Metalized Ceramic Substrates Manufacturer
Metalized Ceramic Substrates Manufacturer,Metalized ceramic substrates are high-performance materials used in advanced electronic and thermal management applications. These substrates combine the durability of ceramic with metalization processes that add conductive layers for electrical connections. The metalized surface allows for efficient heat dissipation and enhances electrical conductivity, making them ideal for power electronics, RF applications, and high-temperature environments. The ceramic base provides excellent mechanical strength and thermal insulation, while the metal layers facilitate reliable signal transmission and connectivity. Metalized ceramic substrates are commonly used in components such as power modules, LED drivers, and high-frequency circuits, offering both thermal and electrical stability in demanding applications.
What is a Metalized Ceramic Substrate?
A Metalized Ceramic Substrate is a specialized type of substrate used in electronic and semiconductor applications. It combines the benefits of ceramic materials with metal layers to enhance performance and reliability.
Ceramic substrates are known for their excellent thermal conductivity, high dielectric strength, and mechanical stability. These properties make them ideal for applications requiring efficient heat dissipation and electrical insulation. However, ceramics alone are not conductive, which limits their use in certain electronic applications.
To address this limitation, metalized ceramic substrates are created by depositing a thin metal layer onto the ceramic base. This metal layer, typically made of materials like copper, nickel, or silver, allows for electrical conductivity and facilitates the creation of electronic circuits on the substrate. The metal layer is often applied using techniques such as sputtering, plating, or screen printing.
The combination of ceramic and metal provides a substrate that supports high-power applications and high-frequency circuits while maintaining thermal and electrical performance. Metalized ceramic substrates are commonly used in power electronics, RF/microwave applications, and LED technology due to their ability to manage heat effectively and their robustness under demanding conditions.
In summary, metalized ceramic substrates offer a balanced solution for applications requiring both high thermal and electrical performance. They are integral in ensuring the reliability and efficiency of modern electronic devices.
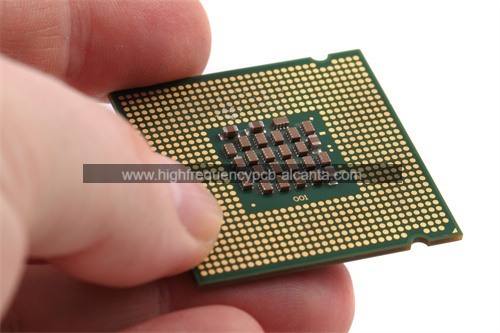
Metalized Ceramic Substrates Manufacturer
What is the Metalized Ceramic Substrate Design Guidelines?
Designing with Metalized Ceramic Substrates involves specific guidelines to ensure optimal performance and reliability. Here are some key considerations:
- Thermal Management: Ensure adequate heat dissipation by considering the thermal conductivity of both the ceramic and metal layers. Design the layout to maximize heat transfer and avoid hotspots, which can lead to component failure.
- Metal Layer Adhesion: Choose appropriate metal deposition techniques (e.g., sputtering, plating) and ensure proper surface preparation of the ceramic to enhance metal adhesion. Poor adhesion can result in delamination and reduced electrical performance.
- Thermal Expansion Matching: Match the coefficients of thermal expansion (CTE) of the ceramic substrate and the metal layer. Significant differences in CTE can lead to mechanical stress and potential cracking or delamination during thermal cycling.
- Electrical Design: Design traces and pads with adequate dimensions to handle current loads and minimize resistance. Ensure that the metal layer’s thickness and layout meet the electrical conductivity requirements for the intended application.
- Dielectric Considerations: Select a ceramic material with appropriate dielectric properties for your application. The dielectric constant and loss tangent should match the requirements of high-frequency or high-power applications to ensure signal integrity and minimal loss.
- Mechanical Stability: Design for mechanical stability, considering factors such as substrate thickness, mounting methods, and the potential for thermal or mechanical stresses. Proper support and handling are crucial to avoid damage during assembly and operation.
- Process Compatibility: Ensure that the substrate design is compatible with the chosen manufacturing processes, including metal deposition and subsequent component attachment. Design rules should accommodate process variations and tolerances.
- Cost and Efficiency: Balance design complexity and material costs with performance requirements. Optimizing the design for both functionality and cost-effectiveness can help in producing a competitive and reliable product.
By adhering to these guidelines, designers can create effective and reliable metalized ceramic substrates that meet the demands of various electronic and semiconductor applications.
What is the Metalized Ceramic Substrate Fabrication Process?
The fabrication process of Metalized Ceramic Substrates involves several key steps to ensure the desired performance and reliability. Here’s an overview of the typical process:
- Ceramic Substrate Preparation: Start with a high-quality ceramic base, such as alumina (Al₂O₃) or aluminum nitride (AlN). The ceramic is typically fabricated into the desired shape and size through methods like pressing, casting, or machining. It is then sintered at high temperatures to achieve the required density and mechanical properties.
- Surface Cleaning: Clean the surface of the ceramic substrate to remove any contaminants, such as dust, oils, or oxides. This step is crucial for ensuring good metal adhesion. Cleaning can be done using ultrasonic baths, chemical cleaning, or abrasive methods.
- Metalization: Apply a thin metal layer to the cleaned ceramic substrate. This can be done through various techniques:
– Sputtering: A physical vapor deposition process where metal atoms are ejected from a target and deposited onto the substrate.
– Electroless Plating: A chemical process that deposits a metal layer without the need for external electrical power.
– Electroplating: A process where metal ions are reduced onto the substrate using an electric current.
- Patterning: Define the metal pattern on the substrate to create conductive traces and pads. This can be done using photolithography, where a photoresist layer is applied, exposed to light through a mask, and then developed to create the desired pattern. The exposed metal is then etched away to form the circuit design.
- Annealing: Heat the substrate to a specific temperature to improve the adhesion of the metal layer and relieve any stress induced during the metal deposition and patterning processes. Annealing can also enhance the metal’s properties, such as its conductivity.
- Inspection and Testing: Conduct thorough inspection and testing to ensure the quality of the metalized ceramic substrate. This includes checking for defects, measuring electrical performance, and verifying the adhesion of the metal layer.
- Assembly: Attach electronic components to the substrate using techniques such as soldering, wire bonding, or adhesive bonding. The design should accommodate the thermal and mechanical stresses associated with these assembly methods.
- Final Testing: Perform final testing to ensure that the fully assembled substrate meets all functional and reliability requirements. This may include electrical, thermal, and mechanical tests.
By following these steps, manufacturers can produce metalized ceramic substrates that are suitable for high-performance applications, including power electronics, RF/microwave devices, and high-power LEDs.
How do you Manufacture a Metalized Ceramic Substrate?
Manufacturing a Metalized Ceramic Substrate involves several key steps to ensure high quality and performance. Here’s a general overview of the process:
- Ceramic Substrate Preparation: Begin by selecting the appropriate ceramic material based on the desired properties, such as thermal conductivity, dielectric strength, and mechanical stability. Common materials include alumina (Al2O3), aluminum nitride (AlN), and beryllium oxide (BeO). The ceramic is then cut and polished to the required dimensions and surface finish.
- Surface Cleaning and Activation: Clean the ceramic surface to remove any contaminants, dust, or oxides. This is typically done using ultrasonic cleaning, chemical etching, or plasma treatment. Surface activation ensures better adhesion of the metal layer by enhancing the surface’s wettability.
- Metal Deposition: Apply a metal layer to the ceramic substrate using one of several deposition techniques:
– Sputtering: A physical vapor deposition process where metal atoms are ejected from a target and deposited onto the ceramic surface.
– Electroplating: A chemical process that uses an electric current to reduce metal cations onto the substrate, forming a metal layer.
– Screen Printing: A technique where metal pastes are printed onto the ceramic and then sintered to form a metal layer.
- Metal Patterning: After the metal layer is deposited, pattern it to create the desired circuitry or features. This is typically done using photolithography, where a photosensitive resist is applied, exposed to UV light through a mask, and then developed to reveal the metal areas to be etched or plated.
- Etching and Sintering: For patterning, etching processes (like wet or dry etching) are used to remove unwanted metal from the substrate. If screen printing was used, the metal is sintered at high temperatures to enhance its adhesion and electrical properties.
- Component Attachment: Once the metal layer is patterned and finalized, electronic components can be attached using techniques such as soldering or wire bonding. The ceramic substrate’s surface and metal layer must be compatible with the chosen attachment methods.
- Final Inspection and Testing:Perform thorough inspections and testing to ensure the metalized ceramic substrate meets design specifications and quality standards. This may include electrical testing, thermal cycling tests, and visual inspections.
- Packaging: Finally, the finished substrates are packaged to protect them from damage during transport and handling. Packaging methods depend on the size and sensitivity of the substrates.
By following these steps, manufacturers can produce high-quality metalized ceramic substrates suitable for a wide range of electronic and semiconductor applications.
How Much Should a Metalized Ceramic Substrate Cost?
The cost of a metalized ceramic substrate can vary significantly based on several factors:
- Material Type: Different ceramic materials have varying costs. For example, alumina (Al2O3) is generally less expensive than aluminum nitride (AlN) or beryllium oxide (BeO), which are used for more demanding applications due to their superior thermal and electrical properties.
- Size and Thickness: Larger and thicker substrates will generally cost more due to increased material and processing requirements. Custom sizes and thicknesses may also influence the price.
- Metal Layer Specifications: The type of metal used (e.g., copper, nickel, silver) and its thickness affect the cost. More expensive metals or thicker layers will increase the overall price.
- Pattern Complexity: The complexity of the metal pattern and the precision required can impact cost. More intricate designs or higher precision requirements generally lead to higher manufacturing costs.
- Manufacturing Processes: The choice of deposition and patterning techniques (e.g., sputtering, electroplating, screen printing) can influence costs. Some processes are more costly due to the equipment and materials involved.
- Volume: Production volume plays a crucial role. Larger volumes typically benefit from economies of scale, reducing the per-unit cost. Small batch or custom orders often have higher per-unit costs.
- Additional Features: Features such as high-temperature stability, special coatings, or additional processing steps can increase costs.
As a rough estimate, basic metalized ceramic substrates might cost between $10 to $50 per unit for standard sizes and materials. More specialized or high-performance substrates can range from $100 to several hundred dollars per unit, depending on the factors mentioned above.
For a precise cost, it’s best to contact suppliers with specific requirements and get a detailed quote based on your particular needs.
What is Metalized Ceramic Substrate Base Material?
The base material of a metalized ceramic substrate refers to the ceramic material used as the foundation upon which metal layers are deposited. The choice of ceramic material is crucial as it affects the substrate’s thermal, electrical, and mechanical properties. Here are some common base materials:
- Alumina (Al2O3): One of the most widely used ceramic substrates, alumina offers good thermal conductivity, high dielectric strength, and cost-effectiveness. It is suitable for many electronic applications, including power electronics and sensors.
- Aluminum Nitride (AlN): Known for its superior thermal conductivity compared to alumina, aluminum nitride is used in high-power applications where efficient heat dissipation is critical. It also has good electrical insulation properties, making it ideal for high-frequency and high-power electronics.
- Beryllium Oxide (BeO): Beryllium oxide provides exceptional thermal conductivity and high thermal conductivity. It is used in high-performance applications but is less common due to its higher cost and handling precautions required due to its toxicity.
- Silicon Nitride (Si3N4): Silicon nitride is valued for its high mechanical strength and thermal shock resistance. It is used in applications where durability and resistance to thermal stress are important.
- Zirconia (ZrO2): Zirconia offers high toughness and is used in applications that require resistance to mechanical wear and thermal stress. It is less common but useful in specific niche applications.
- Magnesium Aluminate (Spinel): Magnesium aluminate spinel is used for its excellent thermal and mechanical properties. It is suitable for high-temperature applications where both strength and thermal resistance are required.
The choice of base material depends on the specific requirements of the application, including thermal management, electrical insulation, mechanical strength, and cost. Each ceramic material has its advantages and trade-offs, making it important to select the one that best fits the needs of the electronic device or system being designed.
Which Company Makes Metalized Ceramic Substrates?
In the field of metalized ceramic substrate manufacturing, several companies offer specialized products and services. These companies typically focus on providing high-quality metalized ceramic substrates for electronic devices and semiconductor applications. Here are some well-known manufacturers and suppliers:
- NTK Ceramics: NTK Ceramics is a leading ceramic material manufacturer offering various metalized ceramic substrates. The company is known for its high-quality aluminum nitride (AlN) substrates, widely used in high-power and high-frequency electronic devices.
- Kyocera: Kyocera is a globally recognized electronic materials supplier that offers a range of ceramic substrates, including metalized ceramic substrates. Kyocera’s products cover various applications, including power electronics, LEDs, and high-frequency applications.
- Rogers Corporation: Rogers is a key player in high-frequency circuit boards and metalized ceramic substrates. The company’s substrates are widely used in communications, automotive, and military electronics.
- LEATEC Fine Ceramics: LEATEC specializes in high-precision ceramic substrates, including metalized ceramic substrates. Their products are widely used in electronics, semiconductors, and optoelectronics.
- CoorsTek: CoorsTek is a global leader in engineering ceramics and metalized ceramic substrates. Their products are known for excellent mechanical and thermal performance, suitable for various high-performance applications.
- CeramTec: CeramTec offers a range of metalized ceramic substrates with high thermal conductivity and electrical insulation properties. The company focuses on providing customized solutions for high-tech applications.
Among these companies, our company also excels in manufacturing high-quality metalized ceramic substrates. Our metalized ceramic substrates are produced using advanced manufacturing processes, ensuring excellent thermal and electrical performance. Our products are suitable for power electronics, RF/microwave applications, and LED technology. With a highly experienced technical team, we provide customized solutions to meet specific customer needs, whether in material selection, metal layer design, or subsequent processing.
Our metalized ceramic substrate products not only guarantee high performance but also offer cost-effectiveness. Whether for standard specifications or custom requirements, we are dedicated to delivering high-quality products and services to help customers achieve optimal performance in various high-tech applications.
What Are the 7 Qualities of Good Customer Service?
Good customer service is essential for building strong relationships with customers and ensuring their satisfaction. Here are seven key qualities that define excellent customer service:
- Responsiveness: Promptly addressing customer inquiries, concerns, or issues is crucial. Quick responses demonstrate that the company values the customer’s time and is committed to resolving their needs efficiently.
- Empathy:Understanding and empathizing with the customer’s situation helps in building trust and rapport. Showing genuine concern for their problems and feelings makes customers feel valued and respected.
- Knowledge: Having a thorough understanding of the products or services offered is essential. Knowledgeable representatives can provide accurate information, offer relevant solutions, and enhance the overall customer experience.
- Communication Skills: Clear and effective communication is vital. This includes not only speaking clearly and professionally but also actively listening to the customer’s needs and responding appropriately.
- Patience: Dealing with customers, especially those who are frustrated or confused, requires patience. Taking the time to carefully address their concerns without rushing them helps in creating a positive experience.
- Consistency: Providing a consistent level of service across all interactions ensures that customers have a reliable experience. Consistency in service quality builds trust and loyalty over time.
- Follow-Up: Following up after resolving an issue or completing a service request shows that the company is committed to customer satisfaction. It provides an opportunity to ensure that the customer is satisfied and to address any remaining concerns.
Incorporating these qualities into customer service practices can lead to improved customer satisfaction, enhanced loyalty, and a stronger overall reputation for the company.
FAQs
What is a metalized ceramic substrate?
A metalized ceramic substrate is a ceramic base material coated with a metal layer. This combination provides both thermal conductivity and electrical conductivity, making it suitable for high-power and high-frequency electronic applications.
What materials are used for the ceramic base?
Common ceramic materials used for the base include alumina (Al2O3), aluminum nitride (AlN), beryllium oxide (BeO), silicon nitride (Si3N4), and zirconia (ZrO2). Each material offers different properties suited to specific applications.
What types of metals are used in metalization?
The metal layer can be made from various materials such as copper, nickel, silver, or gold. The choice depends on the required electrical conductivity, thermal performance, and cost considerations.
What are the main benefits of using metalized ceramic substrates?
They offer excellent thermal conductivity, high electrical insulation, mechanical strength, and reliability under high temperatures and power conditions. They are ideal for applications that require efficient heat dissipation and electrical performance.
How are metalized ceramic substrates manufactured?
The manufacturing process involves preparing the ceramic base, applying a metal layer through techniques like sputtering or electroplating, patterning the metal layer, and then performing any necessary finishing processes.
What are typical applications for metalized ceramic substrates?
They are commonly used in power electronics, RF/microwave applications, LED technology, and other high-performance electronics where thermal management and electrical conductivity are critical.
How do you select the right metalized ceramic substrate for an application?
Consider factors such as the thermal and electrical requirements, mechanical stresses, the operating environment, and cost. The choice of ceramic material and metal layer should align with the specific needs of your application.