High Speed Cavity PCB Manufacturer
High Speed Cavity PCB Manufacturer,High Speed Cavity PCBs are specialized printed circuit boards engineered to meet the demanding requirements of high-frequency applications. Featuring a carefully designed cavity within the substrate, these PCBs offer superior signal integrity by minimizing electromagnetic interference and signal loss. Constructed using advanced materials such as low-loss laminates, High Speed Cavity PCBs ensure reliable performance in telecommunications, networking, radar systems, and other high-speed data transmission applications. Their precise design, controlled impedance routing, and stringent manufacturing processes make them essential components for maintaining the integrity of high-frequency signals in modern electronic systems.
What is a High Speed Cavity PCB?
A High Speed Cavity PCB (Printed Circuit Board) is a specialized type of PCB designed to accommodate high-frequency signals with minimal interference and signal loss. It’s often used in applications where data transmission speeds are critical, such as telecommunications, networking equipment, high-performance computing, and radar systems.
The term “cavity” in High Speed Cavity PCB refers to a cutout or recessed area within the PCB substrate. This cutout helps to isolate and contain electromagnetic interference (EMI) and reduces signal reflections, crosstalk, and other forms of signal degradation that can occur at high frequencies.
High Speed Cavity PCBs typically incorporate advanced materials and design techniques to achieve optimal signal integrity. These may include using specialized substrate materials with high dielectric constants, controlled impedance traces, and careful layout considerations to minimize signal distortion.
Overall, High Speed Cavity PCBs play a crucial role in maintaining the integrity and reliability of high-frequency signal transmission in electronic systems.
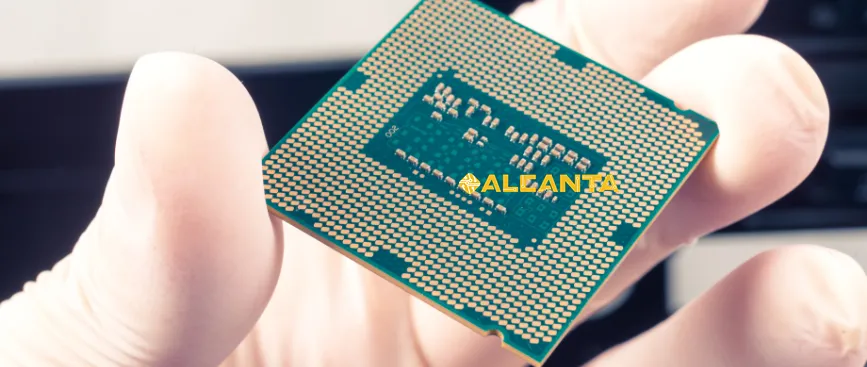
High Speed Cavity PCB Manufacturer
What are the High Speed Cavity PCB Design Guidelines?
Designing High Speed Cavity PCBs requires careful attention to various factors to ensure optimal signal integrity and performance. Here are some essential guidelines:
- Material Selection: Choose high-quality substrate materials with low dielectric constant and low loss tangent to minimize signal loss and dispersion. Common materials include FR-4, PTFE (Teflon), and specialized high-frequency laminates like Rogers or Isola.
- Cavity Design: Design the cavity dimensions and shape to match the specific requirements of the application and the desired signal frequencies. The cavity should effectively isolate sensitive signal traces from external electromagnetic interference.
- Signal Integrity: Ensure controlled impedance for signal traces to match the characteristic impedance of the transmission lines. Maintain consistent trace widths, thickness, and spacing to minimize impedance variations and signal reflections.
- Grounding: Implement a solid ground plane to provide a low-impedance return path for signals and to minimize ground loops. Proper grounding helps reduce noise and crosstalk.
- Power Distribution: Design a robust power distribution network with adequate decoupling capacitors to minimize voltage fluctuations and noise. Use multiple power and ground planes for different voltage levels and signal types.
- Component Placement: Carefully place components to minimize signal path lengths, reduce parasitic capacitance, and optimize signal integrity. Place high-speed components closer to each other to minimize interconnect lengths.
- Routing: Route high-speed signal traces as short, direct paths with minimal bends and vias to reduce signal distortion and delay. Use differential signaling for critical high-speed data paths to improve noise immunity.
- Shielding: Implement shielding techniques such as grounded copper planes or metal shielding cans to protect sensitive components and traces from electromagnetic interference.
- Thermal Management: Consider thermal management techniques to dissipate heat generated by high-speed components or high power dissipation. Ensure adequate spacing between heat-generating components and sensitive signal traces to prevent thermal interference.
- EMI/EMC Compliance: Design the PCB to comply with electromagnetic interference (EMI) and electromagnetic compatibility (EMC) regulations. Use proper filtering, shielding, and grounding techniques to minimize EMI emissions and susceptibility.
By following these guidelines and employing best practices in PCB design, engineers can create High Speed Cavity PCBs that meet the stringent requirements of high-frequency applications while ensuring reliable performance and signal integrity.
What is the High Speed Cavity PCB Fabrication Process?
The fabrication process for High Speed Cavity PCBs is similar to that of traditional PCBs but involves additional steps to create the cavity and ensure precise signal integrity. Here’s a general overview of the fabrication process:
- Design Phase:Create the PCB layout using specialized PCB design software. Pay close attention to signal integrity considerations such as controlled impedance, routing, and component placement.
- Material Selection:Choose high-quality substrate materials suitable for high-frequency applications, such as specialized laminates with low dielectric constant and low loss tangent.
- Cavity Design: Incorporate the cavity design into the PCB layout, specifying its dimensions, shape, and location within the substrate. The cavity is typically created by milling or routing away portions of the substrate material.
- Layer Stackup: Determine the layer stackup configuration based on the PCB design requirements, including the number and arrangement of signal, power, and ground planes.
- Prepreg and Core Preparation: Prepare the prepreg and core materials by cutting them to the required dimensions and applying any necessary surface treatments.
- Lamination: Assemble the PCB stackup by interleaving layers of prepreg and core materials, ensuring proper alignment of conductive layers and the cavity. The stackup is then laminated under heat and pressure to bond the layers together.
- Drilling: Drill holes for through-hole components, vias, and mounting holes using precision drilling equipment. Pay attention to drill accuracy and registration to ensure alignment with the PCB design.
- Cavity Milling/Routing: Mill or route out the cavity area in the PCB substrate using specialized CNC equipment. The cavity dimensions should match the design specifications precisely to achieve optimal signal isolation and integrity.
- Copper Plating: Deposit copper onto the substrate surfaces through processes such as electroplating or chemical deposition. This forms the conductive traces, pads, and planes according to the PCB design.
- Etching: Use chemical etching to remove excess copper from the substrate, leaving behind the desired conductive patterns defined by the PCB layout.
- Surface Finish: Apply a surface finish to protect the copper traces from oxidation and facilitate solderability. Common surface finishes include HASL (Hot Air Solder Leveling), ENIG (Electroless Nickel Immersion Gold), and OSP (Organic Solderability Preservative).
- Solder Mask Application: Apply solder mask ink over the PCB surface, leaving openings for solder pads and vias. The solder mask protects the copper traces and provides insulation between them.
- Silkscreen Printing: Optionally, apply silkscreen printing to add component labels, reference designators, and other markings to the PCB surface.
- Testing and Inspection: Conduct electrical testing and visual inspection to verify the integrity of the fabricated PCB, including continuity, impedance, and dimensional accuracy.
- Final Finishing: Cut the PCB panel into individual boards, remove any remaining burrs or residues, and perform final quality checks before packaging and shipping.
By following these steps and employing precise manufacturing techniques, manufacturers can produce High Speed Cavity PCBs with the required performance characteristics for demanding high-frequency applications.
How do you manufacture a High Speed Cavity PCB?
Manufacturing a High Speed Cavity PCB involves specialized processes to create the cavity and ensure precise signal integrity. Here’s a step-by-step guide to the manufacturing process:
- Design Phase: Develop the PCB layout using dedicated PCB design software, considering signal integrity requirements such as controlled impedance, routing, and component placement. Incorporate the cavity design into the layout, specifying its dimensions and location within the substrate.
- Material Selection: Choose high-quality substrate materials suitable for high-frequency applications, such as specialized laminates with low dielectric constant and low loss tangent. Select materials that can withstand the manufacturing processes involved in creating the cavity.
- Cavity Design: Design the cavity to match the specific requirements of the application and the desired signal frequencies. Determine the dimensions, shape, and location of the cavity within the substrate. Ensure that the cavity design provides effective isolation and containment of electromagnetic interference (EMI).
- Substrate Preparation: Prepare the substrate material by cutting it to the required size and shape. Apply any necessary surface treatments or coatings to enhance adhesion and solderability.
- Cavity Creation: Use specialized CNC equipment to mill or route out the cavity area in the substrate material. Ensure precise control over the dimensions and depth of the cavity to match the design specifications.
- Layer Stackup: Determine the layer stackup configuration based on the PCB design requirements, including the number and arrangement of signal, power, and ground planes. Prepare the prepreg and core materials for lamination.
- Lamination: Assemble the PCB stackup by interleaving layers of prepreg and core materials, ensuring proper alignment of conductive layers and the cavity. Apply heat and pressure to laminate the layers together, forming a solid composite structure.
- Drilling: Drill holes for through-hole components, vias, and mounting holes using precision drilling equipment. Ensure accurate drill registration and alignment with the PCB design.
- Copper Plating: Deposit copper onto the substrate surfaces through processes such as electroplating or chemical deposition. This forms the conductive traces, pads, and planes according to the PCB design.
- Etching: Use chemical etching to remove excess copper from the substrate, leaving behind the desired conductive patterns defined by the PCB layout. Ensure precise control over trace widths and spacing to maintain controlled impedance.
- Surface Finish: Apply a surface finish to protect the copper traces from oxidation and facilitate solderability. Common surface finishes include HASL (Hot Air Solder Leveling), ENIG (Electroless Nickel Immersion Gold), and OSP (Organic Solderability Preservative).
- Solder Mask Application: Apply solder mask ink over the PCB surface, leaving openings for solder pads and vias. The solder mask protects the copper traces and provides insulation between them.
- Silkscreen Printing:Optionally, apply silkscreen printing to add component labels, reference designators, and other markings to the PCB surface.
- Testing and Inspection: Conduct electrical testing and visual inspection to verify the integrity of the manufactured PCB, including continuity, impedance, and dimensional accuracy.
- Final Finishing: Cut the PCB panel into individual boards, remove any remaining burrs or residues, and perform final quality checks before packaging and shipping.
By following these steps and employing precise manufacturing techniques, manufacturers can produce High Speed Cavity PCBs with the required performance characteristics for demanding high-frequency applications.
How much should a High Speed Cavity PCB cost?
The cost of a High Speed Cavity PCB can vary significantly depending on several factors, including the complexity of the design, the size of the board, the materials used, the manufacturing processes involved, and the quantity ordered.
Here are some factors that can influence the cost:
- Complexity of Design: More complex designs with intricate routing, multiple layers, and tight tolerances will generally incur higher costs due to the increased manufacturing difficulty and time required.
- Material Selection: Specialized materials such as high-frequency laminates or exotic substrates can be more expensive than standard FR-4. These materials offer superior performance at high frequencies but come at a higher cost.
- Manufacturing Processes: Processes such as cavity creation, controlled impedance routing, and high-precision drilling may require specialized equipment and skilled labor, contributing to higher manufacturing costs.
- Quantity: Bulk orders typically result in lower unit costs due to economies of scale. Ordering larger quantities of High Speed Cavity PCBs can help reduce the cost per board.
- Additional Features: Extra features such as surface finishes, silkscreen printing, gold plating, or special testing requirements will add to the overall cost.
- Supplier and Location: Different PCB manufacturers may offer varying pricing based on their capabilities, location, and production volume.
As a rough estimate, the cost of a High Speed Cavity PCB can range from tens to hundreds of dollars per board for low to medium volume production, while larger quantities may bring the cost down to a few dollars per board. It’s essential to obtain quotes from multiple suppliers and consider the trade-offs between cost, quality, and lead time when selecting a manufacturer for High Speed Cavity PCBs.
What is the High Speed Cavity PCB base material?
The base material used for High Speed Cavity PCBs is typically a specialized laminate designed to meet the requirements of high-frequency applications. These laminates are engineered to have specific electrical and mechanical properties to ensure optimal signal integrity and performance. Some common base materials used for High Speed Cavity PCBs include:
- Rogers Corporation’s RO4000 Series: This series of high-frequency laminates offers excellent electrical performance, low dielectric loss, and tight dimensional stability. It’s widely used in applications requiring high-speed digital and RF/microwave performance.
- Isola’s ISpeed:ISpeed is a high-performance laminate specifically designed for high-speed digital applications. It offers low dielectric constant, low dissipation factor, and excellent signal integrity at high frequencies.
- Taconic’s TLY-5A: TLY-5A is a PTFE-based (Polytetrafluoroethylene) laminate known for its low loss tangent and stable electrical properties over a wide range of frequencies. It’s suitable for high-frequency RF and microwave circuits.
- DuPont’s Pyralux: Pyralux is a flexible laminate material that can be used for High Speed Cavity PCBs in applications where flexibility or conformal shaping is required. It offers good electrical performance and can be used in applications such as wearable electronics and aerospace.
- Arlon’s AD Series: Arlon’s AD Series laminates are designed for high-frequency applications requiring high thermal performance and reliability. They offer low dielectric loss, low moisture absorption, and excellent thermal conductivity.
These base materials often consist of a substrate layer (typically fiberglass-reinforced epoxy or PTFE) combined with copper foil layers for conductive traces and planes. The specific choice of base material depends on factors such as the frequency range, signal speed, thermal management requirements, and cost considerations for the particular application.
Which company makes High Speed Cavity PCBs?
High Speed Cavity PCBs are typically manufactured by specialized companies dedicated to producing high-performance PCB materials. Some of the companies that manufacture High Speed Cavity PCBs include Rogers Corporation, Isola, Taconic, DuPont, and others. These companies focus on developing and producing advanced PCB materials to meet the stringent requirements of high-frequency applications for signal integrity and performance.
As a manufacturer, our company is also capable of producing High Speed Cavity PCBs. We have advanced manufacturing equipment and a skilled team of technicians capable of meeting the customized needs of our customers for high-speed PCBs. Our manufacturing processes include precision lamination, high-precision drilling, meticulous cavity machining, and other steps to ensure that each PCB exhibits excellent signal integrity and reliability.
We prioritize quality management and adhere to strict quality control standards and inspection procedures to ensure that the High Speed Cavity PCBs we produce meet our customers’ specifications and performance requirements. Moreover, we are committed to continuous innovation and improvement to enhance product quality and technological capabilities, catering to the growing demands of our customers.
Whether in telecommunications, networking equipment, high-performance computing, or radar systems, our High Speed Cavity PCBs can provide reliable solutions to our customers. We are willing to collaborate with customers to develop customized high-speed PCB products, contributing to the success and advancement of their applications.
What are the 7 qualities of good customer service?
Good customer service is characterized by several key qualities that help to foster positive relationships with customers and ensure their satisfaction. Here are seven qualities of good customer service:
- Responsiveness: Good customer service involves being prompt and responsive to customer inquiries, requests, and concerns. Customers appreciate timely assistance and expect quick resolution of their issues.
- Empathy: Empathy is the ability to understand and share the feelings of others, including customers. Good customer service representatives demonstrate empathy by actively listening to customers, acknowledging their concerns, and showing genuine concern for their needs and experiences.
- Clarity and Communication: Clear and effective communication is essential for good customer service. Customer service representatives should communicate information clearly, using language that is easy to understand and free of jargon. They should also be attentive to customers’ communication preferences and adapt their communication style accordingly.
- Problem-solving skills: Good customer service involves the ability to effectively address customer problems and find solutions to their issues. Customer service representatives should be resourceful, knowledgeable about products or services, and capable of resolving customer concerns in a timely and satisfactory manner.
- Professionalism: Professionalism is essential in providing good customer service. Customer service representatives should maintain a professional demeanor at all times, remaining courteous, respectful, and composed, even in challenging situations.
- Consistency:Consistency is key to providing a positive customer service experience. Customers expect consistent service across different channels and interactions with a company. Good customer service involves maintaining consistent standards, policies, and practices to ensure a uniform customer experience.
- Follow-up and feedback: Good customer service doesn’t end with resolving a customer’s immediate issue. It also involves following up with customers to ensure their satisfaction and seeking feedback to continuously improve service quality. Customer service representatives should proactively follow up with customers after resolving their concerns and encourage them to provide feedback on their experience.
By embodying these qualities, businesses can build strong relationships with their customers, foster loyalty, and differentiate themselves in the marketplace through exceptional customer service.
FAQs
What are High Speed Cavity PCBs?
High Speed Cavity PCBs are specialized printed circuit boards designed to accommodate high-frequency signals with minimal interference and signal loss. They feature a cavity or cutout in the substrate to isolate and contain electromagnetic interference (EMI) and maintain signal integrity.
What are the advantages of High Speed Cavity PCBs?
High Speed Cavity PCBs offer several advantages, including improved signal integrity, reduced electromagnetic interference, lower signal loss, and better performance at high frequencies. They are ideal for applications requiring high-speed data transmission, such as telecommunications, networking equipment, and radar systems.
How are High Speed Cavity PCBs different from traditional PCBs?
High Speed Cavity PCBs differ from traditional PCBs primarily in their design and construction. They feature a cavity or recessed area within the substrate to isolate sensitive signal traces, whereas traditional PCBs do not typically incorporate such features.
What materials are used in High Speed Cavity PCBs?
High Speed Cavity PCBs are typically made using specialized laminates with low dielectric constant and low loss tangent to minimize signal loss and distortion. Common materials include FR-4, PTFE (Teflon), and high-frequency laminates such as Rogers or Isola.
What factors should be considered when designing High Speed Cavity PCBs?
When designing High Speed Cavity PCBs, factors such as controlled impedance, routing, grounding, thermal management, and electromagnetic compatibility (EMC) should be carefully considered to ensure optimal signal integrity and performance.
How are High Speed Cavity PCBs manufactured?
The manufacturing process for High Speed Cavity PCBs involves specialized techniques such as cavity creation, controlled impedance routing, and precision drilling. Advanced materials and manufacturing equipment are used to ensure the desired performance characteristics of the PCBs.
What are the applications of High Speed Cavity PCBs?
High Speed Cavity PCBs are used in a variety of high-frequency applications, including telecommunications infrastructure, networking equipment, high-performance computing, radar systems, and aerospace electronics, where maintaining signal integrity is critical.