Glass Substrates Manufacturing
Glass Substrates Manufacturing,Glass substrates are foundational materials used in various industries, including electronics, optics, and display technologies. These substrates, typically made from materials like soda-lime glass, borosilicate glass, or quartz glass, provide a stable and transparent base for the deposition of thin films, fabrication of integrated circuits, and creation of optical components.
These substrates play a critical role in devices such as liquid crystal displays (LCDs), organic light-emitting diode (OLED) displays, lenses, mirrors, and sensors. They offer qualities like transparency, thermal stability, and mechanical strength, making them essential for applications requiring precision and reliability.
Manufactured through processes like melting, forming, cutting, and coating, glass substrates undergo stringent quality control measures to ensure dimensional accuracy, surface quality, and overall performance. With their versatility and adaptability, glass substrates continue to drive advancements in technology, enabling innovations in communication, entertainment, healthcare, and beyond.
What is a Glass Substrate?
A glass substrate is a flat, usually transparent material made from glass that serves as a base or foundation for various applications, particularly in industries like electronics, optics, and display technologies. Its primary function is to provide a stable and smooth surface for other materials to be deposited or attached to, allowing for the creation of various devices and products.
In electronics, glass substrates are commonly used in the manufacturing of integrated circuits (ICs), thin-film transistors (TFTs), and other semiconductor devices. These substrates provide a stable platform for the deposition of semiconductor materials and the fabrication of intricate circuitry through processes such as photolithography and etching.
In optics, glass substrates are utilized in the production of lenses, mirrors, and optical filters. The optical properties of glass, such as its transparency and refractive index, make it an ideal material for shaping and manipulating light in optical systems. Glass substrates can also be coated with thin films to enhance their optical performance, such as anti-reflective coatings or coatings for specific wavelengths of light.
In display technologies, glass substrates play a crucial role in the fabrication of liquid crystal displays (LCDs), organic light-emitting diode (OLED) displays, and other types of flat-panel displays. These substrates provide a rigid and durable surface on which the display components, such as pixels and electrodes, can be deposited or patterned to create the desired visual output.
Glass substrates come in various sizes, shapes, and thicknesses to accommodate different manufacturing processes and applications. They can be produced using different types of glass, each with its own set of properties and characteristics tailored to specific requirements. Overall, glass substrates are essential components in a wide range of technological devices and systems, enabling advancements in electronics, optics, and display technologies.
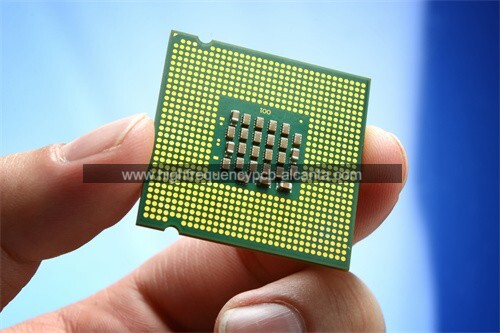
Glass Substrates Manufacturing
What are the Glass Substrate Design Guidelines?
Glass substrate design guidelines typically encompass several key aspects to ensure optimal performance and manufacturability. Here are some common guidelines:
- Material Selection: Choose glass materials with appropriate optical, thermal, mechanical, and chemical properties for the specific application. Factors to consider include transparency, thermal expansion coefficient, surface flatness, and resistance to environmental factors such as moisture and chemicals.
- Dimensional Tolerances: Define precise dimensional tolerances for the glass substrate to ensure compatibility with downstream processes such as deposition, etching, and bonding. Tight tolerances help maintain uniformity and accuracy in device fabrication.
- Surface Quality: Specify surface finish requirements to minimize defects such as scratches, pits, and blemishes. Smooth and defect-free surfaces are essential for maintaining optical clarity and ensuring proper functionality of electronic components.
- Flatness: Ensure the glass substrate has a high degree of flatness to facilitate uniform deposition of thin films and precise patterning of features. Flat substrates minimize distortion and improve the resolution of optical and electronic devices.
- Cleanliness: Implement cleanliness standards to prevent contamination during manufacturing processes. Clean surfaces are crucial for promoting adhesion, reducing defects, and maintaining the integrity of deposited materials.
- Edge Quality: Define requirements for edge quality to prevent chipping, delamination, or other damage that could affect the structural integrity of the substrate or interfere with subsequent processing steps.
- Compatibility with Coatings: Consider compatibility with coatings or surface treatments that may be applied to enhance performance or add functionality to the substrate, such as anti-reflective coatings, conductive layers, or protective films.
- Handling and Packaging: Develop handling and packaging procedures to minimize the risk of damage during transportation, storage, and handling. Proper handling practices help preserve the integrity of the glass substrate and prevent contamination or breakage.
- Cost Efficiency: Optimize design parameters to achieve the desired performance objectives while minimizing production costs. Balancing performance requirements with cost considerations is essential for ensuring competitiveness in the market.
By adhering to these guidelines, designers can effectively develop glass substrates that meet the specific requirements of their applications while ensuring reliability, performance, and manufacturability.
What is the Glass Substrate Fabrication Process?
The fabrication process of glass substrates typically involves several key steps to produce high-quality substrates suitable for various applications. While specific processes may vary depending on the application and desired characteristics of the substrate, the following steps provide a general overview of the fabrication process:
- Raw Material Selection: The process begins with the selection of high-quality glass raw materials that possess the desired optical, mechanical, and chemical properties for the intended application. Various types of glass, such as soda-lime glass, borosilicate glass, or quartz glass, may be chosen based on factors like transparency, thermal stability, and chemical resistance.
- Melting and Forming: The selected glass raw materials are melted in a furnace at high temperatures typically ranging from 1,000 to 1,600 degrees Celsius (1,832 to 2,912 degrees Fahrenheit). Once molten, the glass is formed into sheets or panels using techniques such as floating, rolling, or drawing. During this process, the glass undergoes controlled cooling to ensure uniformity and minimize internal stresses.
- Cutting and Shaping: After forming, the glass sheets are cut into the desired sizes and shapes using precision cutting tools or techniques such as sawing, scoring, or laser cutting. The edges of the glass substrates may also be polished or beveled to improve edge quality and safety.
- Surface Treatment: Depending on the application requirements, the surface of the glass substrates may undergo various treatments to modify its properties. This can include chemical etching to create textured or patterned surfaces, coating deposition to enhance optical or electrical properties, or surface polishing to achieve smoother finishes.
- Cleaning and Inspection: Prior to further processing or packaging, the glass substrates undergo thorough cleaning to remove any contaminants, residues, or particles that may affect performance or quality. Inspection processes may also be employed to assess dimensional accuracy, surface quality, and overall integrity.
- Coating Deposition (Optional): In some applications, additional thin film coatings may be deposited onto the glass substrates to impart specific functionalities such as anti-reflective properties, conductive layers, or scratch resistance. Coating techniques can include physical vapor deposition (PVD), chemical vapor deposition (CVD), or sputtering.
- Quality Assurance:Throughout the fabrication process, rigorous quality control measures are implemented to ensure that the glass substrates meet the specified requirements and standards. This may involve testing for factors such as dimensional accuracy, surface roughness, optical clarity, and mechanical strength.
- Packaging and Shipping: Once fabricated and inspected, the glass substrates are carefully packaged to protect them from damage during transportation and storage. Packaging materials may include protective films, foam padding, or specialized containers designed to prevent breakage or scratching.
By following these fabrication steps with precision and attention to detail, manufacturers can produce glass substrates that meet the stringent requirements of various industries and applications, including electronics, optics, displays, and more.
How do you manufacture a Glass Substrate?
Manufacturing a glass substrate involves a series of steps that transform raw materials into finished substrates suitable for various applications. Here’s a general outline of the manufacturing process:
- Raw Material Selection: High-quality raw materials are chosen based on the desired properties of the glass substrate, such as transparency, thermal stability, and chemical resistance. Common raw materials include silica sand, soda ash, limestone, and other additives.
- Melting: The selected raw materials are mixed and melted in a furnace at high temperatures typically ranging from 1,100 to 1,600 degrees Celsius (2,012 to 2,912 degrees Fahrenheit). This molten glass is often referred to as “batch.”
- Forming: Once melted, the glass is shaped into a continuous sheet or ribbon using one of several forming methods. The most common techniques include the float glass process, in which the molten glass floats on a bath of molten tin, and the draw or sheet process, where the glass is drawn vertically or horizontally through rollers to achieve the desired thickness and width.
- Annealing: The formed glass sheet undergoes an annealing process to relieve internal stresses and improve its mechanical strength and thermal stability. This involves gradually cooling the glass at controlled rates in a temperature-controlled annealing lehr or kiln.
- Cutting and Shaping: After annealing, the glass sheet is cut into smaller sizes and shapes using diamond saws, water jets, or laser cutting techniques. The edges may be polished or beveled to improve their quality and safety.
- Surface Treatment: Depending on the application requirements, the glass substrate may undergo surface treatments such as chemical etching, grinding, or polishing to achieve the desired surface characteristics, such as smoothness, roughness, or texture.
- Coating Deposition (Optional): Additional thin film coatings may be applied to the glass substrate to enhance its properties, such as anti-reflective coatings, conductive layers, or scratch-resistant coatings. Coating techniques may include physical vapor deposition (PVD), chemical vapor deposition (CVD), or sputtering.
- Quality Control: Throughout the manufacturing process, rigorous quality control measures are implemented to ensure that the glass substrates meet the specified requirements and standards. This may involve testing for factors such as dimensional accuracy, surface quality, optical clarity, and mechanical strength.
- Packaging and Shipping: Once manufactured and inspected, the glass substrates are carefully packaged to protect them from damage during transportation and storage. Packaging materials may include protective films, foam padding, or specialized containers designed to prevent breakage or scratching.
By following these steps with precision and attention to detail, manufacturers can produce high-quality glass substrates tailored to the specific needs of their customers and applications.
How much should a Glass Substrate cost?
The cost of a glass substrate can vary widely depending on several factors, including:
- Type of Glass: Different types of glass have varying material costs. For example, standard soda-lime glass is generally less expensive than specialty glasses like borosilicate or quartz.
- Size and Thickness: Larger and thicker glass substrates typically require more material and energy to produce, resulting in higher costs.
- Quality Requirements: Higher quality substrates with tighter tolerances, superior surface finishes, and lower defect rates may command higher prices due to the increased manufacturing complexity and quality control efforts involved.
- Processing and Coating: Additional processes such as cutting, shaping, surface treatment, and coating deposition can add to the overall cost of the substrate.
- Volume and Customization: Bulk orders or standard sizes may benefit from economies of scale and lower unit costs compared to custom orders or smaller quantities.
- Market Demand and Supply: Fluctuations in supply and demand, as well as market conditions, can influence substrate prices.
- Supplier and Location: The choice of supplier and their location can impact costs due to differences in labor, overhead, and transportation expenses.
As a result of these factors, the cost of a glass substrate can range from a few dollars per square meter for basic soda-lime glass to hundreds or even thousands of dollars per square meter for specialized, high-quality substrates with advanced features and coatings. It’s essential for buyers to carefully consider their specific requirements and budget constraints when evaluating substrate options and suppliers.
What is Glass Substrate base material?
The base material for glass substrates is typically glass itself. Various types of glass can be used as substrate materials, each offering different properties suited to specific applications. Some common types of glass used as substrate base materials include:
- Soda-Lime Glass: This is the most common type of glass, made from a mixture of soda ash (sodium carbonate), limestone, and silica sand. Soda-lime glass is known for its low cost, good optical clarity, and ease of manufacturing. It’s widely used in applications such as windows, containers, and basic glass substrates.
- Borosilicate Glass: Borosilicate glass contains boron trioxide, which gives it enhanced thermal shock resistance compared to soda-lime glass. It’s often used in applications where thermal stability and resistance to chemical corrosion are important, such as laboratory glassware, lighting fixtures, and certain electronic substrates.
- Quartz Glass (Fused Silica): Quartz glass is made from pure silica (silicon dioxide) and is known for its exceptional optical properties, high thermal resistance, and low thermal expansion coefficient. It’s used in applications requiring high purity, such as semiconductor manufacturing, optics, and high-temperature environments.
- Aluminosilicate Glass:Aluminosilicate glass contains aluminum oxide in addition to silica, imparting improved mechanical strength and scratch resistance compared to soda-lime glass. It’s used in applications where durability and resistance to damage are important, such as touchscreen displays and protective covers for electronic devices.
- Specialty Glasses: Various specialty glasses are available with unique properties tailored to specific applications. For example, ultra-low expansion glasses are used in precision optical instruments and telescopes, while lead glass is used in radiation shielding applications.
These are just a few examples of the types of glass used as substrate base materials. The choice of glass depends on factors such as desired optical properties, thermal stability, mechanical strength, chemical resistance, and cost considerations specific to the intended application.
Which company makes Glass Substrates?
There are many companies that produce glass substrates, including globally renowned electronics, optics, and display technology companies. Some major manufacturers include Corning, AGC (Asahi Glass), Sharp, Samsung, LG Display, BOE (BOE Technology), and others.
Our company is also capable of manufacturing glass substrates, depending on our processes and equipment. We have advanced glass processing equipment and a professional team to meet various customer needs. Our manufacturing process strictly adheres to quality standards and is customized to produce glass substrates of various sizes, shapes, and characteristics according to customer requirements.
Our manufacturing capabilities span multiple industries, including electronics, optics, display technology, and more. Our glass substrates find wide applications in integrated circuits, liquid crystal displays, organic light-emitting diode (OLED) displays, optical components, sensors, and other fields.
As a glass substrate manufacturer, we are committed to providing high-quality, high-performance products and building long-term partnerships with our customers. Our team has rich experience and expertise to offer customized solutions to customers and ensure strict quality control throughout the manufacturing process, meeting customer requirements and expectations.
Whether customers need standard glass substrates or custom products with special requirements, we can meet their needs and provide excellent service and support. Our goal is to become a trusted partner for customers, driving development and innovation across various industries.
What are the 7 qualities of good customer service?
Good customer service is characterized by several key qualities that contribute to positive experiences for customers. Here are seven essential qualities:
- Responsiveness: Being responsive means promptly addressing customer inquiries, concerns, or issues. Customers appreciate timely responses, whether it’s answering questions, providing assistance, or resolving problems. Responsiveness demonstrates that you value their time and prioritize their needs.
- Empathy: Empathy involves understanding and acknowledging the feelings and perspectives of customers. Listening attentively to their concerns, showing compassion, and putting yourself in their shoes can help build trust and rapport. Empathetic customer service fosters strong relationships and helps resolve issues more effectively.
- Professionalism: Professionalism encompasses maintaining a courteous, respectful, and helpful demeanor in all interactions with customers. This includes being polite, patient, and maintaining composure, even in challenging situations. Professionalism builds credibility and reflects positively on the organization.
- Knowledgeability: Knowledgeability refers to having a thorough understanding of the products, services, policies, and processes related to your role. Being well-informed enables you to provide accurate information, offer relevant solutions, and guide customers effectively. Continuous training and updates help enhance knowledgeability.
- Problem-Solving Skills: Effective problem-solving skills are crucial for resolving customer issues and addressing their needs satisfactorily. This involves identifying the root cause of problems, exploring viable solutions, and taking proactive steps to rectify issues. Problem-solving skills demonstrate competence and commitment to customer satisfaction.
- Flexibility: Flexibility is the ability to adapt to varying customer needs, preferences, and circumstances. It involves being open-minded, resourceful, and willing to accommodate reasonable requests or changes. Flexibility allows you to tailor solutions to meet individual customer requirements, enhancing their experience.
- Consistency: Consistency entails delivering a consistently high level of service across all customer interactions and touchpoints. Whether it’s in-person, over the phone, via email, or online, maintaining consistency in service quality, communication, and policies reinforces trust and reliability. Consistency builds brand loyalty and encourages repeat business.
By embodying these qualities, organizations can provide exceptional customer service experiences that foster customer satisfaction, loyalty, and positive word-of-mouth recommendations.
FAQs
How are glass substrates manufactured?
The manufacturing process of glass substrates typically involves melting raw materials, forming glass sheets or panels, cutting and shaping, surface treatment, optional coating deposition, quality control, and packaging.
What are the advantages of glass substrates?
Glass substrates offer advantages such as transparency, thermal stability, chemical resistance, mechanical strength, and suitability for precision manufacturing processes like photolithography and etching.
What factors affect the cost of glass substrates?
The cost of glass substrates can vary based on factors such as the type of glass used, size and thickness, quality requirements, processing techniques, coatings, volume, market demand, and supplier.
What quality control measures are used in glass substrate manufacturing?
Quality control measures in glass substrate manufacturing include dimensional accuracy testing, surface quality inspection, optical clarity assessment, mechanical strength testing, and adherence to industry standards.
What are the environmental considerations of glass substrates?
Glass substrates are generally environmentally friendly materials as they are recyclable and non-toxic. However, energy consumption during manufacturing and disposal methods should be considered for sustainable practices.
Where can I buy glass substrates?
Glass substrates can be purchased from specialized glass manufacturers, distributors, or suppliers that cater to specific industries and applications.