Micro Via PCB Manufacturing
Micro Via PCB Manufacturing,Micro via PCB manufacturing, an essential innovation in modern electronics, revolutionize circuit board design by integrating miniature drilled holes known as micro vias. These tiny conduits enable intricate routing of signals between layers of the PCB, facilitating compact designs and enhanced functionality in electronic devices. Unlike traditional vias, micro vias boast significantly smaller diameters, often less than 150 micrometers, allowing for higher routing densities and finer pitch components. This advancement is particularly crucial in high-density interconnect (HDI) applications, such as smartphones, tablets, and wearable gadgets, where space optimization is paramount. Micro via PCBs offer superior signal integrity, improved thermal management, and increased reliability, meeting the demands of increasingly compact and powerful electronic devices. With their ability to accommodate complex circuitry in a minimal footprint, micro via PCBs continue to drive innovation across various industries, from consumer electronics to aerospace and telecommunications.
What is a Micro via PCB?
A micro via PCB (Printed Circuit Board) refers to a type of PCB that utilizes micro vias for routing signals between different layers of the circuit board. Micro vias are tiny holes drilled into the PCB substrate and then plated with conductive material to establish electrical connections between different layers.
Micro vias are typically much smaller in diameter compared to traditional vias, which allows for higher routing densities and more compact PCB designs. They are commonly used in high-density interconnect (HDI) PCBs, which are frequently found in modern electronics such as smartphones, tablets, and other portable devices where space is at a premium.
The use of micro vias enables manufacturers to create PCBs with multiple layers while maintaining a small form factor, which is essential for many modern electronic devices that require complex functionality in a compact size.
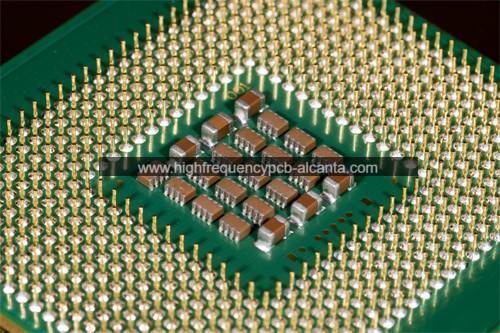
Micro Via PCB Manufacturing
What are the Micro via PCB Design Guidelines?
Micro via PCB design guidelines help ensure that the micro via technology is utilized effectively and reliably in printed circuit boards. Here are some common guidelines:
- Minimum Diameter and Aspect Ratio: Determine the minimum diameter and aspect ratio (hole diameter to board thickness ratio) for the micro vias based on the manufacturing capabilities of your PCB fabrication supplier. Generally, micro vias have diameters less than 150 micrometers.
- Layer Stacking: Plan the layer stacking carefully to optimize signal integrity, power distribution, and thermal management. Use micro vias to connect signal traces between different layers efficiently.
- Annular Ring and Pad Size: Maintain appropriate annular ring and pad sizes around the micro vias to ensure good reliability and manufacturability. The annular ring is the copper area around the hole. Ensure that it’s sufficient to provide a strong connection without causing electrical or mechanical issues.
- Clearance and Spacing: Define minimum clearance and spacing between micro vias, traces, and other elements on the PCB to prevent short circuits and ensure manufacturability.
- Routing Considerations: Route traces away from micro vias to minimize signal interference and impedance mismatch. Ensure that signal traces have proper impedance control.
- Via Filling and Planarization: Consider via filling and planarization techniques to improve the reliability and flatness of the PCB surface. Via filling with conductive or non-conductive materials can enhance the mechanical strength and thermal conductivity of micro vias.
- Manufacturability: Collaborate closely with your PCB manufacturer to ensure that your micro via design is manufacturable within their capabilities. Understand their processes and limitations.
- Testing and Inspection: Implement testing and inspection procedures to verify the integrity and reliability of micro vias during and after manufacturing. This may include electrical testing, microsection analysis, and reliability testing.
- Material Selection: Choose suitable PCB materials that are compatible with micro via fabrication processes and provide desired electrical and thermal properties.
- Documentation: Document the micro via design guidelines comprehensively in your PCB design documentation to ensure consistency and facilitate communication with stakeholders.
By adhering to these guidelines, you can optimize the performance, reliability, and manufacturability of micro via PCB designs.
What is the Micro via PCB Fabrication Process?
The micro via PCB fabrication process involves several steps to create printed circuit boards with micro vias. Below is an overview of the typical process:
- Design Preparation: The process begins with the preparation of the PCB design using specialized CAD software. Design considerations include layer stacking, via placement, trace routing, and other factors relevant to micro via technology.
- Substrate Preparation: A substrate material, typically a laminate composed of epoxy resin and glass fiber, is prepared for the PCB fabrication process. The substrate may also include copper foil laminated onto both sides.
- Drilling: Micro vias are drilled into the substrate using laser drilling or mechanical drilling techniques. Laser drilling is commonly used for micro vias due to its precision and ability to create small-diameter holes.
- Cleaning and Surface Preparation: After drilling, the PCB substrate undergoes cleaning and surface preparation processes to remove debris, residues, and contaminants from the drilling operation. This ensures proper adhesion of subsequent layers.
- Copper Plating: The drilled micro via holes are then plated with copper to establish electrical connections between different layers of the PCB. Copper plating is typically achieved through electroplating or electroless plating processes.
- Lamination: Multiple layers of substrate material, including copper foil if necessary, are laminated together to form the complete PCB stack-up. High-pressure and heat are applied during lamination to bond the layers together.
- Pattern Transfer: A photoresist layer is applied to the outer layers of the PCB stack-up. The desired circuit patterns are then transferred onto the photoresist using photolithography techniques, exposing the photoresist to UV light through a photomask.
- Etching: Exposed areas of the copper layers are etched away using chemical etchants, leaving behind the desired circuit traces and features. The photoresist is then stripped off, leaving clean copper traces on the PCB surface.
- Surface Finish: Surface finish processes such as hot air solder leveling (HASL), immersion gold (ENIG), or other plating methods are applied to protect exposed copper surfaces, enhance solderability, and improve overall reliability.
- Micro Via Filling and Planarization (if required): If micro vias need to be filled with conductive or non-conductive material, this step involves filling the vias and planarizing the surface to ensure a flat PCB profile.
- Final Inspection and Testing: The fabricated PCB undergoes thorough inspection and testing to verify dimensional accuracy, electrical continuity, and reliability. This may include visual inspection, electrical testing, microsection analysis, and other quality control measures.
- Assembly: Once the PCBs pass inspection, they are ready for component assembly, where electronic components are soldered onto the board to create the final electronic product.
By following these steps, manufacturers can produce high-quality PCBs with micro vias suitable for use in various electronic devices.
How do you manufacture a Micro via PCB?
Manufacturing a micro via PCB involves a series of intricate steps to create the necessary small-diameter holes for routing signals between different layers of the board. Below is a detailed outline of the manufacturing process:
- Design Preparation: Begin with the design of the PCB layout using computer-aided design (CAD) software. Ensure that the design includes the placement of micro vias, traces, and components according to the desired circuit functionality and spatial constraints.
- Substrate Selection: Choose a suitable substrate material for the PCB, typically a laminate composed of epoxy resin and glass fiber. The substrate should have properties suitable for micro via fabrication, such as good dimensional stability and thermal performance.
- Drilling: Drill micro vias into the substrate using specialized drilling equipment. Micro via drilling is typically performed using laser drilling machines capable of creating precise holes with diameters less than 150 micrometers. Laser drilling offers high accuracy and control over hole size and position.
- Cleaning and Surface Preparation: After drilling, the PCB substrate undergoes cleaning and surface preparation processes to remove any debris, residues, or contaminants generated during drilling. Proper surface preparation ensures good adhesion of subsequent layers and improves the reliability of the PCB.
- Copper Plating: Plate the drilled micro via holes with copper to establish electrical connections between different layers of the PCB. Copper plating is typically achieved through electroplating or electroless plating processes. The plated copper enhances conductivity and ensures reliable interconnects.
- Lamination: Stack multiple layers of substrate material together, including copper foil if required, and laminate them under heat and pressure. Lamination bonds the layers together to form a multilayer PCB structure.
- Pattern Transfer: Apply a photoresist layer to the outer layers of the PCB stack-up. Transfer the desired circuit patterns onto the photoresist using photolithography techniques. This involves exposing the photoresist to UV light through a photomask, which defines the circuit traces and features.
- Etching: Etch away the exposed areas of copper on the outer layers using chemical etchants. This process removes unwanted copper, leaving behind the desired circuit traces and features defined by the photolithography step. The photoresist is then stripped off, revealing clean copper traces on the PCB surface.
- Surface Finish: Apply a surface finish to protect exposed copper surfaces, enhance solderability, and improve overall reliability. Common surface finish options include hot air solder leveling (HASL), immersion gold (ENIG), or other plating methods.
- Micro Via Filling and Planarization (if required): Fill the micro vias with conductive or non-conductive material if necessary, and planarize the surface to achieve a flat PCB profile. This step enhances the mechanical strength and reliability of the micro vias.
- Final Inspection and Testing: Conduct thorough inspection and testing of the fabricated PCB to ensure dimensional accuracy, electrical continuity, and reliability. This may include visual inspection, electrical testing, microsection analysis, and other quality control measures.
- Component Assembly: Once the PCBs pass inspection, proceed with component assembly, where electronic components are soldered onto the board to create the final electronic product.
By following these steps, manufacturers can successfully fabricate micro via PCBs suitable for use in a wide range of electronic devices.
How much should a Micro via PCB cost?
The cost of manufacturing micro via PCBs can vary significantly depending on several factors, including the complexity of the design, the number of layers, the size of the board, the quantity ordered, and the specific fabrication processes required. Here are some factors that can influence the cost:
- Design Complexity: PCBs with complex designs, such as those requiring high-density interconnects (HDI) with numerous micro vias and fine-pitch components, tend to be more expensive to manufacture due to the increased precision and specialized equipment needed.
- Number of Layers: The number of layers in the PCB stack-up affects the cost, with higher layer counts generally resulting in higher manufacturing costs. Micro via technology is often used in multilayer PCBs to enable dense routing of signals between layers.
- Board Size: Larger PCBs require more materials and processing time, which can contribute to higher manufacturing costs. Conversely, smaller PCBs may have lower costs, but this can vary depending on the complexity of the design.
- Quantity Ordered: Economies of scale often apply in PCB manufacturing, meaning that larger order quantities typically result in lower per-unit costs. However, small prototype runs or low-volume production may incur higher costs per unit.
- Fabrication Processes: The specific fabrication processes required, such as laser drilling for micro vias, surface finish options, and additional treatments like via filling and planarization, can impact the overall cost of manufacturing.
- Material Selection: The choice of materials for the substrate, copper layers, and surface finishes can affect the cost. High-performance materials or specialty finishes may come at a premium compared to standard options.
- Supplier and Location: The pricing structures of PCB fabrication suppliers can vary based on factors like their overhead costs, labor rates, and geographic location. Offshore suppliers may offer lower costs compared to domestic ones, but shipping and lead times should also be considered.
Given these variables, it’s challenging to provide an exact cost without specific details about the PCB design and manufacturing requirements. For a more accurate estimate, it’s best to consult with PCB fabrication companies and provide them with detailed specifications of your project for a quotation.
What is Micro via PCB base material?
The choice of base material for micro via PCBs depends on various factors such as the desired electrical properties, thermal performance, mechanical strength, and cost considerations. Here are some common base materials used for micro via PCBs:
- FR-4: FR-4 (Flame Retardant 4) is the most widely used substrate material for PCBs due to its excellent balance of electrical properties, mechanical strength, and cost-effectiveness. It consists of woven fiberglass impregnated with an epoxy resin binder. FR-4 is suitable for many applications but may have limitations in high-frequency or high-temperature environments.
- High-Frequency Laminates: For applications requiring superior electrical performance at high frequencies, such as RF/microwave circuits, high-frequency laminates are preferred. These materials often utilize specialized substrates with low dielectric constant (Dk) and low loss tangent (Df), such as PTFE (Polytetrafluoroethylene) or hydrocarbon-based materials like Rogers Corporation’s RO4000 series.
- Flexible Materials: Flexible PCBs (Flex PCBs) use flexible substrates such as polyimide (PI) or polyester (PET) instead of rigid FR-4. These materials allow the PCB to bend or flex, making them suitable for applications with space constraints or those requiring dynamic movement.
- Metal Core Materials: Metal core PCBs (MCPCBs) utilize a metal core, typically aluminum or copper, as the substrate instead of fiberglass. MCPCBs offer excellent thermal conductivity, making them ideal for applications requiring efficient heat dissipation, such as LED lighting and power electronics.
- Ceramic Substrates: Ceramic materials like alumina (Al2O3) or aluminum nitride (AlN) are used in specialized applications where high thermal conductivity, excellent mechanical properties, and compatibility with high-temperature environments are required. Ceramic substrates are commonly used in power electronics and high-power RF applications.
- Composite Materials: Some advanced composite materials combine features of traditional substrates with unique properties. For example, composite substrates may incorporate ceramic fillers in an epoxy resin matrix to enhance thermal performance while maintaining manufacturability.
The choice of base material depends on the specific requirements of the PCB design and the intended application. Designers should consider factors such as electrical performance, thermal management, mechanical durability, and cost-effectiveness when selecting the appropriate substrate material for micro via PCBs.
Which company makes Micro via PCB?
Currently, there are many companies specialized in the manufacturing of micro via PCBs, some of which include Foxconn, JLCPCB, Jiangsu Happy Lotto Technology Group, Hitachi Chemical, and Unimicron Technology Corp. These companies possess advanced production equipment, rich experience, and professional technical teams to meet the demands of various industries and applications for micro via PCBs.
As for our company, we have advanced PCB manufacturing equipment and technology, capable of producing micro via PCBs. Our manufacturing processes include high-precision laser drilling technology, enabling precise positioning and drilling of small-diameter micro vias. We also have advanced surface treatment equipment for copper plating, surface finishing, as well as necessary filling and planarization processes.
Additionally, our company has an experienced engineering team and quality control team, capable of providing professional technical support and quality assurance to customers. We are committed to providing customers with high-quality and highly reliable micro via PCB products to meet the demands of high-performance electronic products.
Through the micro via PCBs produced by our company, customers can obtain premium products with excellent electrical performance, thermal management capabilities, and mechanical strength, suitable for various application scenarios. We will continuously optimize our production processes, improve product quality, and enhance production efficiency to provide better service and support to our customers.
FAQs (Frequently Asked Questions)
What are the benefits of using Micro via PCBs?
Micro via PCBs offer advantages such as improved signal integrity, miniaturization of electronic devices, enhanced reliability, and increased design flexibility.
Can Micro via PCBs be used in high-frequency applications?
Yes, Micro via PCBs are suitable for high-frequency applications due to their precise signal transmission properties and impedance control.
What are the limitations of Micro via PCB technology?
Some limitations of Micro via PCBs include increased manufacturing complexity, higher production costs, and potential reliability concerns associated with micro via failure.
How do I choose the right Micro via PCB manufacturer?
When selecting a Micro via PCB manufacturer, consider factors such as their experience, technological capabilities, quality assurance processes, and ability to meet your specific requirements.
What is the typical lead time for manufacturing Micro via PCBs?
Lead times for Micro via PCB manufacturing can vary depending on factors such as order volume, complexity, and supplier availability. It’s advisable to consult with the manufacturer for accurate timelines.
Are there any design considerations unique to Micro via PCBs?
Yes, designing Micro via PCBs requires attention to factors such as via size, aspect ratio, pad size, and routing density to ensure manufacturability and signal integrity.
Can Micro via PCBs be used in consumer electronics?
Yes, Micro via PCBs find applications in various consumer electronics devices, including smartphones, tablets, wearables, and IoT devices, where space-saving and high-performance requirements are critical.