ISOLA 370HR PCB Manufacturer
ISOLA 370HR PCB Manufacturer,ISOLA 370HR PCBs represent the pinnacle of high-performance laminate materials in the realm of printed circuit boards (PCBs). Renowned for their exceptional electrical properties, reliability, and durability, ISOLA 370HR PCBs offer a cutting-edge solution for critical electronic applications. With a low dielectric constant, minimal dissipation factor, and robust thermal stability, these PCBs ensure consistent signal integrity and performance even in the most demanding environments. Whether deployed in telecommunications infrastructure, aerospace systems, networking devices, or high-end computing hardware, ISOLA 370HR PCBs deliver unparalleled quality and performance. Their ability to facilitate high-speed digital and radio frequency signal transmission makes them indispensable in modern electronics. From design to fabrication, ISOLA 370HR PCBs undergo meticulous engineering and stringent quality control measures to guarantee optimal functionality and reliability. As a cornerstone of advanced electronic systems, ISOLA 370HR PCBs embody innovation, precision, and excellence, driving the forefront of technological advancement.
What is ISOLA 370HR PCB?
ISOLA 370HR is a type of high-performance laminate material used in the manufacture of printed circuit boards (PCBs). PCBs made with ISOLA 370HR are known for their excellent electrical performance, reliability, and durability. The “370HR” designation typically refers to the specific grade or version of the material.
ISOLA 370HR PCBs are often chosen for applications that require high-speed digital and RF (radio frequency) signal transmission, such as in telecommunications equipment, networking devices, aerospace systems, and high-end computing hardware. The material offers properties such as low dielectric constant, low dissipation factor, and good thermal stability, making it suitable for demanding electronic applications.
Overall, ISOLA 370HR PCBs are valued for their consistent quality and performance in demanding electronic applications where reliability and signal integrity are critical.
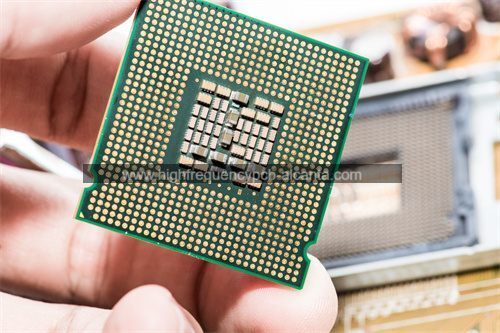
ISOLA 370HR PCB Manufacturer
What are the ISOLA 370HR PCB Design Guidelines?
Design guidelines for ISOLA 370HR PCBs typically encompass several key considerations to ensure optimal performance and reliability. While specific guidelines may vary based on the intended application and manufacturing processes, here are some common recommendations:
- Material Selection: Choose ISOLA 370HR laminate material suitable for your application, considering factors such as desired electrical performance, thermal stability, and compatibility with manufacturing processes.
- Layer Stackup Design: Design the layer stackup with attention to signal integrity, impedance control, and thermal management requirements. Ensure proper layer ordering and signal/power plane distribution to minimize signal interference and optimize signal transmission.
- Trace Routing and Signal Integrity: Follow best practices for trace routing to maintain signal integrity and minimize signal degradation. Consider factors such as trace length, width, and spacing, as well as impedance matching techniques for high-speed signals.
- Copper Weight and Plating Thickness: Specify appropriate copper weight and plating thickness based on the current carrying capacity, thermal requirements, and manufacturing capabilities. Ensure uniform copper distribution to minimize impedance variations and ensure consistent electrical performance.
- Component Placement: Optimize component placement to minimize signal path lengths, reduce parasitic effects, and facilitate efficient heat dissipation. Consider thermal management strategies to prevent localized heating and ensure component reliability.
- Drill and Hole Sizes: Specify drill and hole sizes compatible with ISOLA 370HR material properties and manufacturing processes. Ensure adequate annular ring sizes and drill-to-copper clearances to maintain mechanical strength and reliability.
- Annular Ring and Pad Design: Design annular rings and pads with appropriate dimensions to ensure reliable solder joints and electrical connections. Follow industry standards and manufacturer recommendations for pad sizes, pad shapes, and solder mask clearances.
- Thermal Management: Incorporate thermal vias, heat sinks, and other thermal management techniques as needed to dissipate heat efficiently and prevent thermal stress-related issues. Consider factors such as power dissipation, ambient temperature, and airflow conditions.
- Design for Manufacturability (DFM): Design the PCB layout with manufacturability in mind, considering factors such as panelization, fiducial marker placement, and assembly process requirements. Consult with PCB fabrication and assembly vendors to address any manufacturing constraints early in the design process.
- Testing and Validation: Plan for comprehensive testing and validation of the PCB design to ensure compliance with electrical performance requirements, reliability standards, and regulatory specifications. Perform signal integrity analysis, thermal simulations, and prototype testing as needed to verify the design’s functionality and performance.
By following these guidelines and collaborating closely with PCB fabrication and assembly partners, designers can create ISOLA 370HR PCBs that meet the demanding performance, reliability, and quality standards of modern electronic applications.
What is the ISOLA 370HR PCB Fabrication Process?
The fabrication process for ISOLA 370HR PCBs involves several steps, including material preparation, imaging, etching, drilling, plating, solder mask application, and surface finishing. Here’s an overview of the typical fabrication process:
- Material Preparation: The process begins with the selection of ISOLA 370HR laminate material in the desired thickness and copper foil configuration. The material is inspected for defects, and any necessary surface treatment is applied to ensure proper adhesion and compatibility with subsequent processing steps.
- Imaging: A layer of photosensitive material, called photoresist, is applied to the copper-clad laminate. The PCB design is then transferred onto the photoresist using a photographic process, typically involving exposure to ultraviolet (UV) light through a photomask. This step defines the pattern for the circuit traces and features on the PCB.
- Etching: After imaging, the PCB is immersed in an etchant solution that removes the exposed copper, leaving behind the desired circuit pattern. The etching process is carefully controlled to ensure precise feature dimensions and proper trace geometries.
- Drilling: Precision holes are drilled into the PCB for component mounting and interconnection purposes. High-speed drilling machines equipped with carbide or diamond-coated drill bits are used to achieve accurate hole sizes and positions according to the PCB design specifications.
- Plating: The drilled holes are plated with a conductive metal, typically copper, to provide electrical connectivity between layers and facilitate component soldering. This process, known as through-hole plating, involves the deposition of a thin layer of metal through a chemical or electrochemical process.
- Solder Mask Application: A layer of solder mask is applied to the surface of the PCB to protect the copper traces from oxidation and facilitate soldering during assembly. The solder mask is typically applied using a screen printing or curtain coating process and cured under heat and UV light to harden the material.
- Silkscreen Printing: Identifying information, such as component designators, logos, and reference indicators, are printed onto the PCB surface using a silkscreen printing process. This step helps assembly technicians identify components and ensure correct orientation during assembly.
- Surface Finishing: Surface finishing processes, such as electroless nickel immersion gold (ENIG), hot air solder leveling (HASL), or immersion silver, are applied to the exposed copper surfaces to improve solderability, prevent oxidation, and enhance electrical performance.
- Routing and Profiling: After surface finishing, the individual PCBs are separated from the manufacturing panel using routing or scoring techniques. Precision milling machines or routers are used to cut along the predefined board outline, creating the final shape of the PCB.
- Final Inspection:The finished PCBs undergo thorough visual inspection, dimensional measurement, electrical testing, and quality assurance checks to ensure compliance with design specifications, industry standards, and customer requirements.
By following these fabrication steps with precision and attention to detail, manufacturers can produce high-quality ISOLA 370HR PCBs that meet the demanding performance, reliability, and quality standards of modern electronic applications.
How do you manufacture an ISOLA 370HR PCB?
Manufacturing an ISOLA 370HR PCB involves a series of steps that include material preparation, layer stackup design, imaging, etching, drilling, plating, solder mask application, surface finishing, and final inspection. Here’s a detailed outline of the manufacturing process:
- Material Selection: Choose ISOLA 370HR laminate material suitable for the application requirements, considering factors such as dielectric properties, thermal performance, and compatibility with manufacturing processes.
- Layer Stackup Design: Design the PCB layer stackup according to the circuit requirements, considering factors such as signal integrity, impedance control, and thermal management. Determine the number of layers, copper thickness, and material configuration based on the design specifications.
- Preparation of Laminate Material: Cut the ISOLA 370HR laminate sheets to the required size and clean the surfaces to remove any contaminants. Prepare the copper foil layers with appropriate surface treatments to ensure good adhesion and solderability.
- Prepreg Lamination: If the PCB design includes multiple layers, stack the prepared laminate materials and prepreg layers according to the layer stackup design. Apply heat and pressure to laminate the layers together, forming a single composite structure.
- Drilling: Precision drill holes in the laminated stack for through-hole vias and component mounting holes. Use computer-controlled drilling machines with carbide or diamond-coated drill bits to achieve accurate hole sizes and positions.
- Image Transfer: Apply a layer of photoresist material to the surface of the PCB and transfer the PCB design onto the photoresist using a photomask and UV light exposure. This step defines the circuit pattern on the outer layers of the PCB.
- Etching: Remove the unwanted copper from the outer layers of the PCB using an etching process. The exposed copper areas are dissolved, leaving behind the desired circuit traces and features.
- Plating: Plate the drilled holes with a conductive metal, typically copper, to provide electrical connectivity between layers and facilitate component soldering. This process, known as through-hole plating, may involve electroless or electrolytic plating techniques.
- Solder Mask Application: Apply a layer of solder mask material to the surface of the PCB to protect the copper traces and pads from oxidation and facilitate soldering during assembly. Use screen printing or curtain coating methods to apply the solder mask, followed by curing under heat and UV light.
- Silkscreen Printing: Print identifying information, such as component designators, logos, and reference indicators, onto the PCB surface using a silkscreen printing process. This step helps assembly technicians identify components and ensure correct orientation during assembly.
- Surface Finishing: Apply surface finishing processes, such as electroless nickel immersion gold (ENIG), hot air solder leveling (HASL), or immersion silver, to the exposed copper surfaces to improve solderability, prevent oxidation, and enhance electrical performance.
- Routing and Profiling: Cut the individual PCBs from the manufacturing panel using routing or scoring techniques. Precision milling machines or routers are used to cut along the predefined board outline, creating the final shape of the PCB.
- Final Inspection: Conduct thorough visual inspection, dimensional measurement, electrical testing, and quality assurance checks on the finished PCBs to ensure compliance with design specifications, industry standards, and customer requirements.
By following these manufacturing steps with precision and attention to detail, PCB manufacturers can produce high-quality ISOLA 370HR PCBs suitable for a wide range of electronic applications.
How much should an ISOLA 370HR PCB cost?
The cost of an ISOLA 370HR PCB can vary widely depending on several factors, including the following:
- Board Size: Larger PCBs typically cost more due to the increased material and manufacturing time required.
- Number of Layers: The number of layers in the PCB affects the complexity of the manufacturing process and thus impacts the cost.
- Copper Weight: Thicker copper layers increase material costs and may require additional processing steps, contributing to higher overall costs.
- Surface Finish: Different surface finish options, such as ENIG (Electroless Nickel Immersion Gold), HASL (Hot Air Solder Leveling), or immersion silver, have different costs associated with them.
- Trace Width and Spacing: Narrower trace widths and smaller spacing requirements may increase manufacturing complexity and cost.
- Hole Size and Density: Smaller drill sizes and higher hole densities can increase fabrication costs due to the need for precision drilling and plating processes.
- Quality and Quantity: Higher quality standards and larger order quantities may result in volume discounts but can also increase the upfront cost.
- Lead Time: Rush orders or expedited manufacturing may incur additional fees.
It’s important to request quotes from PCB manufacturers based on your specific design requirements and desired quantity. Prices can vary significantly between suppliers, so it’s a good idea to shop around and compare quotes to ensure you’re getting the best value for your needs. Additionally, factors such as customer service, lead times, and quality control should also be considered when selecting a PCB manufacturer.
What is ISOLA 370HR PCB base material?
The base material of ISOLA 370HR PCB is a high-performance laminate. It is composed of layers of fiberglass fabric impregnated with epoxy resin. The fiberglass provides mechanical strength and dimensional stability to the PCB, while the epoxy resin serves as a bonding agent and dielectric material between the layers.
The specific composition of the base material may vary depending on the grade or version of ISOLA 370HR being used. However, in general, ISOLA 370HR PCB base material typically consists of:
- Fiberglass Reinforcement: The fiberglass reinforcement provides the structural integrity and mechanical strength of the PCB. It is typically made of woven glass cloth or non-woven fiberglass materials.
- Epoxy Resin: The epoxy resin acts as a matrix material that bonds the fiberglass layers together and provides electrical insulation between conductive traces. It also contributes to the overall rigidity and dimensional stability of the PCB.
- Fillers and Additives: Various fillers and additives may be incorporated into the epoxy resin formulation to enhance specific properties of the base material, such as thermal conductivity, flame retardancy, or resistance to environmental factors like moisture and chemicals.
ISOLA 370HR PCB base material is engineered to meet stringent performance requirements for high-speed digital and RF (radio frequency) applications. It offers properties such as low dielectric constant, low dissipation factor, and excellent thermal stability, making it suitable for demanding electronic applications where reliability and signal integrity are critical.
Which company makes ISOLA 370HR PCBs?
ISOLA 370HR PCBs are manufactured by ISOLA Group. ISOLA Group is a global leader in high-performance composite materials and electronic materials. They offer a wide range of printed circuit board (PCB) substrate materials, including ISOLA 370HR, which is one of their high-performance laminate materials.
ISOLA 370HR PCBs are widely used in various applications, including telecommunications equipment, networking devices, aerospace systems, and high-end computing hardware. These PCBs are renowned for their excellent electrical performance, reliability, and durability, capable of meeting the requirements of high-speed digital and radio frequency signal transmission.
Our company is capable of producing ISOLA 370HR PCBs. We have advanced manufacturing equipment and a skilled technical team capable of producing high-quality PCBs according to customer requirements and specifications. We prioritize quality control and adhere to strict manufacturing processes to ensure our products meet industry standards and customer expectations. Whether it’s small batch orders or large-scale production, we can provide efficient and reliable services to meet customer needs.
Our manufacturing process covers the entire process from raw material procurement to final product delivery, ensuring precise control and monitoring at every step. We also have a professional quality inspection team responsible for rigorous inspection and testing of finished products to ensure the highest quality standards.
As your trusted partner, we are committed to providing high-quality ISOLA 370HR PCBs to meet your needs and achieve mutual success. We are willing to establish long-term partnerships with customers, grow together, and share achievements.
What are the 7 qualities of good customer service?
Good customer service is essential for building strong relationships with customers and ensuring their satisfaction. Here are seven qualities that characterize excellent customer service:
- Responsiveness: A key aspect of good customer service is being responsive to customer inquiries, concerns, and requests in a timely manner. Customers appreciate prompt assistance and expect their needs to be addressed promptly.
- Empathy: Empathy involves understanding and showing compassion for the customer’s situation or problem. Good customer service representatives listen actively, acknowledge the customer’s feelings, and demonstrate empathy in their interactions.
- Knowledgeability: Customers expect service representatives to be knowledgeable about the products or services offered by the company. Having a deep understanding of the company’s offerings enables representatives to provide accurate information, answer questions, and offer solutions effectively.
- Professionalism: Professionalism encompasses behaviors such as politeness, respectfulness, and professionalism in communication. Good customer service representatives maintain a positive attitude, remain calm under pressure, and treat customers with courtesy and professionalism at all times.
- Adaptability: Every customer is unique, and their needs and preferences may vary. Good customer service involves being adaptable and flexible in finding solutions that meet the individual needs of each customer. Service representatives should be able to tailor their approach to accommodate different situations and customer requirements.
- Proactivity: Good customer service goes beyond reactive problem-solving; it involves being proactive in anticipating and addressing customer needs. Service representatives should actively seek opportunities to provide assistance, offer relevant recommendations, and address potential issues before they escalate.
- Consistency: Consistency is crucial for building trust and reliability with customers. Good customer service entails delivering consistent experiences across all customer touchpoints, whether it’s in-person interactions, phone calls, emails, or online chats. Consistency in service quality, communication, and follow-up helps foster long-term customer loyalty.
By embodying these qualities, companies can provide exceptional customer service experiences that not only meet but exceed customer expectations, leading to increased satisfaction, loyalty, and advocacy.
FAQs
What is ISOLA 370HR PCB?
ISOLA 370HR PCB is a type of high-performance laminate material used in the manufacture of printed circuit boards (PCBs). It offers excellent electrical performance, reliability, and durability, making it suitable for high-speed digital and RF (radio frequency) applications.
What are the key features of ISOLA 370HR PCB?
ISOLA 370HR PCBs are known for their low dielectric constant, low dissipation factor, and good thermal stability. They provide consistent electrical performance and are suitable for demanding electronic applications where signal integrity and reliability are critical.
What are the applications of ISOLA 370HR PCB?
ISOLA 370HR PCBs are used in various applications, including telecommunications equipment, networking devices, aerospace systems, high-end computing hardware, and other high-speed digital and RF applications.
What are the benefits of using ISOLA 370HR PCB?
The benefits of using ISOLA 370HR PCB include excellent electrical performance, reliability, and durability. These PCBs offer consistent signal integrity, thermal stability, and compatibility with high-speed digital and RF signals, making them ideal for critical electronic applications.
How is ISOLA 370HR PCB manufactured?
ISOLA 370HR PCBs are manufactured using a series of processes, including material preparation, layer stackup design, imaging, etching, drilling, plating, solder mask application, surface finishing, and final inspection. The manufacturing process involves precision engineering and quality control to ensure high-quality PCBs.
Where can I buy ISOLA 370HR PCBs?
ISOLA 370HR PCBs can be purchased from authorized PCB manufacturers or distributors that specialize in high-performance laminate materials. It’s essential to work with reputable suppliers who can provide high-quality products and reliable customer service.
What are the design guidelines for ISOLA 370HR PCBs?
Design guidelines for ISOLA 370HR PCBs include considerations such as material selection, layer stackup design, trace routing, component placement, thermal management, and design for manufacturability. Following these guidelines helps ensure optimal performance and reliability of the PCB design.