High Speed Mixed Dielectric PCB Manufacturing
High Speed Mixed Dielectric PCB Manufacturing,High-Speed Mixed Dielectric PCBs are advanced printed circuit boards engineered to meet the demanding requirements of high-speed signal transmission across various frequencies. These PCBs utilize a combination of different dielectric materials strategically positioned throughout the board to optimize signal integrity and minimize interference. By incorporating materials such as high-frequency laminates, polyimide, PTFE-based substrates, and ceramics, High-Speed Mixed Dielectric PCBs offer superior performance compared to standard PCBs. They excel in applications involving telecommunications, data transmission, RF/microwave systems, and high-speed digital electronics. With precise impedance control, advanced routing techniques, and careful consideration of material properties, these PCBs ensure reliable signal propagation, reduced loss, and enhanced overall system performance. Whether used in aerospace, automotive, telecommunications, or consumer electronics, High-Speed Mixed Dielectric PCBs play a crucial role in enabling the high-speed data transmission and signal integrity required by today’s advanced electronic systems.
What is a High-Speed Mixed Dielectric PCB?
A High-Speed Mixed Dielectric PCB refers to a printed circuit board (PCB) designed for applications where signals of varying speeds and frequencies are present. In such PCBs, different areas of the board may have different dielectric materials, which affect the propagation of signals.
Here’s a breakdown of the key components:
- High-Speed Signals: These are signals that operate at high frequencies, typically in the range of hundreds of megahertz (MHz) to several gigahertz (GHz). Examples include signals used in telecommunications, data transmission, and high-speed digital electronics.
- Dielectric Material: Dielectric materials are insulators that separate the conductive traces on a PCB. They affect the speed at which electrical signals propagate along the traces. Different dielectric materials have different characteristics such as dielectric constant (ε), loss tangent (tan δ), and dispersion.
- Mixed Dielectric: High-Speed Mixed Dielectric PCBs utilize multiple types of dielectric materials across the board. This could mean that different layers of the PCB have different dielectric materials, or even within the same layer, there may be areas with different dielectrics. This allows designers to tailor the electrical properties of the PCB to meet the specific requirements of different signal paths on the board.
Designing a PCB with mixed dielectrics allows for better control over signal integrity, impedance matching, and reducing signal distortion and losses. It’s particularly crucial in high-speed applications where maintaining signal integrity is critical for reliable operation.
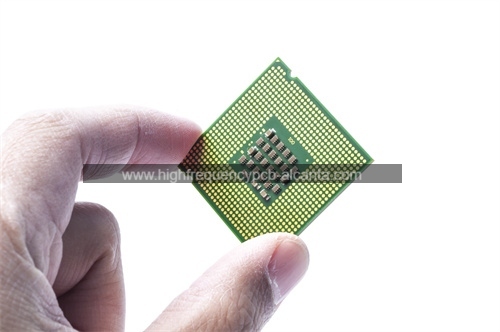
High Speed Mixed Dielectric PCB Manufacturing
What are the High-Speed Mixed Dielectric PCB Design Guidelines?
Designing a High-Speed Mixed Dielectric PCB requires careful consideration of various factors to ensure signal integrity, minimize losses, and maintain performance. Here are some guidelines:
- Impedance Control: Maintain consistent impedance throughout the board by carefully selecting dielectric materials and controlling trace widths and spacing. Use impedance calculators and simulation tools to verify impedance values.
- Signal Integrity Analysis: Perform signal integrity analysis using simulation software to predict and mitigate signal integrity issues such as reflections, crosstalk, and impedance mismatches. Consider factors like signal rise time, skew, and jitter.
- Layer Stackup Design: Plan the layer stackup carefully, placing high-speed signal layers adjacent to low-speed signal or power planes to minimize signal interference. Consider the dielectric constant and thickness of each layer to achieve the desired impedance.
- Grounding Strategy: Implement a solid grounding strategy to minimize ground bounce and noise. Use ground planes effectively and employ stitching vias to connect ground planes across different layers.
- Decoupling Capacitors: Place decoupling capacitors strategically near high-speed components to filter out high-frequency noise and stabilize power distribution. Follow best practices for decoupling capacitor placement and routing.
- Routing Guidelines: Route high-speed traces as short and direct as possible to minimize signal loss and interference. Use controlled impedance routing techniques and avoid sharp bends or corners in traces.
- Via Design: Optimize via design by minimizing via stub length and using proper via structures to maintain controlled impedance. Consider via placement and density to minimize signal reflections.
- Material Selection: Choose appropriate dielectric materials with consistent electrical properties for different regions of the PCB. Consider factors like dielectric constant, loss tangent, and temperature stability.
- Thermal Management: Address thermal concerns by designing adequate thermal relief for high-power components and ensuring sufficient airflow around critical areas. Thermal issues can affect the electrical performance of the PCB.
- Documentation and Review: Document the design thoroughly, including layer stackup details, impedance profiles, and signal routing strategies. Conduct peer reviews and simulations to validate the design before fabrication.
By following these guidelines, designers can create High-Speed Mixed Dielectric PCBs that meet the stringent requirements of modern high-speed electronic systems while maintaining signal integrity and reliability.
What is the High-Speed Mixed Dielectric PCB Fabrication Process?
The fabrication process for High-Speed Mixed Dielectric PCBs follows a series of steps similar to those for standard PCBs but with additional considerations to ensure the integrity of high-speed signals. Here’s an overview of the process:
- Design Preparation: Start with a detailed PCB design that includes the layer stackup, trace routing, component placement, and signal integrity analysis. Ensure that the design accounts for the use of mixed dielectric materials.
- Material Selection: Choose appropriate PCB materials with consistent electrical properties for the desired dielectric layers. This may involve selecting different laminates or prepreg materials with specific dielectric constants, loss tangents, and thicknesses.
- Prepreg and Core Preparation: Prepreg and core materials are prepared by cutting them to the required size and shape according to the PCB design specifications.
- Layer Alignment and Lamination: The prepreg layers and core layers are aligned and stacked according to the layer stackup design. The entire stack is then laminated together under high temperature and pressure to form a solid multilayered panel.
- Drilling: Precision drilling machines are used to create holes or vias in the laminated panel at specific locations according to the PCB design. These holes will later be plated to create electrical connections between layers.
- Through-hole Plating: Through-hole plating involves coating the walls of drilled holes with conductive material, typically copper, to create electrical connections between different layers of the PCB.
- Copper Plating and Etching: Copper is plated onto the surface of the panel to form the conductive traces according to the PCB design. The excess copper is then etched away, leaving behind the desired trace patterns.
- Surface Finish: The exposed copper surfaces are coated with a surface finish to protect them from oxidation and facilitate soldering during assembly. Common surface finishes include HASL (Hot Air Solder Leveling), ENIG (Electroless Nickel Immersion Gold), and OSP (Organic Solderability Preservative).
- Solder Mask Application: A solder mask is applied over the surface of the PCB, leaving only the exposed copper traces uncovered. The solder mask helps to insulate the traces and prevent solder bridges during assembly.
- Silkscreen Printing: Identifying marks, component outlines, and other information are printed onto the PCB surface using a silkscreen printing process.
- Testing and Inspection: The fabricated PCBs undergo various tests and inspections to ensure that they meet the design specifications and quality standards. This may include electrical testing, visual inspection, and dimensional measurement.
- Final Finishing: The finished PCBs are separated from the panel, cleaned, and any remaining burrs or rough edges are removed to prepare them for assembly.
Following these steps ensures that High-Speed Mixed Dielectric PCBs are fabricated to meet the stringent requirements of high-speed electronic systems while maintaining signal integrity and reliability.
How do you manufacture a High-Speed Mixed Dielectric PCB?
Manufacturing a High-Speed Mixed Dielectric PCB involves several steps similar to standard PCB manufacturing, but with specific considerations to ensure signal integrity and reliability. Here’s an overview of the manufacturing process:
- Design Preparation: Begin with a detailed PCB design that incorporates the use of mixed dielectric materials. This includes defining the layer stackup, trace routing, component placement, and signal integrity analysis. Ensure that the design meets the requirements for high-speed signals.
- Material Selection: Choose appropriate PCB materials with consistent electrical properties for different regions of the PCB. This may involve selecting laminates and prepreg materials with specific dielectric constants, loss tangents, and thermal properties suitable for high-speed applications.
- Layer Preparation: Prepare the individual layers of the PCB by cutting the laminate and prepreg materials to the required size and shape according to the design specifications.
- Layer Alignment and Lamination: Stack the prepared layers together according to the layer stackup design. The stack is then laminated under heat and pressure to bond the layers together and form a solid multilayered panel.
- Drilling: Use precision drilling machines to create holes or vias in the laminated panel at specific locations according to the PCB design. These holes will later be plated to create electrical connections between layers.
- Through-hole Plating: Coat the walls of drilled holes with conductive material, typically copper, to create electrical connections between different layers of the PCB. This may involve processes such as electroplating or chemical deposition.
- Copper Deposition and Etching: Deposit a layer of copper onto the surface of the panel to form the conductive traces according to the PCB design. Excess copper is then etched away using chemical etchants, leaving behind the desired trace patterns.
- Surface Finish: Apply a surface finish to protect the exposed copper traces from oxidation and facilitate soldering during assembly. Common surface finishes include HASL (Hot Air Solder Leveling), ENIG (Electroless Nickel Immersion Gold), and OSP (Organic Solderability Preservative).
- Solder Mask Application: Apply a solder mask over the surface of the PCB, leaving only the exposed copper traces uncovered. The solder mask helps to insulate the traces and prevent solder bridges during assembly.
- Silkscreen Printing: Print identifying marks, component outlines, and other information onto the PCB surface using a silkscreen printing process. This helps with component placement and assembly.
- Testing and Inspection: Perform various tests and inspections to ensure that the fabricated PCBs meet the design specifications and quality standards. This may include electrical testing, visual inspection, and dimensional measurement.
- Final Finishing: Separate the finished PCBs from the panel, clean them to remove any residues, and perform any final finishing processes as required.
By following these steps with careful attention to the unique requirements of high-speed mixed dielectric PCBs, manufacturers can produce boards that meet the demanding performance and reliability standards of modern electronic systems.
How much should a High-Speed Mixed Dielectric PCB cost?
The cost of a High-Speed Mixed Dielectric PCB can vary widely depending on various factors such as size, complexity, number of layers, material selection, fabrication technology, and quantity. However, due to the specialized nature of high-speed mixed dielectric PCBs, they tend to be more expensive compared to standard PCBs. Here are some factors that can influence the cost:
- Number of Layers: High-speed PCBs often require multiple layers to accommodate complex signal routing and impedance control, which increases manufacturing costs.
- Material Selection: The choice of dielectric materials, laminates, and substrates can significantly impact the cost. High-quality materials with specific electrical properties suitable for high-speed applications may be more expensive.
- Complexity of Design: PCB designs with intricate routing patterns, high-density components, and tight tolerances require more advanced manufacturing processes, which can drive up costs.
- Fabrication Technology: Advanced fabrication techniques such as laser drilling, controlled impedance routing, and sequential lamination may be necessary for high-speed mixed dielectric PCBs, adding to the overall cost.
- Quantities: Economies of scale apply to PCB manufacturing, meaning that larger production runs typically result in lower per-unit costs. Ordering in higher quantities can help reduce the cost per board.
- Lead Time: Expedited manufacturing services or shorter lead times may incur additional charges.
- Additional Processes: Specialized processes such as impedance testing, signal integrity analysis, and quality control measures may increase the overall cost.
- Supplier and Location: PCB fabrication costs can also vary depending on the chosen supplier, their capabilities, and geographical location.
It’s essential to work closely with PCB manufacturers or suppliers to obtain accurate cost estimates based on your specific design requirements and production volume. Typically, high-speed mixed dielectric PCBs are considered an investment due to their critical role in ensuring signal integrity and reliability in advanced electronic systems.
What is the High-Speed Mixed Dielectric PCB base material?
The base material used for High-Speed Mixed Dielectric PCBs typically consists of a combination of different dielectric materials, chosen to meet the specific requirements of the design. These materials are selected based on their electrical properties, thermal characteristics, and compatibility with high-speed signal transmission. Here are some common types of dielectric materials used in high-speed mixed dielectric PCBs:
- FR-4 (Flame Retardant 4): FR-4 is a widely used standard substrate material for PCBs due to its affordability and good overall performance. However, for high-speed applications, it may be used selectively or in combination with other dielectric materials.
- High-Frequency Laminates: High-frequency laminates are specifically designed for applications where signal integrity is critical. These laminates typically have lower dielectric constants, low loss tangents, and excellent dimensional stability at high frequencies. Examples include materials like Rogers Corporation’s RO4000 series, Taconic’s TLY and TLC series, and Isola’s I-Tera MT.
- Rigid-Flex Materials: In cases where flexibility is required along with high-speed performance, rigid-flex PCBs may be used. These boards incorporate both rigid and flexible substrates, often with mixed dielectric materials in the rigid sections.
- Ceramic Materials: Some high-speed applications, particularly in RF (Radio Frequency) and microwave designs, may utilize ceramic-based substrates for their superior electrical properties, such as low loss and high thermal conductivity.
- Polyimide (PI): Polyimide films, such as DuPont’s Kapton, are used in flexible PCBs and rigid-flex PCBs due to their excellent thermal and mechanical properties. They may be combined with other dielectric materials for mixed dielectric constructions.
- PTFE (Polytetrafluoroethylene): PTFE-based materials, such as Teflon, are known for their low dielectric constants, low loss tangents, and high thermal stability. They are commonly used in high-frequency and microwave applications.
The specific choice of base material depends on the performance requirements, frequency range, signal integrity considerations, and thermal management needs of the application. Designers typically evaluate the electrical properties, cost, manufacturability, and reliability of different materials to select the most suitable combination for their high-speed mixed dielectric PCB designs.
Which company makes High-Speed Mixed Dielectric PCBs?
There are many companies that produce High-Speed Mixed Dielectric PCBs, including major manufacturers such as Rogers Corporation and Taconic Advanced Dielectric Division in the United States, as well as Shengyi Technology in Japan. These companies are dedicated to researching and manufacturing high-performance PCB materials to meet the requirements of high-speed, high-frequency, and high-reliability applications.
Our company is also a professional PCB manufacturer with the capability to produce High-Speed Mixed Dielectric PCBs. We have advanced production equipment and a skilled technical team capable of customizing various complex PCB designs according to customer requirements. Here are the main advantages and capabilities of our company in producing High-Speed Mixed Dielectric PCBs:
- Professional Team: We have experienced engineers and technical personnel proficient in high-speed PCB design and manufacturing technology, able to provide customers with professional technical support and solutions.
- Advanced Equipment: We use advanced production equipment and processes, including high-precision drilling machines, automated production lines, and precise inspection equipment, to ensure the production of high-quality, reliable PCB products.
- Quality Control: We strictly adhere to international standards and quality management systems. From raw material procurement to production manufacturing, each step undergoes rigorous quality control and testing to ensure stable and reliable product quality.
- Customization Services: We can customize various types of High-Speed Mixed Dielectric PCBs according to customer-specific requirements, including different layer counts, materials, thicknesses, etc., to meet diverse application needs.
- Fast Delivery: With efficient production capacity and flexible production planning, we can promptly respond to customer orders and guarantee delivery schedules to meet urgent customer needs.
In summary, our company has the technological strength, production capacity, and service level required to produce High-Speed Mixed Dielectric PCBs. We can provide customers with high-quality, high-performance PCB products, helping them achieve greater success in the field of high-speed electronics.
What are the 7 qualities of good customer service?
Good customer service is essential for building strong customer relationships and fostering loyalty. Here are seven qualities that define good customer service:
- Responsiveness: Customers appreciate prompt responses to their inquiries, concerns, or issues. Good customer service involves acknowledging customer communication promptly and providing timely solutions or assistance.
- Empathy: Showing empathy means understanding and acknowledging the customer’s feelings, concerns, and needs. Empathetic customer service representatives listen actively, demonstrate understanding, and strive to address the customer’s emotions along with their problem.
- Clarity and Communication Skills: Clear and effective communication is crucial for delivering excellent customer service. Customer service representatives should communicate clearly, using language that the customer can understand, and provide information or instructions in a concise manner.
- Problem-Solving Skills: Good customer service involves the ability to identify and resolve customer issues effectively. Customer service representatives should be resourceful, proactive, and capable of finding solutions to problems, even in challenging situations.
- Professionalism: Professionalism encompasses traits such as politeness, respectfulness, and reliability. Customer service representatives should conduct themselves professionally at all times, maintaining a positive attitude and upholding company standards of conduct.
- Product Knowledge: Having a deep understanding of the products or services offered by the company is crucial for delivering quality customer service. Customer service representatives should be knowledgeable about the features, benefits, and usage of the products or services to provide accurate information and assistance to customers.
- Follow-up and Feedback: Good customer service doesn’t end with the resolution of an immediate issue. Following up with customers to ensure their satisfaction and seeking feedback on their experience demonstrates a commitment to continuous improvement and customer satisfaction.
By embodying these qualities, companies can create positive experiences for their customers, strengthen brand loyalty, and differentiate themselves in the competitive marketplace.
FAQs
What are High-Speed Mixed Dielectric PCBs?
High-Speed Mixed Dielectric PCBs are printed circuit boards designed for applications where signals of varying speeds and frequencies are present. They utilize multiple types of dielectric materials across the board to optimize signal integrity and performance.
What are the advantages of High-Speed Mixed Dielectric PCBs?
These PCBs offer improved signal integrity, reduced signal distortion and losses, better impedance matching, and enhanced reliability compared to standard PCBs. They are particularly suitable for high-speed digital and RF/microwave applications.
What types of dielectric materials are used in High-Speed Mixed Dielectric PCBs?
High-Speed Mixed Dielectric PCBs may incorporate a variety of dielectric materials, including FR-4, high-frequency laminates (such as Rogers or Taconic materials), polyimide, PTFE-based materials, and ceramic substrates.
How are High-Speed Mixed Dielectric PCBs fabricated?
The fabrication process involves similar steps to standard PCB manufacturing, but with additional considerations for impedance control, material selection, and signal integrity. It includes design preparation, material selection, layer preparation, lamination, drilling, plating, etching, surface finishing, and testing.
What factors affect the cost of High-Speed Mixed Dielectric PCBs?
The cost depends on factors such as size, complexity, number of layers, material selection, fabrication technology, and quantity. High-speed mixed dielectric PCBs tend to be more expensive due to the specialized materials and processes involved.
What are some design guidelines for High-Speed Mixed Dielectric PCBs?
Design guidelines include impedance control, signal integrity analysis, layer stackup design, grounding strategy, decoupling capacitor placement, routing guidelines, via design, material selection, thermal management, and documentation.
Which companies manufacture High-Speed Mixed Dielectric PCBs?
Major manufacturers include Rogers Corporation, Taconic Advanced Dielectric Division, Shengyi Technology, and other specialized PCB manufacturers with expertise in high-speed applications.
What are the key qualities of good customer service for High-Speed Mixed Dielectric PCBs?
Good customer service qualities include responsiveness, empathy, clarity and communication skills, problem-solving skills, professionalism, product knowledge, and follow-up and feedback mechanisms.