Microtrace Package Substrate Manufacturer
Microtrace Package Substrate Manufacturer,Microtrace Package Substrate is a high-precision packaging substrate designed for microelectronic devices. It features micron-level trace lines to achieve extremely high signal accuracy and stability. This substrate utilizes advanced microfabrication techniques to support high-density integration of complex circuits, offering excellent thermal management and electrical performance. Widely applied in advanced semiconductor packaging, high-frequency communication equipment, and sensor technology, Microtrace Package Substrate provides reliable signal transmission and environmental adaptability for various critical applications.
What is a Microtrace Package Substrate?
A Microtrace Package Substrate refers to a specialized type of substrate used in integrated circuit (IC) packaging. It typically involves embedding very fine, micron-scale traces within the substrate material itself. These traces are crucial for routing signals between different components within the package, such as between the IC chip and external pins or other components on the substrate.
The key advantage of Microtrace Package Substrates lies in their ability to accommodate high-density interconnections in a compact space, which is essential for modern microelectronics where miniaturization and performance are critical. These substrates are often made from advanced materials like organic laminate or ceramics, depending on the application’s thermal and electrical requirements.
Manufacturing Microtrace Package Substrates involves precise fabrication processes such as laser drilling or micro-etching to create the intricate pathways. This level of precision ensures minimal signal loss and optimal electrical performance, meeting the stringent demands of high-speed digital circuits and other applications requiring reliable signal integrity.
In summary, Microtrace Package Substrates play a vital role in enabling the miniaturization and performance enhancements seen in today’s electronic devices, making them indispensable in advanced IC packaging technologies.
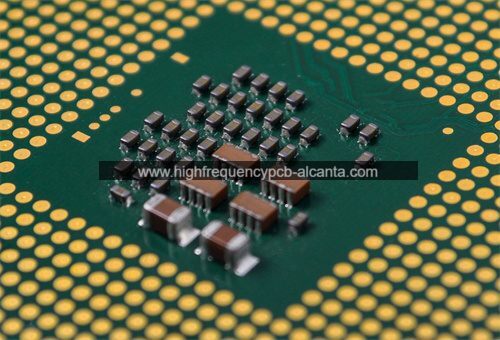
Microtrace Package Substrate Manufacturer
What are Microtrace Package Substrate Design Guidelines?
Designing Microtrace Package Substrates involves adhering to specific guidelines to ensure optimal performance and reliability. Here are some key design guidelines:
- Trace Width and Spacing: Maintain uniform trace widths and appropriate spacing between traces to minimize crosstalk and interference. Typically, for microtrace substrates, trace widths can be very narrow, often in the micron range, to achieve high-density routing.
- Dielectric Material Selection: Choose dielectric materials with low dielectric constant (εr) and low loss tangent (tan δ) to minimize signal attenuation and maintain signal integrity, especially at high frequencies.
- Via Design: Optimize via placement and size to minimize impedance variations and ensure robust electrical connections between layers. Microvias or fine-pitch vias are commonly used to achieve high-density interconnects.
- Signal Integrity Considerations: Analyze and simulate signal integrity (SI) parameters such as impedance matching, reflection, and transmission line effects to ensure reliable signal transmission and reception.
- Thermal Management: Incorporate thermal vias or other heat dissipation techniques to manage thermal loads effectively, particularly in high-power applications.
- Manufacturability: Design with manufacturability in mind, considering the capabilities of fabrication processes such as laser drilling, etching, and plating. Ensure designs are compatible with the chosen substrate material and manufacturing equipment.
- Electromagnetic Compatibility (EMC): Implement shielding techniques or ground planes to minimize electromagnetic interference (EMI) and ensure compliance with EMC regulations.
- Reliability and Testing:Design for reliability by considering factors such as mechanical stress, thermal cycling, and environmental conditions. Conduct thorough testing and validation of prototypes to verify performance under operational conditions.
By following these guidelines, designers can optimize Microtrace Package Substrate designs for high performance, reliability, and manufacturability, meeting the demanding requirements of advanced IC packaging applications.
What is the Microtrace Package Substrate Fabrication Process?
The fabrication process of Microtrace Package Substrates involves several key steps to achieve precise and reliable interconnects for integrated circuit (IC) packaging applications:
- Substrate Material Selection: Choose suitable substrate materials based on thermal, electrical, and mechanical requirements. Common materials include organic laminates or ceramics.
- Laser Drilling or Micro-Etching: Use advanced techniques such as laser drilling or micro-etching to create very fine vias and traces within the substrate material. This process is crucial for achieving high-density interconnections.
- Surface Preparation: Clean and prepare the substrate surfaces for subsequent processing steps, ensuring proper adhesion and conductivity.
- Circuit Patterning: Apply photoresist and use photolithography to define the circuit patterns on the substrate. This step involves exposing the photoresist to UV light through a mask, followed by developing and etching processes to create the desired trace patterns.
- Metal Deposition: Deposit metal (typically copper) onto the substrate surface using techniques such as sputtering or electroplating. The metal fills the vias and forms the conductive traces that connect different components within the package.
- Dielectric Layer Deposition: Deposit additional dielectric layers between metal layers to isolate traces and provide insulation. Choose dielectric materials with appropriate electrical properties to minimize signal loss and interference.
- Lamination and Pressing: For multi-layer substrates, laminate and press individual layers together under controlled temperature and pressure conditions. This step ensures proper bonding and alignment of vias across different layers.
- Surface Finishing: Apply surface finishes such as solder mask and surface treatment to protect exposed metal traces and facilitate soldering of components onto the substrate.
- Quality Assurance and Testing: Conduct rigorous quality control tests, including electrical testing, impedance measurement, and visual inspection, to ensure the substrate meets design specifications and reliability standards.
- Packaging: Package the finished substrate into appropriate containers or trays for further assembly into IC packages, ensuring protection from environmental contaminants and mechanical damage.
By following these fabrication steps with precision and attention to detail, manufacturers can produce Microtrace Package Substrates that offer high-density interconnectivity, excellent signal integrity, and reliability for advanced IC packaging applications.
How do you manufacture a Microtrace Package Substrate?
Manufacturing a Microtrace Package Substrate involves a series of meticulous steps to achieve precise interconnects suitable for advanced IC packaging. Here’s a detailed outline of the manufacturing process:
- Substrate Material Selection:Choose appropriate substrate materials based on thermal, electrical, and mechanical requirements. Options include organic laminates (e.g., FR-4) or ceramics (e.g., alumina or alumina-based materials for high-temperature applications).
- Panel Preparation:Prepare substrate panels by cutting them to size and cleaning them thoroughly to remove any contaminants that could affect subsequent processing steps.
- Laser Drilling or Mechanical Drilling:Use advanced techniques such as laser drilling or mechanical drilling to create microvias (small holes) in the substrate. These holes are crucial for forming the interconnections between different layers of the substrate.
- Electroless Copper Deposition:Initiate the build-up of conductive layers by depositing a thin layer of electroless copper over the entire substrate surface, including the walls of the microvias.
- Seed Layer Deposition:Deposit a thin seed layer of copper onto the substrate surface. This layer acts as a base for subsequent electroplating processes.
- Pattern Plating:Apply photoresist to the substrate surface and use photolithography techniques to define the circuit patterns. Expose the photoresist to UV light through a mask, develop it to remove unwanted areas, and then electroplate copper into the exposed patterned areas.
- Dielectric Layer Deposition:Deposit dielectric materials between metal layers to insulate and separate conductive traces. These layers help prevent electrical shorts and ensure proper signal routing.
- Lamination and Pressing:For multi-layer substrates, laminate individual layers together under controlled temperature and pressure conditions. This process bonds the layers and ensures proper alignment of vias across different layers.
- Surface Finishing:Apply surface finishes such as solder mask to protect exposed metal traces and facilitate soldering of components onto the substrate. Other surface treatments may include ENIG (Electroless Nickel Immersion Gold) for improved solderability and corrosion resistance.
- Quality Assurance and Testing:Conduct thorough quality control checks throughout the manufacturing process. Perform electrical testing, impedance measurement, and visual inspection to verify adherence to design specifications and reliability standards.
- Packaging:Package the finished substrate into suitable containers or trays for storage and transportation. Ensure proper handling to prevent damage to delicate features like microvias and fine traces.
By following these manufacturing steps with precision and using advanced equipment and techniques, manufacturers can produce Microtrace Package Substrates that meet the high-density interconnectivity and performance requirements of modern IC packaging applications.
How much should a Microtrace Package Substrate cost?
The cost of a Microtrace Package Substrate can vary significantly based on several factors, including:
- Complexity of Design: The complexity of the substrate design, including the number of layers, density of traces and vias, and the precision required in manufacturing, directly impacts the cost. More intricate designs that require finer features and tighter tolerances generally incur higher manufacturing costs.
- Substrate Material: The choice of substrate material influences costs. Ceramics such as alumina or specialized high-frequency laminates tend to be more expensive than standard FR-4 materials due to their superior electrical and thermal properties.
- Manufacturing Process: Advanced manufacturing processes such as laser drilling, fine-pitch photolithography, and precise deposition techniques (e.g., electroplating) contribute to higher costs compared to simpler processes.
- Volume and Scale: Economies of scale play a significant role. Larger production volumes typically reduce per-unit costs due to efficiencies in material usage, equipment utilization, and labor.
- Additional Features: Surface finishes (e.g., ENIG), special coatings for enhanced performance (e.g., impedance control), and testing requirements (e.g., electrical testing, reliability testing) can add to the overall cost.
- Supplier and Location: Costs can also vary based on the supplier’s pricing structure, geographic location, and their expertise in manufacturing high-precision substrates.
To provide a rough estimate, Microtrace Package Substrates can range from several dollars per square inch for simpler designs and standard materials to tens or even hundreds of dollars per square inch for complex, high-performance substrates with advanced features. Exact pricing would typically require detailed specifications and possibly consultation with substrate manufacturers to get accurate quotes based on specific project requirements.
What is a Microtrace Package Substrate base material?
A Microtrace Package Substrate base material typically refers to the primary material used as the substrate or base upon which the microtraces, vias, and circuit patterns are constructed for integrated circuit (IC) packaging. The choice of base material is critical as it determines the substrate’s electrical, thermal, and mechanical properties. Here are some common types of base materials used for Microtrace Package Substrates:
- Organic Laminates (e.g., FR-4):FR-4 is a widely used substrate material in electronics manufacturing. It consists of layers of woven fiberglass cloth impregnated with epoxy resin. FR-4 offers good electrical insulation properties, mechanical strength, and ease of processing. However, it may not be suitable for high-frequency applications due to its relatively high dielectric constant and loss tangent.
- Ceramics (e.g., Alumina, Aluminum Nitride):Ceramics such as alumina (Al2O3) and aluminum nitride (AlN) are preferred for high-frequency and high-power applications due to their excellent electrical insulation, thermal conductivity, and stability over a wide temperature range. These materials are capable of supporting fine features and high-density interconnects required in Microtrace Package Substrates.
- Specialized High-Frequency Laminates:For applications demanding superior electrical performance at high frequencies, specialized laminates with low dielectric constant (εr) and low loss tangent (tan δ) are used. Examples include PTFE-based materials (e.g., Rogers Corporation’s RO4000 series) and other proprietary formulations designed to minimize signal loss and maintain signal integrity.
- Metal Core Substrates:Metal core substrates incorporate a metal layer (typically aluminum or copper) as the base for improved thermal management. These substrates are used in applications requiring efficient heat dissipation, such as LED modules and power electronics.
The choice of base material depends on the specific requirements of the application, including operating frequency, power dissipation, thermal management needs, and cost considerations. Designers select the material that best balances these factors to achieve optimal performance and reliability in Microtrace Package Substrate designs.
Which company makes Microtrace Package Substrates?
Several internationally renowned companies and specialized manufacturers produce Microtrace Package Substrates, leveraging extensive experience and technological prowess in the high-performance IC packaging sector. For example, Materion Corporation, based in the United States, focuses on the development and manufacturing of high-performance alloys and specialty materials, offering solutions including Microtrace Package Substrates for the microelectronics and packaging industries. Another American company, Rogers Corporation, occupies a significant position in the market with its advanced high-frequency electronic materials and technologies, providing specialty laminates and substrates for applications in microwave, RF packaging, and more.
In Asia, companies like Nitto Denko from Japan and Sumitomo Electric Industries are also prominent manufacturers of Microtrace Package Substrates. Nitto Denko specializes in advanced films and functional materials, delivering advanced film substrates and material solutions for the electronic packaging sector. Sumitomo Electric Industries, renowned for its expertise in ceramics and metal substrates, provides solutions for high-temperature, high-frequency, and high-reliability applications.
As for our company, we boast advanced technological equipment and a highly experienced technical team dedicated to the design and manufacturing of high-performance Microtrace Package Substrates. We utilize state-of-the-art manufacturing processes such as laser drilling, fine-pitch photolithography, electroplating, and more to ensure our products meet the highest standards in density, signal integrity, and reliability. Our production processes adhere strictly to international standards and customer requirements, ensuring every detail meets optimized engineering design and manufacturing standards.
As a manufacturer, we not only deliver high-quality Microtrace Package Substrates but also offer customized solutions and technical support to help our customers gain a competitive edge in the electronic packaging industry. We are committed to providing cutting-edge packaging technology and material innovations globally, addressing increasingly complex market demands and application challenges.
What are the 7 qualities of good customer service?
Good customer service is characterized by several key qualities that enhance customer satisfaction and loyalty. Here are seven qualities of good customer service:
- Responsiveness:Good customer service involves promptly addressing customer inquiries, concerns, and requests. This includes timely responses to emails, phone calls, and messages, ensuring customers feel valued and their issues are being attended to promptly.
- Empathy: Empathy is crucial in customer service, as it involves understanding and acknowledging the customer’s emotions, concerns, and perspectives. Empathetic responses demonstrate care and build rapport with customers, fostering positive relationships.
- Clear Communication: Effective communication is essential in customer service interactions. This includes using clear and simple language, actively listening to customers to understand their needs, and providing information in a concise and understandable manner.
- Knowledgeability: Good customer service representatives possess a strong understanding of their products, services, and company policies. They can confidently answer questions, provide accurate information, and offer solutions or recommendations that meet the customer’s needs.
- Professionalism:Professionalism in customer service involves maintaining a courteous and respectful demeanor at all times, even in challenging situations. It includes being patient, maintaining composure, and adhering to company standards and ethical practices.
- Problem-Solving Skills: Effective problem-solving skills are crucial in resolving customer issues and complaints satisfactorily. Customer service representatives should be proactive in finding solutions, taking ownership of problems, and following through until the issue is resolved to the customer’s satisfaction.
- Personalization: Providing personalized customer service involves treating each customer as an individual with unique preferences and needs. This can include remembering customer preferences, addressing them by name, and offering tailored recommendations or solutions that align with their specific situation.
By embodying these qualities, organizations can deliver exceptional customer service experiences that build trust, enhance customer loyalty, and contribute to overall business success.
FAQs (Frequently Asked Questions)
What are Microtrace Package Substrates?
Microtrace Package Substrates are specialized substrates used in integrated circuit (IC) packaging, featuring very fine traces for high-density interconnects.
What materials are used in Microtrace Package Substrates?
Common materials include organic laminates like FR-4, ceramics such as alumina, and high-frequency laminates for specific applications.
What are the advantages of using Microtrace Package Substrates?
They offer high-density routing, improved signal integrity, and compact size, making them ideal for advanced electronic devices.
How are Microtrace Package Substrates manufactured?
The process involves laser drilling, photolithography, metal deposition, and lamination to create precise interconnects and multiple layers.
What applications use Microtrace Package Substrates?
They are used in high-frequency RF applications, advanced IC packaging, and any scenario requiring miniaturization and high performance.
How do you choose the right Microtrace Package Substrate?
Selection depends on factors like thermal and electrical requirements, application frequency, and mechanical constraints.
Can Microtrace Package Substrates be customized?
Yes, manufacturers can provide customized solutions tailored to specific design and performance needs, including trace dimensions and substrate materials.