Microtrace RF PCB Manufacturer
Microtrace RF PCB Manufacturer,Military Circuit Boards (MCBs) are the backbone of advanced military and defense systems, engineered to withstand the rigors of harsh environments and deliver unparalleled performance in mission-critical operations. These specialized printed circuit boards are meticulously designed and manufactured to meet stringent military standards and specifications, ensuring reliability, durability, and resilience under extreme conditions.
MCBs are constructed using high-quality materials and advanced manufacturing processes, incorporating features such as ruggedized substrates, reinforced copper traces, and protective coatings to withstand temperature extremes, vibration, shock, and electromagnetic interference. They are meticulously tested and qualified to ensure compliance with military standards, including MIL-PRF-31032, MIL-PRF-55110, and MIL-PRF-50884, guaranteeing their suitability for use in military platforms such as aircraft, ships, ground vehicles, and weapons systems.
With their high reliability, robustness, and performance, Military Circuit Boards play a crucial role in enabling the functionality and effectiveness of military equipment and ensuring the success of military missions in challenging operational environments.
What is a Microtrace RF PCB?
A Microtrace RF PCB (Printed Circuit Board) refers to a type of PCB designed specifically for radio frequency (RF) applications. RF PCBs are engineered to ensure optimal performance and reliability in electronic devices that transmit or receive radio frequency signals.
Microtrace RF PCBs are characterized by their ability to handle high-frequency signals efficiently while minimizing signal loss and interference. They are typically constructed using specialized materials and techniques tailored for RF applications, such as high-frequency laminates, controlled impedance traces, and precise layout design to minimize signal reflections and maintain signal integrity.
These PCBs are commonly used in various RF systems, including wireless communication devices like smartphones, routers, RFID systems, and radar systems. They play a crucial role in enabling the transmission and reception of RF signals with high fidelity and minimal degradation, which is essential for reliable communication and data transfer in modern electronic devices.
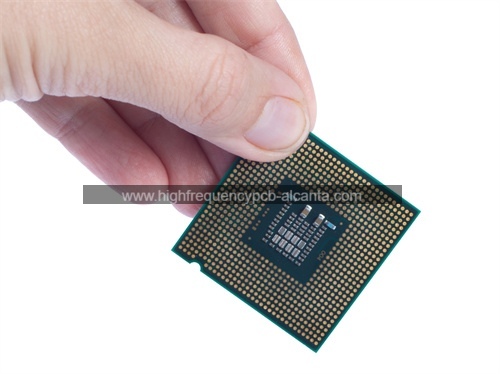
Microtrace RF PCB Manufacturer
What are the Microtrace RF PCB Design Guidelines?
Designing Microtrace RF PCBs requires adherence to specific guidelines to ensure optimal performance in high-frequency applications. While the exact guidelines may vary depending on the specific requirements of the RF circuit and the manufacturer’s recommendations, here are some common principles:
- Use High-Frequency Materials: Select specialized materials optimized for RF applications, such as high-frequency laminates with low dielectric constant (Dk) and low dissipation factor (Df) to minimize signal loss and impedance variations.
- Controlled Impedance: Maintain controlled impedance for transmission lines to minimize signal reflections and ensure signal integrity. This involves precise trace width, spacing, and layer stack-up design to match the characteristic impedance of the transmission lines.
- Grounding: Implement a solid ground plane on all PCB layers to provide a low impedance return path for RF signals and minimize electromagnetic interference (EMI). Proper grounding is crucial for reducing noise and maintaining signal integrity.
- Component Placement: Carefully position RF components, including antennas, RF connectors, amplifiers, and filters, to minimize signal path lengths, reduce parasitic capacitance and inductance, and optimize signal coupling.
- Signal Routing: Use short, direct signal paths with minimal bends and vias to reduce signal losses, impedance mismatches, and electromagnetic radiation. Avoid sharp corners and 90-degree bends, as they can lead to signal reflections and impedance variations.
- Avoid Crosstalk: Maintain adequate spacing between signal traces and between signal and non-signal traces to minimize crosstalk and interference between adjacent lines.
- EMI Shielding: Incorporate shielding techniques, such as copper pours or shielding cans, to contain electromagnetic radiation and prevent external interference from affecting the RF circuitry.
- Thermal Management: Ensure proper thermal management to dissipate heat generated by RF components, as excessive heat can degrade performance and reliability. This may involve incorporating thermal vias, heatsinks, or thermal pads into the PCB design.
- Simulation and Testing: Use electromagnetic simulation tools to analyze and optimize the RF PCB design before fabrication. Additionally, perform thorough testing and validation of prototypes to verify performance and compliance with design specifications.
By following these guidelines and leveraging RF design best practices, engineers can develop Microtrace RF PCBs that meet the stringent requirements of high-frequency applications, ensuring reliable performance and signal integrity.
What is the Microtrace RF PCB Fabrication Process?
The fabrication process for Microtrace RF PCBs involves several steps aimed at creating high-quality printed circuit boards optimized for radio frequency (RF) applications. While specific details may vary depending on factors such as design requirements and manufacturer capabilities, the general process typically includes the following stages:
- Design Preparation: This stage involves preparing the PCB design files using electronic design automation (EDA) software. Designers specify the PCB layout, including component placement, trace routing, layer stack-up, and controlled impedance requirements, adhering to Microtrace RF PCB design guidelines.
- Material Selection: Select specialized materials optimized for RF applications, such as high-frequency laminates with low dielectric constant (Dk) and low dissipation factor (Df). The choice of material depends on factors such as frequency range, signal integrity requirements, and thermal properties.
- Preparation of Substrate: The selected substrate material is prepared for PCB fabrication. This may involve cutting the substrate to size, cleaning it to remove contaminants, and applying a copper foil layer to serve as the conductive surface for the PCB.
- Lamination: In the lamination process, multiple layers of substrate material and copper foil are stacked according to the PCB design specifications. The layers are then bonded together using heat and pressure to form a single, multilayered substrate known as a PCB panel.
- Drilling: Holes are drilled into the PCB panel to create vias, which establish electrical connections between different layers of the PCB. For Microtrace RF PCBs, precise drilling is essential to maintain controlled impedance and minimize signal losses.
- Copper Etching: Copper etching involves removing excess copper from the PCB panel using chemical etchants. This process defines the traces and pads according to the PCB design, leaving behind the desired conductive patterns.
- Surface Treatment: Surface treatment processes, such as solder mask application and surface finish deposition, are performed to protect the PCB and enhance its electrical properties. Solder mask is applied to the PCB surface to insulate and protect the copper traces, while surface finish techniques like gold plating or immersion tin ensure reliable solderability and corrosion resistance.
- Quality Control and Inspection: Throughout the fabrication process, quality control measures are implemented to ensure the PCBs meet the specified design requirements and industry standards. Inspection techniques such as visual inspection, electrical testing, and dimensional measurements are used to identify any defects or deviations from the desired specifications.
- Final Testing and Packaging: Once fabrication is complete, the finished Microtrace RF PCBs undergo final testing to verify their functionality and performance. This may include RF testing to validate signal integrity and impedance matching. After passing quality assurance checks, the PCBs are packaged and prepared for shipment to the customer or assembly facility.
By following a meticulous fabrication process and adhering to Microtrace RF PCB design guidelines, manufacturers can produce high-quality PCBs optimized for demanding RF applications, ensuring reliable performance and signal integrity.
How do you manufacture a Microtrace RF PCB?
Manufacturing a Microtrace RF PCB involves several specialized processes tailored to meet the stringent requirements of high-frequency applications. Here’s an overview of the manufacturing steps:
- Design Preparation: Engineers use electronic design automation (EDA) software to create the PCB layout according to the specific requirements of the RF circuit. This involves placing RF components, defining trace routing, determining layer stack-up, and specifying controlled impedance requirements.
- Material Selection:Choose high-quality materials optimized for RF applications. High-frequency laminates with low dielectric constant (Dk) and low dissipation factor (Df) are commonly used. The choice of material depends on factors such as frequency range, signal integrity requirements, and thermal properties.
- Substrate Preparation: Prepare the substrate material for PCB fabrication. This may involve cutting the substrate to size, cleaning it to remove contaminants, and applying a thin layer of copper foil to serve as the conductive surface for the PCB.
- Layer Lamination: Stack multiple layers of substrate material and copper foil according to the PCB design specifications. Each layer may have a specific copper thickness and may require bonding with adhesive materials. The layers are then pressed together under heat and pressure to form a single, multilayered PCB panel.
- Drilling: Precision drilling is performed to create holes (vias) that establish electrical connections between different layers of the PCB. The drilling process must maintain tight tolerances to ensure controlled impedance and minimize signal losses.
- Copper Etching: Apply a photoresist layer to the copper-clad substrate and expose it to ultraviolet (UV) light through a photomask, defining the conductive patterns. Then, immerse the panel in an etching solution to remove the unprotected copper, leaving behind the desired traces and pads.
- Surface Treatment: Apply a solder mask over the PCB surface to insulate and protect the copper traces. Surface finish techniques such as gold plating or immersion tin are applied to ensure reliable solderability and corrosion resistance.
- Component Assembly:Populate the PCB with RF components such as antennas, RF connectors, amplifiers, and filters using automated pick-and-place machines. The components are soldered onto the PCB using surface mount technology (SMT) or through-hole soldering techniques.
- Testing and Quality Control: Perform rigorous testing and inspection throughout the manufacturing process to ensure the PCBs meet the specified design requirements and industry standards. This includes electrical testing, impedance measurement, visual inspection, and functional testing.
- Final Packaging: Once manufacturing and testing are complete, the finished Microtrace RF PCBs are packaged and prepared for shipment to the customer or assembly facility.
By carefully executing each manufacturing step and adhering to Microtrace RF PCB design guidelines, manufacturers can produce high-quality PCBs optimized for demanding RF applications, ensuring reliable performance and signal integrity.
How much should a Microtrace RF PCB cost?
The cost of a Microtrace RF PCB can vary significantly depending on several factors, including the complexity of the design, the materials used, the manufacturing processes involved, the quantity ordered, and the supplier or manufacturer chosen. Here are some factors that influence the cost:
- Complexity of Design: PCBs with intricate layouts, densely packed components, high layer counts, and advanced features such as controlled impedance routing will typically cost more to manufacture due to the increased design and manufacturing complexity.
- Materials: The choice of materials significantly impacts the cost. High-frequency laminates optimized for RF applications tend to be more expensive than standard FR-4 materials due to their specialized properties.
- Manufacturing Processes: Certain manufacturing processes, such as multilayer lamination, controlled impedance routing, and precision drilling for vias, can add to the manufacturing cost.
- Quantity:Economies of scale apply in PCB manufacturing. Ordering larger quantities often leads to lower per-unit costs due to efficiencies in production and bulk material purchasing.
- Lead Time: Expedited manufacturing services typically incur additional fees. Longer lead times may offer cost savings as they allow for more efficient production scheduling.
- Supplier/Manufacturer:Different suppliers and manufacturers have varying pricing structures, capabilities, and quality standards. Some may offer competitive pricing or discounts for bulk orders, while others may specialize in high-end, premium-quality PCBs at a higher cost.
To get an accurate cost estimate for a specific Microtrace RF PCB project, it’s advisable to consult with PCB manufacturers or suppliers directly. Providing detailed information about the design requirements, including dimensions, layer count, materials, and expected quantity, will help obtain more precise quotes. Additionally, it’s beneficial to consider factors such as quality, reliability, and customer support when choosing a PCB supplier, as these can impact the overall value of the PCBs.
What is Microtrace RF PCB base material?
Microtrace RF PCBs typically use specialized base materials optimized for high-frequency applications. These materials are carefully chosen to meet the demanding requirements of RF circuits, such as low dielectric constant (Dk), low dissipation factor (Df), and excellent electrical properties at high frequencies. While specific formulations may vary depending on the manufacturer and the exact specifications of the RF PCB, some common base materials used for Microtrace RF PCBs include:
- PTFE (Polytetrafluoroethylene): PTFE-based materials, such as Teflon, are widely used in RF PCBs due to their low Dk, low loss tangent, and excellent electrical insulation properties. They offer superior performance at high frequencies and are well-suited for applications requiring minimal signal loss and impedance control.
- PTFE Composite Materials: Composite materials combining PTFE with reinforcing fillers such as woven glass, ceramic, or microfibers are also popular choices for Microtrace RF PCBs. These materials offer improved mechanical strength, dimensional stability, and ease of processing while maintaining the desirable electrical properties of pure PTFE.
- Rogers Corporation Materials: Rogers Corporation manufactures a range of high-performance laminates specifically designed for RF and microwave applications. Materials such as RO4000 series and RO3000 series offer low Dk, tight dielectric thickness control, and excellent stability over a wide frequency range, making them suitable for Microtrace RF PCBs.
- Isola Materials: Isola is another leading manufacturer of high-frequency laminates used in RF PCBs. Their materials, such as the Astra MT laminate series, offer low Dk, low loss, and high thermal conductivity, making them suitable for high-speed digital and RF/microwave applications.
- Nelco Materials: Nelco, a subsidiary of Park Electrochemical Corp., produces a variety of high-performance laminates for RF and microwave applications. Their materials, such as the Nelco N4000 and N5000 series, offer low Dk, low loss, and excellent dimensional stability, ideal for Microtrace RF PCBs requiring precise impedance control.
These base materials, along with others specifically engineered for RF applications, provide the foundation for Microtrace RF PCBs, enabling high-performance signal transmission, minimal loss, and reliable operation in wireless communication systems, radar systems, RF transceivers, and other RF/microwave devices.
Which company makes Microtrace RF PCB?
Currently, many companies offer manufacturing services for Microtrace RF PCBs. Some of these companies specialize in producing high-performance, customized RF PCBs to meet various RF application requirements. However, there isn’t a specific manufacturer of “Microtrace RF PCBs” since “Microtrace” could be a design or manufacturing technique rather than a single company’s brand. In fact, “Microtrace RF PCB” might be a generic term used to describe RF PCBs employing microtrace technology aimed at optimizing the transmission and reception of RF signals.
Our company can provide manufacturing services for Microtrace RF PCBs by adopting advanced design and manufacturing techniques. As a professional PCB manufacturer, we have extensive experience and expertise to meet the stringent requirements of high-frequency RF circuits. Our engineering team has a deep technical background and can precisely design and manufacture high-performance Microtrace RF PCBs according to customer requirements.
We have state-of-the-art production equipment and processes to ensure the high quality and consistency of PCB manufacturing. We utilize advanced materials and technologies, including high-frequency laminates, precise controlled printing processes, and high-precision drilling techniques, to ensure the excellent performance and reliability of Microtrace RF PCBs. Additionally, we strictly adhere to quality management systems, conducting comprehensive quality checks and tests to ensure that each PCB meets customer specifications and standards.
Our company is committed to providing customized solutions to meet our customers’ specific needs and application requirements. Whether in communications, medical, aerospace, or military fields, we can deliver high-quality, highly reliable Microtrace RF PCBs to support our customers’ successful projects. Our services include comprehensive support from design to production to ensure customer satisfaction and project success.
What are the 7 qualities of good customer service?
Good customer service is characterized by several key qualities that contribute to positive interactions and relationships with customers. Here are seven qualities of good customer service:
- Responsiveness: Good customer service involves being prompt and proactive in addressing customer inquiries, requests, and concerns. Responding to customers in a timely manner demonstrates respect for their time and shows that their needs are valued.
- Empathy: Empathy is the ability to understand and share the feelings and perspectives of others, including customers. Good customer service representatives listen attentively to customers, acknowledge their emotions, and demonstrate understanding and compassion when resolving issues or providing assistance.
- Communication Skills: Effective communication is essential for delivering good customer service. Clear, concise, and courteous communication helps ensure that customers understand information, instructions, and solutions. Customer service representatives should be skilled at both verbal and written communication to interact effectively with customers across various channels.
- Product Knowledge: Good customer service requires a deep understanding of the products or services being offered. Customer service representatives should be knowledgeable about the features, benefits, specifications, and usage of the products or services so they can provide accurate information and guidance to customers.
- Problem-Solving Abilities: Customers may encounter issues or challenges with products, services, or transactions, and good customer service involves the ability to resolve problems effectively and efficiently. Customer service representatives should be adept at identifying root causes, offering solutions, and taking proactive steps to prevent similar issues in the future.
- Professionalism: Professionalism encompasses qualities such as courtesy, respect, integrity, and reliability. Good customer service representatives conduct themselves professionally at all times, maintain a positive attitude, and treat customers with dignity and respect, regardless of the situation.
- Follow-Up and Feedback: Good customer service extends beyond the initial interaction by following up with customers to ensure their needs have been met and soliciting feedback to continually improve service quality. Customer service representatives should seek feedback from customers, acknowledge their input, and take appropriate action to address any concerns or suggestions.
By embodying these qualities, organizations can cultivate a customer-centric culture and build strong relationships with their customers, leading to increased satisfaction, loyalty, and advocacy.
FAQs
What are Military Circuit Boards (MCBs)?
Military Circuit Boards, or MCBs, are specialized printed circuit boards designed and manufactured to meet the stringent requirements of military and defense applications. These PCBs are engineered to withstand harsh environments, extreme temperatures, vibration, shock, and electromagnetic interference (EMI), while providing high reliability and performance.
What makes MCBs different from commercial PCBs?
MCBs are designed and built to much higher standards compared to commercial PCBs. They undergo rigorous testing, adhere to strict quality control measures, and often incorporate specialized materials and technologies to ensure durability, reliability, and resistance to environmental factors encountered in military operations.
What are some common applications of MCBs?
MCBs are used in a wide range of military and defense systems, including avionics, radar systems, communication equipment, navigation systems, unmanned aerial vehicles (UAVs), missile guidance systems, electronic warfare systems, and more. They play a critical role in ensuring the performance and functionality of these mission-critical systems in demanding operational environments.
What are the key features of MCBs?
MCBs feature several key characteristics designed to meet military standards and requirements. These include high reliability, ruggedness, resistance to temperature extremes, vibration, and shock, as well as protection against EMI and electromagnetic pulse (EMP). They may also incorporate advanced features such as controlled impedance, high-speed signal processing capabilities, and secure data transmission protocols.
What materials are commonly used in the construction of MCBs?
MCBs are typically constructed using specialized materials optimized for military applications. Common substrate materials include high-temperature FR-4, polyimide, PTFE (Teflon), and ceramic materials. Copper conductors may be plated with materials such as gold or silver for enhanced conductivity and corrosion resistance.
How are MCBs tested and certified for military use?
MCBs undergo extensive testing and qualification procedures to ensure they meet military standards and specifications, such as MIL-PRF-31032, MIL-PRF-55110, and MIL-PRF-50884. Testing may include environmental testing (e.g., temperature cycling, humidity, thermal shock), mechanical testing (e.g., vibration, shock), electrical testing (e.g., continuity, insulation resistance), and reliability testing (e.g., accelerated life testing).
Where can I obtain MCBs for military applications?
MCBs are typically manufactured by specialized PCB manufacturers with expertise in military and defense applications. These manufacturers often hold certifications such as ISO 9001 and AS9100, which ensure compliance with quality management standards. Military contractors, defense agencies, and OEMs can source MCBs from qualified suppliers with a proven track record of delivering high-quality products for military use.