Microtrace PCB Manufacturing
Microtrace PCB Manufacturing,Molded Interconnect Substrate (MIS) is an innovative technology revolutionizing the field of electronics manufacturing. By combining plastic injection molding with traditional circuit printing techniques, MIS allows for the creation of three-dimensional circuitry directly within the substrate material. This enables the integration of electrical components, circuit traces, and interconnects in a single, compact structure, eliminating the need for separate wiring and connectors. MIS offers numerous benefits, including reduced size and weight of electronic devices, improved reliability due to fewer interconnects, and enhanced design flexibility to accommodate complex geometries. This technology finds applications across a wide range of industries, from consumer electronics and automotive electronics to medical devices and aerospace. As demand for smaller, more efficient electronic devices continues to grow, MIS provides a scalable solution for manufacturers seeking to innovate and stay competitive in the rapidly evolving electronics market.
What is Microtrace PCB?
Microtrace PCB is a technology used in printed circuit boards (PCBs) that involves embedding microscopic markers or identifiers within the board’s substrate material. These markers are typically invisible to the naked eye and can only be detected using specialized equipment or techniques.
The purpose of Microtrace PCB is to provide a means of authentication, traceability, and anti-counterfeiting for electronic components and devices. By incorporating unique identifiers directly into the PCB during manufacturing, it becomes possible to verify the authenticity of the board and track its origins throughout the supply chain.
Microtrace PCB technology can help prevent the use of counterfeit components in electronic products, enhance product security, and facilitate the identification of counterfeit or unauthorized goods. It is particularly valuable in industries where counterfeit electronic components pose a significant risk to safety, reliability, and intellectual property.
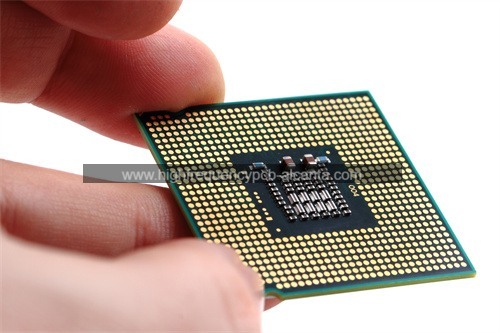
Microtrace PCB Manufacturing
What are the Microtrace PCB Design Guidelines?
Microtrace PCB Design Guidelines refer to a set of recommendations and best practices to follow when designing printed circuit boards (PCBs) that incorporate Microtrace technology. These guidelines are aimed at ensuring the effective integration and performance of Microtrace markers or identifiers within the PCB substrate. While specific guidelines may vary depending on the manufacturer or specific application, some common principles include:
- Marker Placement:Careful consideration of the placement of Microtrace markers within the PCB design to ensure optimal visibility and detection while minimizing interference with circuitry and components.
- Size and Density: Determining the appropriate size and density of Microtrace markers based on factors such as the resolution of detection equipment, the complexity of the PCB design, and the desired level of security.
- Compatibility: Ensuring compatibility between Microtrace PCB technology and other aspects of the PCB fabrication process, including substrate materials, solder masks, and surface finishes.
- Signal Integrity: Minimizing any potential impact of Microtrace markers on signal integrity, electrical performance, and reliability of the PCB.
- Verification and Testing: Establishing procedures for verifying the presence and integrity of Microtrace markers during PCB fabrication and assembly, as well as implementing testing protocols to validate the functionality and effectiveness of the technology.
- Documentation:Providing comprehensive documentation and labeling to clearly identify the presence of Microtrace markers within the PCB, including information on their location, type, and purpose.
By adhering to these guidelines, PCB designers can effectively incorporate Microtrace technology into their designs, enhancing security, traceability, and anti-counterfeiting measures for electronic components and devices.
What is the Microtrace PCB Fabrication Process?
The Microtrace PCB fabrication process involves integrating microscopic markers or identifiers directly into the printed circuit board (PCB) substrate during the manufacturing process. While specific details may vary depending on the manufacturer and technology used, the general steps typically include:
- Substrate Preparation:The process begins with the preparation of the PCB substrate material. This may involve selecting appropriate substrate materials such as FR-4 (fiberglass-reinforced epoxy), preparing the substrate surface, and applying any necessary pre-treatments.
- Marker Integration:Microtrace markers or identifiers are embedded into the PCB substrate material during the fabrication process. This can be achieved through various techniques, such as mixing marker materials into the substrate resin before lamination or using specialized equipment to imprint markers onto the substrate surface.
- Lamination:Once the markers are integrated into the substrate material, the layers of the PCB are laminated together using heat and pressure. This process ensures proper adhesion and bonding between the layers, effectively encapsulating the embedded markers within the PCB.
- Circuit Patterning:After lamination, the desired circuit patterns are created on the PCB layers using techniques such as etching or deposition. This step defines the electrical pathways and connections on the PCB.
- Surface Finishing: Surface finishing processes, such as applying solder masks and surface finishes (e.g., HASL, ENIG), are carried out to protect the PCB and facilitate soldering of components.
- Quality Control and Testing:Throughout the fabrication process, quality control measures are implemented to ensure the integrity and functionality of the PCB, including verification of the presence and integrity of Microtrace markers. Additionally, testing may be conducted to assess electrical performance, reliability, and adherence to specifications.
- Documentation and Labeling: Comprehensive documentation is provided to record details about the Microtrace markers integrated into the PCB, including their location, type, and purpose. Labels or markings may also be applied to the PCB to indicate the presence of Microtrace technology.
By integrating Microtrace markers directly into the PCB substrate during fabrication, this process provides a means of enhancing security, traceability, and anti-counterfeiting measures for electronic components and devices.
How do you manufacture a Microtrace PCB?
Manufacturing a Microtrace PCB involves incorporating microscopic markers or identifiers directly into the printed circuit board (PCB) substrate during the fabrication process. Here’s a general overview of the steps involved:
- Substrate Selection: Choose the appropriate substrate material for the PCB. Common materials include FR-4 (fiberglass-reinforced epoxy) or other substrates suitable for electronic applications.
- Marker Integration: Microtrace markers are embedded into the PCB substrate material. This can be done using various methods:
– Preparation of Marker Material: Prepare the microscopic markers or identifiers. These markers are typically composed of materials that are compatible with the PCB substrate and can withstand the manufacturing process.
– Mixing with Substrate Resin: Incorporate the markers into the substrate resin. This can involve mixing the marker material into the resin before the lamination process.
– Imprinting or Embedding: Utilize specialized equipment or techniques to imprint or embed the markers onto the surface or within the layers of the PCB substrate.
- Lamination: Once the markers are integrated into the substrate material, the layers of the PCB are laminated together. This involves applying heat and pressure to bond the layers and encapsulate the embedded markers within the PCB.
- Circuit Patterning: Define the desired circuit patterns on the PCB layers. This is typically done through processes such as etching or deposition, which create the electrical pathways and connections on the PCB.
- Surface Finishing: Apply surface finishing processes to the PCB. This may include applying solder masks and surface finishes such as HASL (Hot Air Solder Leveling) or ENIG (Electroless Nickel Immersion Gold) to protect the PCB and facilitate soldering of components.
- Quality Control and Testing: Implement quality control measures throughout the fabrication process to ensure the integrity and functionality of the PCB. This includes verifying the presence and integrity of Microtrace markers and conducting testing to assess electrical performance, reliability, and adherence to specifications.
- Documentation and Labeling: Provide comprehensive documentation detailing the Microtrace markers integrated into the PCB, including their location, type, and purpose. Additionally, labels or markings may be applied to the PCB to indicate the presence of Microtrace technology.
By integrating Microtrace markers directly into the PCB substrate during fabrication, this manufacturing process enhances security, traceability, and anti-counterfeiting measures for electronic components and devices.
How much should a Microtrace PCB cost?
The cost of a Microtrace PCB can vary depending on several factors, including the complexity of the design, the quantity ordered, the type of Microtrace technology used, and the specific requirements of the project. Additionally, factors such as the chosen PCB substrate material, surface finish, and additional features can also influence the overall cost.
Microtrace PCBs typically involve additional manufacturing steps and materials compared to standard PCBs, which can contribute to higher production costs. However, the exact cost will depend on the specifics of the project and the pricing structure of the manufacturer or supplier.
To get an accurate cost estimate for a Microtrace PCB, it’s best to consult with PCB manufacturers or suppliers who specialize in Microtrace technology. They can provide quotes based on your specific requirements and offer guidance on optimizing the design to balance cost-effectiveness with the desired security and traceability features.
What is Microtrace PCB base material?
The base material for Microtrace PCBs is typically the same as that used for standard printed circuit boards (PCBs). Common base materials include:
- FR-4 (Flame Retardant 4): FR-4 is a widely used substrate material for PCBs. It is a composite material composed of woven fiberglass cloth impregnated with an epoxy resin binder. FR-4 offers good electrical insulation properties, mechanical strength, and dimensional stability.
- FR-2 (Flame Retardant 2): FR-2 is another type of substrate material commonly used for PCBs. It consists of phenolic paper laminates impregnated with a phenolic resin binder. FR-2 is less expensive than FR-4 but has lower mechanical strength and dimensional stability.
- Polyimide (PI): Polyimide is a high-performance substrate material known for its excellent thermal stability, chemical resistance, and flexibility. It is often used in applications that require PCBs to withstand high temperatures or harsh environments.
- Rogers and Other Specialized Materials: In some cases, specialized substrate materials may be used for Microtrace PCBs, depending on specific performance requirements. Rogers Corporation, for example, offers a range of high-frequency laminates tailored for RF/microwave applications.
The choice of base material for a Microtrace PCB depends on factors such as the application, desired electrical and mechanical properties, thermal requirements, and budget constraints. It’s essential to select a substrate material that meets the performance and reliability requirements of the intended application while also accommodating the integration of Microtrace technology.
Which company makes Microtrace PCB?
Molded Interconnect Substrate (MIS) is an advanced circuit board technology that combines plastic injection molding and circuit printing techniques to achieve three-dimensional circuit routing and device integration. MIS technology finds wide applications in various fields including consumer electronics, automotive electronics, medical devices, and industrial controls.
Currently, there are several companies manufacturing MIS, including well-known manufacturers such as LPKF Laser & Electronics AG, Molex, Harting, Johnan, and DSM Engineering Materials. These companies are continuously improving MIS technology, driving its application across industries.
Our company has the capability to produce Molded Interconnect Substrate (MIS). As a company specialized in electronics manufacturing, we possess advanced production equipment, a professional technical team, and extensive experience, enabling us to provide high-quality, customized MIS solutions.
Our production process covers the entire process from design to manufacturing. Our engineering team collaborates with clients to design customized MIS solutions tailored to their specific requirements. We utilize advanced manufacturing techniques and high-quality materials to ensure the production of products that meet client specifications.
Our MIS products offer the following advantages:
- High integration: MIS technology allows for wiring and device integration in three-dimensional space, increasing the integration and performance of circuit boards.
- Design flexibility:Our engineering team can provide customized MIS solutions according to client design requirements, meeting the needs of different applications.
- Reliable quality: We strictly control the production process, using high-quality materials and advanced equipment to ensure the production of reliable MIS products.
- One-stop service: From design to production, we offer comprehensive services to ensure clients receive satisfactory products and solutions.
As a professional electronics manufacturing company, we are committed to providing clients with high-quality, innovative MIS solutions to help them succeed in various fields. We welcome clients to contact us to learn more about our MIS products and services.
What are the 7 qualities of good customer service?
The seven qualities of good customer service include:
- Promptness: Responding to customer inquiries, requests, and concerns in a timely manner demonstrates respect for their time and shows that you value their business.
- Professionalism: Maintaining a professional demeanor in all interactions with customers, including being courteous, empathetic, and knowledgeable, helps build trust and credibility.
- Empathy: Understanding and empathizing with the customer’s perspective and emotions allows you to address their needs and concerns effectively, fostering positive relationships.
- Effective Communication: Clear and concise communication is essential for ensuring that customers understand the information provided and feel heard and valued.
- Problem-Solving Skills: Being proactive and resourceful in resolving customer issues demonstrates a commitment to customer satisfaction and helps turn negative experiences into positive ones.
- Consistency: Providing consistently high-quality service across all interactions and touchpoints builds customer trust and loyalty over time.
- Personalization: Tailoring the customer experience to meet individual needs and preferences shows that you value and understand them as individuals, enhancing their overall satisfaction and loyalty.
By embodying these qualities, businesses can deliver exceptional customer service that exceeds expectations and fosters long-term relationships with their customers.
FAQs
What is Molded Interconnect Substrate (MIS)?
Molded Interconnect Substrate (MIS) is an advanced technology used in the manufacturing of electronic circuit boards. It combines plastic injection molding with circuit printing techniques to create three-dimensional circuitry and device integration.
What are the advantages of MIS?
MIS offers several advantages, including higher integration capabilities, reduced size and weight of electronic devices, improved reliability due to fewer interconnects, and the ability to create complex 3D designs.
What industries use MIS technology?
MIS technology finds applications in various industries, including consumer electronics, automotive electronics, medical devices, industrial controls, aerospace, and telecommunications.
How is MIS different from traditional PCBs?
Traditional PCBs are typically flat, while MIS allows for the integration of circuitry in three-dimensional space. This enables more compact and efficient designs, especially for small and complex electronic devices.
What materials are used in MIS?
MIS is often made using thermoplastic materials such as polycarbonate (PC), polyethylene terephthalate glycol (PETG), or liquid crystal polymer (LCP). These materials are chosen for their compatibility with injection molding processes and electrical properties.
Is MIS suitable for high-frequency applications?
Yes, MIS technology can be adapted for high-frequency applications by using specialized substrates and design techniques to minimize signal loss and maintain signal integrity.
Can MIS be customized for specific applications?
Yes, MIS can be customized to meet the specific requirements of different applications. This includes designing the circuit layout, selecting appropriate materials, and incorporating features such as RF shielding or thermal management.