What is Microtrace Substrate?
Microtrace Substrate Manufacturer,Microtrace substrate integrates microscopic identifiers into its material, ensuring precise traceability and authentication. These substrates, utilized in various industries like pharmaceuticals and electronics, provide robust protection against counterfeiting and ensure secure supply chain tracking. Featuring high durability and chemical resistance, Microtrace substrates are compatible with diverse manufacturing processes. They enhance brand protection and consumer trust, offering effective anti-counterfeiting measures in products such as pharmaceuticals, electronics, and luxury goods. With their microscopic identifiers seamlessly embedded into the substrate material, Microtrace substrates contribute to the authenticity and reliability of products across industries.
Microtrace substrate refers to a specialized material used in various applications, particularly in forensic science, security, and anti-counterfeiting measures. It typically consists of a substrate material, such as paper or plastic, that has been treated or modified with microscopic particles or additives to impart specific properties or features.
These substrates are designed to incorporate unique characteristics that are difficult to replicate or counterfeit, making them valuable for authentication and verification purposes. For example, they may contain micro-scale patterns, security features, or chemical markers that are invisible to the naked eye but can be detected using specialized equipment or techniques.
Microtrace substrates are used in a wide range of applications, including banknotes, passports, identification cards, product packaging, and secure documents. They help to deter counterfeiting and fraud by providing a reliable means of verifying the authenticity of the item or document.
In addition to security applications, microtrace substrates may also be used in research, diagnostics, and other scientific fields where precise control over material properties or features is required at the micro or nano scale. Overall, these substrates play a crucial role in safeguarding against illicit activities and ensuring the integrity of various products and documents.
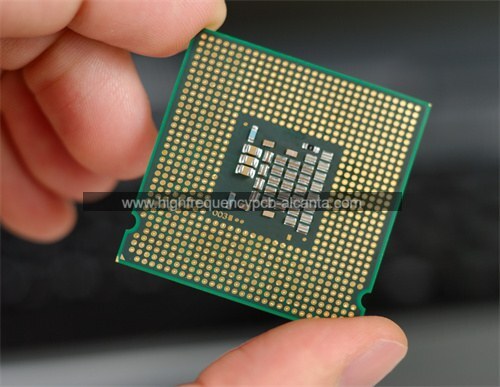
Microtrace Substrate Manufacturer
What are the functions of Microtrace Substrate?
The functions of Microtrace Substrate include:
Anti-counterfeiting: Microtrace Substrate can incorporate unique features such as micro-patterns, security markers, or chemical markers, making it difficult to replicate or counterfeit, thus serving anti-counterfeiting purposes.
Authentication: Microtrace Substrate can be used to verify the authenticity of items or documents. Specific detection methods or equipment can identify the micro-scale features or markers on the substrate, confirming its authenticity.
Security: Microtrace Substrate can enhance the security of products or documents. By adding security features or technologies, it can protect them from threats such as fraud, counterfeiting, or tampering.
Tracking: Microtrace Substrate can be used to track the origin or flow of products or documents. By adding tracking markers or information on the substrate, the production process or distribution path of items can be traced.
Scientific research: Microtrace Substrate can also be used in scientific research to explore the microcosm or conduct material analysis. By controlling specific properties on the substrate or adding specific chemical markers, precise control and analysis of samples can be achieved.
Overall, Microtrace Substrate serves multiple functions such as anti-counterfeiting, authentication, security, tracking, and scientific research, which are crucial for ensuring the authenticity, security, and traceability of products or documents.
What are the different types of Microtrace Substrate?
There are several different types of Microtrace Substrates, each with its own unique properties and applications. Some common types include:
Paper-based substrates: These substrates are typically made from paper materials and can be treated or coated with micro-scale additives or features for security and anti-counterfeiting purposes. They are commonly used in banknotes, passports, and secure documents.
Plastic-based substrates: These substrates are made from plastic materials such as polyethylene (PE), polypropylene (PP), or polyester (PET) and can be modified with micro-scale additives or features for security and authentication purposes. They are often used in identification cards, product packaging, and security labels.
Polymer-based substrates: These substrates are composed of polymer materials and can be engineered with micro-scale additives or features to provide specific properties such as durability, flexibility, or chemical resistance. They are used in various applications ranging from banknotes to medical devices.
Coated substrates: These substrates consist of a base material that is coated with a layer of specialized material containing micro-scale additives or features. The coating can provide additional protection, security, or functionality to the substrate. They are used in applications such as smart cards, labels, and security documents.
Hybrid substrates: These substrates combine different materials or technologies to achieve specific performance or functionality requirements. For example, a hybrid substrate may incorporate both paper and plastic components to provide the benefits of both materials. They are used in diverse applications where unique combinations of properties are needed.
Overall, the choice of Microtrace Substrate depends on the specific requirements of the application, such as security level, durability, flexibility, and compatibility with printing or processing techniques.
What is the relationship between Microtrace Substrate and IC packaging?
Microtrace Substrate and IC (Integrated Circuit) packaging are related in the sense that they both play important roles in electronic devices, particularly in ensuring the functionality, reliability, and security of integrated circuits.
Security and anti-counterfeiting: Both Microtrace Substrate and IC packaging can incorporate features or technologies to enhance security and deter counterfeiting. Microtrace Substrates may contain micro-scale patterns, markers, or additives that are difficult to replicate, while IC packaging may include anti-tampering measures such as holographic labels or encrypted identifiers.
Authentication: Microtrace Substrates and IC packaging can be used for authentication purposes to verify the origin and authenticity of electronic components. Microtrace Substrates may contain unique identifiers or markers that can be detected using specialized equipment, while IC packaging may include serialized codes or embedded authentication features.
Reliability and protection: Both Microtrace Substrate and IC packaging are designed to protect integrated circuits from environmental factors, mechanical stress, and electromagnetic interference. Microtrace Substrates may provide additional layers of protection or insulation for electronic components, while IC packaging serves as a protective enclosure for the integrated circuit die.
Traceability: Microtrace Substrates and IC packaging can facilitate traceability by incorporating tracking markers or information that enables the monitoring of component manufacturing, distribution, and usage. This helps to ensure the integrity of the supply chain and detect any unauthorized alterations or substitutions.
Overall, Microtrace Substrate and IC packaging are complementary technologies that work together to enhance the security, reliability, and traceability of electronic components and devices. They are both essential components in the manufacturing and deployment of integrated circuits for various applications.
How does Microtrace Substrate differ from PCB?
Microtrace Substrate and PCB (Printed Circuit Board) are both used in electronic devices but serve different purposes and have distinct characteristics:
Functionality: Microtrace Substrate is primarily used for security, authentication, and anti-counterfeiting purposes. It typically contains micro-scale patterns, markers, or additives that are difficult to replicate and can be used to verify the authenticity of products or documents. PCB, on the other hand, is used to mechanically support and electrically connect electronic components using conductive pathways, tracks, and pads.
Composition: Microtrace Substrate is often made from specialized materials such as paper, plastic, or polymer, which are modified or treated with micro-scale additives or features. These additives may include security inks, dyes, or particles that are invisible to the naked eye but can be detected using specialized equipment. PCB, on the other hand, is typically made from a rigid or flexible insulating material, such as fiberglass-reinforced epoxy, with copper traces and layers of conductive materials.
Application: Microtrace Substrate is commonly used in security documents, banknotes, passports, product packaging, and other items where authentication and anti-counterfeiting measures are required. PCB, on the other hand, is used in electronic devices and systems such as computers, smartphones, automotive electronics, and consumer electronics, where it serves as the backbone for connecting and integrating various electronic components.
Manufacturing process: The manufacturing process for Microtrace Substrate involves specialized techniques for incorporating micro-scale features or additives into the substrate material. This may include printing, coating, or embedding security elements into the substrate. PCB manufacturing, on the other hand, involves processes such as etching, drilling, soldering, and laminating to create the required circuitry and connections on the board.
In summary, while both Microtrace Substrate and PCB are used in electronic devices, they serve different purposes, have different compositions, applications, and manufacturing processes. Microtrace Substrate focuses on security and authentication, while PCB is essential for the electrical functionality and connectivity of electronic devices.
What are the structure and production technology of Microtrace Substrate?
The structure and production technology of Microtrace Substrate can vary depending on the specific application and desired features, but generally involve several key components and manufacturing processes:
Substrate material: Microtrace Substrate can be made from various materials such as paper, plastic, polymer, or hybrid materials. The choice of substrate material depends on factors such as durability, flexibility, compatibility with printing or coating processes, and desired security features.
Micro-scale additives or features: Microtrace Substrate typically incorporates micro-scale additives, markers, or features that are difficult to replicate or counterfeit. These additives may include security inks, dyes, particles, or patterns that are invisible to the naked eye but can be detected using specialized equipment or techniques.
Printing or coating processes: The production of Microtrace Substrate often involves printing or coating processes to incorporate micro-scale features onto the substrate material. This may include techniques such as offset printing, intaglio printing, gravure printing, or screen printing. Alternatively, specialized coatings or treatments may be applied to the substrate material to embed security elements or markers.
Additive manufacturing techniques: In some cases, additive manufacturing techniques such as inkjet printing or 3D printing may be used to directly deposit micro-scale additives or features onto the substrate material. This allows for precise control over the placement and distribution of security elements.
Quality control and verification: Throughout the production process, quality control measures are implemented to ensure the integrity and authenticity of the Microtrace Substrate. This may involve testing and verification of the substrate material, detection of micro-scale features using specialized equipment, and validation of security elements against established standards or specifications.
Overall, the structure and production technology of Microtrace Substrate involve the careful selection of substrate materials, incorporation of micro-scale additives or features, printing or coating processes, additive manufacturing techniques, and rigorous quality control measures to ensure the effectiveness and reliability of the security features.
Frequently Asked Questions (FAQs)
What is Microtrace Substrate?
Microtrace Substrate refers to a specialized material used in various applications, particularly in forensic science, security, and anti-counterfeiting measures. It typically consists of a substrate material, such as paper or plastic, that has been treated or modified with microscopic particles or additives to impart specific properties or features.
What are the functions of Microtrace Substrate?
Microtrace Substrate serves several functions, including security, authentication, anti-counterfeiting, reliability, and traceability. It incorporates unique features or markers that are difficult to replicate and can be used to verify the authenticity of products or documents.
How does Microtrace Substrate differ from PCB?
Microtrace Substrate focuses on security and anti-counterfeiting measures, incorporating micro-scale features or additives for authentication purposes. PCB (Printed Circuit Board), on the other hand, is used to mechanically support and electrically connect electronic components in electronic devices.
What are the different types of Microtrace Substrate?
Microtrace Substrate can be made from various materials, including paper, plastic, polymer, or hybrid materials. It may incorporate micro-scale additives, markers, or features such as security inks, dyes, particles, or patterns.
What is the production technology of Microtrace Substrate?
The production of Microtrace Substrate typically involves printing or coating processes to incorporate micro-scale features onto the substrate material. It may also include additive manufacturing techniques such as inkjet printing or 3D printing to directly deposit micro-scale additives or features onto the substrate.
Where is Microtrace Substrate used?
Microtrace Substrate is used in a wide range of applications, including security documents, banknotes, passports, product packaging, identification cards, and secure labels. It is also used in forensic science, research, and diagnostic applications.
How can Microtrace Substrate be authenticated?
Microtrace Substrate can be authenticated using specialized equipment or techniques to detect and verify the presence of micro-scale features or markers embedded in the substrate material. This may involve the use of UV light, infrared imaging, spectroscopy, or other detection methods.
Conclusion
In conclusion, Microtrace Substrate is a specialized material used in various applications, primarily focusing on security, authentication, and anti-counterfeiting measures. It consists of a substrate material, such as paper or plastic, that has been treated or modified with microscopic particles or additives to impart specific properties or features. Microtrace Substrate serves several functions, including security, authentication, anti-counterfeiting, reliability, and traceability. It can be made from various materials and incorporates micro-scale additives, markers, or features to enhance its effectiveness. The production technology of Microtrace Substrate involves printing or coating processes, additive manufacturing techniques, and rigorous quality control measures to ensure the integrity and authenticity of the security features. Overall, Microtrace Substrate plays a crucial role in safeguarding against illicit activities, ensuring the integrity of products or documents, and maintaining the security of various applications.