Microtrace HDI PCB Manufacturer
Microtrace HDI PCB Manufacturer,Microtrace HDI PCBs are advanced printed circuit boards utilizing High-Density Interconnect (HDI) technology. With intricate layering and precision drilling of microvias, they offer unparalleled circuit density, making them ideal for compact electronic devices. These boards ensure enhanced signal integrity, reduced electromagnetic interference, and improved reliability. Designed for high-performance applications such as smartphones, medical devices, and aerospace systems, Microtrace HDI PCBs exemplify cutting-edge technology, enabling smaller, lighter, and more efficient electronic products.
What is a Microtrace HDI PCB?
A Microtrace HDI (High-Density Interconnect) PCB, is a type of printed circuit board designed with advanced technology to accommodate a higher density of electronic components in a smaller space. HDI technology allows for more intricate routing and compact layouts, making it ideal for devices where space is limited, such as smartphones, tablets, and wearable devices.
The term “Microtrace” likely refers to the fine traces and microvias used in these PCBs, which enable high-speed signal transmission and improved electrical performance. These PCBs typically involve multiple layers of circuitry interconnected through microvias, which are tiny holes drilled with laser technology to connect different layers. This allows for greater routing flexibility and reduces signal interference, enhancing overall reliability and performance.
In summary, a Microtrace HDI PCB offers superior density, performance, and reliability compared to traditional PCBs, making it a preferred choice for compact and high-performance electronic devices.
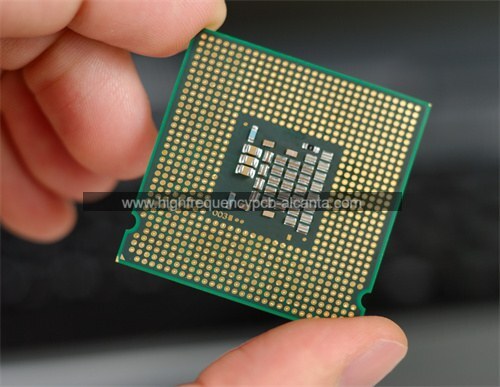
Microtrace HDI PCB Manufacturer
What are the Microtrace HDI PCB Design Guidelines?
Microtrace HDI PCB design guidelines can vary depending on the specific requirements of the project and the capabilities of the manufacturing process. However, here are some general guidelines that are commonly followed when designing HDI PCBs:
- Layer Stackup: Determine the layer stackup based on the number of signal layers, power planes, and ground planes required for the design. HDI PCBs often involve multiple layers stacked closely together to achieve high density.
- Minimum Feature Size: Be aware of the minimum feature size limitations imposed by the manufacturing process, including minimum trace width, spacing between traces, and drill size.
- Aspect Ratio: Consider the aspect ratio of vias (the ratio of their depth to diameter). HDI PCBs often use microvias, which have high aspect ratios. Ensure that the aspect ratio is within the manufacturer’s capabilities to avoid reliability issues during fabrication.
- Via Types: Select appropriate via types for the design, including blind vias, buried vias, and microvias. Microvias are commonly used in HDI PCBs due to their smaller size and higher density capabilities.
- Pad and Annular Ring Sizes: Design pads and annular rings (the copper area around the hole of a via) to accommodate the required drill sizes and manufacturing tolerances.
- Routing Considerations: Optimize routing to minimize signal integrity issues such as crosstalk and impedance mismatches. Use controlled impedance routing where necessary and maintain appropriate signal-to-ground ratios.
- Thermal Management: Consider thermal management strategies, such as the placement of thermal vias or thermal pads, to dissipate heat effectively, especially in high-power applications.
- Design for Manufacturability (DFM): Follow DFM principles to ensure that the design can be manufactured reliably and cost-effectively. This includes avoiding overly complex designs that may increase fabrication time and cost.
- Signal Integrity Analysis: Perform signal integrity analysis to validate the design and ensure that it meets performance requirements, especially for high-speed signals.
- Documentation:Provide comprehensive documentation, including a detailed PCB layout, fabrication drawings, and assembly instructions, to facilitate the manufacturing process and ensure consistency.
These guidelines should be adapted based on the specific requirements of the project and the capabilities of the manufacturer producing the Microtrace HDI PCBs. Collaboration with the PCB manufacturer early in the design process is crucial to ensuring a successful outcome.
What is the Microtrace HDi PCB Fabrication Process?
The fabrication process for Microtrace HDI PCBs follows a series of steps, which may vary slightly depending on the specific requirements of the project and the capabilities of the manufacturer. Here’s a general overview of the fabrication process:
- Design Input: The process begins with the design input, where the PCB design files are provided to the manufacturer. These files typically include the PCB layout, layer stackup information, drill files, and any other relevant documentation.
- Preparation of Substrate:The fabrication process starts with the preparation of the substrate material, usually a laminate or a combination of laminates with different properties. The substrate material is cleaned, and a thin layer of copper is bonded to one or both sides, depending on the design requirements.
- Drilling: Holes are drilled into the substrate material using precision drilling equipment. Microvias, which are small diameter holes, are often used in HDI PCBs to achieve high-density interconnections. Laser drilling or mechanical drilling techniques may be employed depending on the design specifications.
- Copper Plating: After drilling, the holes are plated with copper to form the conductive vias. This process involves depositing a thin layer of copper on the walls of the drilled holes, creating electrical connections between different layers of the PCB.
- Lamination: The individual layers of the PCB are laminated together using heat and pressure to form a solid, multilayered structure. The layers may include signal layers, power planes, and ground planes, as well as any buried or blind vias.
- Circuit Patterning: Photoresist is applied to the surface of the PCB and exposed to UV light through a photomask, which defines the circuit pattern. The exposed areas of the photoresist are then developed, leaving behind the desired circuit pattern on the copper surface.
- Etching: The PCB is submerged in an etchant solution, which removes the unwanted copper from the surface, leaving behind the circuit traces and features defined by the photoresist mask.
- Surface Finishing: Surface finishing processes are applied to protect the exposed copper surfaces from oxidation and improve solderability. Common surface finishes for HDI PCBs include ENIG (Electroless Nickel Immersion Gold), HASL (Hot Air Solder Leveling), and OSP (Organic Solderability Preservatives).
- Final Inspection: The finished PCBs undergo thorough inspection to ensure that they meet the quality standards and specifications defined by the customer. This may include visual inspection, electrical testing, and dimensional measurements.
- Panelization and Separation: If multiple PCBs are fabricated on a single panel, they are separated into individual units using precision milling or routing equipment.
- Packaging and Shipping: The finished PCBs are packaged according to customer requirements and shipped to the designated destination for assembly and integration into electronic products.
Throughout the fabrication process, strict quality control measures are implemented to ensure that the finished HDI PCBs meet the performance, reliability, and dimensional accuracy requirements specified by the customer. Collaboration between the PCB designer and the manufacturer is essential to optimize the fabrication process and achieve the desired results.
How Do You Manufacture a Microtrace HDI PCB?
Manufacturing a Microtrace HDI (High-Density Interconnect) PCB involves several steps, each crucial to achieving the desired level of miniaturization, high density, and performance. Here’s a generalized overview of the manufacturing process:
- Design Preparation: The process starts with PCB design using specialized PCB design software. Designers create the layout considering the specific requirements of the project, including layer stackup, trace routing, via placement, and signal integrity considerations.
- Material Selection: Choose appropriate materials for the PCB based on factors like dielectric constant, thermal conductivity, and compatibility with manufacturing processes. High-quality materials are essential for achieving desired electrical and mechanical properties.
- Layer Lamination: HDI PCBs often have multiple layers of copper and insulating material laminated together. The layers are bonded using heat and pressure to form a single rigid structure.
- Drilling: Precision drilling is performed to create vias, including microvias, blind vias, and buried vias. Microvias are drilled using lasers or mechanical drills with diameters typically less than 150 micrometers.
- Copper Plating: After drilling, the via walls are plated with copper to provide electrical conductivity and ensure proper interconnection between layers.
- Circuit Patterning: Photolithography is used to selectively remove copper from the surface of the PCB to create circuit patterns. A photoresist is applied, exposed to UV light through a mask, developed to remove the unexposed areas, and then etched to remove the unwanted copper.
- Surface Finishing: Apply surface finishes to protect the exposed copper traces and pads from oxidation and facilitate soldering during assembly. Common surface finishes include immersion gold, immersion silver, OSP (Organic Solderability Preservative), and ENIG (Electroless Nickel Immersion Gold).
- Solder Mask Application: Apply solder mask over the entire PCB surface, leaving openings for exposed pads and vias. The solder mask protects the copper traces from environmental factors and prevents solder bridges during assembly.
- Silkscreen Printing: Optionally, silkscreen printing can be performed to add labels, component outlines, and other markings on the PCB surface for assembly and identification purposes.
- Testing and Inspection:Perform electrical testing, such as continuity testing and impedance testing, to ensure that the manufactured PCB meets the required specifications. Visual inspection is also conducted to identify any defects or irregularities in the PCB.
- Final Finishing: Trim the PCB to its final dimensions and perform any additional finishing processes, such as edge plating or beveling, as required.
- Packaging and Shipping: Once the PCBs pass quality control checks, they are packaged according to customer specifications and shipped to the assembly facility for component placement and soldering.
Throughout the manufacturing process, stringent quality control measures are implemented to ensure that the Microtrace HDI PCBs meet the highest standards for performance, reliability, and consistency. Collaboration between designers, engineers, and manufacturers is essential to optimize the design for manufacturability and achieve the desired outcomes.
How Much Should a Microtrace HDI PCB Cost?
The cost of a Microtrace HDI PCB can vary significantly depending on various factors such as:
- Board Size and Complexity: Larger boards with intricate designs and high layer counts will generally cost more to manufacture due to increased material and processing requirements.
- Layer Count: HDI PCBs often have multiple layers, including microvias, buried vias, and blind vias. The more layers involved, the higher the manufacturing cost.
- Material Selection: High-quality materials with specific properties may incur higher costs compared to standard PCB materials.
- Feature Density: Higher feature density, including smaller traces and vias, increases manufacturing complexity and thus can raise the cost.
- Surface Finish:Different surface finishes, such as immersion gold or ENIG, have different costs associated with them.
- Quantities: Bulk orders typically result in lower per-unit costs due to economies of scale. However, smaller quantities may incur setup fees or higher per-unit costs.
- Lead Time: Expedited manufacturing or delivery may come with additional costs.
- Manufacturer: Different PCB manufacturers have varying pricing structures, capabilities, and quality levels.
- Additional Services: Any additional services required, such as electrical testing, panelization, or special packaging, can add to the overall cost.
Without specific details about the design requirements and manufacturing specifications, it’s challenging to provide an exact cost. However, as a rough estimate, Microtrace HDI PCBs can range from a few dollars for simple prototypes to several hundred dollars or more for complex, high-density designs in larger quantities.
For accurate pricing, it’s recommended to consult with multiple PCB manufacturers, provide detailed design specifications, and request quotes tailored to your specific needs.
What is Microtrace HDI PCB Base Material?
The base material used in Microtrace HDI PCBs can vary depending on the specific requirements of the application and the manufacturer’s capabilities. However, commonly used base materials for HDI PCBs include:
- FR-4: FR-4 (Flame Retardant 4) is a widely used substrate material for PCBs due to its cost-effectiveness, good electrical insulation properties, and availability in various thicknesses and grades.
- High-Frequency Laminates: For high-frequency applications where signal integrity is critical, specialized high-frequency laminates such as Rogers or Taconic materials may be used. These materials offer excellent electrical properties and low signal loss at high frequencies.
- Low-Dk and Low-Df Materials: Low-Dk (Dielectric Constant) and low-Df (Dissipation Factor) materials are used in applications requiring minimal signal distortion and high-speed performance. These materials provide excellent signal integrity and are often chosen for advanced HDI PCB designs.
- Flex and Rigid-Flex Materials: In flexible or rigid-flex HDI PCBs, flexible substrates such as polyimide or polyester are used to allow the PCB to bend or conform to complex shapes. These materials offer flexibility while maintaining electrical performance.
- Thermal Substrates: For applications requiring efficient heat dissipation, thermal substrates such as aluminum or copper-based laminates may be used as the base material. These materials help dissipate heat generated by components on the PCB, improving reliability and performance.
The choice of base material depends on factors such as electrical performance requirements, thermal management needs, cost considerations, and compatibility with the manufacturing process. It’s essential to select a base material that meets the specific requirements of the HDI PCB design while ensuring optimal performance and reliability. Collaboration with the PCB manufacturer is crucial in selecting the most suitable base material for the intended application.
Which Company Makes Microtrace HDI PCB?
Microtrace HDI PCB may be a product line or brand of a company specialized in producing high-density interconnect printed circuit boards. However, there is no specific company information directly related to “Microtrace HDI PCB.” Typically, such products are manufactured by professional PCB manufacturers.
Many well-known PCB manufacturers have advanced technology and equipment to produce high-density interconnect printed circuit boards, including Microtrace HDI PCBs. These companies usually have extensive experience to meet various complex design requirements and provide high-quality, reliable products.
For our company, we can produce Microtrace HDI PCBs through the following means:
- Advanced manufacturing equipment:We have advanced PCB manufacturing equipment, including high-precision drilling machines, lasers, chemical processing equipment, and automated production lines. These devices enable precise processing and efficient production to ensure product quality and consistency.
- Rich experience and expertise:Our team has extensive experience and expertise in HDI PCB design and manufacturing processes. We can provide professional consulting services to customers and customize solutions based on their needs.
- Quality control and testing:We strictly adhere to quality management systems, including comprehensive control and inspection from raw material procurement to production processes. Our products undergo rigorous testing and validation to ensure compliance with customer requirements and industry standards.
- Customized services for customers:We are committed to providing customized solutions to meet customers’ specific design and performance requirements. We can produce Microtrace HDI PCBs according to customer design files and specifications, providing timely technical support and after-sales service.
In summary, our company has the advanced equipment, extensive experience, and professional expertise required to produce Microtrace HDI PCBs, meeting customer needs and providing high-quality, reliable products.
What are the 7 Qualities of Good Customer Service?
Good customer service is essential for building strong relationships with customers and ensuring their satisfaction. Here are seven qualities that characterize good customer service:
- Responsiveness: Good customer service involves promptly addressing customer inquiries, concerns, and requests. Whether through phone, email, chat, or in-person interaction, being responsive demonstrates attentiveness and a willingness to help.
- Empathy: Empathy is the ability to understand and share the feelings of others. Good customer service representatives empathize with customers’ frustrations or challenges and strive to resolve issues with compassion and understanding.
- Communication Skills: Effective communication is crucial in customer service. Clear and concise communication helps customers understand solutions or information provided, leading to better outcomes and enhanced satisfaction.
- Product Knowledge: Good customer service representatives have a thorough understanding of the products or services they support. They can provide accurate information, answer questions, and offer relevant recommendations to help customers make informed decisions.
- Problem-Solving Skills: Customers may encounter issues or challenges, and good customer service involves effective problem-solving. Representatives should be resourceful, analytical, and proactive in resolving issues promptly and satisfactorily.
- Professionalism: Professionalism encompasses various qualities, including courtesy, integrity, and reliability. Good customer service representatives maintain professionalism in their interactions, regardless of the situation, to build trust and credibility with customers.
- Personalization: Tailoring interactions to meet individual customer needs and preferences is a hallmark of good customer service. By recognizing and addressing customers on a personal level, representatives can create positive experiences and foster loyalty.
By embodying these qualities, organizations can deliver exceptional customer service that not only meets but exceeds customer expectations, leading to increased satisfaction, loyalty, and advocacy.
FAQs
What is Microtrace HDI PCB?
Microtrace HDI PCB refers to a type of printed circuit board (PCB) utilizing High-Density Interconnect (HDI) technology. It allows for greater circuit density and miniaturization, making it ideal for compact electronic devices.
What are the benefits of Microtrace HDI PCB?
Microtrace HDI PCBs offer benefits such as increased circuit density, reduced size and weight of electronic devices, improved signal integrity, and enhanced reliability due to shorter signal paths and reduced electromagnetic interference (EMI).
What applications are suitable for Microtrace HDI PCBs?
Microtrace HDI PCBs are commonly used in smartphones, tablets, wearables, medical devices, automotive electronics, aerospace systems, and other applications where space constraints and high-performance requirements are critical.
What design considerations are important for Microtrace HDI PCBs?
Design considerations for Microtrace HDI PCBs include layer stackup, minimum feature size, aspect ratio of vias, routing optimization for signal integrity, thermal management, and adherence to design for manufacturability (DFM) principles.
What are the typical manufacturing processes for Microtrace HDI PCBs?
Manufacturing processes for Microtrace HDI PCBs include layer lamination, precision drilling of microvias, copper plating, circuit patterning via photolithography, surface finishing, solder mask application, silkscreen printing, testing, and final finishing.
What materials are used in Microtrace HDI PCBs?
Base materials for Microtrace HDI PCBs include FR-4, high-frequency laminates, low-Dk and low-Df materials, flex and rigid-flex substrates, and thermal substrates, depending on the specific requirements of the application.
How much do Microtrace HDI PCBs cost?
The cost of Microtrace HDI PCBs varies based on factors such as board size, complexity, layer count, material selection, feature density, surface finish, quantities, lead time, and additional services required.