Insulated Metal Substrates Manufacturer
Insulated Metal Substrates Manufacturer,Insulated Metal Substrates (Insulated Metal Substrates) are engineered for applications that require superior heat management and electrical insulation. These substrates consist of a metal base, often aluminum, combined with an insulating layer and a copper circuitry layer. The metal base efficiently conducts heat away from sensitive components, preventing overheating and enhancing overall performance. The insulating layer ensures electrical isolation, protecting against short circuits and improving reliability. Insulated Metal Substrates substrates are commonly used in high-power LED lighting, power electronics, and automotive systems, where effective thermal management is crucial. Their robust design ensures durability and optimal functionality in demanding electronic environments.
What is Insulated Metal Substrate?
Insulated Metal Substrate (IMS) refers to a type of printed circuit board (PCB) that combines a metal base with a dielectric insulating layer to offer superior thermal and electrical performance. IMS technology is primarily used in applications requiring efficient heat dissipation and high reliability, such as in power electronics, automotive systems, and LED lighting.
The structure of an IMS typically consists of a metal core—often aluminum or copper—that acts as the primary heat spreader. This metal core is covered with a dielectric insulating layer that provides electrical insulation while allowing for effective heat transfer away from sensitive electronic components. On top of the dielectric layer, a printed circuit layer is applied to establish electrical connections and circuitry.
The key advantages of IMS include its excellent thermal conductivity, which helps in managing heat generated by high-power components, and its high mechanical strength, which contributes to durability and stability under stress. Additionally, IMS boards can be designed to be lightweight and compact, making them suitable for space-constrained applications.
In the electronics industry, IMS is crucial for enhancing the performance and lifespan of devices by preventing overheating and ensuring reliable operation. Its applications span across various fields, including consumer electronics, telecommunications, automotive electronics, and industrial controls. With the growing demand for more efficient and reliable electronic systems, IMS technology continues to play a significant role in advancing electronic device capabilities.
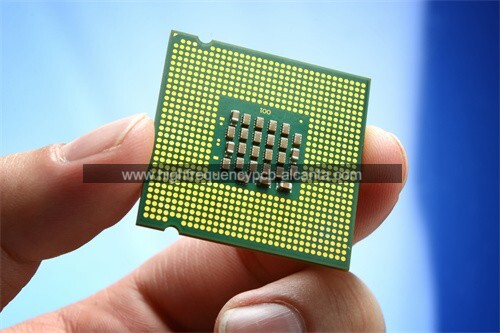
Insulated Metal Substrates Manufacturer
What are the Insulated Metal Substrates Design Guidelines?
Designing Insulated Metal Substrates (IMS) requires careful consideration to ensure optimal performance and reliability in electronic applications. Here are some key design guidelines to follow:
- Thermal Management:Proper heat dissipation is crucial in IMS design. Ensure that the metal core (often aluminum or copper) is adequately sized and positioned to spread heat effectively from high-power components. Consider the thermal conductivity of the metal core and the dielectric layer to optimize heat transfer.
- Dielectric Layer Selection: Choose a dielectric material with appropriate thermal and electrical properties. The dielectric layer should have a high thermal conductivity to facilitate efficient heat transfer and good electrical insulation properties to prevent short circuits.
- Circuit Design: Design the circuit layout to minimize thermal stress and ensure even heat distribution. Place high-power components in areas where heat dissipation can be maximized. Avoid placing sensitive components near high-heat areas to prevent thermal damage.
- Metal Core Thickness:Select the metal core thickness based on the heat dissipation requirements and mechanical strength needed for the application. Thicker metal cores offer better heat spreading but may add to the overall board thickness and weight.
- Adhesive Bonding: Ensure proper adhesion between the metal core and the dielectric layer. The bonding process should be carefully controlled to avoid delamination or weak adhesion that could affect thermal and electrical performance.
- Thermal Via Placement: Use thermal vias to enhance heat transfer from the component pads to the metal core. Properly placed thermal vias can significantly improve thermal management and reduce hot spots.
- Mechanical Considerations: Account for mechanical stresses and strains during the design phase. The IMS board should be robust enough to withstand environmental conditions and mechanical handling without compromising performance.
- Electrical Performance: Ensure that the dielectric layer provides adequate electrical insulation to prevent leakage currents and maintain circuit integrity. Verify that the electrical performance meets the requirements of the specific application.
- Manufacturing Tolerances: Work closely with manufacturers to understand and accommodate their tolerances and capabilities. Accurate manufacturing processes are essential for maintaining the integrity of the IMS board and its performance.
- Compliance and Testing: Ensure that the IMS design complies with relevant industry standards and regulations. Conduct thorough testing, including thermal, electrical, and mechanical tests, to validate the design and performance of the IMS board.
By adhering to these guidelines, designers can create IMS boards that provide effective thermal management, electrical insulation, and mechanical stability, thereby enhancing the overall performance and reliability of electronic devices.
What is the Insulated Metal Substrates Fabrication Process?
The fabrication process of Insulated Metal Substrates (IMS) involves several key steps to produce high-performance, reliable PCBs with effective thermal management and electrical insulation. Here is an overview of the IMS fabrication process:
- Metal Core Preparation: Start with a metal core, typically aluminum or copper. The metal core is often pre-treated to enhance adhesion with the dielectric layer. The core is cut to the required size and shape according to the design specifications.
- Dielectric Layer Application: Apply a dielectric insulating layer onto the metal core. This layer is usually made from materials like epoxy-based composites, ceramic-filled polymers, or other high-thermal-conductivity dielectrics. The application is performed using techniques such as lamination or direct coating. The dielectric layer must be evenly applied to ensure consistent electrical insulation and thermal conductivity.
- Curing Process: If a thermosetting dielectric material is used, it must be cured to achieve its final properties. This curing process involves heating the substrate to a specific temperature to harden the dielectric material and improve its mechanical and thermal properties.
- Circuit Layer Formation: After the dielectric layer is cured, the circuit pattern is created on the substrate. This is typically done using photolithography, where a photoresist layer is applied, exposed to UV light through a mask, and developed to reveal the desired circuit pattern. Alternatively, direct copper plating or etching techniques may be used to form the circuit layer.
- Through-Hole and Via Drilling: Drill holes for through-hole components and vias as needed. This step involves precise drilling to create vias for electrical connections between different layers or to accommodate component leads.
- Plating and Metallization: Plate the drilled holes and vias with a conductive material, usually copper, to establish electrical connections. This is done through electroplating or electroless plating processes, which ensure the vias are electrically conductive.
- Surface Finish: Apply a surface finish to the exposed copper areas to protect against oxidation and enhance solderability. Common finishes include gold, silver, or solder mask coatings.
- Assembly and Testing: After the IMS substrate is fabricated, it undergoes assembly where electronic components are mounted onto the substrate. This includes soldering or bonding components onto the circuit layer. Finally, the assembled substrate is subjected to rigorous testing to ensure it meets electrical, thermal, and mechanical specifications.
- Inspection and Quality Control: Conduct thorough inspections and quality control checks throughout the fabrication process. This includes visual inspections, electrical testing, thermal performance evaluation, and mechanical stress testing to ensure the IMS meets all design requirements and standards.
- Packaging and Shipping: Once the IMS substrates pass all quality checks, they are packaged for shipping. Proper packaging ensures that the substrates are protected during transit and handling.
By following these steps, manufacturers can produce IMS substrates that offer excellent thermal management, electrical insulation, and mechanical strength, making them suitable for high-performance electronic applications.
How Do You Manufacture Insulated Metal Substrates?
Manufacturing Insulated Metal Substrates (IMS) involves a detailed and precise process to ensure that the final product meets performance and reliability standards. Here is a step-by-step overview of the IMS manufacturing process:
- Metal Core Selection and Preparation: Choose the appropriate metal for the core, typically aluminum or copper, based on thermal and mechanical requirements. The metal core is cut to the desired dimensions and pre-treated to enhance adhesion with the dielectric layer. This may involve cleaning and surface roughening processes.
- Dielectric Layer Application: Apply a dielectric insulating layer to the metal core. The dielectric material is chosen for its thermal conductivity and electrical insulation properties. This application can be done using methods such as lamination, where a pre-impregnated dielectric film is bonded to the metal core under heat and pressure, or direct coating, where liquid dielectric materials are applied and then cured.
- Curing: If a thermosetting dielectric material is used, it must be cured to achieve its final properties. This step involves heating the substrate to a specified temperature to harden the dielectric layer, improving its thermal and mechanical characteristics.
- Circuit Pattern Formation: Create the circuit pattern on the dielectric layer using photolithography or direct imaging. Photolithography involves applying a photoresist layer, exposing it to UV light through a mask to define the circuit pattern, and then developing the photoresist to reveal the pattern. Direct imaging methods use laser or digital printing techniques to create the circuit layout.
- Etching and Plating: After pattern formation, etch the circuit layer to remove unwanted copper and leave behind the desired circuit design. This is followed by plating, where additional copper is deposited onto the circuit pattern and through-holes to enhance conductivity and provide a surface for component mounting.
- Through-Hole and Via Drilling: Drill holes for through-hole components and vias. This is done with precision to ensure that the holes align correctly with the circuit design. The drilling process must be carefully controlled to avoid damaging the dielectric layer or metal core.
- Metallization and Plating of Vias: Plate the drilled vias and through-holes with a conductive material, typically copper, to ensure electrical connections between different layers of the substrate. This step involves electroplating or electroless plating processes.
- Surface Finishing: Apply a surface finish to protect the exposed copper areas from oxidation and to improve solderability. Common finishes include gold, silver, or solder mask coatings. The choice of finish depends on the specific application and performance requirements.
- Component Assembly: Mount electronic components onto the IMS substrate. This involves soldering or bonding components onto the circuit pattern. Ensure that the assembly process does not adversely affect the thermal management properties of the IMS.
- Testing and Quality Control:Perform thorough testing and quality control checks to ensure the IMS meets all performance specifications. This includes electrical testing, thermal performance evaluation, and mechanical stress testing. Any defects or issues are identified and addressed before the product proceeds to the next stage.
- Final Inspection and Packaging: Conduct a final inspection to verify that the IMS substrates meet all quality standards. Once approved, package the substrates carefully to protect them during shipping and handling.
By adhering to these manufacturing steps, producers can create high-quality Insulated Metal Substrates that offer effective thermal management, electrical insulation, and mechanical durability, suitable for demanding electronic applications.
How Much Should Insulated Metal Substrates Cost?
The cost of Insulated Metal Substrates (IMS) can vary widely based on several factors, including material composition, substrate size, thermal conductivity, and specific manufacturing processes. Here’s a detailed breakdown of the factors influencing IMS cost:
- Material Type: IMS typically use materials like aluminum, copper, or other metals for the base layer, with insulating materials such as ceramics or polymer resins. The choice of metal significantly impacts the cost. For example, copper is generally more expensive than aluminum due to its superior thermal and electrical conductivity.
- Insulation Material:The insulating layer, often made of ceramics like alumina or aluminum nitride (AlN), or specialized polymers, affects the overall cost. High-performance ceramics or advanced polymers can increase costs but offer better thermal management and reliability.
- Thermal Conductivity:Substrates with higher thermal conductivity generally cost more because they require higher-grade materials and more precise manufacturing techniques. Applications requiring excellent thermal management, such as high-power LEDs or power electronics, will likely involve higher costs.
- Substrate Size and Thickness: Larger and thicker substrates require more material and processing time, thus increasing the cost. Custom sizes and thicknesses that deviate from standard offerings can also add to the cost due to the need for specialized manufacturing.
- Manufacturing Processes: The complexity of the manufacturing process impacts cost. Techniques like direct copper bonding (DCB) or active metal brazing (AMB) involve additional processing steps and equipment, which can drive up costs. High-precision processes for creating detailed patterns or complex shapes also add to the overall expense.
- Volume and Customization: Bulk orders or standardized substrates typically come at a lower unit cost due to economies of scale. Custom or low-volume orders may incur higher costs per unit due to setup and production adjustments. Customization, such as specific cutouts or additional features, can also increase costs.
- Supplier and Region:Prices can vary by supplier and region due to differences in labor costs, material availability, and regional market conditions. Suppliers in regions with high manufacturing costs or import duties may offer higher prices.
- Quality and Reliability:High-quality IMS with stringent reliability and performance standards, such as those used in critical applications or harsh environments, tend to be more expensive. Ensuring consistency and performance often involves additional quality control measures.
In summary, while the cost of IMS substrates can vary widely, a rough estimate might be anywhere from $10 to $100 per piece, depending on the factors mentioned above. For high-end or custom applications, costs can exceed this range significantly. For accurate pricing, it’s advisable to request quotes from multiple suppliers and consider the specific requirements of your application.
What is Insulated Metal Substrates Base Material?
The base material of Insulated Metal Substrates (IMS) plays a crucial role in their performance and functionality. Here’s an in-depth look at the base materials commonly used in IMS:
- Aluminum: Aluminum is one of the most commonly used base materials for IMS due to its excellent thermal conductivity, lightweight properties, and cost-effectiveness. It provides a good balance of thermal management and mechanical strength. Aluminum substrates are often used in applications where moderate to high thermal dissipation is required, such as in LED lighting and power electronics.
- Copper:Copper is another popular base material for IMS, known for its superior thermal and electrical conductivity. Copper substrates are preferred in high-performance applications that require exceptional heat dissipation, such as high-power LED systems, power converters, and RF (radio frequency) applications. Copper substrates are more expensive than aluminum but offer better thermal performance and reliability.
- Alloyed Metals:Some IMS may use alloyed metals, which are blends of aluminum, copper, or other metals to achieve specific properties. These alloys can be designed to enhance thermal conductivity, mechanical strength, or other characteristics based on the application requirements. For example, aluminum-copper alloys may be used to balance cost and performance.
- Ceramics: In some advanced IMS designs, ceramics may be used as the base material. Ceramics like aluminum nitride (AlN) or silicon nitride (Si3N4) offer excellent thermal conductivity and high thermal resistance. They are used in applications where extremely high thermal management is crucial, such as in high-power RF applications or in environments with high thermal stress. Ceramics are generally more expensive and more challenging to process compared to metals.
- Polymer-Based Materials: While less common, certain IMS designs may incorporate polymer-based materials for the base layer. These materials are typically used in applications where cost reduction is more critical than high thermal performance. Polymer-based substrates might be utilized in low-power electronics or consumer products where high thermal conductivity is not as critical.
- Hybrid Materials: Some IMS substrates use hybrid materials that combine metal and ceramic or polymer layers to achieve a balance of properties. For instance, a metal base layer may be combined with a ceramic insulating layer to provide both good thermal conductivity and electrical insulation. Hybrid materials allow for customization based on specific application needs, such as improved thermal management or enhanced durability.
The choice of base material for IMS depends on the specific requirements of the application, including thermal performance, mechanical strength, cost, and reliability. Each material offers distinct advantages and trade-offs, and selecting the right base material is crucial for achieving optimal performance in the final substrate.
Which Company Makes Insulated Metal Substrates?
Many companies manufacture Insulated Metal Substrates (IMS). Some notable ones include:
- Advanced Ceramic X: This company specializes in high-performance ceramic substrates and IMS, particularly excelling in high-power electronics and RF applications. Their products are renowned for their excellent thermal conductivity and electrical insulation properties.
- Rogers Corporation:Rogers is a leading supplier of high-performance circuit materials, including IMS products with high thermal conductivity in copper and aluminum substrates. Their products are widely used in communication, automotive, and industrial electronics, known for their reliable quality and innovative technology.
- Laird Thermal Systems: Laird provides various IMS products focused on excellent thermal management solutions. Their products are suitable for a range of applications from consumer electronics to high-power devices, meeting different performance requirements.
- National Thermal Corporation: This company specializes in high-quality thermal management materials and insulated substrates, with IMS products widely used in electronic device thermal management, offering excellent thermal conductivity and mechanical strength.
- Bergquist Company: Bergquist offers a variety of IMS products, ranging from standard to customized solutions. With deep expertise in thermal management and material science, they meet the high demands of various application scenarios.
Our company also manufactures Insulated Metal Substrates (IMS). We produce IMS products using high-quality aluminum or copper as the base material, combined with advanced insulating materials (such as aluminum nitride, alumina, or high-performance polymers). We maintain strict quality control during production to ensure that our IMS products meet industry standards in thermal management, mechanical strength, and electrical insulation.
We offer customized solutions based on specific customer needs, including different sizes, thicknesses, and special process requirements. Our IMS products are widely used in LED lighting, power converters, automotive electronics, and other applications requiring efficient heat dissipation. Whether for large-scale production or small batches, we provide competitive pricing and delivery times to meet various customer needs.
What are the 7 Qualities of Good Customer Service?
Good customer service is essential for building strong customer relationships and fostering loyalty. Here are seven key qualities that define excellent customer service:
- Responsiveness: Good customer service requires prompt and efficient responses to customer inquiries and issues. This means acknowledging receipt of requests quickly and resolving them in a timely manner. Fast response times show customers that their concerns are valued and prioritized.
- Empathy: Understanding and sharing the feelings of customers is crucial. Empathetic service involves listening actively, acknowledging the customer’s emotions, and addressing their concerns with sensitivity. This helps in building a connection and making customers feel heard and understood.
- Knowledge:Service representatives should be well-informed about the products, services, and policies of the company. A deep understanding of these aspects enables them to provide accurate information, offer helpful solutions, and answer questions effectively, enhancing the overall customer experience.
- Patience: Customers may have complex issues or need time to explain their problems. Patience involves giving them the time they need to articulate their concerns without rushing them. It also means handling difficult or frustrated customers with composure and understanding.
- Clear Communication: Effective communication is key to good customer service. This includes speaking clearly, avoiding jargon, and ensuring that explanations are easy to understand. Good communication helps in minimizing misunderstandings and ensuring that customers are well-informed.
- Professionalism: Maintaining a professional demeanor involves being courteous, respectful, and maintaining a positive attitude, even in challenging situations. Professionalism helps in building trust and credibility, and it reflects positively on the company’s image.
- Consistency: Providing a consistent level of service ensures that customers receive the same high-quality experience every time they interact with the company. Consistency builds reliability and trust, making customers feel assured that they will get the same level of support regardless of when or how they contact the company.
By embodying these qualities, companies can enhance their customer service, leading to higher satisfaction, loyalty, and positive word-of-mouth.
FAQs about Insulated Metal Substrates
What is an Insulated Metal Substrate (IMS)?
An IMS is a type of circuit board that features a metal base layer (typically aluminum or copper) with an insulating layer between the metal and the circuitry. This design enhances thermal management and electrical insulation.
What are the main applications of IMS?
IMS are commonly used in applications requiring effective heat dissipation, such as LED lighting, power converters, automotive electronics, and high-power RF devices.
What materials are typically used for the metal base in IMS?
The metal base is usually made of aluminum or copper. Aluminum is cost-effective and provides good thermal management, while copper offers superior thermal and electrical conductivity but is more expensive.
What insulating materials are used in IMS?
Insulating materials often include ceramics like aluminum nitride (AlN) or alumina (Al2O3), and sometimes high-performance polymers. These materials provide electrical insulation and help manage heat.
What are the benefits of using IMS?
IMS offer several benefits, including improved thermal management, enhanced electrical insulation, reduced thermal expansion issues, and better reliability in high-power applications.
How does IMS compare to traditional PCBs?
IMS generally provide superior thermal performance compared to traditional printed circuit boards (PCBs), making them ideal for applications with high heat generation. Traditional PCBs may not offer the same level of heat dissipation or insulation.
Can IMS be customized?
Yes, IMS can be customized in terms of size, thickness, and insulating material to meet specific application requirements. Customization allows for tailored solutions for various industries and applications.