Micro Cavity PCB Manufacturing
Micro Cavity PCB Manufacturing,Micro cavity PCBs are specialized printed circuit boards designed with embedded voids or cavities within the board itself. These cavities are meticulously crafted using precise routing or milling techniques during the manufacturing process. The primary purpose of these cavities is to accommodate electronic components flush with the surface of the board, allowing for compact and space-efficient designs. Micro cavity PCBs offer several advantages, including reduced footprint, improved thermal management, enhanced mechanical stability, and protection for sensitive components. They find applications in various industries such as aerospace, automotive, medical devices, telecommunications, and consumer electronics, where miniaturization and high-density packaging are crucial. Design considerations for micro cavity PCBs include cavity dimensions, component placement within cavities, routing to avoid interference, thermal management, and ensuring structural integrity. Manufacturers employ stringent quality control measures to ensure precise cavity dimensions, accurate component placement, electrical continuity, and adherence to design specifications.
What is a Micro cavity PCB?
A micro cavity PCB (Printed Circuit Board) refers to a specialized type of PCB designed with embedded cavities or voids within the board itself. These cavities are typically created using controlled depth routing or milling techniques during the PCB manufacturing process.
Micro cavity PCBs are used in applications where components need to be mounted flush with the surface of the board or where space-saving is crucial. By embedding components within the PCB, the overall footprint of the electronic device can be reduced, allowing for more compact and streamlined designs.
These boards are commonly used in various industries such as aerospace, automotive, medical devices, and consumer electronics, where miniaturization and high-density packaging are essential requirements.
The design and manufacturing of micro cavit
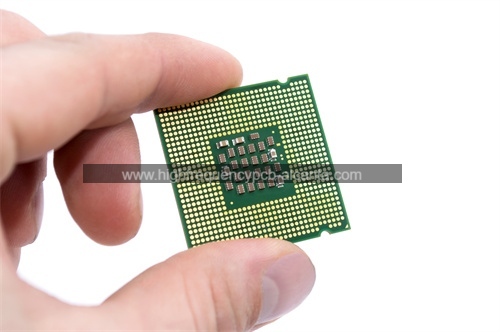
Micro Cavity PCB Manufacturing
What are the Micro cavity PCB Design Guidelines?
Here are some general design guidelines for micro cavity PCBs:
- Cavity Size and Depth: Ensure that the cavities are appropriately sized and deep enough to accommodate the components while maintaining structural integrity. The depth should be sufficient to prevent interference with adjacent layers and traces.
- Component Placement: Plan component placement carefully to ensure that components fit precisely within the cavities without protruding above the PCB surface. This may involve adjusting component sizes or cavity dimensions.
- Routing and Traces: Design routing and traces to avoid passing through cavities whenever possible. If routing through a cavity is unavoidable, ensure that there is enough clearance to prevent short circuits or mechanical interference.
- Cavity Wall Thickness: Maintain adequate wall thickness around the cavities to provide structural support and prevent flexing or deformation during manufacturing and use.
- Material Selection: Choose PCB materials with appropriate properties for micro cavity applications, such as high strength and dimensional stability. Consider materials with low moisture absorption to minimize the risk of warping.
- Cavity Encapsulation: Consider encapsulating cavities with protective materials or coatings to prevent debris accumulation, improve electrical insulation, and enhance mechanical stability.
- Thermal Management: Implement effective thermal management strategies, especially if components inside the cavities generate significant heat. Ensure adequate ventilation and consider adding heat sinks or thermal vias as needed.
- Testing and Inspection: Develop testing and inspection procedures to verify the integrity of cavities and ensure proper component seating. This may include visual inspection, mechanical measurements, and electrical testing.
- Manufacturability: Optimize the design for manufacturability by considering the capabilities and limitations of PCB fabrication processes, such as drilling, milling, and lamination.
- Documentation: Provide clear documentation detailing cavity dimensions, component placement guidelines, material specifications, and any other relevant information to facilitate manufacturing and assembly processes.
By following these guidelines, designers can create micro cavity PCBs that meet performance requirements while ensuring reliability and manufacturability.
What is the Micro cavity PCB Fabrication Process?
The fabrication process for micro cavity PCBs involves several steps, including design, material selection, substrate preparation, cavity creation, component placement, and finishing. Here’s a general overview of the process:
- Design: The PCB design is created using computer-aided design (CAD) software, taking into account the layout of components, routing of traces, and placement of cavities. Design considerations for micro cavity PCBs include cavity dimensions, component placement within cavities, and routing to avoid interference with cavities.
- Material Selection: Choose suitable materials for the PCB substrate based on factors such as mechanical strength, thermal properties, and electrical performance. Common substrate materials for micro cavity PCBs include FR-4, high-frequency laminates, and specialized materials with low dielectric constant.
- Substrate Preparation: Prepare the substrate material by cleaning and surface treatment to ensure proper adhesion of layers and components during the fabrication process.
- Cavity Creation: Use precision drilling, routing, or milling techniques to create cavities in the substrate according to the design specifications. This may involve multiple passes and careful control of depth to achieve the desired cavity dimensions and ensure uniformity across the PCB.
- Component Placement: Mount electronic components onto the PCB substrate using surface mount technology (SMT) or through-hole technology (THT). Carefully place components within the cavities, ensuring proper alignment and clearance to avoid interference with cavity walls.
- Routing and Traces: Route electrical traces on the PCB surface, connecting components and creating electrical pathways according to the design requirements. Special care may be needed to route traces around cavities and avoid crossing through them whenever possible.
- Finishing: Apply surface finishes and coatings to the PCB to improve solderability, protect against corrosion, and enhance electrical performance. Common finishes include solder mask, solder plating, and conformal coatings.
- Quality Assurance: Perform thorough inspection and testing of the fabricated PCBs to verify dimensional accuracy, electrical continuity, and component functionality. This may involve visual inspection, automated testing, and electrical measurements.
- Assembly: If necessary, assemble the PCB into the final product, integrating additional components, connectors, and enclosures as required.
- Packaging and Shipping: Package the finished PCBs for shipment to customers or assembly facilities, ensuring proper handling and protection during transit.
Thoughout the fabrication process, careful attention to detail, precise control of manufacturing parameters, and adherence to design specifications are essential to ensure the quality and reliability of micro cavity PCBs. Collaboration between design engineers, fabrication technicians, and quality control personnel is crucial to achieving successful outcomes.
How do you manufacture a Micro cavity PCB?
Manufacturing a micro cavity PCB involves several intricate steps. Here’s an overview of the process:
- Design Preparation: Begin by creating a detailed design of the PCB using specialized software. This design should include the layout of components, traces, and the precise location and dimensions of the cavities.
- Material Selection: Choose the appropriate substrate material based on the requirements of the PCB, such as FR-4, high-frequency laminates, or specialized materials with specific properties like low dielectric constant.
- Substrate Preparation: Clean and prepare the substrate material to ensure proper adhesion and surface quality. This may involve processes such as chemical cleaning, surface roughening, and applying adhesion promoters.
- Cavity Creation: Use precision drilling, routing, or milling techniques to create the cavities in the substrate according to the design specifications. CNC (Computer Numerical Control) machines are often used for this purpose to achieve high accuracy and consistency.
- Lamination: If the PCB requires multiple layers, the cavities may be created before or after the lamination process. During lamination, multiple layers of substrate material are bonded together with prepreg and copper foil to form the complete PCB stack.
- Component Placement: Mount electronic components onto the PCB substrate using surface mount technology (SMT) or through-hole technology (THT). Carefully place components within the cavities, ensuring proper alignment and clearance.
- Routing and Traces: Use chemical etching or mechanical milling to create the electrical traces on the PCB surface, connecting the components according to the design requirements. Special care must be taken to route traces around cavities and avoid crossing through them whenever possible.
- Surface Finishing: Apply surface finishes and coatings to the PCB to improve solderability, protect against corrosion, and enhance electrical performance. Common finishes include solder mask, solder plating, and conformal coatings.
- Testing and Inspection: Perform thorough testing and inspection of the fabricated PCBs to verify dimensional accuracy, electrical continuity, and component functionality. This may involve visual inspection, automated testing, and electrical measurements.
- Assembly and Packaging: If necessary, assemble the PCB into the final product, integrating additional components, connectors, and enclosures as required. Finally, package the finished PCBs for shipment to customers or assembly facilities.
Throughout the manufacturing process, strict quality control measures should be implemented to ensure the reliability and performance of the micro cavity PCBs. Collaboration between design engineers, manufacturing technicians, and quality assurance personnel is essential to achieving successful outcomes.
How much should a Micro cavity PCB cost?
The cost of a micro cavity PCB can vary significantly depending on various factors such as the complexity of the design, the number of layers, the substrate material, the size of the board, the quantity ordered, and the manufacturer’s pricing structure. Additionally, any additional features such as special surface finishes, impedance control, and tight tolerances will also impact the cost.
As a rough estimate, the cost of a basic micro cavity PCB without many complexities could range from $5 to $50 per square inch for low-volume orders. However, for more complex designs or higher quantities, the cost per square inch may decrease due to economies of scale.
It’s essential to request quotes from multiple PCB manufacturers to compare prices and find the best balance between cost, quality, and lead time for your specific project requirements. Additionally, factors such as manufacturing location, certifications, and the manufacturer’s reputation for quality and reliability should also be considered when choosing a supplier.
What is Micro cavity PCB base material?
The base material for micro cavity PCBs can vary depending on the specific requirements of the application. However, some common base materials used in the manufacturing of micro cavity PCBs include:
- FR-4: FR-4 (Flame Retardant 4) is a widely used epoxy-based laminate material reinforced with woven glass fibers. It offers good mechanical strength, thermal stability, and electrical insulation properties, making it suitable for many applications.
- High-Frequency Laminates: High-frequency laminates are engineered materials designed to provide excellent electrical performance at high frequencies. These materials typically have low dielectric constants and low loss tangents, making them suitable for applications such as RF/microwave circuits and high-speed digital systems.
- Polyimide (PI): Polyimide is a high-temperature-resistant polymer material that offers excellent thermal stability and mechanical properties. It is commonly used in applications requiring flexibility, such as flexible PCBs or circuits subjected to high-temperature environments.
- Rogers Corporation Materials: Rogers Corporation manufactures a range of specialty laminates optimized for specific applications, including high-frequency, high-speed digital, and thermal management. Examples include Rogers RO4000 series and RO3000 series laminates.
- Specialized Materials: In some cases, specialized materials may be used for unique applications, such as ceramic substrates for high-power electronics or metal core PCBs for thermal management.
The choice of base material depends on factors such as the operating environment, electrical performance requirements, thermal management needs, and cost considerations. Design engineers typically select the base material that best meets the specific requirements of the micro cavity PCB design while balancing factors such as performance, cost, and manufacturability.
Which company makes Micro cavity PCBs?
Currently, there are many companies specialized in manufacturing micro cavity PCBs, including well-known electronics manufacturers and professional PCB manufacturers. These companies typically have advanced technological equipment, extensive experience, and professional teams to meet the demand for high-quality micro cavity PCBs.
Our company is also a professional PCB manufacturer with many years of experience and abundant technical strength. We have industry-leading manufacturing processes and equipment capable of producing various types of PCBs, including micro cavity PCBs.
As a professional PCB manufacturer, we have the following advantages and capabilities:
- Advanced Manufacturing Equipment: We have advanced PCB manufacturing equipment and technology, including high-precision CNC drilling, milling, and routing equipment, enabling precise manufacturing of micro cavity PCBs.
- Rich Experience: Our team has rich experience and professional knowledge in the PCB manufacturing field with a good reputation. We can provide customized solutions according to customer requirements and specifications.
- Quality Assurance: We strictly adhere to ISO quality management systems to ensure all PCBs produced meet customer requirements and industry standards. We employ rigorous quality control processes and testing methods to ensure each stage meets the highest quality standards.
- Timely Delivery: We value customer time and requirements, ensuring timely delivery of high-quality products. We optimize production processes and improve production efficiency to ensure on-time delivery.
- Flexible Production Capacity: We have flexible production capacity to meet different order requirements in terms of quantity and specifications. Whether it’s small batch customization or large-scale production, we can meet customer needs.
In summary, as a professional PCB manufacturer, we have the technical strength, experience, and resources required to produce micro cavity PCBs. We are committed to providing customers with high-quality, reliable products, and excellent services, working together with customers to develop and create a better future.
What are the 7 qualities of good customer service?
Good customer service typically encompasses several key qualities that contribute to positive interactions and relationships with customers. Here are seven qualities often associated with excellent customer service:
- Responsiveness: Good customer service involves promptly addressing customer inquiries, concerns, or issues. Responding to customers in a timely manner shows respect for their time and demonstrates a commitment to meeting their needs.
- Empathy: Empathy involves understanding and acknowledging the customer’s feelings, perspectives, and circumstances. Showing empathy can help build rapport, diffuse tense situations, and make customers feel valued and understood.
- Professionalism: Professionalism encompasses maintaining a courteous, respectful, and helpful demeanor when interacting with customers. Professionalism also involves adhering to company policies, procedures, and ethical standards while assisting customers.
- Product Knowledge: Customer service representatives should have a thorough understanding of the products or services offered by the company. Having comprehensive product knowledge enables representatives to provide accurate information, answer questions effectively, and offer appropriate solutions to customer inquiries or issues.
- Problem-Solving Skills: Effective problem-solving skills are crucial for resolving customer issues and addressing their concerns satisfactorily. Customer service representatives should be able to identify the root cause of problems, explore potential solutions, and work collaboratively with customers to reach a resolution.
- Consistency: Consistency in service delivery ensures that customers receive a uniform level of quality and attention across all interactions with the company. Consistency can help build trust and loyalty among customers by reinforcing positive experiences and expectations.
- Follow-Up and Feedback: Following up with customers after resolving their inquiries or issues demonstrates a commitment to customer satisfaction and allows for feedback collection. Soliciting feedback from customers provides valuable insights into areas for improvement and helps identify opportunities to enhance the customer experience further.
By embodying these qualities, organizations can cultivate a culture of excellent customer service and foster long-term relationships with their customers.
FAQs
What are micro cavity PCBs?
Micro cavity PCBs are specialized printed circuit boards that feature embedded voids or cavities within the board itself. These cavities are created to house electronic components flush with the surface, enabling compact and space-saving designs.
What are the advantages of micro cavity PCBs?
Micro cavity PCBs offer several advantages, including reduced footprint, improved thermal management, enhanced mechanical stability, and the ability to protect sensitive components from environmental factors.
What industries commonly use micro cavity PCBs?
Micro cavity PCBs find applications in various industries, including aerospace, automotive, medical devices, telecommunications, consumer electronics, and industrial automation, where miniaturization and high-density packaging are essential.
How are cavities created in micro cavity PCBs?
Cavities in micro cavity PCBs are typically created using controlled depth routing or milling techniques during the PCB manufacturing process. CNC (Computer Numerical Control) machines are often used to achieve precise cavity dimensions and alignment.
What materials are used in micro cavity PCBs?
Micro cavity PCBs are typically made from standard PCB substrate materials such as FR-4, high-frequency laminates, or specialized materials with specific properties suited for high-density applications.
What design considerations are important for micro cavity PCBs?
Design considerations for micro cavity PCBs include cavity dimensions, component placement within cavities, routing to avoid interference with cavities, thermal management, and ensuring structural integrity.
What quality control measures are implemented during micro cavity PCB manufacturing?
Quality control measures during micro cavity PCB manufacturing include thorough inspection and testing of cavity dimensions, component placement accuracy, electrical continuity, mechanical stability, and adherence to design specifications.
What are the cost factors associated with micro cavity PCBs?
The cost of micro cavity PCBs depends on factors such as complexity of design, substrate material, cavity creation techniques, quantity ordered, and additional features like surface finishes or special requirements for thermal management.
What are some common applications of micro cavity PCBs?
Common applications of micro cavity PCBs include sensor modules, medical implants, RF and microwave devices, wearable electronics, smart devices, and automotive electronics where space constraints and performance requirements are critical.
Where can I find a reliable manufacturer for micro cavity PCBs?
Reliable manufacturers for micro cavity PCBs can be found through online directories, industry associations, referrals, and trade shows. It’s essential to research and evaluate manufacturers based on their capabilities, experience, quality standards, and customer reviews before making a decision.