therefore, if you have any requirements for Microvia Package Substrates or would like to know more details, we welcome you to contact us. We are dedicated to providing professional consultation and services to meet your needs.
What are the 7 qualities of good customer service?
Good customer service is characterized by several key qualities that contribute to positive customer experiences and satisfaction. Here are seven essential qualities:
- Responsiveness:Responding promptly to customer inquiries, concerns, and requests demonstrates respect for their time and urgency. Timely responses can help resolve issues quickly and prevent escalation.
- Empathy: Showing empathy means understanding and acknowledging the customer’s feelings, perspectives, and challenges. It involves listening actively, demonstrating compassion, and considering their point of view when providing solutions.
- Clear Communication: Effective communication is essential in customer service. It involves conveying information clearly and concisely, using language that is easy to understand. Clear communication helps prevent misunderstandings and ensures customers are well-informed.
- Knowledgeability: Having thorough knowledge about products or services enables customer service representatives to provide accurate information and solutions. Knowledgeability builds trust and confidence in the company’s expertise.
- Problem-Solving Skills: Good customer service involves the ability to identify and address customer issues effectively. This includes analyzing problems, proposing viable solutions, and taking proactive steps to resolve issues to the customer’s satisfaction.
- Professionalism: Maintaining professionalism in all interactions with customers reflects positively on the company’s image. It involves being courteous, respectful, and maintaining composure, even in challenging situations.
- Personalization: Tailoring interactions to meet individual customer needs and preferences enhances the customer experience. Personalization can include addressing customers by name, remembering their previous interactions, and offering customized solutions when appropriate.
By embodying these qualities, businesses can cultivate strong relationships with customers, foster loyalty, and differentiate themselves in competitive markets.
FAQs
What are Microvia Package Substrates?
Microvia Package Substrates are specialized printed circuit board (PCB) substrates designed with microvias—tiny holes drilled using laser technology. They are used in high-density and high-performance electronic applications.
What are the advantages of Microvia Package Substrates?
Microvia Package Substrates offer several advantages, including higher interconnect density, improved signal integrity at high frequencies, enhanced thermal management, and support for miniaturization in electronic devices.
What applications are Microvia Package Substrates used for?
They are used in various advanced electronic applications such as mobile devices, telecommunications equipment, high-speed computing systems, RF/microwave devices, and automotive electronics where compact size and high performance are crucial.
How are Microvia Package Substrates manufactured?
The manufacturing process typically involves laser drilling of microvias, metallization to create conductive paths, lamination of multiple substrate layers, and application of surface finishes to ensure reliability and performance.
What materials are used in Microvia Package Substrates?
Common materials include high-frequency laminates, thermally conductive substrates, and other advanced materials tailored for specific electrical, thermal, and mechanical properties required by different applications.
What factors should be considered when choosing Microvia Package Substrates?
Key considerations include the electrical performance (signal integrity, impedance control), thermal management requirements, mechanical strength, cost-effectiveness, and compliance with industry standards.
Where can I get Microvia Package Substrates manufactured?
Many PCB manufacturers and suppliers specialize in producing Microvia Package Substrates. Companies with expertise in advanced PCB technologies and materials are typically best suited for these specialized substrates.