What is LCC Package Substrate?
LCC Package Substrate Manufacturer,LCC (Leadless Chip Carrier) package substrate is a compact semiconductor packaging solution featuring a flat surface with conductive pads for chip attachment, eliminating traditional leads. LCC substrates offer efficient heat dissipation, reliable electrical connections, and mechanical stability, making them suitable for high-density applications. Widely used in consumer electronics, automotive, and industrial sectors, LCC package substrates ensure optimal performance in space-constrained environments. Their precise construction and compatibility with various assembly processes make LCC substrates essential for developing compact and reliable electronic devices with superior performance and longevity.
LCC (Leadframe Chip Carrier) package substrate is a type of packaging technology used in integrated circuits (ICs) and semiconductor devices. The substrate serves as a platform for mounting and interconnecting the chip (integrated circuit) with the rest of the electronic system.
In an LCC package, the chip is mounted on a leadframe, which is a thin metal frame with leads (metal pins or terminals) extending outward from it. The chip is bonded to the leadframe using wire bonding or flip-chip bonding techniques. The leadframe provides mechanical support and electrical connections for the chip.
The substrate material used in LCC packages is typically a ceramic or organic material such as epoxy resin. The substrate serves as a base for mounting the leadframe and provides insulation and electrical routing for the chip’s connections.
LCC packages are commonly used in a variety of electronic devices such as microcontrollers, memory chips, and other integrated circuits where moderate to high pin counts and good thermal performance are required. They offer a good balance of performance, cost, and reliability for many applications.
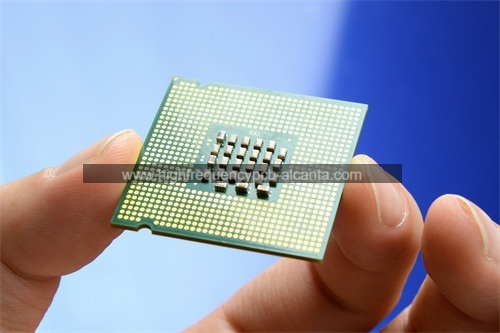
LCC Package Substrate Manufacturer
What are the Functions of LCC Package Substrate?
The LCC (Leadframe Chip Carrier) package substrate serves several important functions in semiconductor packaging:
Mechanical Support: The substrate provides mechanical support for the integrated circuit (IC) chip and the leadframe. It ensures that the chip remains securely in place during handling, assembly, and operation of the electronic device.
Electrical Interconnection: The substrate facilitates the electrical connections between the IC chip and the external circuitry of the electronic device. It contains conductive traces or wiring patterns that route signals, power, and ground connections from the chip to the external leads or terminals of the package.
Thermal Management: The substrate helps to dissipate heat generated by the IC chip during operation. It may include features such as heat sinks, thermal vias, or metal layers that enhance the thermal performance of the package by conducting heat away from the chip and distributing it across the package.
Protection and Isolation: The substrate provides a protective barrier for the IC chip against environmental factors such as moisture, dust, and mechanical shocks. It also electrically isolates the chip and its connections from the surrounding environment to prevent short circuits and other electrical failures.
Signal Integrity: The substrate design plays a critical role in maintaining signal integrity by minimizing signal losses, reflections, and crosstalk. It ensures that the electrical signals transmitted between the chip and the external circuitry remain stable and reliable.
Overall, the LCC package substrate is essential for ensuring the proper operation, reliability, and performance of semiconductor devices in various electronic applications.
What are the Different Types of LCC Package Substrate?
LCC (Leadframe Chip Carrier) package substrates can come in various types, each with its own characteristics and advantages. Some common types include:
Ceramic Substrates: These substrates are made of ceramic materials such as alumina (Al2O3) or aluminum nitride (AlN). Ceramic substrates offer excellent thermal conductivity, mechanical strength, and reliability. They are well-suited for high-power applications and devices that require superior thermal performance.
Organic Substrates: Organic substrates are typically made of epoxy resin or other organic materials. They are lightweight, cost-effective, and offer good electrical insulation properties. Organic substrates are commonly used in consumer electronics and other applications where cost and weight are important considerations.
Metal Substrates: Metal substrates are made of metals such as copper or aluminum. They offer excellent thermal conductivity and can efficiently dissipate heat generated by the IC chip. Metal substrates are commonly used in high-power LED applications and other devices where thermal management is critical.
Flex Substrates: Flex substrates, also known as flexible substrates, are made of flexible materials such as polyimide or polyester. They offer flexibility and can be bent or folded to fit into tight spaces or conform to curved surfaces. Flex substrates are commonly used in applications where space constraints or flexibility are important considerations, such as wearable devices and automotive electronics.
Ceramic-Polymer Hybrids: These substrates combine the thermal and mechanical properties of ceramic materials with the flexibility and cost-effectiveness of organic materials. They offer a good balance of performance and cost and are suitable for a wide range of applications.
These are some of the common types of LCC package substrates available in the semiconductor industry. The choice of substrate type depends on factors such as the specific requirements of the application, cost considerations, thermal management needs, and performance requirements.
How does LCC Package Substrate Relate to IC Packaging?
LCC (Leadframe Chip Carrier) package substrate is a crucial component within the broader context of integrated circuit (IC) packaging. IC packaging encompasses the processes and materials used to encapsulate and protect semiconductor chips, enabling their integration into electronic devices and systems. The LCC package substrate specifically plays a fundamental role in IC packaging by providing a platform for mounting and interconnecting the IC chip with the external circuitry.
Here’s how LCC package substrate relates to IC packaging:
Mounting the IC Chip: The LCC package substrate serves as the foundation on which the IC chip is mounted. The chip is typically bonded to the substrate using wire bonding or flip-chip bonding techniques, ensuring a secure mechanical connection.
Interconnecting the IC Chip: The substrate contains conductive traces or wiring patterns that facilitate the electrical connections between the IC chip and the external leads or terminals of the package. These connections allow signals, power, and ground to be transmitted between the chip and the rest of the electronic system.
Thermal Management: Thermal management is a critical aspect of IC packaging, especially for high-performance chips that generate significant heat during operation. The LCC package substrate helps dissipate heat away from the IC chip, contributing to its overall thermal performance and reliability.
Protecting the IC Chip: The substrate provides a protective barrier for the IC chip, shielding it from environmental factors such as moisture, dust, and mechanical shocks. This protection helps ensure the long-term reliability and functionality of the semiconductor device.
Signal Integrity: The design of the substrate plays a crucial role in maintaining signal integrity by minimizing signal losses, reflections, and crosstalk. A well-designed substrate helps ensure that the electrical signals transmitted between the IC chip and the external circuitry remain stable and reliable.
Overall, the LCC package substrate is an essential component of IC packaging, contributing to the mechanical, electrical, thermal, and reliability aspects of semiconductor devices. It enables the integration of IC chips into various electronic applications, ranging from consumer electronics to industrial equipment and automotive systems.
What are the Differences Between LCC Package Substrate and PCB?
LCC (Leadframe Chip Carrier) package substrate and PCB (Printed Circuit Board) are both essential components in electronics, but they serve different purposes and have distinct characteristics. Here are the key differences between them:
Function and Purpose:
LCC Package Substrate: The primary function of the LCC package substrate is to provide a platform for mounting and interconnecting the integrated circuit (IC) chip within a semiconductor package. It offers mechanical support, electrical connections, thermal management, and protection for the IC chip.
PCB: A PCB, on the other hand, serves as a foundation for mounting and interconnecting various electronic components such as ICs, resistors, capacitors, and connectors. It provides electrical connections between these components, enabling the functioning of electronic circuits.
Construction:
LCC Package Substrate: LCC substrates are typically made of materials such as ceramic, organic substrates (epoxy resin), or metal, depending on the specific requirements of the application. They are designed to be compact and optimized for mounting IC chips.
PCB: PCBs are usually made of a non-conductive substrate material, such as fiberglass-reinforced epoxy resin (FR-4), with copper traces etched onto the surface to create electrical pathways. They may also include additional layers for signal routing and component mounting.
Complexity and Integration:
LCC Package Substrate: LCC substrates are generally simpler in design and functionality compared to PCBs. They are tailored specifically for housing and connecting IC chips within semiconductor packages.
PCB: PCBs can vary significantly in complexity, depending on the circuit design and the number of components integrated onto the board. They can incorporate multiple layers, intricate routing, and various components to form complete electronic systems.
Application:
LCC Package Substrate: LCC substrates are primarily used in semiconductor packaging for ICs, where they provide a compact and efficient means of mounting and connecting chips within packages.
PCB: PCBs are used in a wide range of electronic devices and systems, including computers, smartphones, medical devices, automotive electronics, and industrial equipment. They serve as the backbone of electronic circuits and enable the integration of various components into functional systems.
In summary, while both LCC package substrates and PCBs are critical components in electronics, they serve different functions and are optimized for different applications. LCC substrates focus on housing and connecting IC chips within semiconductor packages, whereas PCBs provide the foundation for building complete electronic circuits and systems.
What are the Main Structures and Production Technologies of LCC Package Substrate?
The main structures and production technologies of LCC (Leadframe Chip Carrier) package substrates can vary depending on the specific requirements of the application and the materials used. However, here are some common structures and production technologies:
Leadframe Structure:
LCC packages typically utilize a leadframe structure as the foundation for mounting the IC chip and providing electrical connections. The leadframe is a thin metal frame with leads (metal pins or terminals) extending outward from it.
The leadframe can be made of various metals such as copper, copper alloy, or iron-nickel alloy. It provides mechanical support and electrical pathways for the IC chip.
Substrate Material:
The substrate material serves as the base for mounting the leadframe and providing insulation and electrical routing for the IC chip’s connections.
Common substrate materials include ceramic (such as alumina or aluminum nitride), organic substrates (such as epoxy resin), metal substrates (such as copper or aluminum), or hybrid materials combining ceramic and polymer components.
Die Attach and Wire Bonding:
The IC chip is typically attached to the leadframe using a die attach process, where a conductive adhesive or solder is used to bond the chip to the leadframe.
Wire bonding is a common method used to connect the bond pads on the IC chip to the leads on the leadframe. Thin wires made of gold, aluminum, or copper are bonded to the chip and leadframe using ultrasonic or thermosonic bonding techniques.
Molding Compound:
After die attach and wire bonding, the IC chip and leadframe are encapsulated in a molding compound to protect them from environmental factors and provide additional mechanical support.
The molding compound is typically a thermosetting plastic material such as epoxy resin. It is injected into a mold cavity, where it cures and hardens around the chip and leadframe, forming the final package structure.
Trimming and Forming:
Once the molding compound has cured, the LCC packages undergo trimming and forming processes to remove excess material and shape the leads to their final configuration.
Trimming involves cutting excess molding compound and leadframe material, while forming involves bending or shaping the leads to the desired shape for soldering onto a printed circuit board (PCB) or other electronic assembly.
Testing and Inspection:
The LCC packages undergo various testing and inspection processes to ensure they meet quality and reliability standards. This may include electrical testing, visual inspection, and reliability testing to verify the functionality and performance of the packaged IC chips.
Overall, the production of LCC package substrates involves several key steps, including leadframe assembly, die attach and wire bonding, encapsulation in molding compound, trimming and forming, and testing and inspection. These processes are essential for manufacturing high-quality LCC packages used in various electronic applications.
Frequently Asked Questions (FAQs):
What is an LCC package substrate?
An LCC package substrate is a component used in semiconductor packaging that serves as a platform for mounting and interconnecting integrated circuit (IC) chips within a semiconductor package. It provides mechanical support, electrical connections, thermal management, and protection for the IC chip.
What materials are used in LCC package substrates?
LCC package substrates can be made of various materials, including ceramic (such as alumina or aluminum nitride), organic substrates (such as epoxy resin), metal substrates (such as copper or aluminum), or hybrid materials combining ceramic and polymer components.
What are the main production technologies used in manufacturing LCC package substrates?
The main production technologies for LCC package substrates include leadframe assembly, die attach and wire bonding, encapsulation in molding compound, trimming and forming, and testing and inspection.
What are the advantages of LCC package substrates?
LCC package substrates offer several advantages, including compact size, good thermal performance, reliable electrical connections, and cost-effectiveness. They are commonly used in a wide range of electronic devices and applications.
What are the applications of LCC package substrates?
LCC package substrates are used in various electronic applications, including microcontrollers, memory chips, sensors, automotive electronics, industrial equipment, consumer electronics, and more.
How do LCC package substrates differ from PCBs?
LCC package substrates are specifically designed for semiconductor packaging, providing a platform for mounting and interconnecting IC chips within semiconductor packages. PCBs, on the other hand, serve as the foundation for building complete electronic circuits and systems, incorporating various components and providing electrical connections between them.
What factors should be considered when selecting an LCC package substrate?
Factors to consider when selecting an LCC package substrate include the specific requirements of the application, such as thermal performance, electrical connectivity, size constraints, reliability standards, and cost considerations.
Conclusion
In conclusion, LCC (Leadframe Chip Carrier) package substrates play a crucial role in semiconductor packaging, providing a platform for mounting and interconnecting integrated circuit (IC) chips within semiconductor packages. They offer mechanical support, electrical connections, thermal management, and protection for the IC chip, contributing to the functionality, reliability, and performance of electronic devices and systems.
LCC package substrates are manufactured using various production technologies, including leadframe assembly, die attach and wire bonding, encapsulation in molding compound, trimming and forming, and testing and inspection. These processes ensure the quality and reliability of the packaged IC chips.
With their compact size, good thermal performance, reliable electrical connections, and cost-effectiveness, LCC package substrates find applications in a wide range of electronic devices and systems, including microcontrollers, memory chips, sensors, automotive electronics, industrial equipment, and consumer electronics.
When selecting an LCC package substrate, factors such as the specific requirements of the application, thermal performance, electrical connectivity, size constraints, reliability standards, and cost considerations should be taken into account.
Overall, LCC package substrates continue to be an essential component in semiconductor packaging, enabling the integration of IC chips into various electronic applications and contributing to the advancement of technology.