Glass Core Package Substrates Manufacturer
Glass Core Package Substrates Manufacturer,Glass Core Package Substrates are advanced materials used in semiconductor packaging, offering exceptional thermal stability and electrical insulation. These substrates feature a glass core that provides superior dimensional stability and low thermal expansion, essential for high-density and high-performance applications. Glass core substrates enable fine pitch wiring, reduced signal loss, and enhanced reliability, making them ideal for use in advanced IC packaging and high-speed electronic devices. Their unique properties support the miniaturization and increased functionality of modern electronics, addressing the demands of next-generation technologies in areas such as telecommunications, computing, and consumer electronics.
What is a Glass Core Package Substrate?
A Glass Core Package Substrate is a type of advanced packaging substrate material that offers unique properties and advantages. Traditional chip packaging substrates mainly use organic materials (such as BT resin) or ceramic materials, whereas glass substrates utilize specially treated glass as the core material. This material possesses several superior characteristics, making it highly suitable for high-performance electronic packaging applications.
Firstly, glass substrates exhibit excellent electrical properties. The dielectric constant and loss factor of glass are relatively low, which helps to improve signal transmission speed and reduce signal loss, making it suitable for high-frequency and high-speed signal transmission needs. Additionally, the thermal expansion coefficient (CTE) of glass is close to that of silicon chips, which helps to reduce the stress between the chip and the substrate during thermal cycling, thereby enhancing the reliability of the packaging.
Secondly, the mechanical properties of glass substrates are also outstanding. Glass materials have higher hardness and rigidity, providing good support and protection, preventing mechanical damage to the chip during operation or use. At the same time, the flatness and surface smoothness of glass substrates are high, which helps to improve the precision and stability of the packaging.
Furthermore, glass substrates have excellent thermal management properties. The thermal conductivity of glass materials is relatively low, which can effectively isolate the heat generated by the chip, preventing heat from transferring to other sensitive components, thereby improving the thermal stability and reliability of the system.
In summary, a Glass Core Package Substrate combines superior electrical, mechanical, and thermal management properties, making it a highly promising high-performance packaging material. As electronic products move towards higher frequency, higher speed, and miniaturization, glass substrates will play an increasingly important role in integrated circuit packaging.
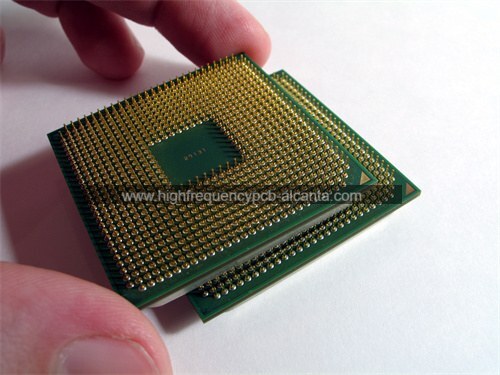
Glass Core Package Substrates Manufacturer
What are the Glass Core Package Substrate Design Guidelines?
Design guidelines for Glass Core Package Substrates (GCPS) focus on optimizing the performance and reliability of electronic packages utilizing glass as the core material. Here are some key design considerations:
- Material Selection: Choose glass materials with appropriate thermal expansion coefficients (CTE) that closely match those of the semiconductor chips to minimize thermal stress during operation.
- Layer Structure: Design the layer stack-up considering signal integrity, power distribution, and thermal management requirements. Ensure sufficient insulation between signal layers and adequate power and ground planes for stable power delivery.
- Routing and Signal Integrity: Pay attention to signal routing to minimize signal loss and electromagnetic interference (EMI). Use controlled impedance routing where necessary to maintain signal integrity, considering the dielectric constant of the glass material.
- Via Design: Optimize via placement and design to minimize parasitic effects and ensure reliable electrical connections between layers. Consider the aspect ratio and aspect ratio limits based on the glass substrate’s thickness and mechanical properties.
- Thermal Management: Incorporate thermal vias and thermal pads strategically to enhance heat dissipation from active components to the substrate. Ensure efficient heat transfer to prevent overheating and ensure long-term reliability.
- Mechanical Considerations: Design the substrate to withstand mechanical stresses, such as bending and shock, by considering the glass material’s mechanical properties, such as hardness and fracture toughness.
- Surface Finish and Coatings: Select appropriate surface finishes and coatings compatible with glass substrates to ensure solderability, reliability under environmental conditions, and protection against corrosion.
- Manufacturing Feasibility: Design features that are manufacturable within the capabilities of glass substrate fabrication processes, such as laser drilling, etching, and lamination.
- Testing and Validation: Plan for testing and validation procedures to ensure the design meets performance and reliability requirements under operational conditions.
By adhering to these design guidelines, engineers can effectively leverage Glass Core Package Substrates to achieve high-performance, reliable electronic packages suitable for various applications demanding stringent electrical, thermal, and mechanical performance criteria.
What is the Glass Core Package Substrate Fabrication Process?
The fabrication process for Glass Core Package Substrates (GCPS) involves several key steps to produce substrates that meet the required specifications for electronic packaging. Here’s an outline of the typical fabrication process:
- Glass Material Selection: High-quality glass with specific thermal expansion properties (CTE) matching semiconductor materials is selected. The glass may undergo special treatments to enhance its electrical and mechanical properties.
- Cleaning and Preparation:The glass sheets are cleaned thoroughly to remove any contaminants that could affect subsequent processing steps. Surface preparation may involve chemical treatments to improve adhesion for subsequent layers.
- Layer Deposition: Thin layers of conductive materials, such as copper or other metals, are deposited onto the glass substrate using techniques like sputtering, electroplating, or chemical vapor deposition (CVD). These layers form the conductive traces and pads necessary for electrical connections.
- Photoresist Application and Patterning: A layer of photoresist is applied onto the substrate. Photolithography techniques are then used to selectively expose and develop the photoresist, creating patterns that define the circuitry and vias.
- Etching: Areas not protected by photoresist are etched away, leaving behind the desired conductive traces and vias on the glass substrate. Wet etching or dry etching processes may be used depending on the design requirements.
- Dielectric Layer Deposition: Insulating layers, typically made of materials with low dielectric constants, are deposited over the conductive traces and vias. These layers serve to isolate and protect the conductive paths while maintaining signal integrity.
- Via Formation: Via holes are drilled or etched through the dielectric layers to establish electrical connections between different conductive layers. Laser drilling or mechanical drilling techniques may be employed based on the substrate thickness and design specifications.
- Surface Finish: Surface finishes such as solder masks and protective coatings are applied to the substrate to protect the circuitry and facilitate soldering during assembly processes. These finishes also provide environmental protection and enhance reliability.
- Final Inspection and Testing: The finished glass core package substrates undergo rigorous inspection and testing to ensure dimensional accuracy, electrical continuity, and reliability under operational conditions. Various electrical tests, including impedance testing and continuity checks, are performed to validate substrate performance.
- Packaging and Shipping: Once validated, the substrates are packaged according to industry standards to prevent damage during transport and storage until they are ready for use in electronic assembly processes.
Each step in the fabrication process is critical to producing Glass Core Package Substrates that meet the demanding requirements of modern electronic devices, balancing high electrical performance, thermal management capabilities, and mechanical robustness.
How do you manufacture a Glass Core Package Substrate?
Manufacturing a Glass Core Package Substrate (GCPS) involves a series of specialized processes to create a substrate that meets the stringent requirements for electronic packaging. Here’s a detailed overview of the typical manufacturing process:
- Glass Substrate Selection: High-quality glass is chosen based on its thermal expansion coefficient (CTE), which should closely match that of semiconductor materials to minimize thermal stress. The glass is also selected for its mechanical strength, electrical properties, and compatibility with subsequent processing steps.
- Cleaning and Preparation: The selected glass substrate undergoes thorough cleaning to remove contaminants and ensure a clean surface for subsequent processing. Surface preparation may include chemical treatments to enhance adhesion for deposited layers.
- Thin Film Deposition: Thin layers of conductive materials (often copper or other metals) are deposited onto the glass substrate. This is typically done using techniques such as sputtering, electroplating, or chemical vapor deposition (CVD). These conductive layers will form the circuit traces and pads required for electrical connections.
- Photolithography: A layer of photoresist is applied to the substrate. Photolithography techniques are used to selectively expose the photoresist to UV light through a mask, defining the patterns for the circuitry and vias.
- Etching: Areas of the conductive layer not protected by the developed photoresist are etched away. This process defines the conductive traces and creates vias (holes) that will later be filled to establish electrical connections between different layers.
- Dielectric Layer Deposition: Insulating layers are deposited over the etched conductive traces and vias. These dielectric layers, often composed of materials with low dielectric constants, provide isolation between conductive paths and protect them from environmental factors.
- Via Formation: Vias are formed through the dielectric layers to connect different conductive layers vertically. This is typically achieved through laser drilling or mechanical drilling processes, depending on the substrate thickness and design requirements.
- Surface Finishing: Surface finishes such as solder masks and protective coatings are applied to the substrate. Solder masks define areas for soldering components onto the substrate during assembly processes, while protective coatings enhance substrate durability and reliability.
- Final Inspection and Testing: The completed glass core package substrates undergo comprehensive inspection and testing. This includes dimensional checks, electrical continuity tests, impedance testing, and reliability assessments under simulated operating conditions.
- Packaging and Shipping: After passing quality control checks, the substrates are packaged according to industry standards to protect them during transport and storage. They are then shipped to electronic assembly facilities where they will be used in the production of electronic devices.
Throughout the manufacturing process, stringent quality control measures are implemented to ensure that Glass Core Package Substrates meet the high standards required for applications in advanced electronic packaging. Each step is crucial in achieving substrates that offer excellent electrical performance, thermal management capabilities, and mechanical reliability.
How much should a Glass Core Package Substrate cost?
The cost of Glass Core Package Substrates (GCPS) can vary significantly based on several factors:
- Material Quality and Specifications: The type and quality of glass used, as well as the specific requirements for thermal expansion coefficient (CTE), electrical properties, and mechanical strength, will influence the cost.
- Manufacturing Complexity: The complexity of the substrate design, including the number of layers, complexity of circuit patterns, and precision of features such as vias and fine traces, affects manufacturing costs.
- Production Volume: Economies of scale play a significant role. Larger production volumes generally reduce per-unit costs due to optimized manufacturing processes and bulk material purchasing.
- Additional Processing and Finishing: Costs can vary based on additional processes such as surface finishing (solder mask, protective coatings), special treatments (chemical strengthening, surface modifications), and testing requirements.
- Supplier and Geographic Location:Costs may vary between suppliers and regions due to differences in labor costs, regulatory requirements, and infrastructure.
- Market Demand: Fluctuations in market demand and availability of materials can also impact pricing.
Given these factors, providing an exact cost without specific details on the substrate’s specifications, manufacturing volume, and other variables is challenging. Typically, GCPS costs are higher compared to traditional organic or ceramic substrates due to the specialized materials and manufacturing processes involved. For precise cost estimation, consulting with substrate manufacturers or suppliers who can provide detailed quotations based on specific project requirements would be advisable.
What is the Glass Core Package Substrate base material?
The base material of a Glass Core Package Substrate (GCPS) is primarily glass. Specifically, it involves using specially selected and processed glass as the core material for the substrate. This glass is chosen for its specific properties that make it suitable for high-performance electronic packaging applications.
Key considerations for the glass base material in GCPS include:
- Thermal Expansion Coefficient (CTE): The glass material must have a CTE that closely matches that of semiconductor materials (such as silicon chips) to minimize thermal stress during operation and thermal cycling.
- Electrical Properties: Glass substrates used in electronic packaging are typically engineered to have low dielectric constants and low loss tangents to ensure good signal integrity and minimal signal loss.
- Mechanical Strength: Glass must possess sufficient mechanical strength and rigidity to support the structure and protect components during handling and operation.
- Surface Quality: The surface of the glass substrate is prepared to be smooth and clean, suitable for thin film deposition and subsequent processing steps like photolithography and etching.
- Environmental Stability: Glass should be resistant to environmental factors such as moisture, chemicals, and temperature variations, ensuring long-term reliability in electronic devices.
Manufacturers may apply special treatments to the glass base material to enhance its properties, such as improving adhesion for deposited layers, adjusting thermal properties, or strengthening mechanical resilience. Overall, the choice and preparation of the glass base material are critical to achieving the desired electrical performance, thermal management capabilities, and mechanical reliability in Glass Core Package Substrates.
Which company makes Glass Core Package Substrates?
Currently, several companies manufacture Glass Core Package Substrates (GCPS), including major international electronics materials manufacturers and technology leaders. For instance, companies like Corning, AGC Inc., Schott AG, Nippon Electric Glass, and Asahi Glass have extensive experience and technical expertise in glass materials, producing high-quality glass-based packaging substrates widely used in electronic device packaging and protection.
Our company also manufactures Glass Core Package Substrates. As a specialist in high-performance electronic materials and packaging solutions, we possess advanced manufacturing facilities and a skilled technical team capable of customizing and producing high-quality GCPS tailored to specific customer requirements. Our manufacturing processes strictly adhere to international standards and quality management systems to ensure that our products meet the technical specifications and market standards expected by our customers.
We are committed to continuous innovation and development in the field of GCPS, offering advanced materials and process solutions to meet the increasing demands for complexity and high performance in electronic products. Our products not only deliver excellent electrical performance, thermal management capabilities, and mechanical reliability but also maintain stability and long-term reliability under various environmental conditions.
If you have further requirements for Glass Core Package Substrates or other electronic materials, or if you would like more detailed information, please feel free to contact us. We are dedicated to providing technical support and solutions to meet your needs.
What are the 7 qualities of good customer service?
The seven qualities of good customer service typically include:
- Responsiveness: Promptly addressing customer inquiries, concerns, and requests shows attentiveness and respect for their time.
- Empathy: Understanding and empathizing with the customer’s situation demonstrates care and helps build rapport.
- Clear Communication: Communicating clearly and effectively, both verbally and in writing, ensures mutual understanding and reduces misunderstandings.
- Knowledgeability: Having sufficient product or service knowledge to answer questions accurately and provide helpful information instills confidence and trust in the customer.
- Professionalism: Conducting interactions with professionalism, courtesy, and respect enhances the customer’s experience and reflects positively on the company.
- Problem-Solving Skills: Being able to resolve issues efficiently and effectively, whether simple or complex, contributes significantly to customer satisfaction.
- Follow-Up: Following up with customers to ensure their issues were resolved satisfactorily or to gather feedback shows commitment to their satisfaction and helps improve service quality.
These qualities collectively contribute to creating a positive customer service experience, fostering customer loyalty, and building a strong reputation for the company.
FAQs
What are Glass Core Package Substrates (GCPS)?
GCPS are advanced packaging materials where specially treated glass serves as the core substrate. They are used in electronic devices for their superior electrical, thermal, and mechanical properties.
What are the advantages of using GCPS?
GCPS offer benefits such as excellent thermal management, high electrical insulation, and compatibility with high-frequency signals. They also provide robust mechanical support and can be customized for specific application needs.
How are GCPS different from traditional substrates?
Unlike traditional organic or ceramic substrates, GCPS leverage the unique properties of glass, including low dielectric constant, precise thermal expansion matching, and superior surface flatness, making them ideal for high-performance electronic packaging.
What applications are GCPS suitable for?
GCPS are used in various applications requiring high reliability and performance, including in telecommunications, aerospace, automotive electronics, and medical devices, among others.
What considerations are important when choosing GCPS?
Key factors include thermal expansion coefficient (CTE) matching with semiconductor materials, dielectric properties, mechanical strength, and the ability to customize layers for specific circuitry and thermal management needs.
How are GCPS manufactured?
The manufacturing process involves steps such as selecting high-quality glass, depositing thin conductive and dielectric layers, photolithography for patterning, via formation, and surface finishing. Each step ensures precise control over electrical, thermal, and mechanical properties.
Where can I find suppliers of GCPS?
Several companies specialize in manufacturing GCPS, offering customized solutions based on specific application requirements. Leading suppliers include global electronics materials manufacturers and specialized substrate providers.