Micro LED Substrate Manufacturer
Micro LED Substrate Manufacturer,Micro LED substrates serve as the fundamental building blocks for Micro LED displays, representing a crucial stage in the intricate process of display manufacturing. These substrates, typically crafted from materials like silicon or glass, provide the stable foundation upon which individual Micro LED chips are meticulously placed and interconnected. With precision engineering, Micro LED substrates facilitate the seamless integration of countless tiny LEDs, each emitting its own light, resulting in vibrant and high-resolution displays.
Beyond mere support, Micro LED substrates play a pivotal role in managing heat dissipation, ensuring optimal performance, and longevity of the display. Their advanced design caters to the demands of modern display technology, accommodating the complexities of high-resolution visuals, energy efficiency, and innovative form factors like flexible or transparent displays. From smartphones to large-scale digital signage, Micro LED substrates pave the way for next-generation display solutions, promising unparalleled brightness, contrast, and visual fidelity in various applications.
What is a Micro LED Substrate?
A Micro LED substrate is a crucial component in Micro LED display technology, which is known for its potential to offer superior brightness, contrast, and energy efficiency compared to traditional LED displays. The substrate serves as the foundation upon which individual Micro LED chips are mounted.
This substrate is typically made from materials such as silicon or glass, providing a stable platform for precise placement of Micro LEDs, which are miniature light-emitting diodes. These LEDs are usually smaller than 100 micrometers in size, allowing for extremely high pixel densities and thus enabling the creation of high-resolution displays.
The substrate not only supports the Micro LEDs but also facilitates electrical connections and heat dissipation, ensuring optimal performance and longevity of the display. Moreover, advancements in substrate technology, such as the development of flexible and transparent substrates, have expanded the potential applications of Micro LED displays, including curved screens, wearable devices, and augmented reality systems.
In summary, a Micro LED substrate is a foundational component in Micro LED display technology, providing the structure and support necessary for the creation of high-resolution, energy-efficient displays with superior visual performance.
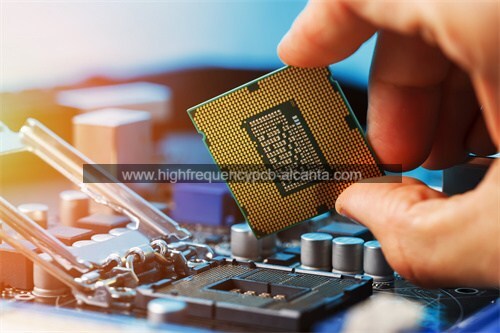
Micro LED Substrate Manufacturer
What are the Micro LED Substrate Design Guidelines?
Micro LED substrate design guidelines encompass a range of considerations to ensure optimal performance and reliability of Micro LED displays. Here are some key aspects typically addressed in these guidelines:
- Pixel Pitch and Resolution: Determine the desired pixel pitch (distance between the centers of adjacent pixels) and overall display resolution to meet the application requirements.
- Substrate Material Selection: Choose appropriate substrate materials such as silicon or glass based on factors like thermal conductivity, mechanical strength, and compatibility with manufacturing processes.
- LED Placement and Size: Define the layout and size of individual Micro LEDs on the substrate, considering factors such as uniformity, brightness, and power efficiency.
- Electrical Connectivity: Design the substrate to facilitate electrical connections between Micro LEDs and the driving circuitry, ensuring efficient power distribution and signal transmission.
- Heat Dissipation: Incorporate heat dissipation mechanisms such as thermal vias, metal layers, or integrated heat sinks to prevent overheating and maintain LED performance.
- Alignment and Accuracy: Implement precise alignment techniques during Micro LED placement to achieve uniformity and consistency across the display, minimizing variations in brightness and color.
- Manufacturability: Optimize substrate design for scalability and cost-effectiveness in manufacturing processes such as pick-and-place, bonding, and encapsulation.
- Durability and Reliability: Enhance substrate robustness to withstand environmental factors, mechanical stress, and thermal cycling, ensuring long-term reliability and operational stability.
- Flexibility and Transparency(optional): If applicable, incorporate features for flexible or transparent substrates to enable novel display form factors and applications.
- Testing and Quality Assurance: Establish testing protocols to evaluate substrate performance and adherence to design specifications, ensuring consistent quality control throughout the manufacturing process.
By adhering to these guidelines, manufacturers can develop Micro LED substrates that meet the demanding requirements of high-performance displays, enabling the realization of next-generation visual technologies.
What is the Micro LED Substrate Fabrication Process?
The fabrication process of Micro LED substrates involves several key steps to create the foundation for mounting and connecting individual Micro LEDs. Here’s a general overview of the process:
- Substrate Preparation: The process typically begins with the preparation of a base substrate, which is often made of materials like silicon or glass. The substrate is cleaned and prepared to ensure a smooth and contamination-free surface.
- Thin Film Deposition: Thin film deposition techniques such as chemical vapor deposition (CVD) or physical vapor deposition (PVD) are used to create layers on the substrate. These layers may include conducting, insulating, or semiconducting materials required for the functioning of Micro LEDs and electrical connections.
- Photolithography: Photolithography is employed to define patterns on the substrate surface. A photoresist material is applied to the substrate, exposed to light through a photomask, and then developed to transfer the pattern onto the substrate. This step defines the locations for Micro LED placement and electrical connections.
- Etching: Etching processes such as dry or wet etching are used to remove material from specific areas of the substrate according to the patterns defined in the previous step. This creates features such as recesses or trenches for Micro LED placement and electrical interconnections.
- Micro LED Placement: Individual Micro LEDs are picked and placed onto the substrate using automated pick-and-place equipment. Precise alignment is crucial to ensure uniformity and consistency across the display.
- Bonding: After placement, the Micro LEDs are bonded to the substrate using techniques such as adhesive bonding or soldering. This step provides mechanical stability and facilitates electrical connections between the LEDs and the substrate.
- Encapsulation: The Micro LEDs and interconnections are encapsulated with a protective layer to shield them from environmental factors such as moisture, dust, and mechanical stress. Encapsulation materials may include epoxy resins, polymers, or glass.
- Testing and Inspection: The fabricated substrates undergo rigorous testing and inspection to assess the performance, functionality, and quality of the Micro LED array. This may include electrical testing, visual inspection, and characterization of optical properties.
- Packaging: Finally, the fabricated Micro LED substrates may be packaged into modules or integrated into larger display assemblies, depending on the specific application requirements.
Throughout the fabrication process, strict quality control measures are implemented to ensure the reliability, consistency, and performance of the Micro LED substrates, ultimately contributing to the production of high-quality Micro LED displays.
How do you manufacture a Micro LED Substrate?
Manufacturing a Micro LED substrate involves a series of intricate processes aimed at creating a stable foundation for mounting and connecting individual Micro LEDs. Here’s a detailed overview of the manufacturing steps:
- Substrate Selection: Choose a suitable substrate material based on factors like thermal conductivity, mechanical strength, and compatibility with manufacturing processes. Common substrate materials include silicon or glass.
- Cleaning and Preparation: Clean the substrate surface thoroughly to remove any contaminants or residues that could affect subsequent processing steps. Surface preparation may involve techniques such as chemical cleaning and plasma treatment.
- Thin Film Deposition: Use techniques like chemical vapor deposition (CVD) or physical vapor deposition (PVD) to deposit thin films of conducting, insulating, or semiconducting materials onto the substrate. These films may serve as electrodes, passivation layers, or semiconductor layers required for Micro LED functionality.
- Photolithography: Apply a photoresist material onto the substrate and expose it to UV light through a photomask to define patterns corresponding to the desired Micro LED layout and electrical connections. After exposure, the photoresist is developed to remove the unexposed areas, leaving behind the patterned photoresist mask.
- Etching: Use etching processes such as dry etching or wet etching to selectively remove material from the substrate according to the pattern defined by the photoresist mask. This creates features such as recesses or trenches for Micro LED placement and electrical interconnections.
- Micro LED Placement: Employ automated pick-and-place equipment to precisely position individual Micro LED chips onto the substrate. Proper alignment is critical to ensure uniformity and consistency across the display.
- Bonding: Bond the Micro LED chips to the substrate using techniques such as adhesive bonding or soldering. This step provides mechanical stability and facilitates electrical connections between the LEDs and the substrate.
- Encapsulation: Encapsulate the Micro LEDs and interconnections with a protective layer to shield them from environmental factors such as moisture, dust, and mechanical stress. Common encapsulation materials include epoxy resins, polymers, or glass.
- Testing and Quality Control: Conduct rigorous testing and inspection of the fabricated substrates to assess performance, functionality, and quality. This may include electrical testing, visual inspection, and characterization of optical properties.
- Packaging: Package the fabricated Micro LED substrates into modules or integrate them into larger display assemblies, depending on the specific application requirements.
Throughout the manufacturing process, stringent quality control measures are implemented to ensure the reliability, consistency, and performance of the Micro LED substrates, ultimately contributing to the production of high-quality Micro LED displays.
How much should a Micro LED Substrate cost?
The cost of a Micro LED substrate can vary significantly depending on several factors, including the substrate material, size, complexity, manufacturing processes, and desired performance characteristics. Generally, Micro LED substrates are considered a critical component in Micro LED display technology, and their cost can contribute significantly to the overall cost of manufacturing Micro LED displays. Here are some factors that influence the cost of Micro LED substrates:
- Substrate Material: The choice of substrate material, such as silicon or glass, can impact the cost. Silicon substrates are typically more expensive than glass substrates due to their higher manufacturing costs and material expenses.
- Size and Dimensions: Larger substrates require more material and may involve additional processing steps, leading to higher costs compared to smaller substrates. Additionally, substrates with non-standard dimensions or custom shapes may incur additional manufacturing costs.
- Manufacturing Processes: The complexity of the manufacturing processes involved in fabricating Micro LED substrates can influence the cost. Processes such as thin film deposition, photolithography, etching, and bonding require specialized equipment, materials, and skilled labor, all of which contribute to the overall manufacturing cost.
- Quality and Performance: Substrates designed to meet higher performance standards, such as those with finer pixel pitches, enhanced electrical connectivity, or improved thermal management, may command higher prices due to the additional materials and manufacturing precision required to achieve these specifications.
- Volume and Economy of Scale: Economies of scale play a significant role in determining the cost of Micro LED substrates. Larger production volumes generally result in lower per-unit costs due to efficiencies in manufacturing, material procurement, and equipment utilization.
- Technology Advancements: Ongoing advancements in Micro LED substrate manufacturing technology can lead to cost reductions over time as processes become more efficient and materials become more readily available. However, early adoption of new technologies may incur higher initial costs.
- Market Dynamics: Market demand and competition among Micro LED substrate manufacturers can influence pricing. Additionally, factors such as supply chain disruptions, raw material costs, and geopolitical factors can impact substrate pricing.
Overall, the cost of a Micro LED substrate can range from a few dollars to several hundred dollars per square inch, depending on the aforementioned factors. As Micro LED technology continues to evolve and mature, it is expected that the cost of substrates will decrease gradually, making Micro LED displays more accessible to a wider range of applications and consumers.
What is Micro LED Substrate base material?
The base material for Micro LED substrates can vary depending on the specific requirements of the application and the manufacturing processes involved. However, two common types of materials used for Micro LED substrates are silicon and glass.
- Silicon Substrates: Silicon substrates are widely used in Micro LED manufacturing due to their excellent thermal conductivity, mechanical stability, and compatibility with semiconductor processing techniques. Silicon substrates can be fabricated with high precision and can accommodate the intricate patterns and structures required for Micro LED placement and interconnections. Additionally, silicon substrates are available in various forms, including single-crystal silicon wafers and silicon-on-insulator (SOI) substrates, offering flexibility to suit different manufacturing needs.
- Glass Substrates: Glass substrates are also commonly used in Micro LED fabrication, particularly for applications requiring flexibility, transparency, or larger display sizes. Glass substrates offer advantages such as excellent optical clarity, smooth surface finish, and compatibility with high-resolution patterning techniques. Moreover, glass substrates can be engineered to be flexible or even bendable, enabling the development of innovative display form factors such as curved or foldable displays. Various types of glass, including soda-lime glass, borosilicate glass, and quartz glass, can be used depending on the specific requirements of the application.
In addition to silicon and glass, other materials such as sapphire, polymer films, and metal foils have also been explored as potential substrates for Micro LED manufacturing, each offering unique properties and advantages. The choice of substrate material depends on factors such as thermal management requirements, mechanical flexibility, cost considerations, and compatibility with downstream processing steps. Ultimately, the selection of the base material for Micro LED substrates is a critical decision that influences the performance, reliability, and manufacturability of Micro LED displays.
Which company makes Micro LED Substrates?
Currently, there are several companies globally dedicated to producing Micro LED substrates. Some of the major manufacturers include Samsung, LG, Sony, Intel, as well as Taiwan’s PlayNitride and AU Optronics. These companies have invested significant research and development resources in the Micro LED technology field and have achieved certain accomplishments.
Regarding our company, we are also one of the leading manufacturers in the Micro LED substrate domain. Equipped with advanced production equipment and technology, we can provide high-quality, high-performance Micro LED substrates to meet various customer needs. Our manufacturing process is meticulously designed and optimized to ensure the production of substrates that meet strict standards, with stable performance and reliable quality.
Here are the characteristics and advantages of our Micro LED substrates:
- High Precision Manufacturing: We employ advanced processes and equipment to achieve high-precision machining and production of substrates, ensuring precise arrangement and connection of Micro LEDs.
- Excellent Thermal Management: We optimize the thermal management design of substrates according to the characteristics of Micro LED technology, effectively dissipating heat to ensure the stability of LEDs’ performance.
- Diverse Material Selection:We can provide substrates made of various materials, including silicon, glass, etc., according to customer requirements, to meet the needs of different application scenarios.
- Strict Quality Control: We have established a comprehensive quality management system to strictly control every aspect of the production process, ensuring the stable and reliable quality and performance of each substrate.
- Customized Services: We offer customized substrate solutions tailored to customer needs, including customization of dimensions, shapes, materials, etc., to meet their individual requirements.
Through the Micro LED substrates produced by our company, customers can obtain high-quality products, providing a stable foundation for their Micro LED display projects. We are committed to continuously improving our technological capabilities and production capacity, working together with customers to promote the development and application of Micro LED technology.
What are the 7 qualities of good customer service?
Good customer service is characterized by several key qualities that contribute to a positive customer experience and foster customer satisfaction and loyalty. Here are seven essential qualities:
- Responsiveness: Good customer service entails promptly addressing customer inquiries, concerns, and requests. Whether it’s answering phone calls, responding to emails, or engaging with customers on social media, being responsive demonstrates attentiveness to customer needs and a commitment to providing timely assistance.
- Empathy: Empathy involves understanding and acknowledging the customer’s perspective, emotions, and concerns. Good customer service representatives demonstrate empathy by actively listening to customers, showing genuine concern for their issues, and expressing empathy in their interactions. This helps build rapport and trust with customers.
- Clear Communication: Effective communication is crucial in delivering good customer service. Clear and concise communication helps ensure that customers understand the information provided, such as product features, policies, or troubleshooting steps. Customer service representatives should communicate in a friendly and professional manner, avoiding jargon or technical language that may confuse customers.
- Problem-solving Skills: Good customer service involves effectively resolving customer issues and complaints. Customer service representatives should possess strong problem-solving skills to identify root causes of problems, offer appropriate solutions or alternatives, and follow up to ensure customer satisfaction. Proactive problem-solving helps turn negative experiences into positive ones and strengthens customer relationships.
- Product Knowledge:Customer service representatives should have a deep understanding of the products or services they support. This includes knowledge of product features, specifications, usage instructions, and troubleshooting techniques. Being knowledgeable allows representatives to provide accurate information, offer helpful advice, and assist customers effectively.
- Professionalism: Professionalism encompasses aspects such as courtesy, respect, integrity, and reliability. Good customer service representatives conduct themselves in a professional manner at all times, treating customers with courtesy and respect, maintaining confidentiality, and adhering to company policies and ethical standards. Professionalism helps instill confidence in customers and enhances the credibility of the business.
- Follow-up and Feedback: Following up with customers after interactions and seeking feedback are important aspects of good customer service. Following up ensures that customer issues are fully resolved and provides an opportunity to address any remaining concerns. Additionally, soliciting feedback allows businesses to gather insights into customer satisfaction levels, identify areas for improvement, and continuously enhance their customer service practices.
FAQs
What are the key features of a Micro LED substrate?
Important features of Micro LED substrates include precise patterning for Micro LED placement, efficient heat dissipation to maintain LED performance, electrical connectivity for driving the LEDs, and compatibility with high-resolution display requirements.
How are Micro LED substrates manufactured?
The manufacturing process of Micro LED substrates involves steps such as substrate preparation, thin film deposition, photolithography, etching, Micro LED placement, bonding, encapsulation, testing, and packaging. Each step is crucial in creating substrates with high quality and performance.
What are the advantages of Micro LED substrates?
Micro LED substrates offer advantages such as high brightness, energy efficiency, wide color gamut, fast response time, and potential for high resolution and pixel density. They also enable the development of innovative display form factors such as flexible and transparent displays.
What applications are Micro LED substrates used for?
Micro LED substrates find applications in various industries, including consumer electronics (smartphones, TVs, wearables), automotive displays, augmented reality (AR) and virtual reality (VR) devices, digital signage, and medical displays, among others.
What factors should be considered when choosing Micro LED substrates?
Factors to consider when selecting Micro LED substrates include substrate material, size, thermal management capabilities, electrical connectivity, manufacturing process compatibility, and cost-effectiveness.
How can I ensure the quality of Micro LED substrates?
Ensuring the quality of Micro LED substrates involves working with reputable manufacturers, conducting thorough testing and inspection procedures, and evaluating factors such as substrate uniformity, electrical performance, and reliability.