HF Radar PCB Manufacturer
HF Radar PCB Manufacturer,HF Radar PCBs are printed circuit boards specifically designed for high-frequency radar systems. These boards operate in the HF (High Frequency) band, typically ranging from 3 MHz to 30 MHz. They are widely used in various radar applications, including over-the-horizon radar (OTHR) and coastal surveillance. HF Radar PCBs feature optimized designs to ensure efficient signal processing and maintain signal integrity at high frequencies. They use specialized substrate materials such as Rogers, Taconic, and Arlon, known for their low dielectric loss and consistent electrical properties. The manufacturing process for these boards involves precise control, including design verification, material selection, PCB fabrication, component mounting, soldering, and testing. HF Radar PCBs play a crucial role in applications such as maritime surveillance, weather monitoring, environmental sensing, and defense systems, thanks to their high sensitivity, long-range detection capability, and reliability in harsh environments.
What is HF Radar PCB?
High Frequency (HF) radar printed circuit board (PCB) is a specialized circuit board designed to operate at high frequencies typically ranging from 3 MHz to 30 MHz. These frequencies fall within the HF band of the electromagnetic spectrum, which is widely used in various applications including communications, radar, and sensing.
HF radar PCBs are specifically tailored for radar systems that operate in the HF band. These radar systems are often used for over-the-horizon radar (OTHR) applications, which involve detecting and tracking targets beyond the line of sight, such as ships or aircraft, over long ranges.
The design of HF radar PCBs is crucial for achieving high performance in radar systems. Here are some key considerations:
- High Frequency Design:HF radar PCBs must be designed to handle high-frequency signals efficiently. This involves careful selection of materials, trace routing, and component placement to minimize signal losses, impedance mismatches, and electromagnetic interference.
- Impedance Matching:Maintaining proper impedance matching throughout the PCB is essential for maximizing signal transfer and minimizing reflections. This is achieved through precise control of trace widths, lengths, and layer stack-up.
- Signal Integrity:Ensuring signal integrity is critical for accurate radar operation. HF radar PCBs must minimize signal distortions such as reflections, crosstalk, and jitter, which can degrade the performance of the radar system.
- RF Shielding:To prevent electromagnetic interference and ensure the integrity of sensitive RF signals, HF radar PCBs often incorporate shielding techniques such as grounded metal layers, RF shielding cans, and controlled impedance connectors.
- Temperature Stability:Many radar systems operate in harsh environments where temperature fluctuations can affect performance. HF radar PCBs may incorporate materials and design techniques to maintain stability over a wide temperature range.
- Power Handling:HF radar systems may require high power amplifiers to transmit signals over long distances. PCBs must be designed to handle high power levels without degrading performance or causing damage to components.
- Reliability:Reliability is crucial for radar systems, especially those used in mission-critical applications. HF radar PCBs undergo rigorous testing and validation to ensure they meet reliability standards and can withstand the demands of operational environments.
Overall, HF radar PCBs play a vital role in the performance and reliability of radar systems operating in the HF band. Their design and manufacturing require careful attention to detail to meet the stringent requirements of high-frequency applications.
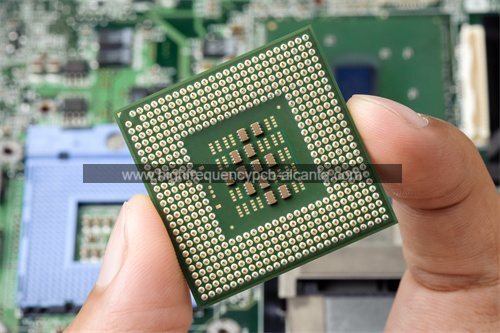
HF Radar PCB Manufacturer
What are the HF Radar PCB Design Guidelines?
Designing PCBs for HF radar systems requires careful consideration of various factors to ensure optimal performance. Here are some key guidelines:
- Impedance Control:Maintain consistent impedance throughout the transmission lines on the PCB. This involves using controlled impedance traces with specific widths and layer stack-up to match the characteristic impedance of the transmission lines.
- Signal Integrity:Minimize signal distortions such as reflections, crosstalk, and jitter. Use techniques such as controlled impedance routing, proper grounding, and signal isolation to maintain signal integrity.
- RF Layout:Keep RF traces short and direct to minimize signal losses and electromagnetic interference. Use coplanar waveguide (CPW) or microstrip transmission line configurations for RF traces and ensure proper termination at both ends.
- Grounding: Implement a solid ground plane to provide a low-impedance return path for RF signals and minimize ground loops. Use stitching vias to connect different ground layers and ensure a continuous ground plane.
- Component Placement:Place critical components such as RF amplifiers, mixers, and filters close to each other to minimize trace lengths and reduce parasitic capacitance and inductance. Pay attention to the orientation and spacing of components to minimize coupling and interference.
- Power Distribution:Design a stable and clean power distribution network to minimize noise and voltage fluctuations. Use bypass capacitors and voltage regulators to filter out high-frequency noise and ensure a steady supply voltage to sensitive components.
- Shielding:Implement shielding techniques to isolate sensitive RF circuits from external electromagnetic interference. Use grounded metal enclosures, RF shielding cans, and shielded cables to minimize electromagnetic emissions and susceptibility.
- Thermal Management:Consider heat dissipation requirements for high-power RF components. Ensure adequate thermal vias and thermal relief patterns to dissipate heat efficiently and maintain temperature stability.
- Test Points: Include test points and access points for troubleshooting, testing, and calibration purposes. Place test points strategically to facilitate measurements without disrupting signal integrity.
- Design for Manufacturability:Optimize the PCB layout for ease of manufacturing and assembly. Minimize the number of vias, use standard PCB materials and fabrication processes, and follow industry best practices to ensure high yield and reliability.
By following these guidelines, designers can create HF radar PCBs that meet the stringent requirements of high-frequency applications, ensuring optimal performance, reliability, and signal integrity. Additionally, thorough testing and validation are essential to verify the performance of the PCB design before deployment in radar systems.
What is the HF Radar PCB Fabrication Process?
The fabrication process for HF radar PCBs involves several steps to translate the design into a physical circuit board capable of meeting the high-frequency requirements of radar systems. Here’s an overview of the typical fabrication process:
- Design Transfer:The fabrication process begins with transferring the PCB design files from the design software to the manufacturing facility. This often involves generating Gerber files, which contain the necessary information for manufacturing the PCB.
- Substrate Selection:Selecting the appropriate substrate material is crucial for HF radar PCBs. Common substrate materials for high-frequency applications include specialized laminates such as Rogers, Taconic, or Arlon, which offer low dielectric loss and consistent electrical properties over a wide frequency range.
- Panelization: Multiple PCBs are often fabricated on a single panel to optimize manufacturing efficiency. The PCB layout is arranged on a panel, taking into account factors such as panel size, routing, and spacing between individual boards.
- Lamination: The selected substrate material is laminated with copper foil to form the base copper layer of the PCB. The copper foil thickness is carefully chosen based on the required RF performance and power handling capabilities of the PCB.
- Photoresist Application: A layer of photoresist is applied to the copper-clad substrate to protect areas of the copper that should remain after etching. The photoresist is typically applied using a process such as screen printing or roller coating.
- Exposure and Development:The PCB panel is exposed to UV light through a photomask containing the PCB pattern. This exposes the photoresist in the desired areas, which are then developed to remove the unexposed photoresist, leaving behind the pattern of copper traces.
- Etching:The exposed copper areas are etched away using chemical etchants, leaving behind the desired copper traces on the substrate. The etching process is carefully controlled to achieve precise trace widths and maintain consistent impedance throughout the PCB.
- Surface Finishing: After etching, the PCB undergoes surface finishing to protect the copper traces from oxidation and improve solderability. Common surface finishes for HF radar PCBs include immersion gold, ENIG (Electroless Nickel Immersion Gold), and OSP (Organic Solderability Preservative).
- Drilling:Precision holes are drilled into the PCB for component mounting and interconnection between layers. Advanced drilling techniques such as laser drilling may be used for high-density PCBs or microvias in multilayer designs.
- Plating and Plating Resist Removal:After drilling, the holes are plated with conductive material to create vias for interconnecting different layers of the PCB. Any remaining plating resist from the drilling process is removed to expose the plated vias.
- Final Inspection:The fabricated PCB undergoes rigorous inspection and testing to ensure it meets the design specifications and quality standards. This may include electrical testing, dimensional inspection, and visual inspection of the PCB.
- Routing and Separation:Once the individual PCBs are inspected and tested, they are routed and separated from the panel using precision cutting techniques such as milling or depanelization machines.
- Packaging and Shipping:The finished PCBs are packaged according to customer requirements and shipped to the assembly facility for component mounting and soldering.
By following these steps, manufacturers can produce high-quality HF radar PCBs that meet the stringent performance and reliability requirements of radar systems operating in the high-frequency band. Close attention to detail, process control, and quality assurance throughout the fabrication process are essential to ensure the integrity and performance of the final PCBs.
How do you manufacture HF Radar PCBs?
Manufacturing HF radar PCBs involves several specialized steps to ensure high performance at high frequencies. Here’s a detailed overview of the manufacturing process:
- Design Verification: Before manufacturing begins, the PCB design undergoes thorough verification to ensure it meets the requirements for high-frequency operation. This includes checking impedance control, signal integrity, and RF layout considerations.
- Material Selection:Selecting the right substrate material is crucial for HF radar PCBs. Specialized laminates with low dielectric loss and consistent electrical properties over a wide frequency range are typically chosen, such as Rogers, Taconic, or Arlon materials.
- Panelization:Multiple PCBs are often fabricated on a single panel to optimize manufacturing efficiency. The PCB layout is arranged on the panel, considering factors such as panel size, routing, and the number of boards per panel.
- Lamination: The selected substrate material is laminated with copper foil to form the base copper layer of the PCB. The copper foil thickness is chosen based on the required RF performance and power handling capabilities.
- Photoresist Application:A layer of photoresist is applied to the copper-clad substrate to protect areas of the copper that should remain after etching. This is typically done using processes such as screen printing or roller coating.
- Exposure and Development:The PCB panel is exposed to UV light through a photomask containing the PCB pattern. This exposes the photoresist in the desired areas, which are then developed to remove the unexposed photoresist, leaving behind the pattern of copper traces.
- Etching:The exposed copper areas are etched away using chemical etchants, leaving behind the desired copper traces on the substrate. The etching process is carefully controlled to achieve precise trace widths and maintain consistent impedance.
- Surface Finishing:After etching, the PCB undergoes surface finishing to protect the copper traces from oxidation and improve solderability. Common surface finishes for HF radar PCBs include immersion gold, ENIG (Electroless Nickel Immersion Gold), and OSP (Organic Solderability Preservative).
- Drilling:Precision holes are drilled into the PCB for component mounting and interconnection between layers. Advanced drilling techniques such as laser drilling may be used for high-density PCBs or microvias in multilayer designs.
- Plating and Plating Resist Removal:After drilling, the holes are plated with conductive material to create vias for interconnecting different layers of the PCB. Any remaining plating resist from the drilling process is removed to expose the plated vias.
- Final Inspection:The fabricated PCB undergoes rigorous inspection and testing to ensure it meets the design specifications and quality standards. This may include electrical testing, dimensional inspection, and visual inspection of the PCB.
- Routing and Separation:Once the individual PCBs are inspected and tested, they are routed and separated from the panel using precision cutting techniques such as milling or depanelization machines.
- Packaging and Shipping:The finished PCBs are packaged according to customer requirements and shipped to the assembly facility for component mounting and soldering.
By following these steps, manufacturers can produce high-quality HF radar PCBs that meet the stringent performance and reliability requirements of radar systems operating in the high-frequency band. Close attention to detail, process control, and quality assurance throughout the manufacturing process are essential to ensure the integrity and performance of the final PCBs.
How much should HF Radar PCBs cost?
The cost of HF radar PCBs can vary significantly depending on several factors, including the complexity of the design, the materials used, the manufacturing processes involved, the quantity ordered, and the supplier’s pricing structure. Here are some factors that can influence the cost:
- Design Complexity:PCBs with complex layouts, high-density components, tight tolerances, and advanced features such as impedance-controlled traces or high-frequency RF circuitry typically incur higher manufacturing costs due to increased processing time and specialized equipment requirements.
- Material Selection:The choice of substrate material can significantly impact the cost of HF radar PCBs. Specialized materials optimized for high-frequency performance, such as Rogers, Taconic, or Arlon laminates, tend to be more expensive than standard FR-4 substrates.
- Manufacturing Processes:Advanced manufacturing processes, such as laser drilling for microvias or impedance-controlled etching for RF traces, may incur additional costs compared to standard processes. Surface finishes, plating techniques, and inspection methods can also affect the overall cost.
- Quantity:Economies of scale often apply in PCB manufacturing, meaning that larger order quantities typically result in lower per-unit costs. However, prototype or low-volume orders may have higher unit costs due to setup fees and minimum order requirements.
- Supplier Pricing:Different PCB manufacturers may offer varying pricing structures based on their capabilities, expertise, geographic location, and overhead costs. It’s essential to obtain quotes from multiple suppliers to compare prices and ensure competitive pricing.
- Additional Services:Additional services such as design validation, testing, conformal coating, and assembly may incur extra charges but can contribute to overall product quality and reliability.
As a rough estimate, the cost of HF radar PCBs can range from a few dollars to several hundred dollars per square inch, depending on the factors mentioned above. For a more accurate cost estimate, it’s recommended to consult with PCB manufacturers and provide detailed specifications of the desired PCB design and quantity.
What is HF Radar PCB base material?
The base material for HF radar PCBs plays a crucial role in determining their performance at high frequencies. HF radar PCBs require substrate materials with specific properties to ensure low dielectric loss, consistent electrical characteristics, and stable performance over a wide frequency range. Here are some common base materials used for HF radar PCBs:
- Rogers 4000 Series:Rogers Corporation manufactures a range of high-frequency laminates, including the 4000 series, which are widely used in HF radar PCBs. These laminates are engineered for low dielectric loss, tight electrical tolerance, and excellent dimensional stability, making them suitable for high-frequency applications.
- Taconic TLY-5A:Taconic Advanced Dielectric Division produces TLY-5A, a high-performance RF laminate designed for microwave and RF applications. TLY-5A offers low loss tangent, uniform dielectric constant, and excellent signal integrity, making it suitable for HF radar PCBs.
- Arlon AD Series:Arlon Electronic Materials manufactures the AD series of laminates, which are specifically formulated for high-frequency circuitry. These laminates feature low dissipation factor, stable dielectric constant, and high thermal conductivity, making them ideal for HF radar applications.
- Isola I-Tera MT40:Isola Group offers I-Tera MT40, a high-performance laminate material designed for multilayer RF and microwave applications. I-Tera MT40 provides excellent signal integrity, low insertion loss, and high reliability, making it suitable for HF radar PCBs.
- DuPont Pyralux LF:DuPont’s Pyralux LF flexible laminates are used in HF radar PCBs where flexibility is required, such as in conformal antenna arrays. Pyralux LF offers low dielectric constant, excellent thermal stability, and mechanical flexibility, making it suitable for high-frequency applications.
These base materials are engineered to provide consistent electrical properties, thermal stability, and mechanical performance, essential for the demanding requirements of HF radar systems. When selecting a base material for HF radar PCBs, designers consider factors such as dielectric constant, dissipation factor, thermal conductivity, and dimensional stability to ensure optimal performance at high frequencies.
Which company makes HF Radar PCBs?
Several companies manufacture HF radar PCBs, including Rogers Corporation, Taconic Advanced Dielectric Division, Arlon Electronic Materials, Isola Group, and DuPont, among others. These companies specialize in producing the substrate materials required for high-frequency circuit boards, such as Rogers’ 4000 series, Taconic’s TLY-5A, Arlon’s AD series, Isola’s I-Tera MT40, and DuPont’s Pyralux LF.
Our company is also capable of manufacturing HF radar PCBs. As a professional PCB manufacturer, we have advanced manufacturing equipment, extensive experience, and a skilled team to meet the design and manufacturing requirements of HF radar PCBs. Our production process includes the following key steps:
- Design Verification: We collaborate with clients to ensure that the design of HF radar PCBs meets the requirements for high-frequency operation, including impedance control, signal integrity, and RF layout.
- Material Selection:We offer a variety of substrate material options for high-frequency circuit boards, such as Rogers, Taconic, Arlon, etc., to meet our clients’ specific needs.
- Manufacturing Process:We employ advanced manufacturing processes, such as controlled impedance routing, precision drilling techniques, and surface treatment, to ensure that HF radar PCBs have excellent performance and reliability.
- Quality Control: We strictly adhere to quality control standards, including raw material inspection, process control, and final inspection, to ensure that HF radar PCBs meet design specifications and quality requirements.
- Customer Service:We work closely with clients to provide customized solutions to meet their specific HF radar PCB needs and offer timely technical support and after-sales service.
With our professional manufacturing capabilities and quality assurance system, we can provide clients with high-quality and reliable HF radar PCBs to meet their application requirements in high-frequency radar systems.
What are the 7 qualities of good customer service?
Good customer service is characterized by several key qualities that contribute to a positive customer experience and build long-term relationships. Here are seven essential qualities:
- Responsiveness:Good customer service involves being prompt and responsive to customer inquiries, concerns, and requests. Responding in a timely manner demonstrates attentiveness and a commitment to addressing customer needs promptly.
- Empathy:Empathy is the ability to understand and share the feelings of customers. Good customer service representatives listen actively, demonstrate compassion, and show genuine concern for the customer’s situation, which helps build trust and rapport.
- Professionalism:Professionalism encompasses maintaining a courteous and respectful demeanor, even in challenging situations. Customer service representatives should conduct themselves professionally, adhere to company policies, and strive to resolve issues efficiently and effectively.
- Knowledgeability:Good customer service requires having a thorough understanding of the products or services offered by the company. Customer service representatives should be knowledgeable about company policies, procedures, and offerings to provide accurate information and assistance to customers.
- Problem-Solving Skills:Effective problem-solving skills are essential for resolving customer issues and addressing their concerns effectively. Customer service representatives should be proactive in identifying solutions, offering alternatives, and taking ownership of issues until they are resolved to the customer’s satisfaction.
- Adaptability:Good customer service involves being adaptable and flexible in responding to different customer needs and preferences. Customer service representatives should be able to adjust their approach and communication style based on the individual customer and the situation at hand.
- Consistency:Consistency is key to delivering excellent customer service consistently across all interactions and touchpoints. Customers value reliability and dependability, so maintaining consistent service standards helps build trust and loyalty over time.
By embodying these qualities, companies can provide exceptional customer service that leaves a positive impression on customers and fosters long-term loyalty and satisfaction.
FAQs (Frequently Asked Questions)
What is an HF Radar PCB?
An HF Radar PCB is a printed circuit board specifically designed for use in high-frequency radar systems. These systems operate in the HF band of the electromagnetic spectrum and are used for various applications, including over-the-horizon radar (OTHR) and coastal surveillance.
What are the key features of HF Radar PCBs?
Key features of HF Radar PCBs include impedance control, signal integrity, RF layout optimization, and high-frequency performance. These PCBs are designed to handle high-frequency signals efficiently and maintain signal integrity over long distances.
What materials are used in HF Radar PCBs?
HF Radar PCBs often use specialized substrate materials with low dielectric loss and consistent electrical properties over a wide frequency range. Common materials include Rogers, Taconic, Arlon, and DuPont laminates optimized for high-frequency applications.
What design considerations are important for HF Radar PCBs?
Design considerations for HF Radar PCBs include impedance matching, RF layout optimization, signal integrity, thermal management, and RF shielding. These factors are crucial for achieving optimal performance and reliability in radar systems operating at high frequencies.
How are HF Radar PCBs manufactured?
The manufacturing process for HF Radar PCBs involves several specialized steps, including design verification, material selection, PCB fabrication, component mounting, soldering, and testing. Advanced manufacturing techniques and quality control measures are used to ensure high performance and reliability.
What are the typical applications of HF Radar PCBs?
HF Radar PCBs are used in a variety of radar applications, including maritime surveillance, weather monitoring, environmental sensing, and defense systems. They are often deployed in coastal regions, maritime borders, and remote areas for long-range detection and tracking of targets.
What are the advantages of using HF Radar PCBs?
Advantages of HF Radar PCBs include high sensitivity, long-range capability, reliability in harsh environments, and the ability to detect targets beyond the line of sight. These PCBs enable the development of advanced radar systems for various civilian and military applications.