Microtrace LED PCB Manufacturer
Microtrace LED PCB Manufacturer,Microtrace LED PCBs represent the pinnacle of precision engineering in the realm of printed circuit boards tailored for LED applications. Characterized by ultra-fine traces and meticulously crafted layouts, these PCBs enable the creation of high-density LED arrays and intricate electronic designs. Leveraging advanced manufacturing techniques such as photolithography and precision etching, Microtrace LED PCBs ensure optimal electrical connectivity and thermal management, vital for the performance and longevity of LED lighting systems. The compact nature of Microtrace LED PCBs makes them ideal for applications where space is at a premium, including but not limited to LED displays, automotive lighting, wearable devices, and medical instruments. With their ability to deliver exceptional performance in compact form factors, Microtrace LED PCBs exemplify innovation and efficiency in modern electronics design.
What is a Microtrace LED PCB?
As of my last update, the term “Microtrace LED PCB” isn’t a widely recognized or standard term in electronics. However, I can help clarify some of the components of the term:
- Microtrace: This likely refers to very small or fine “traces” on a PCB. Traces are the lines on a printed circuit board (PCB) that electrically connect various components. Microtraces would imply that these traces are particularly small, which could be crucial for high-density electronic circuits where space is a limiting factor and precision is crucial.
- LED: Stands for Light Emitting Diode, a type of electronic component that emits light when current flows through it. LEDs are used in a wide range of applications from basic indicator lights to advanced lighting systems.
- PCB: Stands for Printed Circuit Board, which is used to mechanically support and electrically connect electronic components using conductive pathways, or traces, etched from copper sheets laminated onto a non-conductive substrate.
Putting it all together, a “Microtrace LED PCB” could be interpreted as a printed circuit board designed for LEDs that features particularly fine or small traces. Such PCBs might be used in applications where high-resolution or high-density LED arrays are needed, such as in advanced lighting systems, displays, or in miniaturized devices where space is extremely limited.
If you have a specific context or product description where this term is used, that could help clarify further. Alternatively, this term might be specific to a certain manufacturer or a proprietary technology.
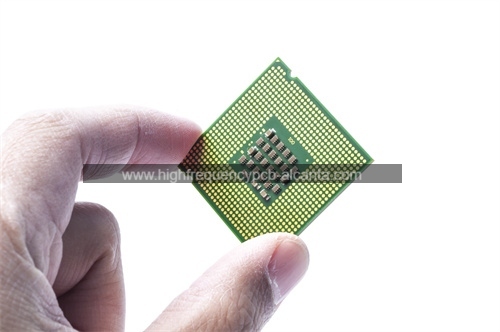
Microtrace LED PCB Manufacturer
What are the Microtrace LED PCB Design Guidelines?
While there might not be specific “Microtrace LED PCB Design Guidelines” as a standardized set of rules, designing a PCB for microtraces and LED applications typically involves considerations that are common in PCB design along with some specifics tailored to LED requirements and the need for fine traces. Here are some general guidelines that could be relevant:
- Trace Width and Spacing: For microtraces, you’ll likely need to use very small trace widths and spacings to fit more traces into a limited space. The specific values will depend on the manufacturing capabilities of your PCB fabrication service, but you may be looking at trace widths in the range of tens of micrometers.
- Material Selection: Choose PCB materials that offer good thermal conductivity and electrical insulation properties, especially if you’re designing for high-power LEDs. Thermal management is crucial for maintaining LED efficiency and lifespan.
- LED Placement and Orientation: Carefully plan the placement and orientation of the LEDs on the PCB to ensure optimal light distribution and minimize shadows. Consider factors such as viewing angles, light intensity, and uniformity across the illuminated area.
- Heat Dissipation: LEDs generate heat, especially high-power LEDs. Design the PCB layout to facilitate heat dissipation, which may include incorporating heat sinks, thermal vias, or copper pours to spread heat away from the LEDs and other sensitive components.
- Power Distribution: Ensure that power distribution traces can handle the current requirements of the LEDs without excessive voltage drop or heating. This may involve using wider traces or copper pours to lower resistance.
- Signal Integrity: Maintain signal integrity by adhering to best practices for impedance control, minimizing signal reflections, and reducing crosstalk between traces, especially important if your design includes high-speed data lines.
- Manufacturability: Keep manufacturability in mind throughout the design process. Ensure that the chosen trace widths and spacing are within the capabilities of your PCB manufacturer, and consider any additional manufacturing steps that may be required for fine traces or specific LED mounting methods.
- Testing and Prototyping: Prototype and test your design thoroughly, especially if you’re pushing the limits of trace size or working with high-power LEDs. Use simulations, breadboarding, or rapid prototyping techniques to validate the design before full-scale production.
Remember that these are general guidelines, and the specific requirements for your Microtrace LED PCB design will depend on factors such as the application, environmental conditions, budget, and manufacturing constraints. Always consult with experienced PCB designers and manufacturers to ensure the success of your project.
What is the Microtrace LED PCB Fabrication Process?
The fabrication process for Microtrace LED PCBs shares many steps with standard PCB fabrication, but it requires additional precision and attention to detail due to the smaller traces and specific requirements for LED integration. Here’s a general overview of the fabrication process:
- Design: Begin by creating the PCB design using PCB design software. Pay close attention to trace widths, spacing, LED placement, thermal management, and signal integrity considerations.
- Material Selection: Choose the appropriate PCB substrate material based on factors such as thermal conductivity, dielectric constant, and mechanical properties. Common materials for LED applications include FR-4, metal-core PCBs (MCPCB), and flexible PCBs (FPC).
- Preparation: Clean the substrate surface to remove any contaminants that could affect adhesion or conductivity. This may involve processes such as degreasing and chemical cleaning.
- Lamination: Apply a layer of copper foil to both sides of the substrate using a lamination process. This forms the conductive layers of the PCB.
- Photoresist Application: Apply a layer of photoresist to the copper surface. Photoresist is a light-sensitive material that will be used to create the PCB traces.
- Exposure and Development: Use a photomask or film to expose the photoresist to UV light, transferring the PCB design onto the photoresist. Develop the exposed photoresist to remove the unexposed areas, leaving behind the pattern of traces.
- Etching: Use an etchant solution (typically an acidic solution) to remove the exposed copper, leaving behind the desired traces. Rinse the PCB thoroughly to remove any remaining etchant.
- Surface Finish: Apply a surface finish to protect the exposed copper traces from oxidation and improve solderability. Common surface finishes include HASL (Hot Air Solder Leveling), ENIG (Electroless Nickel Immersion Gold), and OSP (Organic Solderability Preservatives).
- Drilling: Use a precision drilling machine to drill holes for component mounting and vias. The drill must be accurately aligned with the PCB design to ensure proper hole placement.
- Plating: Plate the drilled holes with copper to create vias, which establish electrical connections between different layers of the PCB.
- Solder Mask Application: Apply a solder mask layer to the PCB surface, leaving openings for component pads and vias. The solder mask protects the PCB traces from environmental damage and prevents unintended solder bridges during assembly.
- Silkscreen Printing: Optionally, add component labels, reference designators, and other markings to the PCB surface using silkscreen printing.
- Final Inspection: Inspect the finished PCB for defects such as missing traces, shorts, or misaligned features. Automated optical inspection (AOI) and electrical testing may be performed to ensure quality and functionality.
- Assembly: Finally, assemble the PCB by soldering LED components and other electronic components onto the board using automated or manual assembly processes.
Throughout the fabrication process, strict quality control measures should be implemented to ensure the final Microtrace LED PCB meets the required specifications for size, accuracy, and performance. Collaboration between design engineers and PCB manufacturers is essential to address any challenges and optimize the fabrication process for Microtrace LED PCBs.
How do you manufacture a Microtrace LED PCB?
Manufacturing a Microtrace LED PCB involves a series of steps that require precision equipment and attention to detail. Here’s a simplified overview of the manufacturing process:
- Design: Start with the PCB design, considering the specific requirements for microtraces and LED integration. Use PCB design software to create the layout, paying close attention to trace widths, spacing, LED placement, thermal management, and signal integrity.
- Material Selection: Choose the appropriate PCB substrate material based on factors such as thermal conductivity, dielectric constant, and mechanical properties. Common materials for LED applications include FR-4, metal-core PCBs (MCPCB), and flexible PCBs (FPC).
- Photolithography: Begin the manufacturing process by applying a layer of photoresist onto the substrate. Then, expose the photoresist to UV light through a photomask that contains the pattern of traces. This step transfers the PCB design onto the photoresist.
- Etching:Use an etchant solution (typically an acidic solution) to remove the exposed copper, leaving behind the desired traces on the substrate. Rinse the PCB thoroughly to remove any remaining etchant.
- Drilling: Use a precision drilling machine to drill holes for component mounting and vias. The drill must be accurately aligned with the PCB design to ensure proper hole placement.
- Plating: Plate the drilled holes with copper to create vias, which establish electrical connections between different layers of the PCB. This may involve processes such as electroplating or chemical deposition.
- Solder Mask Application: Apply a solder mask layer to the PCB surface, leaving openings for component pads and vias. The solder mask protects the PCB traces from environmental damage and prevents unintended solder bridges during assembly.
- Silkscreen Printing: Optionally, add component labels, reference designators, and other markings to the PCB surface using silkscreen printing.
- Surface Finish: Apply a surface finish to protect the exposed copper traces from oxidation and improve solderability. Common surface finishes include HASL (Hot Air Solder Leveling), ENIG (Electroless Nickel Immersion Gold), and OSP (Organic Solderability Preservatives).
- Component Assembly: Place and solder LED components and other electronic components onto the PCB using automated or manual assembly processes. Pay attention to the orientation and alignment of the components to ensure proper functionality.
- Inspection and Testing: Inspect the finished PCB for defects such as missing traces, shorts, or misaligned components. Automated optical inspection (AOI) and electrical testing may be performed to ensure quality and functionality.
- Quality Control:Implement strict quality control measures throughout the manufacturing process to ensure that the final Microtrace LED PCB meets the required specifications for size, accuracy, and performance.
By following these steps with precision and attention to detail, manufacturers can produce high-quality Microtrace LED PCBs that meet the specific requirements of LED applications. Collaboration between design engineers and PCB manufacturers is essential to optimize the manufacturing process and address any challenges that may arise.
How much should a Microtrace LED PCB cost?
The cost of a Microtrace LED PCB can vary widely depending on several factors, including the complexity of the design, the size of the board, the number of layers, the materials used, the manufacturing process, and the quantity ordered. Here are some factors that can influence the cost:
- Design Complexity: PCBs with intricate microtraces and densely packed components may require more advanced manufacturing processes, which can increase costs.
- Number of Layers: Multi-layer PCBs are more complex to manufacture than single-layer PCBs and typically cost more due to the additional materials and processing steps involved.
- Material Selection: The choice of PCB substrate material, surface finish, and solder mask type can impact the cost. High-performance materials with specialized properties may be more expensive than standard FR-4.
- Manufacturing Process: Advanced manufacturing processes such as laser drilling, controlled impedance, and fine-pitch soldering can increase manufacturing costs.
- Quantity: Economies of scale apply in PCB manufacturing, meaning that larger quantities often result in lower per-unit costs due to bulk discounts and more efficient production processes.
- Turnaround Time: Expedited production or quick-turn services may incur additional fees compared to standard lead times.
- Quality Standards:Meeting certain quality standards or certifications (e.g., IPC Class standards) may add to the manufacturing cost.
- Supplier and Location: The choice of PCB manufacturer and their location can influence costs due to differences in labor costs, overhead expenses, and shipping fees.
As a rough estimate, the cost of a Microtrace LED PCB could range from a few dollars for a simple single-layer board to several hundred dollars or more for a complex multi-layer board with advanced features. For a more accurate cost estimate, it’s best to consult with PCB manufacturers and provide them with detailed specifications of your design and requirements. Many PCB manufacturers offer online quotation tools where you can input your design parameters to get a cost estimate.
What is the Microtrace LED PCB base material?
The choice of base material for a Microtrace LED PCB depends on various factors such as thermal conductivity, electrical insulation properties, mechanical strength, and cost considerations. Here are some common base materials used in Microtrace LED PCBs:
- FR-4 (Flame Retardant 4): FR-4 is a widely used and cost-effective substrate material for PCBs. It consists of a woven fiberglass cloth impregnated with an epoxy resin binder. FR-4 offers good electrical insulation properties and mechanical strength, making it suitable for a wide range of applications.
- Metal-Core PCB (MCPCB): MCPCB features a metal core, typically aluminum or copper, sandwiched between layers of dielectric material (usually FR-4 or another thermally conductive material). The metal core provides excellent thermal conductivity, making MCPCB ideal for LED applications where heat dissipation is critical.
- Flexible PCB (FPC): FPC is a thin, flexible substrate material made of polyimide or polyester film. FPCs are lightweight, compact, and can be bent or twisted to fit into tight spaces, making them suitable for applications with space constraints.
- Ceramic Substrates: Ceramic substrates such as aluminum oxide (Al2O3) or aluminum nitride (AlN) offer superior thermal conductivity compared to traditional PCB materials. Ceramic substrates are well-suited for high-power LED applications where efficient heat dissipation is essential.
- Polyimide (PI): Polyimide is a high-temperature resistant polymer often used as a substrate material for flexible PCBs. Polyimide offers excellent thermal stability and mechanical flexibility, making it suitable for applications requiring a combination of heat resistance and flexibility.
The choice of base material depends on the specific requirements of the LED application, including thermal management, mechanical flexibility, and electrical performance. Designers must carefully consider these factors when selecting the base material for a Microtrace LED PCB to ensure optimal performance and reliability.
Which company makes Microtrace LED PCBs?
There are currently many companies that offer manufacturing services for Microtrace LED PCBs. Some well-known companies include Aurora Circuits, RUSH PCB, Advanced Circuits, and RayMing Technology. These companies have advanced manufacturing equipment and technology and can produce high-quality Microtrace LED PCBs according to customer requirements.
As for our company, we also have the capability to provide manufacturing services for Microtrace LED PCBs. We have advanced PCB manufacturing equipment and a skilled technical team capable of producing Microtrace LED PCBs according to customer design requirements and technical specifications. Our manufacturing process can achieve small trace sizes and ensure excellent thermal management and electrical performance of the PCBs. We can also select suitable substrate materials, such as FR-4, metal-core boards, or flexible substrates, to meet the requirements of different applications.
In addition to manufacturing capabilities, we prioritize quality control and customer service. We adhere strictly to international and industry standards to ensure that every stage of production meets the highest quality standards. Our customer service team is professional and efficient, providing timely responses to customer needs and offering comprehensive technical support and solutions.
In summary, as a professional PCB manufacturing company, we have the ability and experience to produce Microtrace LED PCBs and are committed to providing customers with high-quality customized solutions. We are willing to cooperate with customers to promote the development and innovation of LED applications.
What are the 7 qualities of good customer service?
Good customer service is characterized by several key qualities that help to ensure positive interactions and satisfaction for customers. Here are seven important qualities:
- Responsiveness: Good customer service involves being prompt and responsive to customer inquiries, requests, and concerns. This includes answering phone calls and emails promptly, providing timely assistance, and addressing issues in a timely manner.
- Empathy: Empathy is the ability to understand and share the feelings of others. Good customer service representatives demonstrate empathy by listening attentively to customers, acknowledging their concerns, and showing genuine concern for their needs and experiences.
- Communication Skills: Effective communication is essential for good customer service. This includes being able to convey information clearly and concisely, actively listening to customers to understand their needs, and providing information in a helpful and understandable manner.
- Problem-Solving Skills: Good customer service involves being able to effectively resolve customer issues and problems. This requires critical thinking, problem-solving skills, and the ability to find creative solutions to meet customer needs.
- Professionalism: Professionalism encompasses behaviors and attitudes that reflect positively on the company and create a positive impression for customers. This includes being courteous, respectful, and maintaining a positive attitude, even in challenging situations.
- Product Knowledge: Good customer service representatives have a thorough understanding of the products or services offered by the company. They can provide accurate information, answer questions knowledgeably, and offer helpful recommendations or suggestions to customers.
- Follow-Up: Following up with customers after a service interaction is an important aspect of good customer service. This may involve checking in to ensure that the customer’s issue was resolved satisfactorily, providing additional assistance if needed, or soliciting feedback to improve future interactions.
By embodying these qualities, companies can cultivate positive relationships with their customers, enhance satisfaction and loyalty, and ultimately contribute to the success of the business.
FAQs
What are Microtrace LED PCBs?
Microtrace LED PCBs are printed circuit boards designed specifically for LED applications, featuring very small or fine traces that enable high-density LED arrays and precise electrical connections.
What are the advantages of Microtrace LED PCBs?
Microtrace LED PCBs offer advantages such as higher LED density, improved thermal management, precise electrical connections, and enhanced design flexibility for applications with limited space constraints.
What applications are Microtrace LED PCBs used for?
Microtrace LED PCBs are used in a wide range of applications, including LED lighting fixtures, display panels, automotive lighting, signage, wearable devices, medical devices, and more.
How are Microtrace LED PCBs manufactured?
The manufacturing process for Microtrace LED PCBs involves specialized techniques for creating fine traces, precise LED placement, and efficient thermal management. This typically includes processes such as photolithography, etching, drilling, plating, and assembly.
What materials are used in Microtrace LED PCBs?
Common materials used in Microtrace LED PCBs include FR-4 (Flame Retardant 4), metal-core PCB substrates (MCPCB), flexible PCB substrates (FPC), and ceramic substrates. The choice of material depends on factors such as thermal conductivity, flexibility, and application requirements.
What factors should be considered when designing Microtrace LED PCBs?
Design considerations for Microtrace LED PCBs include trace width and spacing, thermal management, LED placement and orientation, material selection, power distribution, signal integrity, and manufacturability.
Can Microtrace LED PCBs be customized for specific applications?
Yes, Microtrace LED PCBs can be customized to meet the specific requirements of different applications. This includes adjusting trace sizes, choosing appropriate materials, optimizing thermal management, and incorporating features tailored to the application’s needs.
Where can I purchase Microtrace LED PCBs?
Microtrace LED PCBs can be purchased from specialized PCB manufacturers or suppliers that offer custom PCB manufacturing services. It’s important to choose a reputable manufacturer with experience in producing high-quality Microtrace LED PCBs.