High precision packaging substrate Manufacturer
High Precision Packaging Substrate Manufacturer,High Precision Packaging Substrate is a crucial component in semiconductor manufacturing, featuring exacting standards for precision and accuracy. These substrates offer meticulous alignment and fine-tuned electrical pathways, ensuring reliable performance in high-frequency applications. Comprising multiple layers of high-quality materials, including insulators and conductors, High Precision Packaging Substrates facilitate optimal signal transmission and efficient heat dissipation. Their advanced manufacturing processes enable tight tolerances and uniformity, essential for demanding electronic devices. These substrates find applications in aerospace, telecommunications, and medical industries, where precision and reliability are paramount. High Precision Packaging Substrates drive advancements in semiconductor packaging, enabling cutting-edge technology solutions.
A “High Precision Packaging Substrate” stands as a pivotal component in the intricate process of assembling integrated circuits (ICs), holding a crucial role in the intricate dance of manufacturing electronic devices, especially within the microelectronics sphere.
These substrates are engineered with the primary goal of providing indispensable support for the physical encapsulation and intricate interconnection of ICs. Their mission is to ensure the seamless operation and unwavering performance of these circuits. To achieve this, these substrates often harness advanced materials and cutting-edge manufacturing techniques, meeting the contemporary demands of electronic devices – think compact form factors, elevated performance benchmarks, and a commitment to superior energy efficiency.
Throughout the meticulous design and manufacturing stages of high precision packaging substrates, engineers are focused on attaining precision in circuit layouts, orchestrating densely interconnected networks, optimizing heat dissipation strategies, and engineering adaptability to tackle the unpredictable challenges posed by diverse environmental conditions. This thorough approach is the linchpin, ensuring that ICs remain steadfast in stability, operational efficiency, and reliability across a spectrum of dynamic use cases.
As electronic devices persist in their pursuit of sleeker dimensions, heightened performance thresholds, and advanced functionalities, the demand for high precision packaging substrates continues its ascent. The evolution of these substrates isn’t merely a response to the relentless march of semiconductor technology; it’s also a reflection of the ceaseless quest within the electronic market for devices that are not just advanced but also unfailingly reliable. In essence, high precision packaging substrates wield a profound influence in steering the ship of technological innovation and propelling the trajectory of product advancement within the dynamic landscape of the electronics industry.
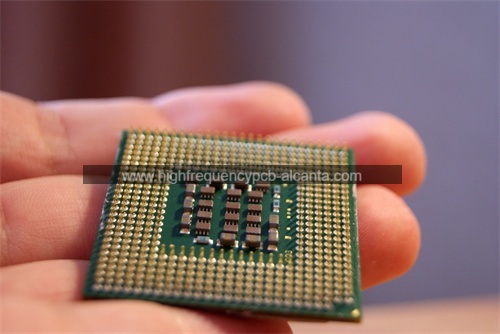
High Precision Packaging Substrate Manufacturer
What are the Functions of High Precision Packaging Substrate?
Step into the intricate world of electronic devices, where the spotlight gracefully falls upon high precision packaging substrates. These unassuming components transcend their silent roles, becoming the architects orchestrating a meticulously choreographed performance within the realms of integrated circuits (ICs) and the dynamic field of microelectronics. Their functions, like a well-composed symphony, extend beyond the surface, weaving a narrative critical to the seamless operation of electronic devices:
Safeguards of Circuit Integrity: Envision high precision packaging substrates as vigilant custodians, erecting an impenetrable fortress around integrated circuits. This protective barrier shields against environmental adversaries—moisture, dust, and contaminants—preserving the sanctity and integrity of the circuits.
Conductors of Electrical Harmony: Behind the scenes, these substrates metamorphose into conductors, guiding a sophisticated symphony of electrical connections between integrated circuits and other components. Their expertise lies in facilitating a harmonious and reliable communication dance within the intricate electronic ensemble.
Harmonizers of Thermal Equilibrium: Armed with thermal finesse, these substrates engage in the delicate art of heat dissipation from integrated circuits. This finesse acts as an elixir, preventing overheating and contributing to the sustained performance and endurance of electronic components.
Sentinels of Signal Purity: High precision packaging substrates stand as meticulous sentinels, ensuring the purity of signals. Through precise circuit layouts and high-density connections, they minimize signal loss and interference, allowing for an uninterrupted flow of information.
Architects of Compact Brilliance: Embracing the rhythm of miniaturization, these substrates evolve into architects of compact brilliance. Their ability to elegantly accommodate multiple functions within a confined space significantly contributes to the overarching trend of downsizing device dimensions.
EMI Custodians: Some substrates take on the role of custodians against electromagnetic interference (EMI). Equipped with features to mitigate interference, they ensure that electronic devices not only comply with regulatory standards but also operate in serene harmony without disruptions from or to other electronic devices.
Guardians of Reliability: High precision packaging substrates emerge as silent guardians of reliability. Crafted to endure a myriad of environmental challenges, withstand mechanical strains, and navigate the ebb and flow of temperature variations, these substrates assure a steadfast and reliable performance that remains unwavering across the entire lifespan of the device.
Harmonious Integration with Cutting-edge Materials:Embracing avant-garde materials, these substrates effortlessly merge with the forefront of semiconductor technologies. This flexibility facilitates the smooth assimilation of cutting-edge components, thereby laying the foundation for the evolution of electronic devices marked by exceptional performance.
In essence, high precision packaging substrates become the virtuoso conductors orchestrating the symphony of electronic devices, seamlessly adapting to the ever-evolving demands and advancements within the dynamic and enchanting landscape of the electronics industry.
What are the Different Types of High Precision Packaging Substrate?
Diverse categories of high precision packaging substrates cater to specific needs within the electronics domain. Each type is meticulously designed to meet particular requirements, offering a range of applications in the ever-evolving landscape of electronic devices:
Ceramic Marvels: Ceramic substrates stand out for their remarkable thermal conductivity and stability. Primarily employed in high-power scenarios, such as power amplifiers and high-frequency circuits, these substrates excel in managing heat.
Organic Packages: Crafted from materials like epoxy or Bismaleimide Triazine (BT), organic substrates emerge as lightweight and cost-effective solutions. Widely embraced in consumer electronics like smartphones and tablets, these substrates balance efficiency with economic viability.
Metal Core Wonders (MCPCB): Metal core substrates, often rooted in aluminum or copper, shine in applications where efficient heat dissipation is paramount. Their role extends to sectors like LED lighting, automotive electronics, and power electronics.
Ceramic-Polymer Hybrids: Blending the strengths of ceramics and polymers, these hybrids strike a harmonious chord between thermal performance and cost efficiency. Applications span from RF modules to power devices, showcasing versatility.
Glass Elegance: Glass substrates, known for dimensional stability, find their niche in precision-centric applications. From sensor manufacturing to the creation of MEMS, these substrates bring a touch of finesse.
Flexibility Unleashed: Flexible substrates, fashioned from materials like polyimide, find their place in the realm of bendable and wearable electronics. In applications where rigidity takes a back seat, these substrates lead the charge.
LTCC (Low-Temperature Co-fired Ceramic) Marvels: Exhibiting ceramic prowess, LTCC substrates facilitate the co-firing of multiple layers at lower temperatures. They find their stride in RF and microwave applications, where exceptional electrical properties are non-negotiable.
SiP (System-in-Package) Artistry: SiP substrates redefine integration by seamlessly melding various components into a unified package. From ICs to passive components, this substrate variety optimizes performance and minimizes the footprint of electronic devices.
Interposer Maestros: Interposers emerge as interface virtuosos, bridging the gap between diverse semiconductor devices. Their role is pivotal in advanced packaging realms like 2.5D and 3D packaging, enhancing connectivity and overall performance.
These diverse high precision packaging substrates embody adaptability, addressing unique thermal, electrical, and mechanical demands across a spectrum of electronic applications.
What is the Relationship Between High Precision Packaging Substrate and IC Packaging?
Immerse yourself in the intricate relationship between high precision packaging substrates and IC (Integrated Circuit) packaging, where their synergy forms the backbone of seamless integration and optimal performance in electronic devices. This intricate connection unfolds through a myriad of crucial facets:
Circuit Choreography: High precision packaging substrates take center stage as the canvas for orchestrating the integration of ICs into a unified and protected environment. They provide a robust foundation for mounting and interconnecting IC components, ensuring meticulous alignment and reliable electrical connections.
Electrical Harmony: Serving as conduits for electrical signals, substrates contribute significantly to maintaining the symphony of signal integrity. The precision and sophistication of the substrate’s circuitry play a pivotal role in minimizing signal loss and elevating the overall electrical performance of the IC.
Thermal Ballet: The graceful dance of heat dissipation is paramount for the IC’s optimal function and durability. High precision substrates, adorned with thermal management features, elegantly perform the ballet of dissipating heat, preventing overheating, and keeping the IC within the bounds of optimal temperatures.
Guardians of Purity: Beyond electrical considerations, substrates emerge as guardians enveloping the IC, shielding it from environmental adversaries such as moisture, dust, and contaminants. This protective embrace is fundamental in preserving the IC’s integrity and ensuring unwavering reliability across diverse operational conditions.
Size Poetry: In the poetry of miniaturization, high precision substrates take on a leading role. Their ability to gracefully accommodate intricate circuit layouts within confined spaces is instrumental in meeting the demands of modern technology, where devices continually shrink in size.
Material Fusion: The compatibility of high precision substrates with an array of materials used in IC packaging is akin to a harmonious fusion. This compatibility ensures a seamless integration process, elevating the overall reliability of the packaged IC.
Technological Duet: The evolution of advanced packaging technologies, such as System-in-Package (SiP) and 3D packaging, necessitates a synchronized duet with high precision substrates. These technologies, involving the intricate integration of multiple components, rely on substrates to facilitate this sophisticated dance of miniaturization and complexity.
In essence, high precision packaging substrates and IC packaging engage in a dance of mutual influence, where progress in one realm propels the need for sophistication in the other, and vice versa. Together, they compose the symphony that propels the development of smaller, more potent, and reliable electronic devices.
What Sets High Precision Packaging Substrate Apart from Ordinary PCBs?
Embark on a journey through the intricacies of electronic craftsmanship, where high precision packaging substrates emerge as distinct virtuosos, setting themselves apart from the conventional notes of ordinary PCBs (Printed Circuit Boards). In this symphony of technological evolution, these substrates showcase a unique set of characteristics:
Precision Choreography: High precision substrates are the choreographers of precision, meticulously designed with tight tolerances to ensure flawless alignment and component placement. In applications where precision is paramount, these substrates take center stage, while ordinary PCBs may not dance to the same refined tune.
Material Alchemy: The substrates engage in a sophisticated alchemy of materials, weaving ceramics, metal-core blends, or hybrid compositions to elevate thermal conductivity, stability, and reliability. This material mastery caters specifically to the demands of high-performance applications, distinguishing them from the more commonplace materials used in ordinary PCBs.
Thermal Waltz: High precision substrates perform a graceful waltz with heat, excelling in applications where electronic components generate significant warmth. This thermal finesse sets them apart in high-power or thermally challenging environments, an arena where ordinary PCBs may not dance with the same level of sophistication.
Signal Sonata: In the symphony of high-frequency and high-speed applications, maintaining signal integrity is a virtuoso sonata. High precision substrates compose intricate circuit layouts and shielding techniques to minimize signal loss and interference, standing out from the more standard designs of ordinary PCBs.
Environmental Guardians: These substrates become guardians, offering advanced protection against environmental elements that could compromise integrated circuits. This level of environmental fortification is indispensable, setting them apart from ordinary PCBs that may not provide the same shield against the elements.
Complexity Ballet: High precision substrates gracefully perform a complexity ballet, accommodating intricate circuit designs and multiple layers with finesse. This flexibility shines in advanced packaging technologies like System-in-Package (SiP) or 3D packaging, where ordinary PCBs may struggle to execute the intricate dance of layer count and complexity.
Tailored Symphony: Crafted as bespoke creations, high precision substrates find their place in specific applications that demand heightened performance, reliability, and precision. Industries such as aerospace, telecommunications, medical devices, and high-performance computing become their stage, a realm where ordinary PCBs may not be able to play the same tune.
In summary, high precision packaging substrates emerge as the maestros of electronic design, conducting a symphony of sophistication that transcends the capabilities of ordinary PCBs. Their meticulous design and advanced features position them as indispensable players in the grand performance of high-performance electronic systems.
What are the Main Structure and Production Technologies of High Precision Packaging Substrate?
Embark on a journey into the intricacies of high precision packaging substrate architecture and production technologies, where precision and advanced methodologies converge to shape the foundation of cutting-edge electronic components:
Main Structure:
Foundation Material:
Diverse materials set the stage, with ceramics like aluminum oxide and aluminum nitride providing robust thermal conductivity, while organic options such as epoxy or Bismaleimide Triazine offer a lighter and cost-effective alternative. Metal core substrates, often aluminum or copper-based, step in for superior heat dissipation.
Insulating Layers:
An intricate dance of multiple dielectric layers unfolds, serving as the substrate’s insulating core. These layers contribute not only to electrical insulation but also define the substrate’s electrical properties.
Pathways of Conductivity:
Precision takes center stage with the delicate dance of conductive traces intricately patterned to minimize signal loss. These pathways form the lifeline, carrying electrical signals with finesse.
Mounting Haven:
An allocated region becomes a haven for mounting integrated circuits (ICs) and electronic components. The layout is meticulously designed, ensuring a symphony of alignment and connectivity.
Surface Elegance:
The surface, adorned with gold, tin, or solder mask finishes, becomes an elegant canvas for the intricate art of soldering, a crucial step in the substrate’s functionality.
Guardians of Integrity:
A protective layer or encapsulation becomes the guardian, shielding components from environmental elements. This shield ensures reliability and longevity in the face of diverse environmental challenges.
Production Technologies:
Substrate Genesis:
The substrate’s journey commences with precision machining or laser cutting for ceramics, and sophisticated lamination processes for organic counterparts, setting the foundation for what’s to come.
Ink of Connectivity:
Conductive traces are painted onto the substrate through advanced printing techniques like screen printing, inkjet printing, or the meticulous art of photolithography, each demanding a brushstroke of precision.
Dielectric Symphony:
Layers of dielectric material emerge through the poetic movements of chemical vapor deposition (CVD) or physical vapor deposition (PVD), contributing layers of insulation and electrical harmony.
Component Ballet:
Component mounting unfolds as a ballet of surface mount technology (SMT) or through-hole technology (THT), where electronic components pirouette into their designated spaces, engaging in a dance of connectivity.
Ephemeral Encapsulation:
The final act, encapsulation, is unveiled with processes like conformal coating or molding, ensuring the substrate’s resilience against the ephemeral forces of the environment.
Quality Overture:
Rigorous quality control measures conduct an overture, testing the substrate’s electrical conductivity, thermal properties, and dimensional accuracy, ensuring that each component performs in harmony.
Advanced Packaging Choreography:
For specific applications, a choreography of advanced packaging technologies such as System-in-Package (SiP) or 3D packaging takes center stage, seamlessly integrating multiple components into a cohesive performance.
Material Alchemy Reflection:
The choice of materials, a reflection of alchemy throughout the production process, becomes a critical consideration, ensuring the substrate’s compatibility and desired properties.
In essence, the architecture and production technologies of high precision packaging substrates unfold as a symphony of precision and technological finesse, crafting the backbone of advanced electronic components.
Frequently Asked Questions (FAQs)
What is a high precision packaging substrate, and what role does it play in electronic devices?
A high precision packaging substrate is a specialized component used in electronic devices. It serves as a foundation for mounting and connecting integrated circuits (ICs) and other electronic components. Its role is crucial in providing a stable platform, ensuring precise alignment, and facilitating efficient electrical connections.
What distinguishes high precision packaging substrates from standard PCBs (Printed Circuit Boards)?
High precision packaging substrates differ from standard PCBs in terms of their materials, tolerances, and advanced features. They are crafted with tighter tolerances, often using advanced materials like ceramics or metal-core compositions. These substrates excel in thermal management, signal integrity, and environmental protection, making them suitable for high-performance applications.
What industries commonly use high precision packaging substrates?
High precision packaging substrates find applications in industries where reliability, precision, and high performance are paramount. These include aerospace, telecommunications, medical devices, high-performance computing, and other advanced electronic systems.
How are high precision packaging substrates manufactured?
The manufacturing process involves several steps, including substrate formation, circuit printing, dielectric layer deposition, component mounting, surface finishing, encapsulation, and quality control. Precision machining, advanced printing technologies, and specific material deposition techniques contribute to the intricate manufacturing process.
What are the key considerations when choosing a high precision packaging substrate manufacturer?
When selecting a manufacturer, factors such as experience, quality certifications, production capabilities, material expertise, and adherence to industry standards should be considered. The manufacturer’s ability to meet specific application requirements, provide customization options, and offer reliable technical support are also essential considerations.
Can high precision packaging substrates be customized for specific applications?
Yes, many manufacturers offer customization options for high precision packaging substrates. This includes tailoring the substrate’s material composition, dimensions, and features to meet the specific requirements of the intended application.
What is the typical lead time for high precision packaging substrate production?
Lead times can vary depending on factors such as order quantity, customization requirements, and the complexity of the substrate. Manufacturers often provide estimated lead times based on project specifications.
How can I ensure the reliability of high precision packaging substrates in my electronic device?
Ensuring reliability involves selecting a reputable manufacturer with a track record of producing high-quality substrates. Additionally, adherence to proper handling and installation practices, as well as compliance with recommended operating conditions, contributes to the overall reliability of the electronic device.
Are high precision packaging substrates compatible with advanced packaging technologies like System-in-Package (SiP) or 3D packaging?
Yes, high precision packaging substrates are often compatible with advanced packaging technologies. They play a crucial role in facilitating the integration of multiple components in compact and complex configurations, making them suitable for SiP, 3D packaging, and other advanced assembly techniques.
How do I request a quote or inquire about high precision packaging substrates from a manufacturer?
Most manufacturers provide contact information on their websites for inquiries and quoting. Reach out to them with details about your specific requirements, and they will typically respond with information regarding pricing, lead times, and other relevant details.
Conclusion
In wrapping up our exploration of high precision packaging substrates, we find ourselves immersed in a realm where technology meets artistry. These substrates, often unsung heroes in the electronic landscape, weave a narrative of sophistication, reliability, and precision.
Setting the stage for integrated circuits and electronic components, high precision packaging substrates elevate the standards in applications where perfection is not just desired but essential. Their distinction from standard PCBs becomes evident in the dance of materials, the intricacy of design, and the prowess in handling diverse challenges.
The manufacturing odyssey of these substrates is akin to a symphony, where each step plays a unique role in the creation of a technological masterpiece. From the initial substrate formation to the final encapsulation, precision is the guiding principle, ensuring that these components meet the demanding requirements of modern electronic systems.
Selecting a manufacturer becomes an art in itself, requiring a discerning eye for experience, certifications, and customization capabilities. The collaboration with a reputable manufacturer is not just a transaction but a partnership that ensures the reliability and quality of these substrates.
As high precision packaging substrates continue to evolve, their compatibility with advanced packaging technologies opens doors to new possibilities. They seamlessly integrate into the complex choreography of modern electronics, providing tailored solutions for applications that demand nothing short of excellence.
In essence, these substrates emerge as the conductors of electronic symphonies, orchestrating a harmonious blend of technology and precision. Their meticulous craftsmanship and advanced features position them as unsung virtuosos, playing a pivotal role in the grand composition of high-performance electronic systems, shaping the trajectory of technological innovation.