Microtrace/Microwave Substrates Manufacturer
Microtrace/Microwave Substrates Manufacturer,Microtrace/Microwave Substrates are essential materials used in high-frequency electronic applications. With properties like low dielectric loss and high thermal conductivity, these substrates ensure optimal signal integrity and efficiency in circuits. They serve as the foundation for fabricating transmission lines, antennas, and other components vital for wireless communication, radar systems, and more. Fabricated through precise deposition and etching processes, these substrates offer reliability and performance crucial for modern electronic devices. Whether in satellite communication, automotive radar sensors, or medical equipment, Microtrace/Microwave Substrates play a pivotal role in enabling seamless connectivity and advanced technology.
What are Microtrace/Microwave Substrates?
Microtrace substrates, sometimes referred to as microwave substrates, are materials used in various applications, particularly in the field of microwave engineering and electronics. These substrates are designed to provide specific properties that enhance the performance of microwave devices and circuits.
Microtrace substrates typically have characteristics such as low dielectric loss, high thermal conductivity, and excellent dimensional stability. These properties are crucial for maintaining signal integrity, minimizing signal loss, and maximizing the efficiency of microwave components like antennas, filters, and amplifiers.
One common material used in microtrace substrates is ceramic-based composites, such as alumina (Al2O3) or aluminum nitride (AlN). These materials offer high thermal conductivity, allowing efficient heat dissipation, which is essential for high-power microwave applications.
Microtrace substrates are often engineered with precise dimensions and surface properties to enable the fabrication of microstrip transmission lines, which are essential components in microwave circuits. These transmission lines facilitate the propagation of electromagnetic waves at microwave frequencies while minimizing losses.
In addition to their use in microwave engineering, microtrace substrates find applications in other fields such as integrated circuits, radio frequency (RF) communication systems, and radar technology. Their versatility and performance characteristics make them indispensable in modern electronic devices and systems that operate at microwave frequencies.
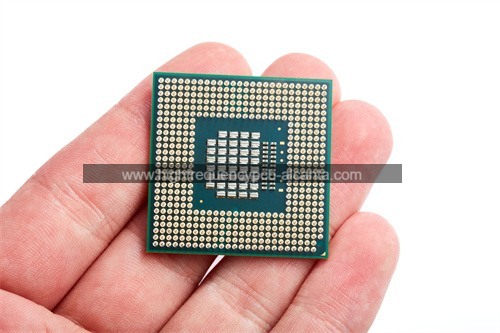
Microtrace/Microwave Substrates Manufacturer
What are the Microtrace/Microwave Substrates Design Guidelines?
Designing with microtrace or microwave substrates involves adhering to specific guidelines to ensure optimal performance of electronic components and circuits. Here are some key design guidelines:
- Dielectric Constant (ε_r): Select a substrate material with a dielectric constant appropriate for the application. The dielectric constant affects the characteristic impedance of transmission lines and the propagation velocity of electromagnetic waves. Lower dielectric constants are generally preferred for better signal integrity.
- Substrate Thickness: The substrate thickness determines the impedance of transmission lines and affects the coupling between traces. Thinner substrates are often preferred for high-frequency applications to minimize signal loss and reduce the size of components.
- Conductor Width and Spacing: Design transmission line traces with appropriate widths and spacing to achieve the desired characteristic impedance (usually 50 ohms for RF/microwave applications) and to minimize signal crosstalk and impedance mismatch.
- Grounding: Ensure proper grounding techniques, such as using ground planes or vias, to minimize electromagnetic interference (EMI) and to provide a stable reference plane for transmission lines.
- Thermal Management: Consider the thermal conductivity of the substrate material and incorporate thermal vias or heat sinks as needed to dissipate heat generated by high-power components or circuits.
- Surface Finish: Choose appropriate surface finishes for the substrate material to ensure good solderability and reliable electrical connections.
- Environmental Considerations: Take into account environmental factors such as temperature, humidity, and mechanical stress, and select substrate materials and construction techniques that can withstand the operating conditions.
- Manufacturability: Design with manufacturability in mind, considering factors such as substrate material availability, fabrication processes, and cost constraints.
- Simulation and Testing: Utilize electromagnetic simulation software and prototyping/testing techniques to validate the design and optimize performance before mass production.
By following these design guidelines, engineers can create robust and high-performance electronic components and circuits using microtrace or microwave substrates.
What is the Microtrace/Microwave Substrates Fabrication Process?
The fabrication process for microtrace or microwave substrates involves several steps to create the substrate material and then pattern it to form the desired circuitry. Here’s a general overview of the fabrication process:
- Substrate Material Selection: Choose a suitable substrate material based on the specific requirements of the application. Common materials include ceramics such as alumina (Al2O3) or aluminum nitride (AlN) due to their high thermal conductivity and low dielectric loss.
- Substrate Preparation: Begin with a clean substrate surface free of contaminants. The substrate may undergo surface treatment processes such as cleaning, etching, or surface roughening to improve adhesion of subsequent layers.
- Thin Film Deposition: Apply thin films of conductive and dielectric materials onto the substrate surface using techniques such as physical vapor deposition (PVD) or chemical vapor deposition (CVD). These thin films form the conductive traces, capacitors, and other circuit elements on the substrate.
- Photolithography: Use photolithography to pattern the deposited thin films. This process involves coating the substrate with a photoresist material, exposing it to ultraviolet (UV) light through a photomask with the desired circuit pattern, and then developing the exposed photoresist to remove unwanted areas.
- Etching: Etch away the exposed areas of thin films using wet or dry etching techniques, leaving behind the desired circuit pattern on the substrate surface. Etching selectively removes the conductive or dielectric material to define the traces and components of the circuit.
- Surface Finish: Apply a surface finish to the substrate to improve solderability and prevent oxidation of metal surfaces. Common surface finishes include immersion tin, immersion silver, and gold plating.
- Inspection and Testing: Inspect the fabricated substrate for defects and conduct electrical testing to verify the integrity and functionality of the circuitry. This may involve checking for continuity, impedance matching, and other electrical parameters.
- Packaging and Integration: Once the substrate is fabricated and tested, it may be packaged with other electronic components and integrated into larger systems or devices, such as RF modules, antennas, or microwave circuits.
Throughout the fabrication process, careful attention to detail is crucial to ensure the reliability, performance, and consistency of the fabricated microtrace or microwave substrate. Advanced fabrication facilities equipped with precision equipment and cleanroom environments are often used for producing high-quality substrates for demanding applications.
How do you manufacture Microtrace/Microwave Substrates?
Manufacturing microtrace or microwave substrates involves specialized processes to create materials with precise electrical and mechanical properties suitable for high-frequency electronic applications. Here’s an overview of the typical manufacturing process:
- Material Preparation: Start by preparing the substrate material, which is often a ceramic-based composite such as alumina (Al2O3) or aluminum nitride (AlN). The raw materials are mixed, shaped, and then sintered at high temperatures to form solid ceramic substrates with the desired properties, including low dielectric loss and high thermal conductivity.
- Thin Film Deposition: Thin films of conductive and dielectric materials are deposited onto the substrate surface using techniques such as physical vapor deposition (PVD) or chemical vapor deposition (CVD). These thin films form the conductive traces, capacitors, and other components of the circuit.
- Photolithography: Photolithography is used to define the circuit patterns on the substrate. A layer of photoresist material is applied to the substrate surface, exposed to UV light through a photomask, and then developed to remove the exposed areas, leaving behind the desired circuit pattern.
- Etching: The exposed areas of thin films are etched away using wet or dry etching processes, leaving behind the defined circuit traces and components on the substrate surface. Etching selectively removes the conductive or dielectric material according to the pattern defined by the photolithography step.
- Surface Finish: After etching, the substrate may undergo surface finishing processes to improve solderability and prevent oxidation of metal surfaces. Common surface finishes include immersion tin, immersion silver, and gold plating.
- Quality Control: Throughout the manufacturing process, quality control measures are implemented to ensure the integrity and performance of the substrates. This may include inspection of substrate dimensions, visual inspection for defects, and electrical testing to verify circuit functionality and performance.
- Packaging and Integration: Once manufactured and tested, the substrates may be packaged with other electronic components and integrated into larger systems or devices, such as RF modules, antennas, or microwave circuits.
Advanced manufacturing facilities equipped with precision equipment and cleanroom environments are typically used for producing high-quality microtrace or microwave substrates. These facilities adhere to strict quality standards to meet the demanding requirements of high-frequency electronic applications.
How much should Microtrace/Microwave Substrates cost?
The cost of microtrace or microwave substrates can vary widely depending on several factors, including the material used, substrate size and thickness, complexity of the circuitry, manufacturing processes involved, and the quantity ordered. Here are some factors that can influence the cost:
- Material Cost:The cost of the substrate material itself, such as alumina or aluminum nitride, can vary based on factors such as purity, availability, and supplier pricing.
- Manufacturing Processes:The complexity of the manufacturing processes involved, including thin film deposition, photolithography, etching, and surface finishing, can impact the overall cost. More complex processes may require specialized equipment and skilled labor, contributing to higher costs.
- Substrate Size and Thickness: Larger substrate sizes and thicker substrates typically require more material and may involve additional processing steps, leading to higher costs.
- Circuit Complexity: The complexity of the circuit patterns and the number of layers required on the substrate can affect the manufacturing time and materials needed, influencing the overall cost.
- Quantity Ordered: Economies of scale often apply in manufacturing, meaning that larger production quantities may result in lower unit costs due to efficiencies in material usage, setup time, and overhead expenses.
- Quality and Tolerance Requirements: Meeting tight tolerances and quality standards may require additional inspection and testing procedures, which can contribute to higher costs.
- Supplier and Geographic Location: The choice of supplier and their geographic location can impact costs due to differences in labor rates, overhead expenses, and shipping costs.
Due to these factors, it’s challenging to provide a specific cost estimate without knowing the details of the substrate specifications and manufacturing requirements. Typically, companies that require microtrace or microwave substrates will work closely with substrate manufacturers to obtain customized quotes based on their specific needs and volume requirements.
What is Microtrace/Microwave Substrates base material?
Microtrace or microwave substrates are typically made from materials with specific electrical and thermal properties suitable for high-frequency electronic applications. The choice of base material depends on the requirements of the application. Some common materials used as the base substrate for microtrace or microwave circuits include:
- Alumina (Al2O3): Alumina is a ceramic material known for its high thermal conductivity and excellent dielectric properties. It is widely used as a substrate material for microwave circuits due to its stability over a wide temperature range and low dielectric loss.
- Aluminum Nitride (AlN):Aluminum nitride is another ceramic material with high thermal conductivity and low dielectric loss, making it suitable for high-frequency applications. AlN substrates offer better thermal performance than alumina and are preferred for applications requiring efficient heat dissipation.
- Rogers RO4000 Series: Rogers Corporation produces a range of high-performance laminate materials specifically designed for microwave and RF applications. These materials are based on reinforced hydrocarbon and ceramic composites and offer excellent electrical properties, dimensional stability, and ease of fabrication.
- DuPont Pyralux®: DuPont offers flexible circuit materials such as Pyralux®, which are used for applications requiring flexibility or conformal shaping. These materials are based on polyimide substrates with copper foils and are suitable for high-frequency applications when designed properly.
- Glass Ceramic Substrates: Glass ceramic materials, such as glass-ceramic composites based on alumina or silica, are used for some specialized microwave applications. These materials offer a unique combination of low dielectric constant, high thermal conductivity, and dimensional stability.
These base materials provide the foundation for fabricating microtrace or microwave substrates, onto which thin films of conductive and dielectric materials are deposited to create the desired circuit patterns. The choice of base material depends on factors such as frequency of operation, power handling capability, thermal management requirements, and cost considerations.
Which company makes Microtrace/Microwave Substrates?
Microtrace/Microwave substrates are produced by several companies, including well-known manufacturers such as Rogers Corporation, DuPont, Murata Manufacturing, and Kyocera Corporation. These companies have rich experience and technology in the field of microwave and RF electronics, offering a variety of substrate products based on ceramics, polyimides, and composite materials.
As an emerging company, we can also manufacture Microtrace/Microwave substrates, providing high-quality products to customers through our advanced manufacturing technology and innovative process. Our manufacturing process is based on the latest materials science and engineering technology to ensure that our substrates meet customers’ stringent requirements and high standards.
Our manufacturing capabilities include the following key aspects:
- Material Selection and Design: We can choose suitable substrate materials according to customer requirements and design Microtrace/Microwave substrates that meet their performance requirements.
- Advanced Thin Film Deposition Technology: We employ advanced physical vapor deposition (PVD) and chemical vapor deposition (CVD) technologies to deposit thin film layers on the substrate surface for creating conductive paths and devices.
- Precision Photolithography and Etching Processes: We have advanced lithography equipment and etching processes to achieve precise circuit pattern definition and etching on the substrate, ensuring accurate circuit structures.
- Strict Quality Control: We have a comprehensive quality control system, from material inspection to finished product testing, to ensure that every Microtrace/Microwave substrate meets customer specifications and quality standards.
- Customized Production:We can customize Microtrace/Microwave substrates according to specific customer requirements, including dimensions, materials, circuit patterns, etc., to meet the needs of different application scenarios.
Through our efforts and innovation, we believe our company can become one of the leading players in the Microtrace/Microwave substrate manufacturing field, providing customers with high-quality products and services.
What are the 7 qualities of good customer service?
Good customer service is essential for building positive relationships with customers and fostering loyalty to a brand. Here are seven qualities that contribute to providing excellent customer service:
- Responsiveness: Responding promptly to customer inquiries, concerns, and requests demonstrates attentiveness and a commitment to meeting their needs in a timely manner. Whether it’s answering a phone call, replying to an email, or addressing a question on social media, being responsive shows customers that their satisfaction is a priority.
- Empathy: Showing empathy involves understanding and acknowledging the customer’s feelings, concerns, and perspectives. By putting yourself in the customer’s shoes and demonstrating empathy, you can create a more personalized and supportive interaction that builds trust and rapport.
- Clear Communication: Effective communication is crucial for conveying information clearly and ensuring that customers understand the solutions or options available to them. Using clear, concise language and actively listening to customers’ needs helps avoid misunderstandings and enhances the overall customer experience.
- Knowledgeability: Being knowledgeable about products, services, and company policies enables customer service representatives to provide accurate information and helpful guidance to customers. By demonstrating expertise and competence, you instill confidence in customers and increase their trust in the company.
- Professionalism: Maintaining professionalism in all interactions with customers, regardless of the circumstances, is essential for building credibility and fostering a positive impression of the brand. This includes maintaining a courteous demeanor, adhering to company guidelines and standards, and handling challenging situations with composure and respect.
- Problem-Solving Skills: Effective problem-solving involves identifying and resolving customer issues or complaints efficiently and effectively. Customer service representatives should be equipped with the skills and resources to address a wide range of problems, offering practical solutions that meet customers’ needs and expectations.
- Follow-Up and Follow-Through: Following up with customers after resolving an issue or completing a transaction shows that you value their feedback and are committed to their satisfaction. Additionally, following through on any promises or commitments made during the interaction reinforces trust and demonstrates reliability.
By embodying these qualities and consistently delivering exceptional customer service, businesses can cultivate strong customer relationships, drive customer loyalty, and differentiate themselves in the marketplace.
FAQs (Frequently Asked Questions)
What are Microtrace/Microwave Substrates?
Microtrace/Microwave substrates are materials used in high-frequency electronic applications, such as microwave engineering and RF circuits. They provide the foundation for fabricating components like transmission lines, antennas, and filters.
What are the key properties of Microtrace/Microwave Substrates?
Microtrace/Microwave substrates typically exhibit low dielectric loss, high thermal conductivity, and excellent dimensional stability. These properties are essential for maintaining signal integrity and minimizing losses in high-frequency circuits.
What materials are commonly used to make Microtrace/Microwave Substrates?
Common materials used for Microtrace/Microwave substrates include ceramics such as alumina (Al2O3) and aluminum nitride (AlN), as well as specialized laminate materials designed for high-frequency applications.
What are the applications of Microtrace/Microwave Substrates?
Microtrace/Microwave substrates are used in a wide range of applications, including wireless communication systems, radar technology, satellite communications, automotive radar sensors, and medical devices.
How are Microtrace/Microwave Substrates fabricated?
The fabrication process typically involves depositing thin films of conductive and dielectric materials onto the substrate surface, defining circuit patterns through photolithography and etching, and applying surface finishes to improve solderability and reliability.
What factors affect the cost of Microtrace/Microwave Substrates?
The cost of Microtrace/Microwave substrates can vary depending on factors such as the substrate material, size and thickness, complexity of the circuitry, manufacturing processes involved, and the quantity ordered.
Where can I purchase Microtrace/Microwave Substrates?
Microtrace/Microwave substrates are available from various manufacturers and suppliers specializing in high-frequency electronic components. You can contact these companies directly or through authorized distributors to inquire about purchasing options