FR408HR Materials PCB Manufacturer
FR408HR Materials PCB Manufacturer,FR408HR Materials PCB is a high-performance printed circuit board made from FR408HR composite material with outstanding electrical characteristics and thermal stability. The material boasts a low dielectric constant, approximately 4.08, making it suitable for high-frequency applications such as communication equipment, aerospace systems, and radar systems. During the design and manufacturing process of FR408HR PCBs, special attention is required for aspects like layer stackup design, impedance control, signal routing, thermal management, and surface treatment. Compared to standard FR-4 material, FR408HR Materials PCB offers superior electrical performance and thermal stability, ensuring reliable functionality. By adhering to strict design guidelines and manufacturing processes, FR408HR Materials PCBs can meet the requirements of high-speed data transmission and signal integrity, making them an ideal choice for many high-performance electronic applications.
What is FR408HR Materials PCB?
FR408HR is a high-performance laminate material used in printed circuit boards (PCBs). It’s a type of composite material made primarily of woven glass reinforcement and epoxy resin. The “FR” stands for “flame retardant,” indicating its ability to resist combustion and reduce the spread of flames in case of fire. The “408” in its name refers to its dielectric constant (εr) of approximately 4.08, which is a measure of its ability to store electrical energy in an electric field. This low dielectric constant makes it suitable for high-frequency applications where signal integrity is critical. The “HR” stands for “high reliability,” denoting its enhanced performance and durability compared to standard FR408 laminates.
FR408HR PCBs offer several advantages, including excellent electrical properties, low signal loss, stable dielectric constant over a wide range of frequencies, and high thermal reliability. These characteristics make it ideal for demanding applications such as telecommunications equipment, aerospace systems, high-speed data transmission, and radar systems.
Furthermore, FR408HR laminates exhibit good dimensional stability, meaning they maintain their shape and size under various environmental conditions and mechanical stresses. This stability is crucial for ensuring the accuracy and reliability of electronic components mounted on the PCB.
Overall, FR408HR materials provide designers with a reliable solution for high-frequency and high-speed circuitry, offering a balance of electrical performance, thermal stability, and mechanical strength necessary for advanced electronic applications.
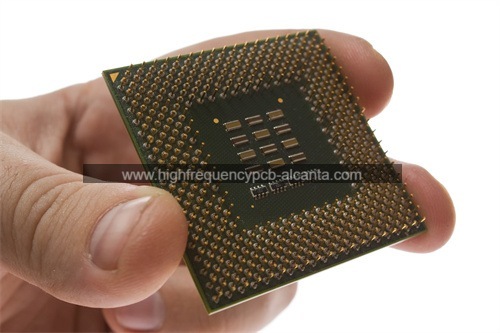
FR408HR Materials PCB Manufacturer
What are the PCB Design Guidelines for FR408HR Materials PCB?
Designing a printed circuit board (PCB) with FR408HR materials requires careful consideration of various factors to ensure optimal performance and reliability. Here are some important PCB design guidelines specific to FR408HR materials:
- Layer Stackup Design: Optimize the layer stackup to achieve desired impedance control and signal integrity. FR408HR laminates typically have specific dielectric thicknesses and copper weights, so ensure the layer stackup adheres to manufacturer recommendations for optimal electrical performance.
- Impedance Control: FR408HR materials are often used in high-speed and high-frequency applications where impedance matching is critical. Design controlled impedance traces using appropriate widths, spacing, and layer configurations to maintain signal integrity and minimize signal distortions.
- Transmission Line Routing: Route high-speed signal traces as transmission lines with proper impedance control techniques such as controlled trace width, differential pair routing, and impedance matching structures like microstrips or striplines.
- Ground and Power Planes: Design robust ground and power planes to provide low impedance return paths, minimize noise, and ensure stable power distribution throughout the PCB. Implement split planes carefully to avoid impedance mismatches and signal integrity issues.
- Component Placement: Place components strategically to minimize signal path lengths, reduce parasitic capacitance and inductance, and optimize signal integrity. Pay attention to high-speed components, critical signal paths, and thermal considerations when placing components on the board.
- Thermal Management: FR408HR laminates offer good thermal stability, but efficient heat dissipation is still crucial, especially in high-power or densely populated PCBs. Ensure adequate thermal relief for vias and thermal vias to facilitate heat transfer away from heat-generating components.
- Via Design:Use appropriate via structures such as blind vias, buried vias, and via stub minimization techniques to maintain signal integrity and impedance control, especially in high-frequency designs.
- Design for Manufacturability (DFM): Follow DFM guidelines to ensure the design can be manufactured reliably and cost-effectively. Consider manufacturability aspects such as minimum trace widths, minimum annular ring sizes, and panelization requirements during PCB layout.
- Signal Integrity Analysis: Perform signal integrity simulations and analysis using tools like electromagnetic field solvers or signal integrity analysis software to validate the design and predict potential issues such as impedance mismatches, crosstalk, and signal reflections.
- Testing and Validation: Conduct thorough testing and validation of the PCB design to verify its performance against specifications and requirements. Use techniques like time-domain reflectometry (TDR) and network analyzers to measure impedance, signal integrity, and other electrical parameters.
By adhering to these PCB design guidelines specific to FR408HR materials, designers can ensure the reliable operation and optimal performance of high-speed and high-frequency electronic systems.
What is the PCB Fabrication Process for FR408HR Materials PCB?
The PCB fabrication process for FR408HR materials follows standard procedures with some considerations specific to the characteristics of the material. Here’s an overview of the typical fabrication process:
- Material Selection: Choose FR408HR laminate material based on the specific requirements of the PCB design, considering factors such as dielectric constant, thickness, and copper weight. Ensure that the material meets the performance and reliability standards for the intended application.
- Preparation of Substrate: Cut the FR408HR laminate sheets to the required size for the PCB panels. Clean the substrate surfaces to remove any contaminants that could affect adhesion during the subsequent processes.
- Layer Stackup Preparation: Determine the layer stackup configuration based on the PCB design requirements, including the number of layers, signal, power, and ground planes. Prepare the layer stack by laminating the FR408HR cores with copper foils on both sides.
- Drilling: Drill the required holes for vias, through-holes, and component mounting pads using precision drilling machines. Consider the aspect ratio limitations of the material and drill size tolerances to avoid issues such as burring or delamination.
- Copper Patterning: Apply a photoresist layer onto the copper foils and expose it to UV light through a photomask to transfer the PCB pattern onto the copper surfaces. Develop and etch the exposed copper areas to create the desired circuit traces and features.
- Inner Layer Inspection: Conduct thorough inspections of the inner layers to ensure the accuracy of the copper patterning, registration, and quality of the vias. Repair any defects or errors found during inspection.
- Lamination: Assemble the PCB stackup by bonding the inner layers together with prepreg layers and copper foil outer layers using heat and pressure in a lamination press. Ensure proper alignment and registration of the layers to maintain signal integrity and reliability.
- Drill Registration and Plating: Precisely align the drilled holes with the inner layer circuitry using optical registration systems. Plate the drilled holes with copper to create conductive vias that establish electrical connections between layers.
- Outer Layer Patterning: Repeat the copper patterning process on the outer layers to define the final circuit traces, pads, and solder mask openings. Apply solder mask over the exposed copper areas to protect them from oxidation and facilitate soldering.
- Surface Finish: Apply a surface finish to the exposed copper pads to improve solderability and prevent oxidation. Common surface finishes for FR408HR PCBs include HASL (Hot Air Solder Leveling), ENIG (Electroless Nickel Immersion Gold), and OSP (Organic Solderability Preservative).
- Final Inspection and Testing: Perform comprehensive inspections and electrical testing to verify the integrity, quality, and functionality of the finished PCBs. Inspect for defects such as shorts, opens, misalignments, and dimensional inaccuracies.
- Routing and Separation: Route individual PCBs from the panel and separate them using routing or depanelization techniques. Clean the boards to remove any residues or contaminants accumulated during fabrication.
- Packaging and Shipping: Package the finished PCBs according to customer specifications and industry standards to protect them during transit. Label the packages with relevant information and documentation for easy identification and traceability.
Throughout the fabrication process, it’s essential to follow industry best practices, quality standards, and manufacturer recommendations specific to FR408HR materials to ensure the production of high-quality, reliable PCBs suitable for demanding applications.
How do you manufacture FR408HR Materials PCB?
Manufacturing FR408HR materials PCB involves several steps, including material preparation, circuit patterning, layer stacking, drilling, plating, and finishing. Here’s a detailed overview of the manufacturing process:
- Material Selection: Choose FR408HR laminate material based on the specific requirements of the PCB design, considering factors such as dielectric constant, thickness, and copper weight. Ensure that the material meets the performance and reliability standards for the intended application.
- Panel Preparation: Cut the FR408HR laminate sheets to the required size for the PCB panels. Clean the substrate surfaces to remove any contaminants that could affect adhesion during the subsequent processes.
- Copper Cladding: Apply copper foil to both sides of the FR408HR laminate panels using an adhesive bonding process. Ensure proper lamination of the copper foil to the substrate to achieve good adhesion and conductivity.
- Circuit Patterning (Inner Layers): Apply a layer of photoresist to the copper-clad panels and expose them to UV light through a photomask to transfer the PCB pattern onto the photoresist layer. Develop and etch the exposed copper areas to create the desired circuit traces and features on the inner layers.
- Inspection (Inner Layers): Conduct inspections of the inner layers to verify the accuracy of the circuit patterning, registration, and quality of the vias. Repair any defects or errors found during inspection.
- Layer Stacking: Assemble the PCB stackup by bonding the inner layers together with prepreg layers using heat and pressure in a lamination press. Ensure proper alignment and registration of the layers to maintain signal integrity and reliability.
- Drilling: Precisely drill the required holes for vias, through-holes, and component mounting pads using computer-controlled drilling machines. Consider the aspect ratio limitations of the material and drill size tolerances to avoid issues such as burring or delamination.
- Copper Plating (Electroless and Electroplating): Plate the drilled holes with copper to create conductive vias that establish electrical connections between layers. Use a combination of electroless and electroplating processes to deposit copper uniformly inside the drilled holes.
- Circuit Patterning (Outer Layers): Apply a layer of photoresist to the outer copper layers and expose them to UV light through a photomask to define the final circuit traces, pads, and solder mask openings. Develop and etch the exposed copper areas to create the desired features on the outer layers.
- Surface Finish: Apply a surface finish to the exposed copper pads to improve solderability and prevent oxidation. Common surface finishes for FR408HR PCBs include HASL (Hot Air Solder Leveling), ENIG (Electroless Nickel Immersion Gold), and OSP (Organic Solderability Preservative).
- Solder Mask Application: Apply solder mask over the exposed copper areas on both sides of the PCB to protect them from oxidation and facilitate soldering. Define openings in the solder mask for component pads, vias, and other necessary areas.
- Final Inspection and Testing: Perform comprehensive inspections and electrical testing to verify the integrity, quality, and functionality of the finished PCBs. Inspect for defects such as shorts, opens, misalignments, and dimensional inaccuracies.
- Routing and Separation: Route individual PCBs from the panel and separate them using routing or depanelization techniques. Clean the boards to remove any residues or contaminants accumulated during fabrication.
- Packaging and Shipping: Package the finished PCBs according to customer specifications and industry standards to protect them during transit. Label the packages with relevant information and documentation for easy identification and traceability.
Throughout the manufacturing process, it’s essential to follow industry best practices, quality standards, and manufacturer recommendations specific to FR408HR materials to ensure the production of high-quality, reliable PCBs suitable for demanding applications.
How much should FR408HR Materials PCB cost?
The cost of FR408HR materials PCB can vary widely depending on several factors such as board size, complexity, layer count, copper weight, surface finish, tolerances, quantity ordered, and the manufacturer’s capabilities and pricing structure. However, to provide a general idea:
- Material Cost: FR408HR laminate material tends to be more expensive compared to standard FR-4 materials due to its high-performance characteristics. The cost of FR408HR laminate can range from $5 to $20 per square foot or more, depending on the specific grade, thickness, and supplier.
- Manufacturing Costs: PCB manufacturing costs include various processes such as material procurement, fabrication, assembly, testing, and finishing. For FR408HR PCBs, expect manufacturing costs to be higher than those for standard FR-4 PCBs due to the more complex manufacturing processes and higher material costs.
- Design Complexity: The complexity of the PCB design, including factors such as the number of layers, fine trace widths, tight tolerances, blind/buried vias, and HDI (High-Density Interconnect) features, can significantly impact the overall manufacturing cost.
- Surface Finish and Copper Weight: The choice of surface finish (e.g., HASL, ENIG, OSP) and copper weight (e.g., 1 oz, 2 oz) can influence the cost of FR408HR PCBs. Finishes like ENIG tend to be more expensive than HASL due to the additional processing steps involved.
- Quantity Ordered: Economies of scale often apply in PCB manufacturing, meaning that larger order quantities typically result in lower per-unit costs. However, ordering small quantities or prototypes may incur higher costs per unit due to setup fees and less efficient production processes.
- Supplier and Location: The choice of PCB manufacturer and their location can affect pricing due to differences in labor costs, overhead expenses, and shipping fees.
As a rough estimate, the cost of FR408HR materials PCBs can range from $10 to $100 or more per square inch for small quantities, while larger production runs may lower the cost to a few dollars per square inch. For accurate pricing, it’s advisable to consult with PCB manufacturers and provide detailed specifications of your project for a customized quote.
What is FR408HR Materials PCB base material?
FR408HR is a high-performance laminate material used as the base material in PCB (printed circuit board) fabrication. It’s a composite material consisting primarily of woven glass reinforcement and epoxy resin.
The main components of FR408HR material include:
- Woven Glass Reinforcement: This provides mechanical strength and dimensional stability to the laminate. The woven glass fibers are impregnated with epoxy resin to form a sturdy substrate.
- Epoxy Resin: Epoxy resin acts as a binder, holding the glass fibers together and providing insulation properties. It also contributes to the material’s rigidity and thermal stability.
- Fillers and Additives: FR408HR may contain various fillers and additives to enhance specific properties such as flame retardancy, thermal conductivity, and electrical performance.
FR408HR materials are engineered to offer high electrical performance, low signal loss, stable dielectric constant over a wide frequency range, and excellent thermal reliability. These properties make FR408HR ideal for high-speed digital and RF (radio frequency) applications where signal integrity and reliability are critical.
Overall, FR408HR serves as a robust and reliable base material for manufacturing PCBs that require high-frequency performance and stringent quality standards.
Which company makes FR408HR Materials PCB?
There are many FR408HR material PCB manufacturing companies, some of the well-known companies include Isola and Rogers Corporation in the United States. These companies have extensive experience and technical strength in the field of high-performance PCB materials and are able to produce FR408HR material PCBs that meet strict requirements.
As our company, we also have the capability and experience to produce FR408HR material PCB. We have advanced production equipment, technical team and quality management system to meet our customers’ needs for high-performance PCBs. We focus on product quality and customer satisfaction, and strictly control every link during the production process to ensure the production of high-quality FR408HR material PCBs that meet specifications.
Our company has extensive experience in PCB manufacturing and is able to provide a full range of services from samples to high-volume production. Whether the customer’s needs are rapid prototyping or large-scale production orders, we can meet them and guarantee timely delivery. At the same time, we also provide flexible customization services and customize PCB design and manufacturing solutions according to customers’ specific needs to meet the requirements of different application scenarios.
In addition to producing high-quality FR408HR material PCBs, we are also committed to continuous innovation and upgrading of technology to meet the evolving market needs. We pay attention to the latest technological trends and standard requirements in the industry, constantly optimize production techniques and processes, and provide customers with better products and services.
In short, as a PCB manufacturing company with rich experience and professional technology, we have the ability to produce FR408HR material PCBs that meet high-performance requirements, and provide customers with a full range of customized services and technical support to jointly promote the development of the electronics industry.
What are the 7 qualities of good customer service?
Good customer service is essential for building positive relationships with customers and fostering loyalty. Here are seven qualities that contribute to providing excellent customer service:
- Responsiveness: Customers appreciate prompt responses to their inquiries, concerns, or requests. Being readily available and acknowledging customer needs in a timely manner demonstrates attentiveness and commitment to customer satisfaction.
- Empathy:Empathy involves understanding and sharing the feelings of customers, especially when they encounter challenges or frustrations. Showing empathy by listening actively, acknowledging their emotions, and demonstrating genuine concern helps build rapport and trust.
- Clear Communication: Effective communication is key to resolving issues and providing accurate information to customers. Communicate clearly, using simple language, and avoid technical jargon. Ensure that customers understand the solutions or instructions provided.
- Product Knowledge: Having comprehensive knowledge about products or services enables customer service representatives to address inquiries, offer recommendations, and troubleshoot effectively. Educate staff members about your offerings to empower them to assist customers effectively.
- Problem-Solving Skills: Customers often seek assistance to resolve issues or overcome challenges. Customer service representatives should possess strong problem-solving skills to identify root causes, explore solutions, and resolve issues efficiently, ensuring customer satisfaction.
- Professionalism: Maintain a professional demeanor at all times, regardless of the situation. Treat customers with respect, courtesy, and patience, even in challenging interactions. Uphold ethical standards and company policies while delivering service.
- Follow-Up and Feedback: After resolving customer issues, follow up to ensure their satisfaction and address any lingering concerns. Encourage feedback to gather insights into customer experiences and identify areas for improvement. Utilize feedback to enhance service quality and exceed customer expectations.
By embodying these qualities, businesses can deliver exceptional customer service experiences that leave a positive impression on customers and foster long-term loyalty.
FAQs
What is FR408HR material?
FR408HR is a high-performance laminate material used in printed circuit boards (PCBs). It offers excellent electrical properties, low signal loss, stable dielectric constant over a wide frequency range, and high thermal reliability.
What are the key characteristics of FR408HR material?
FR408HR material is known for its low dielectric constant (typically around 4.08), which is crucial for high-frequency applications. It also exhibits good thermal stability, mechanical strength, and dimensional stability.
What are the applications of FR408HR materials PCB?
FR408HR PCBs are used in various high-frequency and high-speed applications such as telecommunications equipment, aerospace systems, radar systems, high-speed data transmission, and networking infrastructure.
How does FR408HR material compare to standard FR-4 material?
FR408HR material offers superior electrical performance and thermal reliability compared to standard FR-4 material. It has a lower dielectric constant, reduced signal loss, and better impedance control, making it suitable for demanding applications.
What are the fabrication considerations for FR408HR materials PCB?
Fabricating FR408HR PCBs requires careful attention to factors such as layer stackup design, impedance control, transmission line routing, thermal management, and surface finish selection to ensure optimal performance and reliability.
Where can I source FR408HR materials PCB?
FR408HR materials PCBs can be sourced from various PCB manufacturers and suppliers specializing in high-performance materials. It’s essential to choose a reputable supplier with experience in handling FR408HR materials and meeting quality standards.
What are the cost implications of using FR408HR materials PCB?
The cost of FR408HR materials PCBs can vary depending on factors such as board size, complexity, layer count, surface finish, and quantity ordered. Generally, FR408HR PCBs may be more expensive than standard FR-4 PCBs due to the higher material cost and specialized manufacturing processes.
Are there any design guidelines specific to FR408HR materials PCB?
Yes, there are specific design guidelines for FR408HR materials PCB, including considerations for layer stackup design, impedance control, transmission line routing, ground and power planes, thermal management, via design, and testing/validation. Adhering to these guidelines ensures optimal performance and reliability.