Megtron7 Materials PCB Manufacturer
Megtron7 Materials PCB Manufacturer,Megtron7 Materials PCBs are advanced printed circuit boards renowned for their high-performance characteristics in demanding applications. These PCBs utilize Megtron7 materials, known for their exceptional electrical properties including low dielectric constant and low dissipation factor. Megtron7 Materials PCBs are designed for high-speed digital and RF/microwave applications where signal integrity and reliability are critical. They offer excellent thermal stability and mechanical strength, making them suitable for aerospace, telecommunications, and high-frequency electronic devices. Megtron7 Materials PCBs are manufactured with stringent quality control processes to ensure consistent performance and reliability in complex electronic systems requiring high-speed data transmission and precise impedance control.
What is Megtron7 Materials PCB?
Megtron7 (M7) is a high-performance PCB material developed by Panasonic. It belongs to the Megtron series, renowned for their excellent electrical properties suitable for high-frequency applications. Megtron7 PCBs are characterized by low transmission loss and low dielectric constant, which contribute to maintaining signal integrity at high frequencies. This makes them ideal for use in applications requiring high-speed data transmission, such as telecommunications, networking equipment, and high-frequency electronic devices.
The key features of Megtron7 include its high thermal reliability, allowing it to withstand high temperatures without significant loss of electrical properties, which is crucial for reliability in demanding environments. It also offers good dimensional stability and mechanical strength, which enhances its suitability for complex PCB designs and multilayer structures.
Manufacturing Megtron7 PCBs involves advanced processes to ensure uniformity and reliability across the board. This includes precise control over resin content and resin distribution within the laminate, which helps in achieving consistent electrical performance and reliability.
In summary, Megtron7 Materials PCBs are sought after for their high-frequency performance, reliability in harsh conditions, and suitability for complex designs, making them a preferred choice in the realm of high-speed and high-frequency electronic applications.
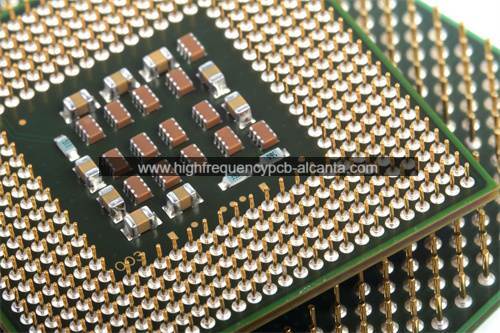
Megtron7 Materials PCB Manufacturer
What are the Megtron7 Materials PCB Design Guidelines?
Design guidelines for Megtron7 Materials PCB focus on optimizing the performance and reliability of circuits using this high-performance substrate. Here are some key considerations:
- Material Properties: Understand and leverage the electrical properties of Megtron7, such as its low dielectric constant (εr) and low dissipation factor (Df), which are crucial for high-speed signal integrity.
- Stackup Design: Design the PCB stackup to minimize signal loss and impedance variations. Utilize controlled impedance routing to maintain signal integrity, considering the dielectric thickness and copper thickness variations.
- Transmission Line Design: Follow transmission line guidelines to ensure controlled impedance traces. Maintain consistent trace width, spacing, and layer stackup to minimize signal reflections and losses, especially at high frequencies.
- Via Design: Optimize via design for high-frequency performance. Use proper via structures like microvias or buried vias to minimize signal distortion and impedance changes.
- Thermal Management: Megtron7 has good thermal conductivity, but effective thermal management is still essential for reliability. Design for adequate heat dissipation, especially in high-power applications, and consider using thermal vias or heat sinks as necessary.
- Mechanical Considerations: Ensure adequate mechanical strength and dimensional stability in the PCB design. Megtron7’s properties contribute to its robustness, but designs should account for mechanical stresses and environmental factors.
- Manufacturing and Assembly: Work closely with PCB manufacturers experienced with handling Megtron7. Consider manufacturing tolerances and capabilities for achieving the desired PCB performance.
- Testing and Validation: Perform thorough signal integrity simulations and testing to verify design performance. Validate impedance calculations, signal integrity, and thermal management through prototype testing.
By adhering to these guidelines, designers can harness the full potential of Megtron7 Materials PCBs for demanding applications requiring high-frequency performance, reliability, and signal integrity.
What is the Megtron7 Materials PCB Fabrication Process?
The fabrication process for Megtron7 Materials PCBs involves several key steps to ensure the material’s high-performance properties are maintained throughout manufacturing. Here’s an overview of the typical fabrication process:
- Material Preparation:Megtron7 laminate sheets are prepared, which consist of prepreg layers (resin-impregnated fiberglass) and copper foils adhered together. These materials are selected based on specific thickness and copper weight requirements for the PCB design.
- Drilling:Holes for vias and component mounting pads are drilled into the laminate sheets. Advanced drilling techniques ensure precision and accuracy to meet the design specifications.
- Copper Foil Application:Copper foils are laminated onto both sides of the laminate sheets. These foils provide the conductive pathways for electrical signals and are patterned according to the PCB layout design.
- Etching:The excess copper is removed from the laminate surface using chemical etching processes. This step defines the copper traces and pads according to the design’s circuit pattern.
- Layer Alignment and Lamination: Multiple layers of prepped laminate with copper foil are aligned and laminated together under heat and pressure. This process forms the multilayer structure of the PCB, with each layer contributing to the overall circuit design.
- Via Formation: Vias (holes for electrical connections between different layers) are formed either through mechanical drilling or laser drilling techniques. For Megtron7 PCBs, precise via formation is critical to maintain high-frequency performance and signal integrity.
- Copper Plating:Through electrolytic copper plating, the walls of the vias and the exposed copper surfaces are plated to enhance conductivity and ensure reliable electrical connections throughout the PCB.
- Surface Finishing:The PCB’s surface is coated with a finish to protect the copper from oxidation and facilitate soldering during component assembly. Common surface finishes include HASL (Hot Air Solder Leveling), ENIG (Electroless Nickel Immersion Gold), and OSP (Organic Solderability Preservatives).
- Solder Mask Application:A solder mask layer is applied over the PCB surface, leaving openings for solder pads and vias. The solder mask protects the PCB from environmental factors and defines the soldering areas during assembly.
- Silkscreen Printing:Component designators, logos, and other markings are printed onto the PCB surface using silkscreen printing. This step helps in identifying components and provides assembly instructions.
- Testing and Inspection:Each fabricated PCB undergoes rigorous testing and inspection to ensure it meets the design specifications for electrical performance, dimensional accuracy, and reliability.
- Final Fabrication Steps:After testing, the PCBs are separated into individual units (depanelization) if necessary. They are then packaged and prepared for shipment to assembly facilities or end-users.
By following these steps with careful attention to detail and quality control, manufacturers can produce Megtron7 Materials PCBs that meet the stringent requirements of high-frequency applications, ensuring robust performance and reliability in electronic systems.
How do you manufacture a Megtron7 Materials PCB?
Manufacturing a Megtron7 Materials PCB involves a series of detailed steps to ensure the material’s high-performance characteristics are preserved throughout the process. Here’s a step-by-step outline of how Megtron7 PCBs are typically manufactured:
- Material Selection:Choose Megtron7 laminate sheets based on specific requirements such as dielectric constant, thermal reliability, and mechanical strength. Ensure the laminate sheets meet the thickness and copper weight specifications needed for the PCB design.
- Preparation of Substrate Materials:Cut Megtron7 laminate sheets to the required size for the PCB panels. This involves precise cutting to ensure uniformity across all panels.
- Drilling:Use precision drilling machines to create holes in the laminate sheets. These holes are for vias and through-hole components. For high-frequency applications, laser drilling may be used to achieve smaller and more precise holes.
- Copper Foil Lamination:Apply copper foil to both sides of the Megtron7 laminate sheets. This is typically done using a heated press to ensure proper adhesion of the copper foils to the laminate surface.
- Circuit Patterning (Etching):Apply a photoresist layer over the copper foils and expose it to UV light through a photomask that defines the circuit pattern. Develop and etch away the exposed copper using chemical etchants, leaving behind the desired copper traces and pads.
- Layer Alignment and Bonding:Align multiple layers of the prepared Megtron7 laminate with copper traces and bond them together using heat and pressure. This step forms the multilayer structure of the PCB, with each layer contributing to the overall circuit design.
- Via Formation:Drill holes for vias that connect different layers of the PCB. Ensure precise alignment and drill sizes according to the design specifications. Vias can be mechanically drilled or laser drilled for smaller diameters and higher precision.
- Copper Plating:Electroplate the walls of the drilled vias and the exposed copper surfaces with additional copper. This step enhances conductivity and ensures reliable electrical connections throughout the PCB.
- Surface Finishing:Apply a surface finish to protect the PCB and facilitate soldering during component assembly. Common surface finishes include HASL (Hot Air Solder Leveling), ENIG (Electroless Nickel Immersion Gold), and OSP (Organic Solderability Preservatives).
- Solder Mask Application:Apply a solder mask over the PCB surface, leaving openings for solder pads and vias. The solder mask protects the PCB from environmental factors and defines the soldering areas during assembly.
- Silkscreen Printing:Print component designators, logos, and other markings on the PCB surface using silkscreen printing. This helps in identifying components and provides assembly instructions.
- Testing and Inspection:Perform rigorous testing and inspection of each fabricated PCB to ensure it meets the design specifications for electrical performance, dimensional accuracy, and reliability. Tests may include electrical continuity tests, impedance testing, and visual inspection.
- Final Fabrication Steps: After testing and inspection, the PCBs are separated into individual units (depanelization) if necessary. They are then packaged and prepared for shipment to assembly facilities or end-users.
By following these manufacturing steps with precision and quality control measures, manufacturers can produce Megtron7 Materials PCBs that meet the demanding requirements of high-frequency and high-speed electronic applications, ensuring excellent performance and reliability in use.
How much should a Megtron7 Materials PCB cost?
The cost of Megtron7 Materials PCBs can vary widely depending on several factors, including the following:
- Board Size and Complexity: Larger PCBs or those with intricate designs requiring multiple layers, fine traces, and small vias will generally cost more due to increased material and manufacturing complexity.
- Material Thickness and Copper Weight: Different thicknesses of Megtron7 laminate and copper foils will affect costs. Thicker materials and heavier copper weights typically increase material costs.
- Quantity: Economies of scale apply in PCB manufacturing. Larger production runs often lower the per-unit cost due to optimized processes and bulk purchasing of materials.
- Technology and Processes: Advanced features such as laser drilling for fine vias, controlled impedance requirements, and specific surface finishes can add to the overall cost.
- Lead Time: Shorter lead times may incur rush charges or expedited shipping costs, impacting the total cost of the PCBs.
- Supplier and Location: PCB costs can vary by supplier and geographic location due to differences in labor costs, overheads, and market competitiveness.
To provide a rough estimate, typical pricing for Megtron7 Materials PCBs can range from a few dollars per square inch for standard designs with basic features to tens or even hundreds of dollars per square inch for highly specialized or complex designs. For precise pricing, it’s best to request quotes from multiple PCB manufacturers based on your specific design requirements and quantities needed. This allows you to compare costs and choose the best option based on quality, lead time, and pricing.
What is Megtron7 Materials PCB base material?
Megtron7 (M7) Materials PCBs are based on a specialized laminate material developed by Panasonic. This laminate comprises a combination of resin and glass fiber reinforcement, which are impregnated with epoxy resin to form a solid substrate. The key components of Megtron7 base material include:
- Resin System: The resin used in Megtron7 PCBs provides mechanical support and electrical insulation properties. It is chosen for its compatibility with high-frequency signals and its ability to maintain dimensional stability under varying environmental conditions.
- Glass Reinforcement:Glass fibers are embedded within the resin to enhance the laminate’s mechanical strength, stiffness, and thermal properties. The type and orientation of glass fibers used contribute to the laminate’s overall performance characteristics.
- Copper Foil: Thin sheets of copper are bonded to both sides of the Megtron7 laminate during the PCB manufacturing process. These copper foils serve as conductive pathways for electrical signals, providing connectivity between components and ensuring signal integrity.
- Additives and Fillers: Various additives and fillers may be included in the Megtron7 laminate formulation to achieve specific performance enhancements, such as improved thermal conductivity, reduced moisture absorption, or enhanced flame resistance.
Overall, Megtron7 base material is engineered to offer exceptional electrical properties, including low dielectric constant (εr) and low dissipation factor (Df), which are crucial for maintaining signal integrity in high-frequency applications. Its robust construction also supports reliable performance in environments where thermal stability and mechanical resilience are essential.
Which company makes Megtron7 Materials PCB?
Megtron7 (M7) is a high-performance PCB material developed by Panasonic. Panasonic, a globally renowned manufacturer of electronic devices and materials, is well-known for its advanced technology and innovative capabilities. Megtron7 PCB material features excellent electrical properties with low dielectric constant (εr) and low dissipation factor (Df), making it suitable for high-frequency applications such as communication equipment, networking devices, and other high-speed electronic devices.
Our company has the capability to produce Megtron7 Materials PCBs. We possess advanced PCB manufacturing equipment and a skilled technical team capable of manufacturing high-quality Megtron7 PCB boards according to customer design requirements and technical specifications. We are committed to ensuring the performance and reliability of each PCB through precise manufacturing processes and rigorous quality control. Our production process includes material selection, lamination, drilling, copper foil lamination, plating, surface treatment, printing, and final testing to ensure each Megtron7 PCB meets customer needs and expectations.
As a manufacturer, we focus on technological innovation and continuous improvement to meet the growing demand for high-performance PCBs in the rapidly evolving electronics industry. We not only offer competitive prices and high-quality products but also strive to build long-term and stable partnerships with customers, providing reliable electronic solutions for their innovative products.
Whether in technical support, production capacity, or quality assurance, we are committed to providing satisfactory service and support to our customers. Feel free to contact us for more information about Megtron7 Materials PCB manufacturing and other electronic solutions.
What are the 7 qualities of good customer service for Megtron7 Materials PCB?
Good customer service for Megtron7 Materials PCBs should embody several key qualities to ensure customer satisfaction and support. Here are seven important qualities:
- Technical Expertise: Customer service representatives should possess deep knowledge about Megtron7 PCBs, including their properties, applications, and manufacturing processes. This expertise helps them provide accurate information and technical assistance to customers.
- Responsiveness: Timely response to customer inquiries, whether through phone, email, or other channels, is crucial. Promptly addressing questions, concerns, and requests demonstrates commitment to customer support.
- Problem-Solving Skills: Effective customer service involves the ability to troubleshoot issues and resolve problems efficiently. This may include coordinating with technical teams or offering solutions to manufacturing or quality concerns related to Megtron7 PCBs.
- Clear Communication: Clear and concise communication is essential in customer service interactions. Providing information about product specifications, pricing, lead times, and order statuses in a transparent manner helps build trust and clarity.
- Customer Focus: Understanding and anticipating customer needs is vital. Tailoring solutions and recommendations based on customer requirements for Megtron7 PCBs fosters a customer-centric approach that enhances satisfaction.
- Reliability: Consistency in delivering accurate information, meeting commitments, and following through on promises builds confidence and reliability. This includes providing updates on orders, deliveries, and any potential issues promptly.
- Professionalism: Maintaining professionalism in all interactions, whether with customers, colleagues, or partners, reinforces trust and credibility. This includes respecting customer confidentiality, adhering to company policies, and handling sensitive information with discretion.
By embodying these qualities, customer service for Megtron7 Materials PCBs can effectively support customers throughout their product inquiries, orders, and technical assistance needs, contributing to overall customer satisfaction and loyalty.
FAQs about Megtron7 Materials PCB
What is Megtron7 (M7) PCB material?
Megtron7 is a high-performance PCB material developed by Panasonic. It offers excellent electrical properties with low dielectric constant (εr) and low dissipation factor (Df), making it ideal for high-frequency applications.
What are the key features of Megtron7 Materials PCBs?
Key features include high electrical reliability, low transmission loss, excellent thermal stability, and mechanical strength. These properties make Megtron7 suitable for applications requiring high-speed data transmission and reliability in harsh environments.
What are the typical applications of Megtron7 Materials PCBs?
Megtron7 PCBs are used in telecommunications equipment, networking devices, high-speed data communication systems, automotive electronics, and other applications requiring high-frequency performance and reliability.
How does Megtron7 compare to other PCB materials?
Compared to traditional PCB materials, Megtron7 offers superior electrical performance at high frequencies and maintains its properties over a wide temperature range. It is often chosen for demanding applications where signal integrity and reliability are critical.
What are the manufacturing capabilities for Megtron7 Materials PCBs?
Manufacturing capabilities include multilayer PCB fabrication, precise drilling for high-density vias, copper plating for signal integrity, various surface finishes (such as ENIG or HASL), and stringent quality control processes to ensure consistent performance.
Can Megtron7 PCBs be customized for specific applications?
Yes, Megtron7 PCBs can be customized to meet specific design requirements, such as layer stackup, controlled impedance requirements, special surface finishes, and dimensional specifications. Customization ensures optimal performance for diverse applications.
Where can I purchase Megtron7 Materials PCBs?
Megtron7 Materials PCBs are available through authorized distributors and directly from PCB manufacturers with expertise in high-performance materials. It’s recommended to choose suppliers with a proven track record in Megtron7 PCB fabrication and customer support.