High Frequency Package Substrate Manufacturer
High Frequency Package Substrate Manufacturer,High Frequency Package Substrate is a specialized component designed for optimal performance in high-frequency electronic applications. These substrates feature materials and construction techniques tailored to minimize signal loss and interference, ensuring reliable transmission of high-frequency signals. Comprising multiple layers of high-quality materials such as specialized dielectrics and conductors, High Frequency Package Substrates offer precise impedance control and minimal crosstalk. Their design supports efficient heat dissipation, maintaining signal integrity even under demanding conditions. Used in telecommunications, aerospace, and radar systems, High Frequency Package Substrates are essential for achieving high-speed data transmission and maintaining system reliability in critical applications.
A High-Frequency Package Substrate takes center stage in the realm of electronics, strategically crafted to facilitate the smooth transmission of high-frequency signals and meet the intricate demands of radio frequency (RF) applications. Its significance becomes notably pronounced in cutting-edge communication and radar systems, empowering devices to adeptly manage signals at heightened frequencies, thereby amplifying overall performance and data transfer rates.
This substrate leverages state-of-the-art materials and manufacturing techniques to establish a reliable environment characterized by low signal loss and minimal crosstalk—a fundamental requirement for transmitting electrical signals in high-frequency scenarios. Commonly employed materials for these substrates include polytetrafluoroethylene (PTFE), RO4003C, and RO4350B, celebrated for their exceptional dielectric constants and low-loss characteristics, making them well-suited for RF and microwave applications.
The design process for high-frequency package substrates involves meticulous considerations, encompassing effective heat dissipation, electromagnetic compatibility, and achieving precise impedance matching to ensure the accurate transmission of signals. The incorporation of design elements such as microstrip lines, apertures, and metal layers becomes paramount to meet specific electrical and mechanical requirements.
In essence, the High-Frequency Package Substrate emerges as a linchpin in optimizing the functionality of electronic devices, particularly in the dynamic landscape of modern communication and radar systems, where adept processing of high-frequency signals takes precedence.
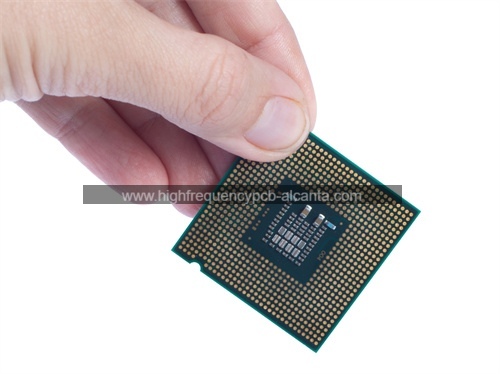
High Frequency Package Substrate Manufacturer
What functions does High-Frequency Package Substrate serve?
Within the intricate landscape of electronic systems, the High-Frequency Package Substrate assumes a central role, particularly adept at navigating the complexities associated with managing high-frequency signals. Let’s explore its primary functions:
Facilitating Seamless Signal Transmission: Fundamentally, the substrate establishes an environment that fosters the seamless transmission of high-frequency signals. Its design intricacies are finely tuned to minimize signal loss, ensuring the transmitted signals maintain resilience and reliability.
Ensuring Precision in Impedance Matching: Maintaining optimal impedance matching assumes a pivotal role, acting as a linchpin for the precise operation of the electronic circuit. This paramount task ensures that the circuit functions with meticulous accuracy, mitigating signal distortions and reflections. In doing so, it significantly enhances the overall precision and accuracy of signal communication.
Enhancing Electromagnetic Compatibility (EMC): Recognizing the inherent vulnerability of high-frequency circuits to electromagnetic interference, the substrate undergoes meticulous engineering to elevate EMC. This mitigates the risk of interference from external sources and prevents crosstalk among diverse components on the board.
Strategic Heat Dissipation: Acknowledging the challenges posed by heat in high-frequency applications, the substrate incorporates designs that facilitate efficient heat dissipation. This feature is indispensable for sustaining the stability and longevity of electronic components.
Discerning Dielectric Properties: The substrate material is carefully curated to impart specific dielectric properties. Optimal insulation and support for high-frequency signals are achieved through materials featuring low dielectric constants and minimal losses.
Providing Robust Mechanical Support: Beyond its electrical functions, the substrate serves as a stalwart mechanical support for the components it houses. This structural integrity is vital, enabling the system to withstand diverse environmental conditions and handling with resilience.
Tailored Excellence for RF and Microwave Applications: The High-Frequency Package Substrate is meticulously designed for RF and microwave applications, where stringent standards for signal integrity and minimal losses are non-negotiable. This encompasses a broad spectrum of applications, including wireless communication, radar systems, and satellite communication.
In essence, the High-Frequency Package Substrate emerges as a versatile linchpin, ensuring not only the efficient transmission of high-frequency signals but also addressing critical considerations related to impedance matching, electromagnetic compatibility, heat dissipation, and mechanical support across a diverse array of electronic applications.
What are the different types of High-Frequency Package Substrate?
High-Frequency Package Substrates manifest in diverse types, finely tuned to address the nuanced demands of electronic applications, particularly those immersed in high-frequency signals. Here’s a panorama of the varied types:
Rigid-Flex Substrates: A harmonious fusion of flexibility and rigidity, these substrates prove their mettle in compact spaces and scenarios that demand a marriage of bending and flexibility.
Microstrip Substrates: With a slender dielectric layer nestled between a conductive trace and a ground plane, these substrates shine in the realms of microwave and RF applications, boasting low signal loss and controlled impedance.
Stripline Substrates: Embracing a conductive trace cocooned between two dielectric layers, flanked by ground planes, stripline substrates carve a niche in high-frequency and microwave applications, providing isolation and reliability.
Coplanar Waveguide Substrates: Featuring a conductor strip amidst ground planes on either side, these substrates cater to microwave and millimeter-wave landscapes, ensuring controlled impedance and minimal radiation loss.
Multilayer High-Frequency PCBs: Layered intricately with conductive traces and dielectric layers, these substrates elevate the bar for signal integrity, making them apt for intricate high-frequency designs.
Ceramic Substrates: Crafted from materials like alumina or aluminum nitride, ceramic substrates flaunt stellar thermal conductivity and stability, earning their stripes in RF and microwave circuits.
PTFE-Based Substrates: Harnessing the prowess of materials like polytetrafluoroethylene (PTFE), exemplified by Rogers RO4003C, these substrates flaunt low dielectric constant and loss, tailor-made for high-frequency and microwave applications.
Liquid Crystal Polymer (LCP) Substrates: At the intersection of high-frequency performance, low loss, and stellar dimensional stability, LCP substrates find a home in wireless communication and high-speed data transfer realms.
Metal Core PCBs (MCPCBs): Flaunting a metal core, typically aluminum, MCPCBs take the lead in efficient heat dissipation, finding their calling in high-power and high-frequency landscapes.
RF Integrated Passive Devices (IPDs): Unveiling a realm of integration, these specialized substrates weave passive components seamlessly within, stepping into the limelight for compact RF designs.
Choosing the right High-Frequency Package Substrate becomes an art, a thoughtful consideration driven by specific application needs, encompassing factors like frequency range, thermal dynamics, mechanical flexibility, and the overarching performance narrative.
How is High-Frequency Package Substrate related to IC packaging?
The relationship between High-Frequency Package Substrate and IC (Integrated Circuit) packaging is akin to a well-orchestrated symphony in the realm of electronics, especially when orchestrating the intricacies of cutting-edge electronic devices. Unraveling this intricate dance reveals the symbiotic connection:
Conduit for Signal Symphony:
High-Frequency Package Substrate: Serving as the stage for mounting integrated circuits, the substrate plays a pivotal role in conducting the seamless transmission of high-frequency signals within the electronic ensemble.
IC Packaging: As the grand enclosure for integrated circuits, the packaging harmonizes the pathways, allowing signals to dance gracefully between different components of the IC, orchestrating effective communication and operational brilliance.
Mechanical Ballet and Fusion:
High-Frequency Package Substrate: Beyond its electrical duties, the substrate assumes the role of a choreographer, providing robust mechanical support for ICs and other components, ensuring their seamless integration into a choreographed masterpiece.
IC Packaging: Like a protective ballet, the packaging envelopes ICs, shielding them from external elements and forming a resilient physical structure. The substrate within the IC package waltzes intricately, supporting the integration of semiconductor devices with poise and endurance.
Heat Pas de Deux:
High-Frequency Package Substrate: Acknowledging the significance of thermal grace in high-frequency applications, the substrate’s design incorporates features to perform an elegant pas de deux, effectively dissipating the heat pirouettes generated by electronic components.
IC Packaging: In tandem with the substrate, IC packaging joins the thermal dance. Heat dissipation features within the package execute a choreography that prevents overheating, maintaining the optimal temperature for the integrated circuits to perform their ballet.
Electromagnetic Harmony (EMC):
High-Frequency Package Substrate: The substrate’s design is a conductor in the electromagnetic symphony, minimizing interference and signal distortions in the high-frequency crescendo.
IC Packaging: EMC considerations dance gracefully within IC packaging, where shielding and grounding perform an intricate ballet, creating a controlled environment that harmonizes the risk of electromagnetic interference.
Dielectric Sonata:
High-Frequency Package Substrate: The substrate material is a soloist, chosen meticulously for its dielectric properties that influence the sonata of insulation and support for high-frequency signals.
IC Packaging: The dielectric properties within IC packaging, including the substrate, compose a sonnet critical for maintaining the integrity of the signal melody and preventing crosstalk dissonance.
In essence, while the High-Frequency Package Substrate leads the orchestra in crafting an optimal environment for high-frequency signal transmission, IC packaging joins the ensemble, contributing to a more extensive composition that includes protection, mechanical grace, thermal rhythm, and electromagnetic harmony. The substrate emerges as a virtuoso within the IC package, ensuring a harmonious performance and reliability of electronic systems, especially in domains that demand the finesse of high-frequency capabilities.
How does High-Frequency Package Substrate differ from traditional PCBs?
High-Frequency Package Substrates and traditional Printed Circuit Boards (PCBs) don distinct attires in the electronic ensemble, each contributing its unique notes to the symphony. Let’s delve into the nuances that set them apart:
Material Ballet:
High-Frequency Package Substrate: Stepping into the limelight with bespoke materials like PTFE or ceramics, these substrates twirl with low dielectric constants and minimal signal loss at the high-frequency ball.
Traditional PCBs: A supporting cast clad in FR-4, a cost-effective garment that may carry a higher dielectric tone, adding different hues to the electronic canvas.
Dielectric Sonata:
High-Frequency Package Substrate: A maestro in crafting a low dielectric hum, these substrates orchestrate a seamless signal dance, especially at higher frequencies.
Traditional PCBs: The dielectric notes may be more diverse, potentially weaving a symphony of signal losses and attenuations, particularly in the higher-frequency cadence.
Signal Loss Waltz:
High-Frequency Package Substrate: A virtuoso in minimizing signal loss and attenuation, these substrates take center stage, ensuring a pristine signal performance in high-frequency suites.
Traditional PCBs: While capable dancers, the standard PCB ensemble may execute a more pronounced loss and attenuation routine, particularly as the electronic tempo ascends.
Impedance Choreography:
High-Frequency Package Substrate: Precision in impedance becomes the lead choreography, ensuring signals pirouette in harmony with transmission line impedance, minimizing distortions.
Traditional PCBs: While capable of following the impedance script, the precision may not demand the same meticulous choreography, catering to a broader range of applications.
Applications Symphony:
High-Frequency Package Substrate: The prima donna in applications where high-frequency prowess takes the spotlight, such as RF, microwave circuits, and the grand stage of wireless communication.
Traditional PCBs: Versatile ensemble players, harmonizing in various electronic devices and systems, particularly in scenarios where the intricate requirements of high-frequency substrates play a supporting role.
Cost Overture:
High-Frequency Package Substrate: The maestro’s performance comes at a cost, with specialized materials and manufacturing processes composing a more expensive opus.
Traditional PCBs: The cost-effective chorus, resonating across diverse applications where the grandeur of high-frequency performance steps aside.
In essence, High-Frequency Package Substrates and traditional PCBs waltz together in the electronic ballroom, each showcasing its unique dance. The former leads in high-frequency concertos, while the latter provides a versatile backdrop, pirouetting through a myriad of electronic landscapes.
What is the main structure and manufacturing technology of High-Frequency Package Substrate?
Crafting High-Frequency Package Substrates involves a meticulous dance of materials and manufacturing techniques, specially choreographed to meet the demands of high-frequency applications. Here’s a reimagined exploration of their main structure and manufacturing technology:
Harmony of Structure:
Foundation Material:
High-frequency substrates step onto the stage adorned in materials like polytetrafluoroethylene (PTFE), ceramics, or liquid crystal polymers (LCP). These materials, chosen for their low dielectric constants, lay the groundwork for optimal signal integrity.
Copper Ballet:
Thin copper foils pirouette onto the substrate, weaving conductive pathways for signals. The copper thickness, akin to dancers’ precision, is delicately managed to ensure flawless signal transmission and impedance matching.
Dielectric Layers Waltz:
The dance floor features multiple dielectric layers. These layers, much like skilled partners, separate signal traces, providing insulation and controlling impedance, contributing to the choreography of flawless signal transmission.
Surface Finishes Elegance:
Exquisite surface finishes, like the shimmer of immersion gold (ENIG) or the grace of immersion silver, are applied to the copper surfaces. This not only enhances conductivity but also shields against the elements, a protective layer in the dance of durability.
Masked Performance:
A solder mask dons the ensemble, protecting the copper traces from unintended soldering during the assembly act. It’s akin to a costume, adding both flair and functionality to the performance.
Component Pads Pas de Deux:
Pads for mounting electronic components join the performance, designed with precision for the dance of soldering during assembly. These pads, like skilled partners, ensure a seamless connection.
Symphony of Manufacturing:
Material Ballet Selection:
The overture begins with the careful selection of substrate material. PTFE-based materials, ceramics, or other virtuoso materials take the stage, each contributing to the electrical symphony.
Layered Crescendo:
High-frequency substrates unfold in multiple layers, each layer playing a unique note in the electrical crescendo. Layering involves a delicate dance of laminating substrate material and copper foil, a symphony of precision.
Circuit Pattern Waltz:
The desired circuit pattern emerges through a dance of photoresist and etching. It’s a carefully choreographed routine involving exposure to light, development, and etching, creating the intricate dance of circuit traces.
Copper Plating Rhythm:
Additional copper plating may be introduced, a rhythmic addition to enhance trace thickness or create microvias. It’s a subtle dance to perfect the conductivity of the ensemble.
Surface Finish Sonata:
The application of surface finish takes center stage, a sonata of protection and reliability. ENIG, immersion silver, or immersion tin – each note contributes to the overall harmony.
Masked Elegance Application:
Solder mask is gracefully applied, leaving openings for component pads and vias. It’s an elegant mask, ensuring insulation and preventing unintended soldering in the intricate ballet of assembly.
Quality Control Symphony:
Throughout this artistic journey, rigorous quality control measures are akin to a symphony conductor ensuring every note is in tune. Advanced testing techniques, a part of the grand composition, validate that the substrate performs in harmony with specified criteria.
In essence, the crafting of High-Frequency Package Substrates is a ballet of materials and processes, a symphony of precision and artistry, where every element dances together to create a performance tailored for the demanding stages of high-frequency applications.
FAQs for High-Frequency Package Substrate Manufacturers
How does the Manufacturing Process Diverge from Traditional PCB Production?
The manufacturing process involves specialized techniques such as precise layering of low-dielectric materials, controlled impedance design, and advanced testing for signal integrity. These processes cater to the unique demands of high-frequency applications.
What Stringent Quality Control Measures are Implemented in Manufacturing?
Rigorous quality control measures include impedance testing, signal integrity analysis, and comprehensive inspections of materials and circuit patterns. Advanced testing techniques guarantee that the substrate aligns with specified performance criteria.
Is the Cost of High-Frequency Package Substrates Higher than Traditional PCBs?
Yes, High-Frequency Package Substrates can be more expensive due to the involvement of specialized materials and manufacturing processes. This increased cost is justified by their superior performance in high-frequency applications.
Can High-Frequency Package Substrates be Customized for Specific Applications?
Indeed, manufacturers often offer customization options to meet the unique requirements of diverse applications. This may involve tailored material selections, customized circuit patterns, and specific impedance control.
What are the Vital Considerations for Designing High-Frequency Package Substrates?
Key considerations encompass material selection, controlled impedance design, signal integrity analysis, effective thermal management, and adherence to industry standards governing high-frequency applications.
Conclusion
In summary, the saga of High-Frequency Package Substrates unfolds as a fascinating journey into the realm of precision and intricacy within electronic packaging. These substrates, tailored for the intricate orchestration of high-frequency signals, stand as a testament to the artistry inherent in engineering excellence. The expedition from material curation to the subtleties of manufacturing unravels as a symphony of design nuances, where low dielectric constants, impedance control, and sophisticated surface finishes take center stage.
The unique attributes of High-Frequency Package Substrates, juxtaposed against the traditional backdrop of PCBs, highlight their distinctive prowess in applications that demand nothing short of impeccable signal integrity. Materials such as PTFE, ceramics, and LCP form the palette for a choreographed masterpiece, where minimal signal loss and optimal performance emerge as the leading dancers, especially in the arenas of RF, microwave circuits, and wireless communication.
Manufacturers engage in a manufacturing ballet, delicately layering substrates, refining circuit patterns, and applying surface finishes with a finesse reminiscent of virtuoso performers. The rigorous measures of quality control serve as the maestro, ensuring that each note resonates in harmony with the prescribed performance criteria.
As these substrates take center stage in diverse high-frequency applications, their role in safeguarding signal accuracy, mitigating distortions, and contributing to the overall reliability of electronic systems becomes increasingly apparent. The customizable facets offered by manufacturers underscore the adaptability of High-Frequency Package Substrates to the unique demands of varied applications.
In essence, the tale of High-Frequency Package Substrates is one of meticulous precision, artistic ingenuity, and technological finesse. Their influence on the landscape of high-frequency electronics transcends mere functionality, evolving into a symphony of engineering brilliance, where each element plays a pivotal role in ensuring the seamless transmission of signals in the intricate and dynamic panorama of contemporary electronics.