Micro LED PCB Manufacturing
Micro LED PCB Manufacturing,Micro LED PCBs are specialized circuit boards designed to accommodate Micro LED technology, which utilizes miniature light-emitting diodes (LEDs) for high-resolution displays. These PCBs are engineered to provide precise electrical connections to each individual Micro LED within the display matrix, enabling accurate control over brightness and color. The fabrication process involves advanced manufacturing techniques to achieve the required precision and density, including microfabrication and fine-pitch surface mount assembly. Key features of Micro LED PCBs include their ability to support high-density arrangements of Micro LEDs, efficient power distribution, and effective thermal management to prevent overheating. These PCBs play a crucial role in enabling the development of high-resolution displays with vibrant colors, superior image quality, and energy efficiency. With their compact size and advanced technology, Micro LED PCBs are revolutionizing the display industry, powering applications in TVs, monitors, smartphones, and other electronic devices.
What is a Micro LED PCB?
A Micro LED PCB (Printed Circuit Board) refers to a specialized type of circuit board designed to accommodate Micro LED technology. Micro LEDs are miniature light-emitting diodes that are significantly smaller than traditional LEDs, often with sizes ranging from tens to hundreds of micrometers. They are commonly used in high-resolution displays, such as those found in TVs, monitors, smartphones, and other electronic devices.
The PCB for Micro LEDs is engineered to provide electrical connections to each individual Micro LED within the display matrix. These connections enable precise control over each LED’s brightness and color, allowing for the creation of vibrant and detailed images. Additionally, the PCB must be designed to handle the high-density arrangement of Micro LEDs while ensuring efficient power distribution and thermal management to prevent overheating.
Micro LED PCBs typically involve advanced manufacturing techniques to achieve the required precision and density. This may include technologies such as microfabrication, fine-pitch surface mount assembly, and specialized material deposition processes. Overall, Micro LED PCBs play a crucial role in enabling the development of high-resolution displays with superior image quality and energy efficiency.
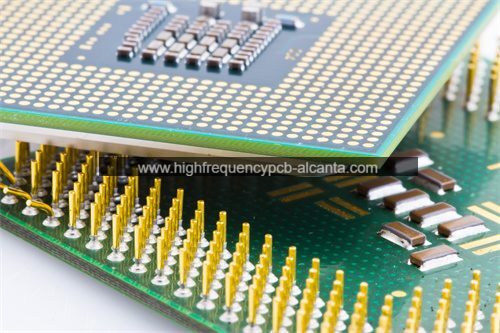
Micro LED PCB manufacturing
What is the Micro LED PCB Fabrication Process?
The fabrication process of Micro LED PCBs involves several steps, each crucial for ensuring the quality and performance of the final product. Below is an overview of the typical Micro LED PCB fabrication process:
- Design:The process starts with the design of the PCB layout, taking into account the specific requirements of the Micro LED display, such as resolution, size, and power distribution. Design software is used to create the circuit layout and define the placement of Micro LEDs and other components.
- Substrate Preparation:The chosen substrate material, often a specialized type of high-temperature resistant material like ceramic or glass, is prepared. This includes cleaning and surface treatment to ensure proper adhesion of the conductive layers.
- Deposition of Conductive Layers:Thin layers of conductive materials, such as copper, are deposited onto the substrate through techniques like sputtering or electroplating. These layers form the circuit traces and pads that will provide electrical connections to the Micro LEDs.
- Photoresist Application:A layer of photoresist is applied onto the conductive layers. Photoresist is a light-sensitive material used to create patterns on the PCB. It is exposed to UV light through a photomask, which defines the circuit pattern.
- Etching:The exposed areas of the photoresist are chemically removed, leaving behind the desired circuit pattern on the conductive layers. Subsequently, the exposed areas of the conductive layers are etched away, leaving the circuit traces and pads.
- Micro LED Placement:Micro LEDs are then precisely placed onto the PCB using pick-and-place machines. This step requires high precision to ensure accurate positioning of each LED according to the design layout.
- Attachment and Connection:The Micro LEDs are attached to the PCB using conductive adhesives or soldering techniques. Fine-pitch bonding is often employed to establish electrical connections between the LED anodes and cathodes and the corresponding pads on the PCB.
- Encapsulation:To protect the Micro LEDs and the circuitry from environmental factors such as moisture and mechanical stress, the entire PCB assembly may be encapsulated with a transparent protective material, such as epoxy resin.
- Testing and Quality Control:The fabricated Micro LED PCBs undergo rigorous testing to ensure functionality and reliability. This may include electrical testing, visual inspection, and performance testing of the display functionality.
- Packaging:Once the Micro LED PCBs pass quality control, they are packaged and prepared for integration into the final product, such as display panels for TVs, monitors, or other electronic devices.
Overall, the fabrication process of Micro LED PCBs requires advanced manufacturing techniques and precise control to achieve the desired performance and reliability for high-resolution displays.
How do you manufacture a Micro LED PCB?
Manufacturing a Micro LED PCB involves several intricate steps to ensure precision, reliability, and functionality. Here’s a detailed overview of the manufacturing process:
- Design:The process starts with the design of the Micro LED PCB layout using specialized design software. Engineers determine the placement of Micro LEDs, circuit traces, and other components based on the display’s specifications and requirements.
- Substrate Preparation:The chosen substrate material, often a high-temperature resistant material like ceramic or glass, undergoes preparation. This includes cleaning and surface treatment to enhance adhesion and ensure the substrate’s compatibility with subsequent manufacturing steps.
- Deposition of Conductive Layers:Thin layers of conductive materials, typically copper, are deposited onto the substrate. This is achieved through techniques such as sputtering or electroplating. These conductive layers form the circuit traces and pads necessary for electrical connections.
- Photoresist Application:A layer of photoresist is applied onto the conductive layers. Photoresist is a light-sensitive material used to create patterns on the PCB. The desired circuit pattern is transferred onto the photoresist through exposure to UV light using a photomask.
- Etching:The exposed areas of the photoresist are chemically removed, leaving behind the desired circuit pattern on the conductive layers. Subsequently, the exposed areas of the conductive layers are etched away, leaving the circuit traces and pads according to the design.
- Micro LED Placement:Micro LEDs are precisely placed onto the PCB using automated pick-and-place machines. This step requires high precision to ensure accurate positioning of each LED according to the design layout.
- Attachment and Connection:The Micro LEDs are attached to the PCB using conductive adhesives or soldering techniques. Fine-pitch bonding is often employed to establish electrical connections between the LED anodes and cathodes and the corresponding pads on the PCB.
- Encapsulation:To protect the Micro LEDs and the circuitry from environmental factors such as moisture and mechanical stress, the entire PCB assembly may be encapsulated with a transparent protective material, such as epoxy resin.
- Testing and Quality Control:The fabricated Micro LED PCBs undergo rigorous testing to ensure functionality and reliability. This may include electrical testing, visual inspection, and performance testing of the display functionality.
- Packaging:Once the Micro LED PCBs pass quality control, they are packaged and prepared for integration into the final product, such as display panels for TVs, monitors, or other electronic devices.
Throughout the manufacturing process, strict quality control measures are implemented to ensure that the Micro LED PCBs meet the required standards for performance, reliability, and durability.
How much should a Micro LED PCB cost?
The cost of a Micro LED PCB can vary widely depending on various factors such as the size, complexity, quality, and quantity of the PCBs required. Additionally, factors such as the choice of substrate material, fabrication techniques, and the presence of specialized features can also influence the cost. Here are some key factors that contribute to the cost of a Micro LED PCB:
- Design Complexity:PCBs with intricate designs, dense circuitry, and fine-pitch components (such as Micro LEDs) may require more advanced manufacturing processes, which can increase production costs.
- Substrate Material:The choice of substrate material can significantly impact the cost. High-quality materials like ceramic or glass are more expensive than standard FR-4 fiberglass substrates but offer better thermal performance and reliability.
- Manufacturing Techniques:Advanced manufacturing techniques such as laser drilling, sequential build-up (SBU), and fine-pitch surface mount assembly can increase production costs but may be necessary for high-performance Micro LED PCBs.
- Component Integration:The cost of Micro LEDs themselves can be significant, especially for high-resolution displays requiring a large number of LEDs. Additionally, integrating other components such as driver ICs, connectors, and encapsulation materials can add to the overall cost.
- Quantity:Economies of scale typically apply in PCB manufacturing, meaning that larger production volumes can result in lower per-unit costs. However, prototyping or low-volume production runs may incur higher costs per unit.
- Quality Assurance and Testing:Ensuring the quality and reliability of Micro LED PCBs often involves rigorous testing and quality assurance measures, which can increase manufacturing costs.
- Customization and Special Requirements:Customization, specialized features, and additional requirements such as specific certifications or environmental protection may also contribute to higher costs.
Due to the diverse range of factors influencing the cost, it’s challenging to provide a precise figure without specific details about the PCB’s requirements. However, Micro LED PCBs can range from a few dollars for simple prototypes to hundreds or even thousands of dollars for high-performance, high-resolution displays used in commercial products.
What is Micro LED PCB base material?
The choice of base material for Micro LED PCBs depends on various factors such as thermal performance, electrical properties, cost, and application requirements. Here are some common base materials used in Micro LED PCB manufacturing:
- Ceramic Substrates:Ceramic substrates, such as aluminum nitride (AlN) and aluminum oxide (Al2O3), are popular choices for Micro LED PCBs due to their excellent thermal conductivity. They efficiently dissipate heat generated by Micro LEDs, helping to maintain optimal operating temperatures and improve overall reliability.
- Glass Substrates:Glass substrates offer similar advantages to ceramics in terms of thermal performance. They also provide excellent dimensional stability and reliability, making them suitable for high-precision applications. Borosilicate glass is commonly used for Micro LED PCBs due to its thermal properties and compatibility with fabrication processes.
- Flexible Substrates:Flexible substrates, such as polyimide (PI) or polyester (PET), are used in applications where flexibility or bendability is required. Flexible Micro LED PCBs can conform to curved surfaces, making them suitable for wearable devices, curved displays, and other innovative applications.
- FR-4 Fiberglass:FR-4 fiberglass is a common substrate material used in conventional PCB manufacturing. While it has lower thermal conductivity compared to ceramics and glass, it offers good electrical insulation properties and is cost-effective. FR-4 PCBs are suitable for less demanding applications or prototypes where thermal performance is not a critical factor.
- Metal Core Substrates (MCPCB):Metal core substrates, typically aluminum or copper, are used when enhanced thermal management is required. MCPCBs have a metal core that efficiently dissipates heat away from the Micro LEDs, helping to prevent overheating and maintain optimal performance.
The choice of base material depends on the specific requirements of the Micro LED application, including thermal management, mechanical flexibility, electrical properties, and cost considerations. Manufacturers may select different materials based on the desired performance characteristics and the constraints of the application.
Which company makes Micro LED PCB?
Currently, many companies are involved in the research, development, and manufacturing of Micro LED PCBs. These companies include well-known electronic component manufacturers, PCB manufacturers, as well as companies specializing in Micro LED technology. Some of the notable companies in this field include Samsung, Huawei, LG, Sony, Infineon, and Taiwan Semiconductor Manufacturing Company (TSMC).
As a company specializing in electronic component manufacturing, our company is also capable of producing Micro LED PCBs. We have advanced production equipment and technology, as well as an experienced engineering team, to meet various customer requirements for Micro LED PCBs.
Our company possesses the following capabilities and advantages:
- Advanced manufacturing equipment:We are equipped with advanced production equipment, including automated production lines, precision machining equipment, and advanced testing devices. These facilities ensure the high-quality production of Micro LED PCBs.
- Professional engineering team:We have an experienced engineering team with strong technical expertise and innovation capabilities. They can provide customized designs according to customer requirements and offer professional technical support and solutions.
- Quality assurance system:Our company has established a strict quality management system, including full-process control from raw material procurement to production manufacturing, to ensure that products meet customer requirements and standards.
- Quick response capability:We prioritize customer needs and can respond quickly to customer demands, providing timely services. We are committed to establishing long-term and stable partnerships with customers to achieve mutual development.
In summary, our company has the technology, equipment, and team necessary for producing Micro LED PCBs. We can meet various customer requirements and provide high-quality products and services.
What are the 7 qualities of good customer service?
Good customer service is essential for building and maintaining strong relationships with customers. Here are seven qualities that contribute to excellent customer service:
- Responsiveness:Responding promptly to customer inquiries, concerns, and requests demonstrates attentiveness and shows customers that their needs are being prioritized. Timely responses help resolve issues efficiently and enhance customer satisfaction.
- Empathy:Empathy involves understanding and acknowledging the customer’s feelings, concerns, and perspectives. It requires putting oneself in the customer’s shoes and showing genuine concern for their well-being. Empathetic interactions can help build trust and rapport with customers.
- Clear Communication:Effective communication is crucial for conveying information clearly and accurately. Customer service representatives should communicate in a manner that is easy to understand, avoiding jargon or technical language when interacting with customers. Listening actively and asking clarifying questions can ensure mutual understanding and prevent misunderstandings.
- Problem-solving Skills:Good customer service involves the ability to identify and resolve customer issues efficiently. Customer service representatives should be equipped with problem-solving skills to address challenges effectively and find solutions that meet the customer’s needs. They should also have the authority and resources to resolve issues promptly.
- Professionalism:Professionalism entails maintaining a courteous and respectful demeanor when interacting with customers. Customer service representatives should remain calm and composed, even in challenging situations, and treat customers with respect and courtesy at all times. Professionalism fosters trust and confidence in the company’s brand and services.
- Product Knowledge:Having a thorough understanding of the company’s products or services allows customer service representatives to provide accurate information and assistance to customers. Product knowledge enables them to answer questions, make recommendations, and troubleshoot issues effectively, enhancing the overall customer experience.
- Going the Extra Mile:Exceptional customer service often involves going above and beyond to exceed customer expectations. This may include offering personalized assistance, providing additional support or resources, or offering special discounts or incentives to show appreciation for the customer’s business. Going the extra mile demonstrates a commitment to customer satisfaction and can lead to long-term loyalty and advocacy.
By embodying these qualities, companies can deliver outstanding customer service that fosters positive relationships, builds loyalty, and drives business success.
FAQs
What are the lead times for Micro LED PCB production?
Lead times can vary depending on factors such as order size, complexity, and current production workload. Our sales team can provide specific lead time estimates based on your requirements.
Do you offer prototype Micro LED PCB manufacturing?
Yes, we offer prototype manufacturing services to help clients validate designs and test functionalities before mass production.
What quality control measures do you have in place during Micro LED PCB production?
We implement rigorous quality control processes at every stage of production to ensure that Micro LED PCBBs meet our high standards for performance, reliability, and durability.
Can you assist with Micro LED PCB design optimization?
Yes, our engineering team can provide design optimization recommendations to enhance the performance, manufacturability, and cost-effectiveness of Micro LED PCBB designs.
What are the available surface finish options for Micro LED PCBBs?
We offer various surface finish options, including HASL (Hot Air Solder Leveling), ENIG (Electroless Nickel Immersion Gold), and OSP (Organic Solderability Preservatives), among others, to meet specific application requirements.
Do you provide Micro LED PCBB assembly services?
Yes, we offer PCB assembly services, including surface mount technology (SMT) and through-hole assembly, to provide comprehensive solutions for our clients’ PCB manufacturing needs.