Low CET PCB Manufacturing
Low CET PCB Manufacturing,Low CET PCB (Coefficient of Thermal Expansion Printed Circuit Board) features materials with minimal thermal expansion, ensuring stability in temperature fluctuations. These PCBs maintain precise alignment of components, crucial for high-frequency applications and reliability in harsh environments. Comprising specialized laminates and conductive traces, Low CET PCBs offer robust electrical connections and effective heat dissipation. They find applications in aerospace, automotive, and telecommunications industries where thermal stability is paramount. Low CET PCBs enable the development of electronic systems that can withstand extreme conditions while maintaining optimal performance, driving innovation in electronic device manufacturing for critical applications.
Low CET PCB adopts low chlorine epoxy technology, with lower levels of chlorine and bromine in the materials, reducing the risk of halogen release. It has excellent environmental performance and can be applied in fields with high environmental requirements, such as aerospace and medical equipment. Through strict manufacturing processes and quality control, the PCB ensures stability and reliability, complying with the latest environmental regulations.
What is Low CET PCB?
Low CET PCB stands for Low Chlorine Epoxy Technology Printed Circuit Board. This type of PCB is designed with materials that have reduced levels of chlorine and bromine, which are typically found in the epoxy resins used in traditional PCB manufacturing processes.
The use of low CET materials is particularly important in applications where the potential for outgassing or contamination can impact the performance or reliability of electronic components, such as in aerospace, medical, and military applications. By minimizing the levels of halogens in the PCB materials, low CET PCBs help reduce the risk of corrosion, electromigration, and other reliability issues that can arise in harsh environments.
Overall, low CET PCBs offer improved reliability, stability, and performance compared to conventional PCBs, especially in applications where stringent environmental or reliability requirements must be met.
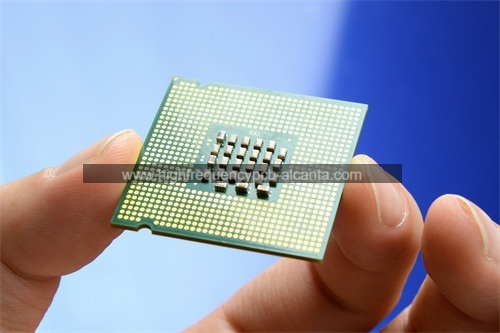
Low CET PCB Manufacturing
What are the Low CET PCB Design Guidelines?
The Low CET PCB design guidelines typically include the following recommendations:
- Material Selection: Choose epoxy resins and other substrate materials with low chlorine and bromine content. Prefer materials that comply with RoHS (Restriction of Hazardous Substances) and other environmental standards.
- Layer Stackup Design: When designing the PCB, minimize layers with higher halogen content. Optimize the PCB stackup to minimize potential halogen release.
- PCB Manufacturing Process: Select PCB manufacturing processes that minimize the risk of halogen contamination during production. This may involve using specific treatment methods and technologies such as controlled coating, plating, and cleaning processes.
- Soldering Methods: Prefer low-temperature soldering methods to reduce the risk of halogen release during soldering. Consider using lead-free solder.
- Testing and Validation: After PCB manufacturing is complete, conduct testing and validation to ensure that the PCB meets low CET requirements and does not exceed halogen content limits.
- Supply Chain Management: Collaborate with suppliers to ensure that the materials and components purchased meet low CET requirements and provide corresponding documentation.
By following these Low CET PCB design guidelines, PCB manufacturing processes, and material selection can be optimized to minimize the use and release of halogens, thereby enhancing the reliability and stability of the PCB.
What is the Low CET PCB Fabrication Process?
The translation of the text into English is as follows:
The Low CET PCB fabrication process is similar to traditional PCB manufacturing but emphasizes the use of materials and techniques that minimize the presence and release of halogens such as chlorine and bromine. Here’s an overview of the steps involved:
- Design: The PCB design process begins with the creation of a schematic and layout using design software. During this phase, designers should consider the selection of materials with low halogen content and optimize the PCB layout to minimize the use of high-halogen layers.
- Material Selection: Choose materials with low halogen content for the substrate, copper layers, solder mask, and surface finish. Low CET materials typically include halogen-free laminates and lead-free solder alloys.
- Preparation of Substrate: The chosen substrate material is prepared by cutting it into the required size and shape for the PCB. Surface preparation may involve cleaning and roughening to enhance adhesion.
- Layer Stackup: Stack the prepared substrate layers with copper foil layers according to the design specifications. Ensure that layers with higher halogen content are minimized in the stackup.
- Circuit Patterning: Use a process like photolithography to transfer the PCB design onto the copper layers. A photoresist is applied, exposed through a mask, developed, and then etched to remove unwanted copper, leaving behind the desired circuit pattern.
- Drilling: Drill holes for component mounting and interconnection between layers. Drilling should be performed with appropriate equipment to minimize contamination and ensure accuracy.
- Plating: Apply a thin layer of copper to the walls of the drilled holes through a process called electroplating. This forms the vias that facilitate electrical connections between layers.
- Surface Finish: Apply a surface finish to protect exposed copper and ensure solderability. Common surface finishes for Low CET PCBs include immersion silver, immersion tin, and OSP (Organic Solderability Preservatives).
- Solder Mask Application: Apply a solder mask to the PCB surface, leaving openings for component pads and vias. The solder mask protects the copper traces from oxidation and provides insulation.
- Component Assembly: Mount components onto the PCB using soldering techniques such as reflow soldering or wave soldering. Use low-temperature soldering methods to minimize halogen release during assembly.
- Testing and Inspection: Conduct electrical testing and visual inspection to ensure the functionality and quality of the assembled PCB. Test for adherence to low CET requirements and halogen content limits.
- Final Inspection and Packaging: Perform a final inspection to verify that the PCB meets specifications and standards. Once approved, package the PCBs for shipment to customers or assembly into end products.
Throughout the Low CET PCB fabrication process, careful attention should be paid to material selection, process control, and testing to ensure compliance with environmental regulations and to minimize halogen content and release.
How do you manufacture a Low CET PCB?
The Low CET PCB fabrication process refers to the manufacturing process of printed circuit boards (PCBs) using materials and methods that minimize the presence and release of halogens such as chlorine and bromine. Here’s a simplified outline of the Low CET PCB fabrication process:
- Design: The PCB design is created using specialized software, including schematic capture and PCB layout tools. Design considerations include selecting materials with low halogen content and optimizing the layout to minimize high-halogen layers.
- Material Selection: Choose PCB substrate materials with low halogen content, such as halogen-free laminates and lead-free solder alloys. Ensure all materials comply with relevant environmental regulations.
- Preparation of Substrate: The substrate material (typically fiberglass-reinforced epoxy) is prepared by cutting it to size and cleaning its surface to remove any contaminants.
- Copper Cladding: Copper foil is laminated onto the substrate to create the conductive layers of the PCB. The foil is etched to remove excess copper and form the desired circuit pattern.
- Drilling: Holes are drilled into the PCB for through-hole components and vias. Special care is taken to minimize contamination during drilling.
- Plating: A thin layer of copper is electroplated onto the walls of the drilled holes to provide conductivity between layers and facilitate component connections.
- Surface Finish: The exposed copper surfaces are coated with a surface finish to protect against oxidation and ensure solderability. Common surface finishes include immersion silver, immersion tin, and organic solderability preservatives (OSP).
- Solder Mask Application: A solder mask is applied over the PCB surface, leaving openings for component pads and vias. The solder mask protects copper traces from oxidation and provides insulation.
- Silkscreen Printing: Component designators, logos, and other markings are printed onto the PCB using a silkscreening process.
- Component Assembly: Electronic components are mounted onto the PCB using automated pick-and-place machines. The components are soldered onto the board using reflow soldering or wave soldering techniques.
- Testing and Inspection: The assembled PCBs undergo electrical testing to ensure proper functionality and adherence to design specifications. Visual inspection is also performed to check for defects.
- Final Inspection and Packaging: After passing quality control checks, the PCBs are inspected one final time and then packaged for shipment to customers or further assembly into electronic devices.
Throughout the Low CET PCB fabrication process, strict adherence to low-halogen materials and manufacturing techniques is essential to minimize halogen content and ensure compliance with environmental regulations.
How much should a Low CET PCB cost?
The cost of a Low CET PCB depends on several factors, including but not limited to:
- Specifications and Size: The size, layers, thickness, and other specifications of the PCB directly impact the cost. Larger and more complex PCBs typically cost more.
- Materials: The type and quality of materials used will affect the cost. Low CET materials might incur slightly higher costs, but the difference in cost is usually not significant.
- Manufacturing Process: Different manufacturing processes and requirements can affect the cost. For example, if special surface treatments or precise drilling techniques are needed, the cost may increase.
- Quantity: Generally, PCBs produced in larger quantities have a lower unit cost. Bulk orders may receive discounts.
- Delivery Time: Urgent orders may require expedited production, which could incur additional costs.
Therefore, it’s not possible to provide a specific price range because each project has different requirements and circumstances. It’s advisable to request quotes from multiple PCB manufacturers based on specific needs and requirements.
What is Low CET PCB base material?
Low CET PCB base material typically refers to the substrate material used in the fabrication of printed circuit boards (PCBs) that comply with Low Chlorine Epoxy Technology (CET) standards. This base material is chosen specifically for its low content of halogens such as chlorine and bromine, which helps reduce the risk of halogen-related issues such as corrosion and outgassing in electronic applications.
Some common base materials used for Low CET PCBs include:
- Halogen-Free Laminates: These laminates are formulated without the use of halogen-containing materials, such as halogen-free FR-4 (Flame Retardant-4). They provide good electrical properties and mechanical strength while minimizing halogen content.
- Polyimide (PI) Laminates: Polyimide substrates are known for their excellent thermal stability and resistance to harsh environments. Low-CET versions of polyimide laminates are available to meet stringent environmental requirements.
- Ceramic Substrates: Ceramic materials offer high thermal conductivity, excellent dimensional stability, and resistance to temperature extremes. They are suitable for applications requiring high reliability and performance.
- PTFE-Based Materials: Polytetrafluoroethylene (PTFE) substrates, such as Rogers Corporation’s RT/duroid®, offer low dielectric loss, high-frequency performance, and resistance to moisture and chemicals.
- Non-Halogen FR-4: Some manufacturers produce FR-4 laminates with reduced halogen content compared to traditional FR-4 materials. These non-halogen FR-4 laminates still provide good electrical and mechanical properties while minimizing halogen content.
When selecting a base material for Low CET PCBs, it’s essential to consider factors such as environmental regulations, electrical performance, mechanical properties, and thermal stability to ensure the PCB meets the required specifications and standards while minimizing halogen content.
Which company makes Low CET PCB? (Note: Our company can produce Low CET PCB)
Many companies are involved in the manufacturing of Low CET PCBs, including PCB manufacturers, electronic equipment manufacturers, and material suppliers worldwide. For instance, companies such as Foxconn, Renesas Electronics, and Taiwan’s Unimicron have capabilities and technical expertise in this field.
As a professional PCB manufacturer, our company has advanced manufacturing equipment and extensive experience to provide high-quality Low CET PCBs. We employ advanced manufacturing processes and stringent quality control procedures to ensure that our PCBs meet the strictest environmental standards and the requirements of our customers.
Our engineering team possesses specialized technical knowledge and experience to customize Low CET PCBs according to the specific needs and specifications of our customers. We offer a variety of options, including different substrate materials, surface treatments, and lamination methods, to meet the requirements of various applications.
We are committed to continuously improving our technical capabilities and production capacity to meet the growing demands of our customers. We understand the importance of environmental consciousness and strictly control halogen content during the production process to ensure that our Low CET PCBs comply with the latest environmental regulations and standards.
In summary, our company is capable of producing high-quality Low CET PCBs and is willing to collaborate with customers to promote environmental awareness and sustainable development. We are dedicated to providing our customers with superior products and services to meet their needs and achieve mutual growth.
What are the 7 qualities of good customer service?
Good customer service is characterized by several key qualities that contribute to a positive experience for customers. Here are seven essential qualities of good customer service:
- Responsiveness: Good customer service involves promptly addressing customer inquiries, concerns, and requests. Being responsive means acknowledging customers’ needs in a timely manner and providing assistance or information promptly.
- Empathy: Empathy involves understanding and acknowledging customers’ feelings, concerns, and perspectives. Good customer service representatives empathize with customers, showing compassion and understanding to build rapport and trust.
- Communication skills: Effective communication is crucial in customer service. Good customer service representatives communicate clearly, actively listen to customers’ needs, and provide information or assistance in a concise and understandable manner.
- Problem-solving abilities: Good customer service involves resolving customer issues and complaints effectively. Customer service representatives should be equipped with problem-solving skills to address challenges efficiently and find satisfactory solutions for customers.
- Professionalism: Professionalism encompasses various aspects of behavior, including courtesy, respect, and reliability. Good customer service representatives maintain a professional demeanor, treat customers with respect, and adhere to company policies and standards.
- Product knowledge: Good customer service requires a thorough understanding of the products or services offered by the company. Customer service representatives should be knowledgeable about the company’s offerings to provide accurate information and assistance to customers.
- Adaptability: Good customer service involves being adaptable and flexible to meet the diverse needs and preferences of customers. Customer service representatives should be able to adjust their approach and solutions based on individual customer situations and requirements.
By embodying these qualities, organizations can deliver exceptional customer service experiences that foster customer satisfaction, loyalty, and positive brand reputation.
FAQs
What is Low CET PCB?
Low CET PCB stands for Low Chlorine Epoxy Technology Printed Circuit Board. It uses materials with reduced levels of chlorine and bromine, minimizing the risk of halogen release.
What are the benefits of Low CET PCBs?
Low CET PCBs offer improved environmental performance by reducing halogen content, making them suitable for applications with strict environmental regulations. They also provide enhanced reliability and stability.
Which industries commonly use Low CET PCBs?
Low CET PCBs are commonly used in industries such as aerospace, medical devices, military, and telecommunications, where environmental regulations and reliability are critical.
How does Low CET PCB differ from traditional PCBs?
Low CET PCBs use materials with lower halogen content compared to traditional PCBs. This reduces the risk of halogen-related issues such as corrosion and outgassing, making them more environmentally friendly.
Are Low CET PCBs more expensive?
The cost of Low CET PCBs can vary depending on factors such as size, complexity, and quantity. While they may incur slightly higher costs due to specialized materials, the difference is usually not significant compared to the benefits they offer.
Are Low CET PCBs compatible with standard manufacturing processes?
Yes, Low CET PCBs can be manufactured using standard PCB manufacturing processes with minor adjustments to accommodate the specific materials and requirements.
How can I ensure that my PCBs meet Low CET requirements?
To ensure compliance with Low CET requirements, work with reputable PCB manufacturers who specialize in producing Low CET PCBs. Additionally, specify your environmental requirements clearly during the design and manufacturing process.