Micro Cavity Substrates Manufacturing
Micro Cavity Substrates Manufacturing,Microcavity substrates are foundational materials crucial for the construction of advanced photonic and optoelectronic devices. These substrates play a pivotal role in confining and controlling light within extremely small volumes, typically on the scale of the wavelength of light or smaller. By harnessing the principles of optical resonance and confinement, microcavity substrates enable the development of highly efficient and compact devices such as lasers, light-emitting diodes (LEDs), optical filters, and sensors. Their precise fabrication involves techniques such as thin-film deposition, lithography, and etching to create intricate microstructures tailored to specific applications. Key properties of microcavity substrates include high optical transparency, low optical losses, uniform thickness, smooth surface finish, and compatibility with semiconductor processing techniques. These substrates serve as the backbone for innovations in fields ranging from telecommunications and biomedical imaging to environmental sensing and quantum computing, driving advancements in optical technology and enabling new possibilities for miniaturized and integrated photonic systems.
What is a Micro cavity Substrate (MCS)?
A Micro cavity Substrate (MCS) typically refers to a substrate material used in microelectronic and optoelectronic devices, particularly in the context of microcavity structures. Microcavities are optical or photonic structures that confine light within a small volume, typically on the order of the wavelength of light or smaller.
MCS is designed to facilitate the fabrication and performance of microcavity devices. It often possesses specific properties such as high optical transparency, low optical losses, precise thickness control, and compatibility with semiconductor processing techniques.
These substrates are crucial for applications such as microcavity lasers, microcavity light-emitting diodes (LEDs), photonic integrated circuits, and various sensors. By confining and controlling the propagation of light within tiny cavities, microcavity devices can achieve enhanced light-matter interactions and improved performance characteristics compared to conventional devices.
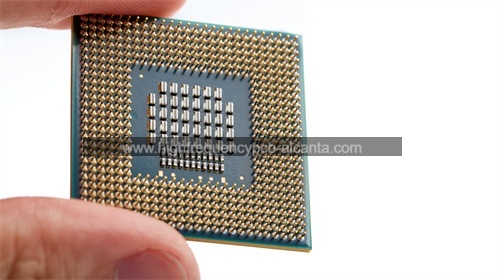
Micro cavity substrates manufacturing
What are the Micro cavity Substrate Design Guidelines?
Microcavity substrate design guidelines may vary depending on the specific application and the desired characteristics of the microcavity device. However, some general design guidelines for microcavity substrates include:
- Optical Transparency: The substrate material should have high optical transparency in the wavelength range of interest for the application. This ensures efficient transmission of light through the substrate and into the microcavity.
- Low Optical Losses: Minimize optical losses within the substrate material to maintain high optical efficiency of the microcavity device.
- Smooth Surface: The substrate surface should be smooth to minimize scattering and absorption of light, which can degrade the performance of the microcavity device.
- Uniform Thickness: Ensure uniform thickness across the substrate to maintain consistency in optical properties and device performance.
- Compatibility with Fabrication Processes: Select a substrate material that is compatible with the fabrication processes involved in manufacturing the microcavity device, such as deposition, etching, and bonding techniques.
- Thermal Stability: The substrate material should have good thermal stability to withstand processing conditions and to ensure the stability of the microcavity device during operation.
- Chemical Compatibility: Ensure that the substrate material is chemically compatible with other materials used in the microcavity device to prevent degradation or unwanted reactions.
- Dielectric Properties: Consider the dielectric properties of the substrate material, such as refractive index and permittivity, to optimize the optical behavior of the microcavity.
- Mechanical Strength: The substrate material should have sufficient mechanical strength to withstand handling and integration into the device without damage.
- Cost and Availability: Consider the cost and availability of the substrate material, especially for large-scale production of microcavity devices.
By adhering to these design guidelines, engineers and researchers can optimize the performance, reliability, and manufacturability of microcavity devices for various applications such as lasers, LEDs, sensors, and photonic integrated circuits.
What is the Micro cavity Substrate Fabrication Process?
The fabrication process for microcavity substrates can vary depending on the specific requirements of the device and the materials involved. However, a general overview of the fabrication process for microcavity substrates may include the following steps:
- Substrate Selection: Choose a suitable substrate material based on its optical, mechanical, and chemical properties, as well as its compatibility with the fabrication process and the intended application of the microcavity device.
- Cleaning and Surface Preparation: Clean the substrate surface thoroughly to remove any contaminants or residues that could affect the subsequent processing steps. Surface preparation may involve treatments such as solvent cleaning, plasma cleaning, or chemical etching to improve adhesion and uniformity.
- Deposition of Thin Films: Deposit thin films of materials onto the substrate surface using techniques such as physical vapor deposition (PVD), chemical vapor deposition (CVD), sputtering, or spin coating. These thin films may include layers of dielectric materials, semiconductors, metals, or other functional materials required for the microcavity structure.
- Patterning: Define the desired microcavity structure and features on the substrate surface through patterning techniques such as photolithography, electron beam lithography, or nanoimprint lithography. Patterning creates the geometric layout and dimensions of the microcavities, waveguides, or other optical elements.
- Etching and Removal: Use etching processes such as dry etching (plasma etching) or wet etching to selectively remove material from the substrate surface and create the desired features. Etching is typically performed to define the cavity structures, waveguides, or other components of the microcavity device.
- Surface Planarization: Optionally, perform surface planarization techniques such as chemical mechanical polishing (CMP) or spin coating to smoothen the substrate surface and remove any roughness or irregularities introduced during the etching process.
- Final Cleaning and Inspection: Clean the fabricated microcavity substrate to remove any residues or contaminants introduced during the fabrication process. Perform thorough inspections to ensure the quality, uniformity, and integrity of the fabricated substrate.
- Integration and Device Assembly: Integrate the fabricated microcavity substrate with other components, such as semiconductor chips, optical elements, electrodes, or packaging materials, to assemble the complete microcavity device.
- Characterization and Testing: Characterize the optical, electrical, and mechanical properties of the fabricated microcavity device through various testing techniques such as spectroscopy, microscopy, and device performance measurements.
By following these fabrication steps and optimizing the process parameters, researchers and engineers can fabricate high-quality microcavity substrates tailored to specific applications in photonics, optoelectronics, and microelectronics.
How do you manufacture a Micro cavity Substrate?
Manufacturing a microcavity substrate involves several steps, which can vary depending on the specific design and materials involved. Here’s a general overview of the manufacturing process:
- Substrate Selection: Choose a substrate material that meets the requirements for optical transparency, mechanical stability, and compatibility with fabrication processes. Common substrate materials include silicon, glass, quartz, sapphire, and various polymers.
- Cleaning and Preparation: Clean the substrate surface thoroughly to remove any contaminants, dust, or residues. This step is crucial to ensure proper adhesion and uniformity of subsequent layers. Techniques such as solvent cleaning, plasma cleaning, or chemical etching may be used.
- Deposition of Thin Films: Deposit thin films onto the substrate surface using techniques such as physical vapor deposition (PVD), chemical vapor deposition (CVD), sputtering, or spin coating. These thin films may include dielectric layers, semiconductors, metals, or other functional materials required for the microcavity structure.
- Patterning: Define the desired microcavity structure and features on the substrate surface through patterning techniques such as photolithography, electron beam lithography, or nanoimprint lithography. Patterning creates the geometric layout and dimensions of the microcavities, waveguides, or other optical elements.
- Etching and Removal: Use etching processes such as dry etching (plasma etching) or wet etching to selectively remove material from the substrate surface and create the desired features. Etching is typically performed to define the cavity structures, waveguides, or other components of the microcavity device.
- Surface Planarization: Optionally, perform surface planarization techniques such as chemical mechanical polishing (CMP) or spin coating to smoothen the substrate surface and remove any roughness or irregularities introduced during the etching process.
- Cleaning and Inspection: Clean the fabricated microcavity substrate again to remove any residues or contaminants introduced during the manufacturing process. Perform thorough inspections to ensure the quality, uniformity, and integrity of the fabricated substrate.
- Integration and Packaging: Integrate the fabricated microcavity substrate with other components, such as semiconductor chips, optical elements, electrodes, or packaging materials, to assemble the complete microcavity device. This step may involve bonding, assembly, and encapsulation processes.
- Testing and Characterization: Characterize the optical, electrical, and mechanical properties of the fabricated microcavity device through various testing techniques such as spectroscopy, microscopy, and device performance measurements. This step ensures that the device meets the desired specifications and performance requirements.
By following these manufacturing steps and optimizing the process parameters, manufacturers can produce high-quality microcavity substrates for applications in photonics, optoelectronics, and microelectronics.
How much should a Micro cavity Substrate cost?
The cost of a microcavity substrate can vary widely depending on factors such as the material used, the size and complexity of the substrate, the fabrication process involved, and the quantity being produced. Additionally, market dynamics, supply chain factors, and specific application requirements can also influence the cost.
Here are some factors to consider when determining the cost of a microcavity substrate:
- Material Cost: The cost of the substrate material itself is a significant factor. Different materials, such as silicon, glass, quartz, sapphire, and various polymers, have different costs associated with them.
- Fabrication Process Cost: The cost of the fabrication process, including deposition, patterning, etching, and other manufacturing steps, contributes to the overall cost of the substrate. More complex or specialized fabrication processes may incur higher costs.
- Labor Cost: Labor costs associated with the manufacturing process, including skilled labor required for handling and processing, also influence the overall cost.
- Quality and Precision Requirements: Higher quality substrates with tighter tolerances and more precise features may require additional manufacturing steps or tighter process control, which can increase costs.
- Volume and Scale: Economies of scale play a significant role in determining the cost. Larger production volumes often result in lower per-unit costs due to spreading fixed costs over a larger number of units.
- Customization and Specialization: Customized or specialized substrates designed for specific applications may involve additional design, development, and testing costs, which can increase the overall cost.
- Market Factors: Market demand, competition, and supply chain dynamics can also impact the cost of microcavity substrates. Prices may fluctuate based on market conditions and availability of materials and resources.
Given these factors, it’s challenging to provide a specific cost estimate without knowing the details of the substrate’s specifications, materials, and manufacturing process. However, microcavity substrates can range in cost from a few dollars for simple, standard substrates to hundreds or even thousands of dollars for complex, specialized substrates designed for specific applications.
What is a Micro cavity Substrate base material?
The base material used for microcavity substrates can vary depending on the specific requirements of the device and the fabrication process. Some common base materials for microcavity substrates include:
- Silicon: Silicon is a widely used material for microcavity substrates due to its excellent optical transparency in the infrared range, compatibility with semiconductor processing techniques, and mechanical stability.
- Glass: Various types of glasses, such as fused silica, borosilicate glass, and quartz, are used as substrates for microcavity devices. Glass substrates offer high optical transparency across a broad range of wavelengths and can be fabricated with smooth surfaces.
- Sapphire: Sapphire (single-crystal aluminum oxide) substrates are valued for their high optical transparency, mechanical hardness, and thermal stability. Sapphire substrates are often used in high-power and high-temperature applications.
- Polymers: Certain polymers, such as poly(methyl methacrylate) (PMMA), cyclic olefin copolymers (COC), and polydimethylsiloxane (PDMS), are used as substrate materials for flexible and bio-compatible microcavity devices.
- Semiconductor Substrates: Substrates made from semiconductor materials like gallium arsenide (GaAs) or indium phosphide (InP) are used in microcavity devices, especially in integrated photonics applications.
- Metals: Metal substrates, such as aluminum or stainless steel, are sometimes used as base materials for microcavity devices, particularly in applications requiring high thermal conductivity or electrical conductivity.
The choice of base material depends on factors such as optical transparency, mechanical stability, thermal properties, compatibility with fabrication processes, and the specific requirements of the microcavity device’s application. Each material offers unique advantages and limitations, and the selection is often tailored to optimize the performance and functionality of the microcavity device.
Which company manufactures Micro cavity Substrates?
There are many companies dedicated to manufacturing microcavity substrates, with some of them leading in this field. These companies are typically focused on photonics, semiconductor, or nanotechnology, possessing advanced manufacturing equipment and technical teams.
For example, Japanese company Panasonic Corporation and American company Corning Incorporated are among the companies that have made achievements in the field of microcavity substrates. Their products are widely used in areas such as lasers, LEDs, optical sensors, and bio-sensors.
Our company also has the capability to produce microcavity substrates. We have advanced manufacturing equipment and an experienced technical team, capable of customizing various types of microcavity substrates according to customer requirements. Our production process is precise and reliable, ensuring that our products have excellent optical transparency, surface smoothness, and dimensional accuracy.
Our microcavity substrates are widely used in photonics devices, lasers, sensors, biomedical devices, and other fields. We are committed to providing high-quality products and excellent services to meet our customers’ needs and contribute to the success of their projects.
Our core competitive advantages include:
- Professional Team: We have an experienced technical team that can provide professional technical support and customized solutions.
- Advanced Equipment: We have introduced advanced production equipment and technology to ensure the quality and stability of our products.
- Flexible Production: We can flexibly adjust production plans according to customer needs to meet orders promptly.
- Quality Assurance: We strictly control the production process and conduct rigorous quality testing to ensure that each batch of products meets high-quality standards.
Through our efforts and continuous innovation, we believe that we can become a reliable supplier of microcavity substrates for you and contribute to the success of your projects.
What are the 7 qualities of good customer service?
Good customer service typically involves providing assistance or support to customers in a manner that meets or exceeds their expectations and leaves them satisfied with their experience. Here are seven qualities commonly associated with good customer service:
- Responsiveness: Responding promptly to customer inquiries, requests, or concerns demonstrates attentiveness and shows customers that their needs are being prioritized. Whether it’s answering phone calls, replying to emails, or addressing issues in person, being responsive is essential for good customer service.
- Empathy: Empathy involves understanding and sharing the feelings of customers, especially when they are facing challenges or expressing dissatisfaction. Showing empathy can help build rapport, establish trust, and make customers feel valued and understood.
- Clear Communication: Effective communication is crucial for good customer service. Clearly conveying information, instructions, or solutions in a courteous and understandable manner helps prevent misunderstandings and ensures that customers receive the assistance they need.
- Knowledgeability: Having a good understanding of the products or services offered, as well as company policies and procedures, enables customer service representatives to provide accurate and helpful information to customers. Knowledgeable staff can address inquiries more efficiently and effectively, leading to a positive customer experience.
- Professionalism: Maintaining professionalism in all interactions with customers, regardless of the situation, is essential for building trust and credibility. This includes being courteous, respectful, and maintaining a positive attitude, even when dealing with challenging or difficult customers.
- Problem-Solving Skills: Being able to effectively identify and resolve customer issues or concerns demonstrates problem-solving skills. Customer service representatives should be empowered to take ownership of problems and work towards finding satisfactory solutions for customers.
- Consistency: Consistency in delivering high-quality customer service across all channels and interactions is key to building a strong reputation and fostering customer loyalty. Customers should receive consistent levels of service regardless of the time of day, the channel used to contact support, or the specific representative they interact with.
By embodying these qualities, businesses can create positive experiences for their customers, enhance satisfaction levels, and build long-term relationships that contribute to business success.
FAQs (Frequently Asked Questions)
What are microcavity substrates?
Microcavity substrates are materials used as the foundation for microcavity structures, which confine and manipulate light in small volumes. These substrates are crucial components in various photonics and optoelectronic devices.
What are the applications of microcavity substrates?
Microcavity substrates find applications in a wide range of devices, including lasers, light-emitting diodes (LEDs), photonic integrated circuits, sensors, and optical filters.
What materials are commonly used for microcavity substrates?
Common materials include silicon, glass, quartz, sapphire, polymers, and semiconductor substrates like gallium arsenide (GaAs) or indium phosphide (InP), depending on the specific requirements of the application.
What are the key properties of microcavity substrates?
Key properties include high optical transparency, low optical losses, precise thickness control, smooth surface finish, thermal stability, and compatibility with fabrication processes.
How are microcavity substrates fabricated?
Fabrication typically involves processes such as deposition of thin films, patterning using lithography techniques, etching to define cavity structures, surface planarization, cleaning, and inspection.
What factors influence the cost of microcavity substrates?
Factors such as the substrate material, fabrication process complexity, volume of production, customization requirements, and market dynamics can impact the cost of microcavity substrates.
Where can microcavity substrates be purchased?
Microcavity substrates can be sourced from specialized manufacturers, suppliers of photonics or optoelectronics components, or through custom fabrication services, depending on the specific requirements.