LED Ceramic Substrate Manufacturer
LED Ceramic Substrate Manufacturer,LED ceramic substrates are crucial components of LED devices, responsible for supporting and managing the performance of LED chips. Typically made from high thermal conductivity ceramic materials such as aluminum nitride (AlN) or alumina (Al2O3), they exhibit excellent heat dissipation and electrical insulation properties. Designed to efficiently dissipate heat and prevent circuit shorts, LED ceramic substrates also provide mechanical support. These substrates often incorporate thermal vias to facilitate heat transfer from LED chips to heat sinks. LED ceramic substrates boast excellent durability and environmental adaptability, suitable for a wide range of applications including automotive lighting, displays, general illumination, and industrial lighting. Through optimized design and manufacturing, LED ceramic substrates enhance the performance and reliability of LED devices, driving the advancement of LED technology to meet growing market demands.
What is an LED Ceramic Substrate?
An LED ceramic substrate is a type of material used in the construction of light-emitting diodes (LEDs). LEDs are semiconductor devices that emit light when an electric current passes through them. The ceramic substrate serves as the base upon which the LED chips are mounted and provides mechanical support, thermal management, and electrical insulation.
Ceramic substrates offer several advantages for LED applications compared to traditional materials like metal or organic substrates. They have excellent thermal conductivity, which helps dissipate heat generated by the LED, thereby improving the LED’s efficiency and lifespan. Ceramic substrates also provide good electrical insulation properties, which are crucial for preventing short circuits and ensuring the proper functioning of the LED.
Additionally, ceramic substrates are durable and resistant to environmental factors such as moisture and corrosion, making them well-suited for use in various lighting applications, including automotive lighting, displays, and general illumination.
Overall, LED ceramic substrates play a vital role in enhancing the performance, reliability, and longevity of LED devices.
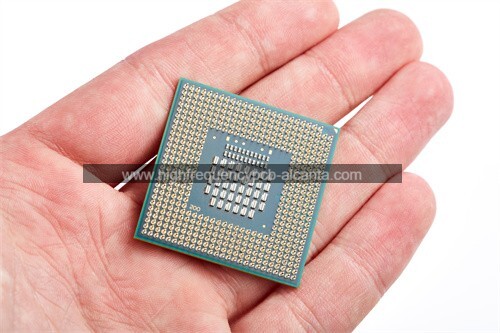
LED Ceramic Substrate Manufacturer
What are the LED Ceramic Substrate Design Guidelines?
LED ceramic substrate design guidelines encompass various factors to ensure optimal performance and reliability of LED devices. Some key design considerations include:
- Thermal Management: Efficient heat dissipation is critical for LED operation. Design the substrate with adequate thermal conductivity to dissipate heat generated by the LED chips effectively. This may involve incorporating features such as thermal vias or metal traces to facilitate heat transfer to a heat sink.
- Electrical Insulation: Ensure the substrate provides sufficient electrical insulation to prevent short circuits and electrical failures. Choose materials with high dielectric strength and carefully design the layout to minimize the risk of electrical leakage.
- Mechanical Stability: The substrate should offer mechanical stability to support the LED chips and withstand mechanical stress during handling and operation. Consider factors such as substrate thickness, material strength, and mounting methods to ensure structural integrity.
- Compatibility with LED Chips: Select substrate materials and surface treatments that are compatible with the LED chip technology being used. Different LED chip types (e.g., flip-chip, surface-mount) may require specific substrate characteristics for optimal performance.
- Environmental Durability: Design the substrate to withstand environmental factors such as temperature fluctuations, humidity, and chemical exposure. Choose materials with appropriate resistance to corrosion and degradation over time.
- Electrical Routing and Interconnects: Design the substrate layout to accommodate the electrical routing and interconnects necessary for connecting the LED chips to power sources and control circuits. Ensure proper spacing, trace widths, and via placements to minimize resistance and impedance issues.
- Manufacturability: Consider manufacturability factors such as ease of fabrication, assembly, and testing during the substrate design process. Optimize the design for cost-effective production while maintaining performance and reliability requirements.
- Optical Performance: While primarily a function of the LED chip itself, substrate design can indirectly impact optical performance through factors such as thermal management and light scattering. Ensure that substrate design does not compromise the intended optical characteristics of the LED device.
By following these guidelines, designers can develop LED ceramic substrates that meet the requirements for high-performance, reliable LED lighting applications.
What is the LED Ceramic Substrate Fabrication Process?
The fabrication process for LED ceramic substrates typically involves several steps to create the base material with the desired properties and features for mounting LED chips. Here’s a general overview of the process:
- Material Selection: Choose a suitable ceramic material for the substrate based on factors such as thermal conductivity, electrical insulation, mechanical strength, and compatibility with LED chip technology. Common ceramic materials used include aluminum nitride (AlN) and alumina (Al2O3).
- Substrate Preparation: The ceramic material is initially in the form of a raw substrate, which may come in sheets or blocks. The substrate surface is cleaned and prepared for subsequent processing steps to ensure proper adhesion and performance.
- Laser Machining or Cutting: Laser machining or cutting techniques are used to shape the ceramic substrate into the desired size and dimensions. This process may involve precision cutting to create individual substrate units or panels suitable for LED chip mounting.
- Surface Treatment: Surface treatment processes such as polishing, grinding, or chemical etching may be employed to smoothen the substrate surface and remove any imperfections that could affect LED chip adhesion or performance.
- Metallization: Metallization is performed to create conductive pathways on the substrate surface for electrical connections. Thin layers of metal such as copper, silver, or gold are deposited onto the substrate through techniques like sputtering, evaporation, or screen printing.
- Patterned Film Deposition: In some cases, patterned thin films or layers may be deposited onto the substrate surface to enhance specific properties such as thermal conductivity or electrical insulation. This step may involve techniques like physical vapor deposition (PVD) or chemical vapor deposition (CVD).
- Through-Hole Drilling: If thermal vias or electrical vias are required for heat dissipation or interconnects, through-hole drilling is performed to create holes in the substrate. These holes may be filled with conductive material to form vias that connect different layers of the substrate.
- Quality Control and Testing: Throughout the fabrication process, quality control measures are implemented to ensure that the substrates meet the desired specifications for thermal performance, electrical insulation, mechanical stability, and other key parameters. Testing may include visual inspection, dimensional measurements, and electrical testing.
- Packaging and Shipping: Once fabricated and tested, the LED ceramic substrates are packaged appropriately to protect them during transportation and storage. They are then shipped to LED module or luminaire manufacturers for further assembly into LED lighting products.
By following these fabrication steps with precision and quality control, manufacturers can produce LED ceramic substrates that provide the necessary support and performance for high-quality LED lighting applications.
How do you manufacture an LED Ceramic Substrate?
Manufacturing an LED ceramic substrate involves a series of steps aimed at creating a robust, efficient, and reliable base for mounting LED chips. Here’s an overview of the typical manufacturing process:
- Material Selection: Choose the appropriate ceramic material for the substrate, considering factors such as thermal conductivity, electrical insulation, mechanical strength, and compatibility with LED chip technology. Common materials include aluminum nitride (AlN) and alumina (Al2O3).
- Substrate Formation: The ceramic material is processed into a substrate form. This can involve techniques such as pressing, casting, or extrusion to create sheets, blocks, or panels of the desired size and thickness.
- Shaping and Cutting: Use machining techniques like laser cutting or diamond sawing to shape the ceramic substrate into the required dimensions and configurations. This step may involve cutting individual substrate units or creating arrays for batch processing.
- Surface Treatment: Treat the substrate surface to ensure cleanliness and proper adhesion for subsequent processing steps. Surface treatments may include cleaning, polishing, or chemical etching to remove contaminants and roughness.
- Metallization: Apply conductive metal layers onto the substrate surface to create electrical pathways and bonding pads for LED chip attachment. Metallization can be achieved through techniques such as physical vapor deposition (PVD), chemical vapor deposition (CVD), or screen printing.
- Die Attachment: Place and bond the LED chips onto the metallized substrate surface using die bonding techniques such as epoxy or solder bonding. Ensure precise alignment and adequate thermal interface for efficient heat dissipation.
- Wire Bonding: Connect the LED chips to the substrate’s electrical pathways using wire bonding techniques. This involves using fine wires (usually gold or aluminum) to make electrical connections between the LED chip’s electrodes and the substrate’s bonding pads.
- Encapsulation or Coating: Apply encapsulation materials or coatings to protect the LED chips and wire bonds from environmental factors such as moisture, dust, and mechanical stress. Encapsulation can be done using materials like epoxy resin or silicone.
- Testing and Quality Control: Perform rigorous testing to verify the performance, reliability, and functionality of the LED ceramic substrates. This may include electrical testing, thermal testing, visual inspection, and reliability testing to ensure compliance with specifications and standards.
- Packaging and Shipping: Package the finished LED ceramic substrates securely for transportation and storage. Ensure appropriate labeling and documentation to track the substrates’ specifications and manufacturing details.
By following these manufacturing steps with precision, quality control, and attention to detail, manufacturers can produce high-quality LED ceramic substrates suitable for a wide range of lighting applications.
How much should an LED Ceramic Substrate cost?
The cost of an LED ceramic substrate can vary depending on several factors, including the material used, size, complexity of design, manufacturing processes involved, and quantity ordered. Here are some factors that can influence the cost:
- Material Cost: The type of ceramic material used for the substrate can significantly impact the cost. For example, aluminum nitride (AlN) substrates tend to be more expensive than alumina (Al2O3) substrates due to their superior thermal conductivity properties.
- Size and Thickness: Larger and thicker substrates require more raw material and may involve additional processing steps, which can contribute to higher costs.
- Complexity of Design: Substrates with intricate designs, features such as thermal vias, or specific surface treatments may require more advanced manufacturing processes, leading to higher costs.
- Manufacturing Processes: The manufacturing processes involved, such as metallization, die attachment, wire bonding, and encapsulation, can vary in complexity and cost. Substrates that require more labor-intensive processes or specialized equipment may be more expensive.
- Quantity Ordered: Economies of scale typically apply, meaning that larger quantities ordered can result in lower per-unit costs due to efficiencies in manufacturing and bulk purchasing of materials.
- Quality and Reliability: High-quality substrates that undergo rigorous testing and quality control measures may command a higher price due to their reliability and performance.
- Supplier and Market Factors: Pricing can also be influenced by the supplier’s pricing strategy, market demand, competition, and geographic location.
As a rough estimate, LED ceramic substrates can range in cost from a few dollars to several tens of dollars per unit, depending on the factors mentioned above. For precise pricing information, it’s best to contact manufacturers or suppliers directly and provide detailed specifications for the desired substrate.
What is LED Ceramic Substrate base material?
The base material for LED ceramic substrates is typically a ceramic compound chosen for its properties that suit the requirements of LED applications. Two common ceramic materials used for LED substrates are aluminum nitride (AlN) and alumina (Al2O3).
- Aluminum Nitride (AlN): AlN is favored for its excellent thermal conductivity, which helps dissipate heat generated by the LED chips. It also has good electrical insulation properties, making it suitable for high-power LED applications. AlN substrates are often preferred for applications where thermal management is critical, such as high-brightness LEDs used in automotive lighting or high-power LED modules.
- Alumina (Al2O3):Alumina substrates, also known as aluminum oxide, are widely used for LED applications due to their cost-effectiveness and versatility. While not as thermally conductive as AlN, alumina substrates still offer good thermal stability and electrical insulation properties. They are suitable for a wide range of LED lighting applications, including general illumination, displays, and consumer electronics.
Both AlN and alumina substrates can be engineered with specific characteristics such as surface roughness, thermal conductivity, dielectric strength, and dimensional stability to meet the requirements of LED device designs. Additionally, manufacturers may apply various surface treatments or coatings to further enhance the substrate’s performance and compatibility with LED chip technologies.
Which companies make LED Ceramic Substrates?
LED ceramic substrates are one of the key components in LED devices, and many companies are dedicated to producing high-quality LED ceramic substrates. Some major LED ceramic substrate manufacturers include CeramTec, Kyocera, Maruwa, and others. These companies have rich experience and expertise in the design, manufacturing, and supply of LED ceramic substrates, providing reliable solutions to the LED industry.
As for our company, as a specialized enterprise in advanced material processing, we have the capability of independently developing and producing LED ceramic substrates. With advanced production equipment and a skilled technical team, we can customize LED ceramic substrates of various specifications and requirements according to customer needs.
Our LED ceramic substrates feature the following characteristics and advantages:
- High Thermal Conductivity: We use high-quality ceramic materials such as aluminum nitride (AlN) or alumina (Al2O3) with excellent thermal conductivity, aiding effective heat dissipation for LED chips, thus enhancing the performance and reliability of LED devices.
- Excellent Electrical Insulation: Our LED ceramic substrates possess excellent electrical insulation properties, effectively preventing circuit short-circuits and faults, ensuring the safe operation of LED devices.
- Precision Processing: With advanced processing technology and equipment, we can achieve precision processing and production of LED ceramic substrates, ensuring product quality and stability.
- Customization Services: We can customize LED ceramic substrates of various specifications, sizes, and shapes according to customer requirements, catering to different application scenarios.
- Strict Quality Control: We strictly implement a quality management system, conducting strict screening and testing of raw materials to ensure product stability and reliability.
In summary, our company has rich experience and professional knowledge in the design, manufacturing, and supply of LED ceramic substrates, giving us a competitive advantage in the market. We will continue to strive to improve product quality and technical level, providing customers with higher quality LED ceramic substrate products and services.
What are the 7 qualities of good customer service?
Good customer service is characterized by several key qualities that contribute to positive interactions and relationships between businesses and their customers. Here are seven essential qualities:
- Responsiveness: Good customer service involves promptly addressing customer inquiries, concerns, and requests. Being responsive demonstrates attentiveness to customer needs and a commitment to resolving issues in a timely manner.
- Empathy: Empathy involves understanding and empathizing with the customer’s perspective and emotions. Good customer service representatives listen actively, show genuine concern for customer issues, and strive to put themselves in the customer’s shoes to provide appropriate assistance and support.
- Professionalism: Professionalism entails maintaining a courteous, respectful, and polite demeanor in all customer interactions. Good customer service representatives adhere to company policies and standards while effectively representing the organization’s values and brand image.
- Knowledgeability: Knowledgeability refers to having a thorough understanding of the products or services offered by the business, as well as relevant policies, procedures, and industry trends. Good customer service representatives possess the expertise to answer customer questions accurately, provide helpful recommendations, and troubleshoot issues effectively.
- Problem-Solving Skills: Good customer service involves the ability to identify and address customer problems and concerns effectively. Customer service representatives should be resourceful, proactive, and creative in finding solutions to meet customer needs and resolve issues satisfactorily.
- Consistency: Consistency is crucial for building trust and credibility with customers. Good customer service should be consistently high-quality across all channels and touchpoints, ensuring a positive and reliable experience for customers every time they interact with the business.
- Personalization: Personalization involves tailoring interactions and solutions to meet the specific needs and preferences of individual customers. Good customer service representatives take the time to understand each customer’s unique situation, preferences, and history with the business, allowing them to deliver more personalized and relevant assistance.
By embodying these qualities, businesses can cultivate strong customer relationships, foster loyalty, and differentiate themselves in the competitive marketplace.
FAQs
What materials are used for LED ceramic substrates?
Common materials for LED ceramic substrates include aluminum nitride (AlN) and alumina (Al2O3). These materials have high thermal conductivity and electrical insulation properties.
How are LED ceramic substrates manufactured?
The manufacturing process typically involves material selection, substrate preparation, shaping, metallization, die attachment, wire bonding, encapsulation, and quality control.
What factors should be considered when designing LED ceramic substrates?
Design considerations include thermal management, electrical insulation, mechanical stability, compatibility with LED chips, environmental durability, electrical routing, manufacturability, and optical performance.
What are thermal vias in LED ceramic substrates?
Thermal vias are holes drilled through the substrate to improve heat dissipation by allowing heat to flow more efficiently from the LED chips to a heat sink or thermal management system.
Can LED ceramic substrates be customized?
Yes, LED ceramic substrates can be customized to meet specific requirements such as size, shape, thermal properties, electrical characteristics, and surface treatments.
What applications are LED ceramic substrates used for?
LED ceramic substrates are used in various applications, including automotive lighting, displays, general illumination, consumer electronics, and industrial lighting.
How do LED ceramic substrates compare to other substrate materials?
LED ceramic substrates generally offer superior thermal performance compared to traditional materials like metals or organic substrates. They provide better heat dissipation and electrical insulation, leading to improved LED performance and reliability.