LED Substrate Material Manufacturer
LED Substrate Material Manufacturer,LED Substrate Materials are specialized components designed to support and enhance the performance of LED (Light Emitting Diode) devices. These materials are chosen for their excellent thermal conductivity, which is crucial for dissipating heat generated by LEDs and preventing overheating. Commonly used substrates include aluminum, copper, and advanced ceramics, each offering different thermal and electrical properties. Aluminum substrates provide good thermal management and cost-effectiveness, while copper substrates offer superior heat dissipation and electrical conductivity. Advanced ceramics, such as aluminum nitride, deliver exceptional thermal performance and durability. The choice of substrate material directly impacts the efficiency, brightness, and lifespan of LED lighting solutions.
What is LED Substrate Material?
LED substrate material is a crucial component in the design and manufacture of Light Emitting Diodes (LEDs). It serves as the base upon which the LED components are mounted and plays a significant role in the thermal management and electrical performance of the LED.
The substrate material provides mechanical support and helps in the efficient dissipation of heat generated during operation. This thermal management is vital to maintain LED performance and longevity. Common substrate materials include Aluminum Nitride (AlN), Silicon Carbide (SiC), and various types of metal-core materials like Aluminum (Al) and Copper (Cu).
Aluminum-based substrates, such as Aluminum PCB (Al PCB), are widely used due to their excellent thermal conductivity and cost-effectiveness. For high-performance applications, materials like Copper-based substrates are preferred for their superior thermal management properties. Additionally, advanced substrates like Silicon Carbide offer high thermal conductivity and electrical insulation, making them suitable for high-power LED applications.
Choosing the appropriate substrate material depends on factors such as thermal requirements, electrical conductivity, and cost considerations, all of which impact the overall efficiency and reliability of the LED.
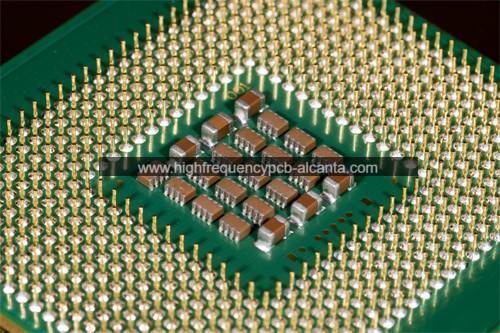
LED Substrate Material Manufacturer
What are the LED Substrate Material Design Guidelines?
LED substrate material design guidelines are essential for ensuring optimal performance, durability, and cost-effectiveness in LED applications. Here are key considerations:
- Thermal Management: Efficient heat dissipation is crucial for LED longevity and performance. Select substrates with high thermal conductivity, such as Aluminum Nitride (AlN) or Copper, to manage heat effectively and prevent thermal degradation of the LED components.
- Electrical Insulation: Ensure the substrate provides adequate electrical insulation to prevent short circuits and interference. Materials like Aluminum PCB and Silicon Carbide offer good electrical insulation properties.
- Thermal Expansion Compatibility: Match the thermal expansion coefficient of the substrate material with that of the LED chip to avoid mechanical stress and delamination during temperature fluctuations.
- Mechanical Strength: The substrate must have sufficient mechanical strength to support the LED components and withstand any handling or mounting stresses. Consider the substrate’s durability and resistance to mechanical damage.
- Cost vs. Performance: Balance the cost of the substrate material with its performance characteristics. While high-performance materials like Copper or Silicon Carbide offer superior thermal management, they may be more expensive compared to Aluminum-based substrates.
- Fabrication Compatibility: Ensure the substrate material is compatible with the manufacturing processes used in LED production. The material should be easy to process and adhere well to soldering and bonding techniques.
- Environmental Considerations: Choose substrates that can withstand environmental conditions such as humidity, temperature extremes, and exposure to chemicals, especially for applications in harsh environments.
By adhering to these guidelines, designers can enhance the reliability, efficiency, and overall performance of LED systems.
What is the LED Substrate Material Fabrication Process?
The fabrication process for LED substrate materials involves several key steps to ensure high-quality performance and reliability of the final product. Here’s a general overview of the process:
- Material Selection: Choose the appropriate substrate material based on thermal conductivity, electrical insulation, and mechanical strength requirements. Common choices include Aluminum Nitride (AlN), Copper, and Aluminum-based materials.
- Material Preparation: Obtain the substrate material in the desired form, such as sheets or wafers. The material may need to be cut to size or processed to meet specific dimensions and thickness requirements.
- Surface Cleaning: Clean the substrate surface to remove any contaminants, oils, or residues that could affect adhesion or performance. This is typically done using ultrasonic cleaning, chemical solvents, or other cleaning methods.
- Patterning: Apply a photoresist layer to the substrate, then expose it to ultraviolet (UV) light through a photomask that defines the desired patterns. This process creates a pattern on the substrate surface, which will be used for further processing.
- Etching: Use chemical or plasma etching techniques to remove unwanted material from the substrate, following the pattern defined by the photoresist. This step creates the necessary features or structures on the substrate.
- Metallization: Deposit metal layers onto the substrate to create conductive pathways. Techniques such as sputtering, evaporation, or electroplating are used to apply metal coatings, typically including copper or aluminum.
- Bonding: Attach the LED chip to the substrate using methods such as die bonding, which may involve soldering or adhesive bonding. Ensure strong adhesion to support the LED chip and facilitate electrical connections.
- Encapsulation: Apply a protective layer over the LED chip and substrate to safeguard against environmental factors and mechanical damage. Encapsulation materials may include epoxy resins or silicones.
- Testing and Quality Control: Conduct tests to verify the performance, thermal management, and electrical properties of the LED substrate. Inspect for defects and ensure that the substrate meets all design specifications and quality standards.
- Cutting and Packaging: Cut the substrate into final sizes and shapes as needed for the end application. Package the completed substrates to protect them during shipping and handling.
Each step in the fabrication process is crucial for ensuring that the LED substrates meet the necessary performance and reliability standards for their intended applications.
How Do You Manufacture LED Substrate Material?
Manufacturing LED substrate material involves a series of precise and controlled steps to ensure high quality and performance. Here’s a detailed overview of the process:
- Material Procurement: Select and acquire the raw material for the substrate. Common materials include Aluminum Nitride (AlN), Copper, and Aluminum. The material is often purchased in bulk as sheets, wafers, or plates.
- Material Cutting and Shaping: Cut the raw material into the desired size and shape. This step involves precision cutting to meet specific dimensions and tolerances required for the final substrate. Techniques like sawing, laser cutting, or waterjet cutting may be used.
- Surface Preparation: Clean the substrate material thoroughly to remove contaminants, dust, or residues. Methods include ultrasonic cleaning, chemical washes, and drying processes to ensure a clean surface for further processing.
- Thermal Treatment: If necessary, perform thermal treatments or annealing to enhance the material’s properties, such as improving thermal conductivity or relieving internal stresses. This step is crucial for materials like Aluminum Nitride, which benefits from controlled heat treatments.
- Patterning and Lithography: Apply a photoresist layer to the substrate and use photolithography to define patterns. This involves exposing the photoresist to UV light through a mask to create a pattern on the substrate’s surface. The exposed areas are then developed to reveal the pattern for subsequent processing.
- Etching: Etch away the unwanted material from the substrate according to the pattern created in the previous step. This can be done using chemical etching or plasma etching techniques, which precisely remove material to form the necessary features.
- Metallization: Deposit metal layers onto the substrate to form conductive pathways. This is achieved through methods such as sputtering, evaporation, or electroplating. The deposited metal is typically copper or aluminum, depending on the application requirements.
- Bonding and Assembly: Attach the LED chips to the substrate using die bonding techniques. This process involves placing the LED chips onto the substrate and securing them with solder or adhesive. This step ensures a strong mechanical and electrical connection between the chip and the substrate.
- Encapsulation: Apply an encapsulation layer to protect the LED chip and substrate from environmental damage and mechanical stress. Materials used for encapsulation include epoxy resins or silicones, which provide both protection and optical enhancement.
- Testing and Inspection: Perform rigorous testing and quality control checks to ensure that the LED substrates meet performance specifications. Tests include thermal conductivity measurements, electrical testing, and visual inspections to detect any defects or inconsistencies.
- Cutting and Packaging: Finally, cut the substrates into the required final sizes and package them for shipment. Proper packaging ensures that the substrates are protected during transport and handling.
This manufacturing process ensures that LED substrates are produced with high precision and quality, meeting the demands of various LED applications.
How Much Should LED Substrate Material Cost?
The cost of LED substrate materials varies widely depending on several factors, including material type, size, thickness, and production volume. Here are key considerations that influence the cost:
- Material Type: The choice of substrate material significantly impacts cost. For example, Aluminum-based substrates (such as Aluminum PCBs) are generally more cost-effective compared to high-performance materials like Copper or Silicon Carbide. Copper substrates, known for their excellent thermal conductivity, tend to be more expensive than Aluminum-based alternatives. Silicon Carbide substrates, used in high-power applications, can be among the most costly options.
- Size and Thickness: Larger substrates or those requiring specific thicknesses will generally be more expensive due to increased material usage and processing requirements. Custom sizes and thicknesses can also add to the cost.
- Production Volume:High-volume production can reduce the cost per unit due to economies of scale. Lower volumes or custom orders may result in higher per-unit costs.
- Fabrication Complexity:The complexity of the fabrication process affects cost. Substrates requiring intricate patterning, high precision, or additional processing steps will typically be more expensive. Advanced materials and processes, such as those used for high-performance LEDs, will also drive up costs.
- Quality and Specifications: Higher-quality substrates with stricter performance specifications, such as enhanced thermal conductivity or electrical insulation, will command higher prices. Quality control and testing requirements can also influence the final cost.
- Supplier and Market Conditions: Prices can vary depending on the supplier and market conditions, including material availability and demand. Changes in raw material costs or supply chain disruptions can affect pricing.
In general, LED substrate materials can range from a few dollars per unit for standard Aluminum-based substrates to several hundred dollars per unit for high-performance materials like Silicon Carbide. For precise pricing, it’s advisable to contact suppliers with specific requirements and request quotes based on your needs.
What is LED Substrate Material Base Material?
LED (Light Emitting Diode) substrate materials provide structural support for LED chips and can significantly impact their thermal, optical performance, and lifespan. The main types of substrate materials include the following:
- Sapphire:Sapphire is a common LED substrate material, especially in blue and white LEDs. It has high transparency, hardness, and good thermal conductivity, which aids in heat dissipation, though it has poor electrical conductivity, necessitating an additional conductive layer. Sapphire substrates are typically used in GaN (Gallium Nitride)-based LEDs.
- Silicon:Silicon substrates offer the advantages of low cost and compatibility with existing semiconductor manufacturing processes, making them suitable for mass production. However, silicon’s thermal conductivity and heat dissipation capabilities are inferior to those of sapphire and silicon carbide (SiC). Silicon-based LEDs are suitable for low-power applications but may face thermal limitations in high-power applications.
- Silicon Carbide (SiC):SiC substrates have excellent thermal conductivity and high hardness, making them suitable for high-power LED applications. The primary advantage of SiC substrates is their thermal expansion coefficient, which closely matches that of GaN, reducing defects caused by thermal stress. However, the high cost of SiC substrates limits their widespread use.
- Aluminum Nitride (AlN):AlN substrates boast very high thermal conductivity and excellent thermal expansion coefficient matching, making them ideal for high-power and high-frequency applications. AlN substrates can effectively dissipate heat, extending the lifespan of LEDs, but their high cost and complex manufacturing process can be limiting factors.
- Metal Substrates:Metal substrates, such as aluminum and copper, are known for their excellent thermal conductivity and are commonly used in high-power and high-brightness LED applications. Metal substrates typically include an insulating layer to prevent electrical short circuits. Aluminum-based substrates (IMS) achieve good heat dissipation and electrical insulation through an insulating layer and copper circuits.
- Glass Substrates:Glass substrates are typically used in low-cost LED applications. They offer high transparency and low manufacturing costs but have lower thermal conductivity, making them unsuitable for high-power LEDs.
Selecting the appropriate substrate material is crucial for optimizing LED performance and lifespan. High-power LEDs require excellent heat dissipation, making silicon carbide, aluminum nitride, and metal substrates the preferred choices. For low-power and cost-sensitive applications, silicon and glass substrates may be more economical. The thermal expansion coefficient matching between different substrate materials also affects the reliability and performance of LED chips.
In conclusion, the choice of LED substrate material needs to balance factors such as thermal conductivity, thermal expansion coefficient, electrical performance, and cost to meet the specific application requirements.
Which Company Makes LED Substrate Material?
LED substrate materials are produced by several internationally renowned companies, including Mitsubishi Chemical, NGK Insulators from Japan, Cree from the USA, and LG Innotek from South Korea. These companies utilize advanced material science and manufacturing processes to produce various types of LED substrate materials, catering to different LED application needs.
Our company also manufactures LED substrate materials. As a specialized electronic materials manufacturer, we have advanced R&D teams and production facilities that can provide a range of materials, such as sapphire, silicon, silicon carbide, aluminum nitride, and metal substrates. We are committed to continuous innovation and optimization of our products to ensure excellent thermal conductivity, mechanical strength, and long-term stability.
Our LED substrate materials are widely used in the production of various LED chips, including high-power LEDs and high-brightness LEDs. Our products not only meet international standards and industry regulations but can also be customized to meet specific customer requirements, ensuring optimal performance and cost-effectiveness. We understand the importance of LED technology for energy efficiency and environmental protection, and we are dedicated to providing reliable material solutions that help our customers stand out in a competitive market.
Through ongoing technological innovation and high-quality manufacturing, our LED substrate materials have gained widespread application and recognition globally. We will continue to contribute to the development of the LED industry by providing high-quality materials and excellent customer service, working together with our clients to advance industry progress and innovation.
What are the 7 Qualities of Good Customer Service?
Good customer service is crucial for building strong relationships with customers and ensuring their satisfaction. Here are seven key qualities that define excellent customer service:
- Responsiveness:Good customer service is characterized by prompt and efficient responses to customer inquiries, concerns, or complaints. This involves answering phone calls, emails, and messages quickly, and addressing issues in a timely manner to avoid prolonged frustration.
- Empathy:Showing empathy involves understanding and sharing the feelings of the customer. It means listening actively to their concerns, acknowledging their problems, and expressing genuine care and concern for their situation. Empathetic service helps build trust and rapport with customers.
- Effective Communication:Clear, concise, and polite communication is essential. This includes using simple language, avoiding jargon, and ensuring that information is conveyed accurately. Good communication also involves active listening, confirming understanding, and providing straightforward solutions.
- Knowledgeability:Service representatives should have a deep understanding of the products or services offered. They should be able to provide accurate information, answer questions confidently, and resolve issues effectively. Knowledgeable staff can enhance the customer experience by offering reliable support and advice.
- Patience:Patience is crucial, especially when dealing with difficult or frustrated customers. Taking the time to listen and understand their concerns without rushing or showing irritation helps to de-escalate situations and provides a more positive customer experience.
- Professionalism:Maintaining a professional demeanor involves being courteous, respectful, and maintaining a positive attitude. Professionalism also includes following company policies and procedures while interacting with customers in a manner that reflects well on the organization.
- Follow-Up:Good customer service includes following up with customers after their issue has been addressed. This might involve checking in to ensure their problem has been resolved to their satisfaction or offering additional assistance if needed. Follow-up demonstrates a commitment to ongoing customer satisfaction and builds long-term loyalty.
Incorporating these qualities into customer service practices can significantly enhance customer satisfaction and loyalty, leading to positive word-of-mouth and a stronger reputation for the business.
FAQs about LED Substrate Material
What is an LED substrate?
An LED substrate is a material that provides structural support for an LED chip. It affects the chip’s thermal management, light output, and overall performance.
What materials are commonly used for LED substrates?
Common LED substrate materials include sapphire, silicon, silicon carbide, aluminum nitride, and metal substrates (like aluminum or copper).
Why is thermal conductivity important in LED substrates?
Thermal conductivity is crucial because it helps dissipate the heat generated by the LED chip, which improves performance and extends the lifespan of the LED.
What is the role of sapphire in LED substrates?
Sapphire is often used for blue and white LEDs due to its high transparency, hardness, and good thermal conductivity.
Why might silicon substrates be used for LEDs?
Silicon substrates are cost-effective and compatible with existing semiconductor manufacturing processes, making them suitable for low-power LEDs.
What advantages do metal substrates offer for high-power LEDs?
Metal substrates, such as aluminum and copper, provide excellent thermal conductivity, which is essential for high-power LED applications to manage heat effectively.
How does aluminum nitride (AlN) benefit LED performance?
AlN offers very high thermal conductivity and good thermal expansion coefficient matching, making it ideal for high-power and high-frequency LED applications.