What is IC Substrate?
IC Substrate,IC Substrate (Integrated Circuit Substrate) is a crucial component in electronic devices for mounting and connecting integrated circuits (ICs). It provides a platform for chips to interface with Printed Circuit Boards (PCBs). Typically composed of multiple layers of thin films including insulation, metal, and conductor layers, IC Substrate ensures reliable electrical connections and effective thermal management. Its design considerations encompass signal transmission, thermal regulation, and miniaturization to meet the demands of modern electronic devices. These substrates are vital for optimizing the performance, reliability, and form factor of electronic products.
IC Substrate, often referred to as the linchpin or foundation in the realm of semiconductor technology, serves as the dynamic nexus that bridges an integrated circuit (IC) or semiconductor device with the expansive electronic landscape of circuit boards. It transcends its static role as a support structure, actively choreographing the intricate dance of components within the IC.
Going beyond the realm of mechanical stability, the substrate assumes an active role in orchestrating thermal considerations and weaving the intricate web of essential electrical connections. This multifaceted engagement is not just supportive but is paramount in safeguarding the operational integrity of the IC. The judicious curation of substrate material and design commands a profound impact on electrical dynamics, heat dissipation, and the holistic reliability of the integrated circuit.
A diverse panorama of IC substrates unfolds, each distinguished by its unique material composition and structural intricacies:
Ceramic Substrates: Forged from materials like alumina or aluminum nitride, ceramic substrates flaunt noteworthy thermal conductivity, becoming a pivotal player in the symphony of efficient heat dissipation.
Organic Substrates: Crafted from organic materials such as epoxy resin and glass fiber, these substrates present a cost-effective and lightweight alternative to ceramics, albeit with a subtle compromise on thermal conductivity.
Metal Core Substrates (MCPCB): Stepping into the limelight with a metal core, often sculpted from aluminum or copper, these substrates emerge as virtuosos in thermal conductivity, finding their forte in high-power scenarios where heat dissipation is a non-negotiable.
Flexible Substrates: Unveiling their flexibility in the realm of flexible electronics, these substrates showcase adaptability, gracefully conforming to diverse shapes. Their composition often involves flexible materials like polyimide.
The design and selection of the substrate are a meticulously curated ballet, choreographed to meet the specific demands of the integrated circuit, encompassing considerations such as power dissipation, thermal equilibrium, and dimensional constraints. The perpetual evolution in semiconductor technology propels an ongoing symphony of enhancements in IC substrate materials and designs, harmonizing seamlessly with the ever-evolving demands of modern electronic devices.
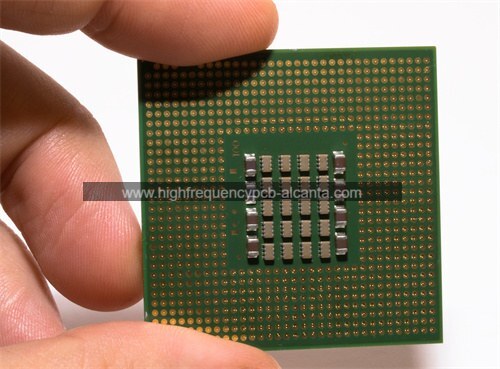
IC Substrate
What are the Functions of IC Substrate?
In the intricate landscape of semiconductor technology, IC substrates take on a myriad of roles, each contributing significantly to the seamless operation and dependability of integrated circuits (ICs). Let’s explore the diverse functions that IC substrates fulfill:
Architectural Pillar: At its essence, IC substrates serve as the architectural backbone, providing a sturdy foundation for the delicate components within integrated circuits. This foundational role is paramount in ensuring the resilience of semiconductor elements during various stages, from handling to operational use.
Electrical Conduit: Functioning as a conduit for electrical connections, IC substrates facilitate the smooth transmission of electrical signals among different components of the IC. Through the inclusion of conductive pathways, they enable effective communication, underpinning the proper functionality of the integrated circuit.
Thermal Maestro: A critical responsibility of IC substrates lies in the management of heat generated by the integrated circuit. By incorporating materials with commendable thermal conductivity, substrates play a pivotal role in dissipating heat effectively. This is crucial for averting overheating issues and maintaining optimal performance.
Guardian of Signal Purity: IC substrates actively contribute to maintaining the purity of electrical signals. They create a controlled environment that mitigates signal losses, crosstalk, and other undesirable effects, thus upholding the quality and reliability of transmitted signals.
Environmental Sentinel:In the role of vigilant guardians, IC substrates provide a protective shield, safeguarding semiconductor components against environmental factors such as moisture, contaminants, and mechanical stress. This shielding mechanism is essential, playing a crucial role in guaranteeing the prolonged durability and unwavering reliability of the integrated circuit.
Size and Weight Artisan: Tailored to specific applications, IC substrates can be fine-tuned to meet size and weight requirements. The use of flexible substrates, for instance, caters to scenarios where flexibility and reduced weight are paramount, as seen in wearable devices and flexible electronic products.
Harmony with Manufacturing Processes: Meticulously crafted, IC substrates seamlessly integrate with diverse manufacturing processes, encompassing assembly and packaging techniques. This seamless compatibility is essential for the smooth assimilation of IC substrates into the broader production of electronic devices.
Versatility Across Technological Frontiers: IC substrates showcase versatility by adapting to different IC technologies, spanning advanced semiconductor processes. This adaptability ensures that IC substrates align with the dynamic technological demands of semiconductor devices.
In summary, IC substrates emerge as versatile orchestrators, providing the essential physical and electrical infrastructure for the effective functioning and reliability of integrated circuits. Their multifaceted functions span foundational support, electrical connectivity, thermal management, signal integrity preservation, environmental protection, and adaptability to diverse manufacturing processes and technological advancements.
What are the Different Types of IC Substrate?
In the expansive domain of IC substrates, a panorama of diversity unfolds, revealing a myriad of types meticulously designed to cater to specific applications and distinctive needs. Let’s embark on an exploration of these categories:
Ceramic Substrates:
Materials: Forged from the robust embrace of ceramic elements like alumina (Al2O3) or aluminum nitride (AlN), these substrates unveil not just strength but a thermal prowess that elevates them in the realm of resilience.
Characteristics: With outstanding thermal conductivity, robust mechanical resilience, and effective electrical insulation, these substrates stand as exemplars of engineering excellence.
Applications: Carving a niche in high-power and high-frequency realms, these substrates stand out in scenarios demanding top-tier thermal properties.
Organic Substrates:
Materials: Crafted from organic elements such as epoxy resin and glass fiber.
Attributes: Noteworthy for their cost-effectiveness, lightweight demeanor, and versatility for general-purpose applications.
Applications: Embraced in the realm of consumer electronics and environments where the spotlight is on weight efficiency and cost-effectiveness.
Metal Core Substrates (MCPCB):
Materials: Flaunting a metal core, typically hewn from aluminum or copper.
Features: Showcasing excellent thermal conductivity, positioning them as stalwarts for applications requiring efficient heat dissipation.
Applications: Flourishing in domains housing high-power LED modules, power electronics, and environments marked by substantial heat generation.
Flexible Substrates:
Materials: Crafted from flexible materials such as polyimide.
Qualities: Offering a ballet of flexibility and adaptability, these substrates take center stage in scenarios demanding unconventional form factors.
Applications: Gracing the world of flexible electronics, wearable devices, and settings where the need for bendable substrates unfolds.
Glass Substrates:
Materials: Crafted from the elegance of glass or glass-ceramic materials.
Attributes: Exhibiting regal dimensional stability, electrical insulation, and the allure of transparency.
Applications: Integral in the realms of optoelectronics, display panels, and environments where the enchantment of transparency becomes a defining feature.
Semiconductor Integrated Substrates:
Materials: Primarily born from the realm of silicon or other semiconductor materials.
Features: Encompassing a harmonious integration of substrate and semiconductor components, composing a unified symphony.
Applications: Paving the way for emerging technologies seamlessly integrating semiconductor devices and substrates.
LTCC (Low-Temperature Co-Fired Ceramic) Substrates:
Materials: Born from ceramics processed at low temperatures, unfolding a tapestry of uniqueness.
Attributes: Suited for the intricate ballet of multi-layer structures and the integration of passive components.
Applications: Echoing in the corridors of RF and microwave applications, as well as finding resonance in modules designed for sophisticated electronic systems.
Silicon Interposers:
Materials: Embracing the essence of silicon-based marvels.
Features: Facilitating a symphony of integration for silicon-based interconnects between chips.
Applications: Taking the spotlight in the three-dimensional marvels of IC packaging, seamlessly connecting stacked semiconductor chips.
These diverse IC substrates unfurl a tapestry of versatility, presenting solutions ranging from the classic printed circuit boards (PCBs) to avant-garde semiconductor packaging techniques. The selection of a specific substrate transforms into an art form, guided by considerations such as thermal prerequisites, the choreography of form factors, the economics of cost, and the unique aspirations of the electronic device eagerly awaiting its substrate companion.
Does a relationship exist between IC substrate and chip packaging technology?
The intricate dance between IC substrates and chip packaging technology is pivotal in orchestrating the seamless integration and optimal performance of semiconductor devices. Let’s explore the nuances that define this dynamic relationship:
Structural Pillar:
IC substrates emerge as the structural pillars, providing a robust foundation for securely housing semiconductor chips within the packaging architecture.
Conductive Nexus:
Functioning as a conductive nexus, IC substrates intricately weave the pathways for electrical interconnection, allowing the semiconductor chip to harmonize with other components through conductive traces.
Thermal Maestro:
Serving as thermal maestros, IC substrates, armed with high thermal conductivity, lead the symphony of heat dissipation during chip operation, ensuring an environment of optimal temperatures.
Integration Ballet:
IC substrates seamlessly integrate into a myriad of chip packaging technologies – be it the agile flip-chip packaging, the versatile ball grid array (BGA), or the compact chip-on-board (COB) configurations – adapting their design and materials with finesse.
Form Factor Alchemist:
In the alchemy of miniaturization and form factor optimization, IC substrates, especially their flexible counterparts, take center stage, enabling the creation of more compact and streamlined chip packaging designs.
Signal Symphony Conductor:
The design intricacies and material choices of IC substrates act as conductors in the symphony of signal integrity, orchestrating a seamless flow that minimizes losses and elevates overall performance.
Pioneering Advanced Packaging Choreography:
As electronic packaging ventures into the realms of innovation, such as System-in-Package (SiP) and 3D IC packaging, IC substrates play a pioneering role, leading the choreography of stacking and interconnecting diverse semiconductor elements.
Compatibility Artistry:
The relationship extends to an artistry of compatibility with semiconductor manufacturing processes, where IC substrates seamlessly align with the intricacies of these processes, ensuring a flawless integration performance.
In essence, the dynamic interplay between IC substrates and chip packaging technology is a ballet of support, connectivity, thermal finesse, and adaptability. As chip packaging technologies evolve, the role of IC substrates remains not just instrumental but artistic, actively contributing to the efficiency and advancement of semiconductor devices.
How does IC Substrate Differ from Traditional PCBs?
IC substrates and traditional PCBs diverge in design and functionality, embodying distinct roles within the intricate tapestry of electronic systems. Let’s explore the distinctive features that set these two components apart:
Core Purpose and Function:
IC Substrate: Articulated as a specialized canvas crafted for the mounting and interconnection of semiconductor devices, with a laser focus on meeting the unique demands posed by integrated circuits (ICs) and chips.
Traditional PCB: Assumes a more expansive role, serving as a versatile canvas accommodating an array of electronic components, from resistors to capacitors and ICs, contributing to the overarching functionality of electronic devices.
Integration Intricacy:
IC Substrate: Tailored for the delicate integration ballet of semiconductor components, showcasing advanced elements like fine-pitch traces, microvias, and materials meticulously chosen for the intricacies of densely packed semiconductor devices.
Traditional PCB: Offers a broader integration palette, providing a canvas for various electronic components with a layout that may carry less intricate details compared to the specialized dance of IC substrates.
Material Symphony:
IC Substrate: Conducts a material symphony, leveraging substances fine-tuned for thermal, electrical, and mechanical prowess, purposefully optimized for the unique challenges posed by semiconductor packaging.
Traditional PCB: Joins the material ensemble, with FR-4 being a common note. Material selection dances to the tune of cost, electrical properties, and the application’s specific requirements.
Form Factor and Size Waltz:
IC Substrate: Choreographed with a specific form factor, moving in harmony with the dimensions of semiconductor devices, showcasing variations like flip-chip substrates, ball grid array (BGA) substrates, and more.
Traditional PCB: Engages in a versatile waltz of form factors and sizes, accommodating the diverse needs of electronic devices. PCBs may sway between rigidity, flexibility, or a dance of both depending on the application.
Interconnection Poetry:
IC Substrate: Composes a symphony of interconnection methods finely tuned for semiconductor devices, featuring movements like fine-pitch bonding, wire bonding, or the elegant flip-chip interconnects.
Traditional PCB: Weaves a poetic narrative of interconnection techniques—through-hole vias, surface-mount technology (SMT), and basic traces—suitable for a diverse ensemble of electronic components.
Thermal Ballet:
IC Substrate: Takes center stage in the thermal ballet, designed with a keen focus on dissipating the heat emanating from semiconductor devices. Features may include graceful heat sinks, thermal vias, and materials with a thermal conductivity encore.
Traditional PCB: While appreciating the nuances of thermal considerations, the focus may not be as intensive as in the specialized choreography of IC substrates. Heat dissipation methods harmonize with the application’s needs, featuring elements like heat sinks, copper planes, and vias.
Cost and Manufacturing Symphony:
IC Substrate: Engages in a manufacturing symphony, marked by complexity and specialization, incorporating intricate steps such as laser drilling, microvia formation, and the performance of advanced packaging technologies. This symphony may resonate with higher manufacturing costs.
Traditional PCB: Contributes to the symphony with a more straightforward manufacturing composition, resulting in a cost-effective performance suitable for standard electronic applications.
In essence, the interplay between IC substrates and traditional PCBs unfolds as a dance of specialization versus versatility, each taking center stage to cater to the unique demands of semiconductor packaging and the diverse harmonies of electronic applications, respectively.
What is the Main Structure and Production Technology of IC Substrate?
The creation of IC substrates involves a meticulous dance of materials and processes, tailored to meet the intricate demands of semiconductor integration. Let’s explore the main structure and the symphony of production technology orchestrating the birth of these substrates:
Main Structure:
Substrate Canvas:
At its core lies the substrate base, a canvas crafted from materials such as ceramics (like alumina or aluminum nitride), organic substrates (comprising epoxy resin and glass fiber), metal cores (often aluminum or copper), or the very essence of semiconductors, primarily silicon.
Insulating Elegance:
Layers of dielectric grace the substrate, providing an elegant insulation dance between conductive layers, ensuring electrical isolation. These layers showcase the artistry of materials with specific electrical properties.
Conductive Choreography:
Conductor traces and interconnects adorn the substrate, tracing intricate paths to enable the graceful ballet of electrical connections between diverse components. This intricate dance is choreographed through advanced lithography and etching techniques.
Bonding Pads Centerstage:
Bonding pads take center stage, designated areas where semiconductor chips elegantly attach. These pads become the interface, the connection point for the electrical synergy to unfold.
Vertical Flourish:
Through-hole vias or microvias make a vertical entrance, establishing connections between different layers of the substrate. This vertical flourish is orchestrated through techniques such as laser drilling or mechanical drilling.
Solder Mask Veil and Surface Finish:
A veil of solder mask graces the substrate’s surface, a protective layer with openings that reveal the bonding pad beauty. The surface finish, often composed of noble metals like gold or tin, enhances solderability and resists the corrosion waltz.
Additional Embellishments:
Depending on the application’s desires, the substrate may showcase additional embellishments. Embedded passive components may add a touch of resistance or capacitance, while structures for heat dissipation (such as thermal vias and sinks) may join the ensemble.
Production Technology:
Substrate Alchemy:
The production spectacle commences with the alchemy of substrate fabrication. Different types of substrates, each with its own unique charm, undergo specific manufacturing processes. Ceramics may engage in the enchanting sintering ritual, while organics follow the rhythmic dance of lamination.
Lithography Elegance:
Advanced lithography takes the stage, etching intricate patterns of conductive traces and interconnects on the substrate surface. This elegance is essential for achieving the desired connectivity, a visual sonnet of electrical pathways.
Dielectric Layer Ballet:
Dielectric layers pirouette onto the substrate, providing an electrical insulation ballet between conductive layers. The layers elegantly deposit through techniques like chemical vapor deposition (CVD) or physical vapor deposition (PVD).
Via Waltz:
Vias take center stage, whether through-hole or micro, establishing vertical connections in a waltz of creation. Laser drilling or mechanical drilling join the dance, creating pathways for vertical synergy.
Finish and Mask Harmony:
The substrate surface is adorned with a suitable finish, a finishing touch of gold, tin, or other noble metals. Solder mask then gracefully wraps the substrate, leaving openings for the bonding pad orchestra.
Component Integration Pas de Deux:
Semiconductor chips and components join in a pas de deux, delicately attached to the substrate through wire bonding, flip-chip bonding, or the graceful attachment of solder balls.
Quality Ballet and Testing Overture:
The finished IC substrates enter the ballet of quality control and testing. Visual inspections, electrical tests, and reliability testing compose an overture, ensuring that the substrate symphony meets the specified requirements.
Optional Flourishes (Encore):
For the grand finale, optional processes may join the encore. Embedded passive components may play a supporting role, and heat dissipation structures may add a final touch of sophistication.
In essence, the creation of IC substrates becomes a grand performance, where materials and processes waltz and pirouette to bring forth the intricate canvas that forms the foundation for the integration of semiconductor devices.
Frequently Asked Questions (FAQs)
What pivotal role does an IC Substrate play?
Answer: The primary role of an IC Substrate is to provide structural support and facilitate electrical connectivity for semiconductor devices. By serving as a foundation for mounting ICs, it ensures reliable connections and significantly contributes to the overall performance of integrated circuits.
Which materials find common use in IC Substrates?
Answer: IC Substrates exhibit versatility in materials, including ceramics (like alumina or aluminum nitride), organic substrates (such as epoxy resin and glass fiber), metal cores (typically aluminum or copper), or semiconductor materials (primarily silicon). Material selection depends on specific application requirements.
How is the manufacturing process of IC Substrates orchestrated?
Answer: The manufacturing process unfolds with substrate fabrication, followed by lithographic circuit patterning, dielectric layer deposition, via formation (utilizing through-hole or microvias), surface finish and solder mask application, semiconductor component attachment, and rigorous quality control procedures.
Can IC Substrates incorporate embedded passive components?
Answer: Absolutely. Some IC Substrates showcase the capability to integrate embedded passive components like resistors and capacitors. This integration not only saves space but also enhances electrical performance in specific applications.
What role does an IC Substrate play in advanced packaging technologies?
Answer: IC Substrates take center stage in advanced packaging technologies such as System-in-Package (SiP) and 3D IC packaging. They orchestrate the stacking and interconnection of diverse semiconductor elements, contributing significantly to the miniaturization and enhanced performance of electronic devices.
Conclusion
In summary, the realm of IC substrates unfolds as a dynamic interplay of materials, precision engineering, and functional finesse. Serving as the bedrock for semiconductor integration, an IC Substrate orchestrates a choreography that harmonizes structural support, electrical connectivity, and thermal equilibrium. The diverse palette of materials, spanning ceramics to organics, bestows adaptability to this indispensable component.
As we delve into the manufacturing journey, the craftsmanship of substrate fabrication, the symphonic resonance of lithographic processes, and the meticulous artistry of via formations converge to create a masterpiece – a canvas that forms the core of reliable and high-performance integrated circuits. The myriad types of IC substrates, each with its own signature, offer tailored solutions for a spectrum of applications, be it the graceful flip-chip substrates or the versatile ball grid array (BGA) substrates.
The IC Substrate’s influence on thermal dynamics emerges as a pivotal element, featuring a ballet of thermal vias, heat sinks, and thermally conductive materials. This choreography ensures the delicate balance of optimal operating temperatures, enhancing the durability and reliability of semiconductor devices.
Embedded passive components introduce a nuanced dimension, elevating space efficiency and electrical performance to a level of sophisticated integration. In the arena of advanced packaging technologies, IC Substrates take center stage, directing the intricate dance of stacking and interconnecting semiconductor elements in groundbreaking innovations like System-in-Package (SiP) and 3D IC packaging.
In essence, the IC Substrate stands as an architectural cornerstone in the domain of semiconductor integration, weaving together technology, artistic precision, and engineering finesse to create a platform that propels the electronic devices of the future. It is a testament to the perpetual evolution and refinement of electronic components, carving the path for advancements in miniaturization, performance, and unwavering reliability.