Microtrace BGA Substrates Manufacturer
Microtrace BGA Substrates Manufacturer,Ultrathin LED PCBs are cutting-edge printed circuit boards designed specifically for LED lighting applications. Characterized by their incredibly slim profile and lightweight construction, these PCBs offer unparalleled flexibility and versatility in various lighting projects. With thicknesses ranging from mere fractions of a millimeter to a few millimeters, Ultrathin LED PCBs are ideal for applications where space is limited, such as slim-profile luminaires, edge-lit LED panels, and compact backlight modules for displays.
Constructed using high-quality materials like FR-4, polyimide, or metal core substrates, Ultrathin LED PCBs ensure excellent thermal management and electrical performance, ensuring optimal functionality and longevity of LED lighting systems. These PCBs can be fully customized to meet specific design requirements, allowing for flexibility in dimensions, shapes, layer configurations, and surface finishes. Whether in residential, commercial, or industrial settings, Ultrathin LED PCBs offer efficient, reliable, and aesthetically pleasing lighting solutions tailored to the needs of modern lighting applications.
What are Microtrace BGA substrates?
Microtrace BGA (Ball Grid Array) substrates are specialized components in the field of microelectronics, used as a platform on which semiconductor chips are mounted. They are part of the larger category of electronic packaging solutions known as BGA substrates. Here’s a detailed breakdown of what these are and how Microtrace BGA substrates fit into the picture:
- BGA Substrates: A Ball Grid Array substrate is a type of printed circuit board (PCB) used to mount devices such as microprocessors, ASICs (Application-Specific Integrated Circuits), and other semiconductor chips. Unlike older packaging styles like Dual Inline Package (DIP) or Pin Grid Array (PGA), BGA substrates use an array of solder balls as their connectors. These solder balls are arrayed across the bottom of the package in a grid pattern and provide both electrical connections and mechanical attachment to the PCB on which the BGA is mounted.
- Microtrace BGA Substrates: The term “Microtrace” in Microtrace BGA substrates refers to the extremely fine line widths and spacing on the substrate. This is essential in modern electronics where increasing functionality and decreasing size are critical. Microtrace technology allows for higher density of interconnections and smaller package sizes, enabling the integration of more features into smaller chips and devices. The trace lines on these substrates are often just a few micrometers wide.
- Applications and Importance: These substrates are crucial in high-performance computing, smartphones, tablets, and other digital devices where efficient use of space and enhanced electrical performance are required. They facilitate higher circuit densities and faster signal transmission speeds, contributing to the overall miniaturization and optimization of electronic devices.
- Manufacturing and Design: The design and manufacturing of Microtrace BGA substrates demand high precision and advanced technologies. This involves sophisticated photolithography, etching, and plating processes to create the fine trace lines that characterize these substrates. The quality of these substrates is critical because they need to ensure reliable electrical connections under thermal stress and other operating conditions.
In essence, Microtrace BGA substrates are at the forefront of enabling advanced microelectronics by providing the necessary infrastructure for mounting increasingly complex and smaller semiconductor chips. They are a key component in the continuous evolution towards smaller, faster, and more efficient electronic devices.
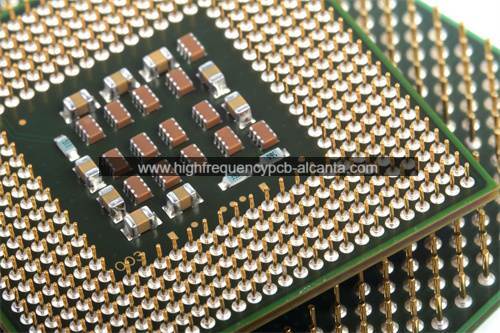
Microtrace BGA Substrates Manufacturer
What are the Microtrace BGA substrate Design Guidelines?
Design guidelines for Microtrace BGA substrates are crucial for ensuring the successful integration and operation of semiconductor chips on these specialized substrates. While specific guidelines may vary depending on the manufacturer and the intended application, here are some common design considerations:
- Trace Width and Spacing: Microtrace BGA substrates are characterized by extremely fine trace widths and spacings. Design guidelines typically specify the minimum allowable trace width and spacing to ensure reliable electrical connections and to prevent signal interference or crosstalk between traces. These dimensions are often measured in micrometers (μm) or mils.
- Minimum Annular Ring: The annular ring refers to the copper pad area surrounding the via hole. Design guidelines may specify a minimum annular ring size to ensure proper soldering and electrical connection between the via and the component lead or pad. This helps prevent solder joint failure or inadequate electrical contact.
- Via Placement and Size:Vias are conductive holes used to establish electrical connections between different layers of the substrate. Design guidelines may provide recommendations for via placement, spacing, and size to optimize signal integrity, minimize signal reflections, and ensure proper thermal management.
- Solder Mask Openings: Solder mask is a protective layer applied over the substrate to insulate copper traces and pads from environmental factors and solder bridging during assembly. Design guidelines may specify the size and clearance of solder mask openings around pads and vias to ensure proper solder deposition and avoid solder bridging or short circuits.
- Pad Size and Shape: Pads are the areas on the substrate where component leads or solder balls make contact for electrical connection. Design guidelines may recommend specific pad sizes and shapes to accommodate the dimensions of the component leads or solder balls, ensure adequate solder wetting, and minimize the risk of solder joint failure.
- Thermal Management: Microtrace BGA substrates often require efficient thermal management to dissipate heat generated by the mounted semiconductor chips. Design guidelines may include recommendations for thermal vias, thermal pads, or other features to enhance heat dissipation and prevent thermal issues such as overheating or solder joint fatigue.
- Signal Integrity Considerations: High-speed digital signals on Microtrace BGA substrates require careful consideration of signal integrity to minimize signal degradation and maintain reliable communication between components. Design guidelines may include recommendations for controlled impedance routing, signal layer stackup, and signal via placement to optimize signal integrity and minimize signal reflections.
- Assembly and Manufacturing Constraints: Design guidelines should also take into account assembly and manufacturing constraints, such as solder paste stencil design, pick-and-place accuracy, and assembly process compatibility. Design features that facilitate automated assembly and inspection can help streamline the manufacturing process and improve overall product quality.
These are just some of the key design guidelines for Microtrace BGA substrates. It’s essential for designers to work closely with substrate manufacturers and adhere to their specific guidelines and recommendations to ensure optimal performance and reliability of the final electronic product.
What is the Microtrace BGA substrate Fabrication Process?
The fabrication process for Microtrace BGA substrates involves several intricate steps to create the fine trace lines, vias, and other features characteristic of these specialized substrates. While specific processes may vary depending on factors such as substrate material, design requirements, and manufacturing capabilities, here is a general overview of the fabrication process:
- Substrate Material Selection: The fabrication process begins with the selection of suitable substrate materials. Common materials used for Microtrace BGA substrates include high-performance laminates such as FR-4, polyimide, or ceramic substrates. The choice of substrate material depends on factors such as thermal conductivity, electrical properties, and mechanical strength.
- Substrate Preparation:The selected substrate material undergoes preparation steps such as cleaning and surface treatment to ensure proper adhesion of subsequent layers and to remove any contaminants that could affect the fabrication process or final product quality.
- Layer Deposition: Depending on the design requirements, multiple layers of conductive and insulating materials may be deposited onto the substrate using techniques such as thin-film deposition, plating, or lamination. Conductive layers typically consist of copper or other metals, while insulating layers may be comprised of materials such as epoxy resin or polyimide.
- Photolithography: Photolithography is a key process used to define the intricate patterns of trace lines, pads, and vias on the substrate. It involves applying a photoresist material onto the substrate surface, exposing it to UV light through a photomask containing the desired pattern, and developing the photoresist to selectively remove areas not protected by the mask.
- Etching: After photolithography, the substrate undergoes etching to selectively remove the exposed areas of the conductive layer, leaving behind the desired trace patterns. Wet or dry etching techniques may be employed, depending on the substrate material and design requirements.
- Via Formation: Vias are conductive holes that establish electrical connections between different layers of the substrate. Vias are typically formed using drilling, laser ablation, or other specialized techniques, followed by plating to deposit a conductive material (e.g., copper) within the vias to facilitate electrical continuity.
- Surface Finish: Surface finish processes are applied to the substrate to improve solderability, corrosion resistance, and overall reliability of the final product. Common surface finishes for Microtrace BGA substrates include electroless nickel immersion gold (ENIG), immersion silver, or organic solderability preservatives (OSP).
- Solder Mask Application: Solder mask is applied over the substrate surface to insulate and protect the conductive traces and pads from environmental factors and solder bridging during assembly. Solder mask application involves coating the substrate with a liquid photoimageable solder mask material, exposing it to UV light through a solder mask stencil, and developing the solder mask to define the openings for soldering areas.
- Final Inspection and Testing: Once fabrication is complete, the Microtrace BGA substrates undergo thorough inspection and testing to ensure compliance with design specifications, dimensional accuracy, and electrical functionality. Quality control measures may include visual inspection, electrical testing, and dimensional measurements.
- Packaging and Shipping: The finished Microtrace BGA substrates are packaged according to industry standards to protect them during transit and storage. They are then shipped to semiconductor manufacturers or electronic assembly facilities for further integration into electronic devices.
Overall, the fabrication process for Microtrace BGA substrates requires a combination of precision manufacturing techniques, advanced materials, and rigorous quality control measures to achieve the fine features and high performance required for modern microelectronics applications. Collaboration between substrate manufacturers and design engineers is essential to ensure the successful fabrication of substrates that meet the specific requirements of each application.
How do you manufacture Microtrace BGA substrates?
Manufacturing Microtrace BGA (Ball Grid Array) substrates involves a series of specialized processes to create the fine trace lines, vias, and other features required for high-density interconnection and reliable performance in microelectronics applications. Here’s an overview of the manufacturing steps involved:
- Substrate Material Selection: The manufacturing process begins with selecting a suitable substrate material based on the specific requirements of the application. Common substrate materials include FR-4 (a type of fiberglass-reinforced epoxy laminate), polyimide, and ceramic. The choice of substrate material depends on factors such as thermal conductivity, electrical properties, and mechanical strength.
- Substrate Preparation: The selected substrate material undergoes preparation steps to ensure a clean and uniform surface for subsequent processing. This may involve cleaning the substrate surface to remove contaminants and applying surface treatments to enhance adhesion and promote uniform deposition of subsequent layers.
- Conductive Layer Deposition: Thin layers of conductive material, typically copper, are deposited onto the substrate surface using techniques such as physical vapor deposition (PVD), chemical vapor deposition (CVD), or electroplating. These conductive layers will form the trace lines, pads, and vias on the substrate.
- Lamination or Build-up: In some cases, multiple layers of conductive and insulating materials are built up to create complex multilayer structures. This may involve processes such as lamination, where alternating layers of conductive foil and insulating material are pressed together under heat and pressure to form a single integrated substrate.
- Photoimaging: Photoimaging techniques are used to define the intricate patterns of trace lines, pads, and vias on the substrate. This typically involves applying a layer of photoresist material onto the substrate surface, exposing it to ultraviolet (UV) light through a photomask containing the desired pattern, and then developing the photoresist to selectively remove areas not protected by the mask.
- Etching: The substrate undergoes etching to selectively remove the exposed areas of the conductive layer, leaving behind the desired trace patterns. Wet or dry etching techniques may be used, depending on the substrate material and design requirements.
- Via Formation: Vias are conductive holes that establish electrical connections between different layers of the substrate. Vias are typically formed using drilling, laser ablation, or other specialized techniques, followed by plating to deposit a conductive material (e.g., copper) within the vias to facilitate electrical continuity.
- Surface Finish: Surface finish processes are applied to the substrate to improve solderability, corrosion resistance, and overall reliability of the final product. Common surface finishes for Microtrace BGA substrates include electroless nickel immersion gold (ENIG), immersion silver, or organic solderability preservatives (OSP).
- Solder Mask Application:Solder mask is applied over the substrate surface to insulate and protect the conductive traces and pads from environmental factors and solder bridging during assembly. Solder mask application involves coating the substrate with a liquid photoimageable solder mask material, exposing it to UV light through a solder mask stencil, and then developing the solder mask to define the openings for soldering areas.
- Final Inspection and Testing: Once manufacturing is complete, the Microtrace BGA substrates undergo thorough inspection and testing to ensure compliance with design specifications, dimensional accuracy, and electrical functionality. Quality control measures may include visual inspection, electrical testing, and dimensional measurements.
- Packaging and Shipping: The finished Microtrace BGA substrates are packaged according to industry standards to protect them during transit and storage. They are then shipped to semiconductor manufacturers or electronic assembly facilities for further integration into electronic devices.
Overall, manufacturing Microtrace BGA substrates requires a combination of precision manufacturing techniques, advanced materials, and rigorous quality control measures to achieve the fine features and high performance required for modern microelectronics applications. Collaboration between substrate manufacturers and design engineers is essential to ensure the successful fabrication of substrates that meet the specific requirements of each application.
How much should Microtrace BGA substrates cost?
The cost of Microtrace BGA substrates can vary widely depending on several factors, including:
- Size and Complexity: Larger substrates with more intricate designs and higher layer counts will generally cost more to manufacture due to increased material and processing requirements.
- Materials: The choice of substrate material can significantly impact the cost. Advanced materials such as polyimide or ceramic tend to be more expensive than standard FR-4 laminates.
- Manufacturing Processes: The complexity of the manufacturing processes involved, such as fine line lithography, precise drilling, and advanced surface finishes, can influence the cost of production.
- Volume: Economies of scale come into play with larger production volumes. Higher volumes typically lead to lower per-unit costs due to efficiencies in material procurement, labor, and equipment utilization.
- Customization: Custom features or special requirements specified by the customer may incur additional costs for tooling, setup, or engineering design.
- Supplier and Location: The choice of substrate manufacturer and their geographical location can impact costs due to differences in labor rates, overhead expenses, and shipping fees.
Given these factors, it’s challenging to provide a specific cost without knowing the exact specifications and volume requirements of the Microtrace BGA substrates in question. Prices can range from a few dollars per unit for simple, standard-size substrates in high volumes to several hundred dollars or more for complex, custom-designed substrates with specialized materials and features.
Businesses interested in obtaining pricing for Microtrace BGA substrates should reach out to substrate manufacturers or suppliers directly, providing detailed specifications and volume projections to receive accurate cost estimates. Additionally, it’s essential to consider factors beyond just the initial substrate cost, such as overall project budget, quality, reliability, and long-term supplier relationships.
What is Microtrace BGA substrate base material?
The base material for Microtrace BGA substrates can vary depending on the specific requirements of the application and the manufacturing processes used by the substrate manufacturer. However, several common materials are frequently used as the substrate base for Microtrace BGA substrates:
- FR-4 (Flame Retardant-4): FR-4 is a widely used substrate material in the electronics industry due to its excellent electrical properties, mechanical strength, and cost-effectiveness. It is a type of fiberglass-reinforced epoxy laminate, providing good dimensional stability and resistance to heat and moisture.
- Polyimide: Polyimide substrates offer excellent thermal stability, flexibility, and chemical resistance, making them suitable for applications requiring high-temperature operation or harsh environmental conditions. Polyimide substrates are often used in flexible circuit applications.
- Ceramic: Ceramic substrates, such as alumina (Al2O3) or aluminum nitride (AlN), offer superior thermal conductivity and mechanical properties compared to organic substrates like FR-4 or polyimide. Ceramic substrates are well-suited for high-power applications and those requiring excellent thermal management.
- Rogers High Frequency Laminates: Rogers Corporation produces a range of high-frequency laminates specifically designed for RF (radio frequency) and microwave applications. These laminates offer low dielectric loss, consistent electrical performance over a wide frequency range, and excellent mechanical stability.
- Other Specialty Materials: In addition to the above, there are various specialty substrate materials available for specific applications, such as liquid crystal polymer (LCP) for high-frequency and high-speed applications, or metal core substrates for thermal management in LED and power electronics.
The choice of base material for Microtrace BGA substrates depends on factors such as electrical performance requirements, thermal management needs, mechanical constraints, and cost considerations. Design engineers and substrate manufacturers work together to select the most appropriate base material and optimize the substrate design to meet the specific requirements of each application.
Which company makes Microtrace BGA substrates?
Currently, there are many companies dedicated to manufacturing Microtrace BGA substrates, with some leading in this field. Manufacturers worldwide continuously enhance their technologies and production capabilities to meet the growing demands of the electronics market. Some of these companies include Rogers Corporation in the United States, Hitachi Chemical in Japan, and KB Semi Tech in South Korea. These companies possess advanced manufacturing equipment and technologies capable of producing high-quality, high-performance Microtrace BGA substrates to meet various application requirements.
At our company, we not only manufacture Microtrace BGA substrates but also provide Ultrathin LED PCBs. These printed circuit boards are specifically designed for LED lighting applications and feature the following characteristics:
- Ultra-thin Design: Ultrathin LED PCBs have an exceptionally thin thickness, meeting the strict space requirements of applications such as LED backlight modules and luminaires.
- Excellent Thermal Management: LED lighting products typically generate a significant amount of heat. Therefore, Ultrathin LED PCBs are designed with excellent thermal management structures to ensure effective heat dissipation from LED chips, prolonging their lifespan and enhancing performance stability.
- High Customization: Our company can customize Ultrathin LED PCBs according to specific customer requirements, including material selection, layer design, dimensions, shapes, and surface treatments, to meet the needs of different applications.
- Reliable Quality and Performance: We employ advanced manufacturing technologies and strict quality control processes to ensure that each Ultrathin LED PCB meets the expected standards of quality and performance for our customers.
Through our manufacturing capabilities, customers can obtain high-quality Microtrace BGA substrates and Ultrathin LED PCBs to meet their various needs in the electronics and lighting industries. We are committed to providing reliable solutions to our customers and working with them to drive the advancement of technology and innovation.
What are the 7 qualities of good customer service?
Good customer service is essential for building strong relationships with customers and fostering loyalty to a brand or company. Here are seven qualities that characterize good customer service:
- Responsiveness: Good customer service involves promptly addressing customer inquiries, concerns, and requests. Whether it’s answering phone calls, responding to emails, or assisting customers in person, being responsive demonstrates attentiveness to their needs and shows that their satisfaction is a priority.
- Empathy: Empathy involves understanding and acknowledging the emotions and perspectives of customers. Good customer service representatives empathize with customers’ frustrations, concerns, and challenges, and they respond with compassion and understanding. By demonstrating empathy, they build rapport and trust with customers.
- Clear Communication:Effective communication is essential in providing good customer service. Customer service representatives should communicate clearly and concisely, using language that is easy for customers to understand. They should also actively listen to customers, ensuring that they fully understand their needs and concerns before providing solutions or assistance.
- Knowledgeability: Good customer service requires a strong understanding of the products, services, and policies offered by the company. Customer service representatives should be knowledgeable about the company’s offerings and be able to provide accurate and helpful information to customers. This helps build credibility and instills confidence in customers.
- Professionalism:Professionalism involves maintaining a courteous and respectful demeanor when interacting with customers, even in challenging situations. Customer service representatives should remain calm, patient, and composed, regardless of the customer’s demeanor or the complexity of the issue. Professionalism builds trust and fosters positive relationships with customers.
- Problem-Solving Skills: Good customer service representatives possess strong problem-solving skills and the ability to resolve customer issues effectively and efficiently. They identify root causes of problems, propose viable solutions, and take proactive steps to address customers’ concerns. By effectively solving problems, they demonstrate competence and reliability to customers.
- Follow-Up and Follow-Through: Good customer service doesn’t end with the initial interaction. Customer service representatives should follow up with customers to ensure that their issues have been fully resolved and that they are satisfied with the outcome. Additionally, they should follow through on any promises or commitments made during the interaction, demonstrating reliability and accountability.
By embodying these qualities, businesses can deliver exceptional customer service experiences that not only meet but exceed customers’ expectations, leading to increased customer satisfaction, loyalty, and advocacy.
FAQs
What are BGA substrates?
BGA (Ball Grid Array) substrates are specialized printed circuit boards designed to provide the electrical and mechanical interconnection between integrated circuits (ICs) and the PCB. They feature a grid of solder balls on the underside of the substrate, which connects the ICs to the PCB.
What makes Microtrace BGA substrates unique?
Microtrace BGA substrates are known for their high-quality materials, advanced manufacturing processes, and precise engineering. They are designed to meet the demanding requirements of modern electronic devices, offering excellent electrical performance, thermal management, and reliability.
What applications are Microtrace BGA substrates used for?
Microtrace BGA substrates are commonly used in a wide range of electronic devices and applications, including smartphones, tablets, computers, automotive electronics, medical devices, aerospace systems, and more. They are particularly well-suited for applications requiring high-density packaging, fine-pitch interconnects, and high-speed data transmission.
What are the key features of Microtrace BGA substrates?
Microtrace BGA substrates feature several key attributes, including high-density interconnects, fine-pitch solder balls, excellent signal integrity, low electrical impedance, efficient thermal management, and compatibility with advanced packaging technologies such as flip-chip assembly and stacked die configurations.
Can Microtrace BGA substrates be customized?
Yes, Microtrace offers customization services to tailor BGA substrates to specific customer requirements. This includes customization of substrate materials, dimensions, layer stackup, ball pitch, ball composition, surface finishes, and other features to meet the unique needs of each application.
What quality standards do Microtrace BGA substrates adhere to?
Microtrace BGA substrates are manufactured according to stringent quality control processes and adhere to industry standards such as IPC (Association Connecting Electronics Industries) specifications, RoHS (Restriction of Hazardous Substances) compliance, and other relevant quality and environmental standards.
How can I request more information or place an order for Microtrace BGA substrates?
To request more information about Microtrace BGA substrates, including specifications, customization options, pricing, and ordering details, you can contact Microtrace directly through their website, customer service hotline, or authorized distributors.