Flip Chip RF Substrates Manufacturer
Flip Chip RF Substrates Manufacturer,Flip Chip RF substrates are specialized materials designed for high-frequency and high-performance applications. These substrates support flip chip packaging, where the integrated circuit is mounted face-down onto the substrate, enabling improved electrical connectivity and reduced signal path lengths. They are crafted from materials with low dielectric loss and high thermal conductivity to handle the demands of radio frequency (RF) signals effectively. Ideal for use in communication systems, radar, and other RF applications, these substrates ensure minimal signal degradation, enhanced performance, and reliable thermal management. Their design facilitates high-density interconnections and supports advanced RF circuitry in compact and efficient layouts.
What is a Flip Chip RF Substrate?
A Flip Chip RF Substrate is a specialized type of substrate used in the fabrication of high-frequency integrated circuits, particularly those used in radio frequency (RF) applications. It is designed to support flip chip technology, where the integrated circuit (IC) is mounted upside down on the substrate. This mounting method allows for a high-density interconnection and reduces the inductance and resistance in the signal paths, which is crucial for maintaining signal integrity in high-frequency applications.
The RF substrate provides a stable and high-performance platform for the IC, featuring materials that offer low dielectric losses and high thermal conductivity. Common materials used for RF substrates include advanced ceramics, high-frequency laminates, or composite materials with tailored electrical properties. The substrate’s design includes carefully engineered signal traces, grounding, and shielding to minimize interference and signal degradation.
In addition to supporting the flip chip assembly, RF substrates often have intricate features like microvias and embedded passive components to further optimize performance. These substrates are used in various high-performance applications, including RF and microwave communication systems, satellite communications, and advanced radar systems. Their ability to handle high frequencies while providing excellent signal integrity makes them critical components in modern electronic systems.
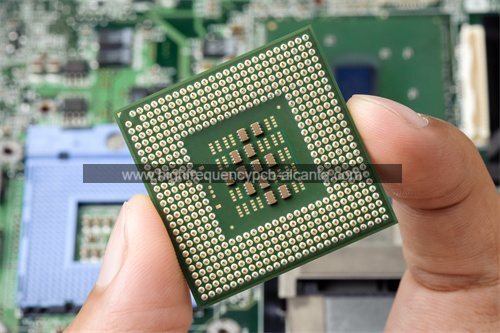
Flip Chip RF Substrates Manufacturer
What are the Flip Chip RF Substrate Design Guidelines?
Designing Flip Chip RF Substrates involves several key guidelines to ensure high performance and reliability in RF applications. Here are the main considerations:
- 1. Material Selection: Choose materials with low dielectric loss and high thermal conductivity to minimize signal attenuation and heat buildup. Common materials include high-frequency laminates like Rogers or Arlon, and advanced ceramics for their superior electrical properties.
- Impedance Matching: Ensure proper impedance matching between the flip chip and the RF substrate to minimize signal reflections and maximize power transfer. This involves designing trace widths and spacing according to the substrate’s dielectric properties.
- Signal Integrity: Design trace geometries to control impedance and reduce signal distortion. Use microstrip or stripline configurations and pay attention to trace lengths and angles to prevent signal degradation.
- Grounding and Shielding: Implement effective grounding techniques and shield the RF traces to prevent interference and crosstalk. Use ground planes and keep them as close to the signal layers as possible to provide a solid reference ground and minimize noise.
- Thermal Management: Design the substrate to manage heat dissipation effectively. Include thermal vias, heat spreaders, or metalized areas to transfer heat away from the flip chip and prevent overheating.
- Via and Pad Design: Use appropriately sized vias and pads for reliable electrical connections. Ensure that vias are optimized for high-frequency signals and that pad sizes support reliable soldering and electrical performance.
- Mechanical Considerations: Design for mechanical stability and durability, especially in high-stress environments. Account for thermal expansion differences between the flip chip and substrate to prevent mechanical stress and potential delamination.
- Manufacturability: Ensure that the substrate design can be produced using available fabrication techniques and equipment. Consider factors such as minimum feature sizes and tolerances to avoid manufacturing issues.
- Testing and Validation: Include test points and design for in-circuit testing to validate performance. Perform thorough testing to ensure the substrate meets all RF performance specifications and reliability standards.
By adhering to these guidelines, designers can create flip chip RF substrates that meet the stringent requirements of high-frequency applications, ensuring optimal performance and reliability.
What is the Flip Chip RF Substrate Fabrication Process?
The fabrication process for Flip Chip RF Substrates involves several detailed steps to create a high-performance platform for mounting integrated circuits. Here’s a general overview of the process:
- Material Preparation: Start with selecting and preparing the substrate material, which could be high-frequency laminate, ceramic, or composite material. The choice of material is based on the desired electrical properties and application requirements.
- Layer Deposition: Apply a base layer of conductive material, typically copper, onto the substrate. This layer forms the initial circuitry and is used for etching the signal traces. In multi-layer substrates, additional layers of dielectric material and copper are sequentially added and bonded.
- Patterning and Etching: Use photolithography to apply a photoresist coating onto the copper layer. Expose the photoresist to light through a mask to define the circuitry pattern. Develop the photoresist to reveal the underlying copper, then etch away the unprotected copper to form the desired trace patterns.
- Via Formation: Drill or laser-cut vias (holes) through the substrate to connect different layers of circuitry. For high-frequency applications, ensure that the vias are precisely placed and sized to maintain signal integrity and reduce losses.
- Plating and Coating: Plate the vias with a thin layer of metal, such as copper or gold, to ensure good electrical connection between layers. Apply additional coatings if necessary to protect the circuitry from environmental factors and enhance performance.
- Solder Mask Application: Apply a solder mask layer over the circuitry to protect it during soldering and to prevent short circuits. The solder mask is patterned to expose areas where solder will be applied, such as pad locations.
- Surface Finish: Apply a surface finish, such as electroplated gold or immersion silver, to the exposed pads. This finish helps in achieving reliable solder joints when mounting the flip chip and provides additional protection against oxidation.
- Flip Chip Assembly:Position and align the flip chip (IC) onto the substrate. The flip chip is typically mounted using solder bumps or balls that reflow during soldering to create electrical connections between the chip and substrate.
- Reflow Soldering: Heat the assembly to reflow the solder bumps or balls, establishing electrical and mechanical connections between the flip chip and the substrate. Ensure precise temperature control to avoid damage to the components.
- Inspection and Testing: Perform detailed inspection and testing of the substrate and assembled flip chip. Check for soldering quality, signal integrity, and overall functionality. Common tests include electrical testing, thermal testing, and visual inspection.
- Final Assembly:Complete any additional processes, such as encapsulation or packaging, to protect the substrate and integrated circuit. Ensure that the final product meets all performance and reliability standards before shipping.
This fabrication process ensures that flip chip RF substrates are built to support high-frequency applications effectively, maintaining signal integrity and reliability throughout their operational lifespan.
How do You Manufacture a Flip Chip RF Substrate?
Manufacturing a Flip Chip RF Substrate involves several critical steps to ensure high performance and reliability. Here’s a comprehensive overview of the process:
- Material Selection and Preparation: Choose a suitable substrate material, such as high-frequency laminate or ceramic. Prepare the material by cutting it to the desired size and thickness.
- Copper Foil Lamination: Apply a thin layer of copper foil to the substrate material using a lamination process. This copper layer forms the basis for creating the circuit patterns.
- Photolithography: Coat the copper layer with a photoresist material. Use photolithography to project a circuit pattern onto the photoresist through a mask. Develop the photoresist to reveal the copper layer underneath where the circuit will be etched.
- Etching: Remove the exposed copper using an etching solution, leaving behind the desired circuit traces and pads. Ensure precise control over the etching process to maintain trace integrity and performance.
- Via Drilling and Plating: Drill or laser-cut vias through the substrate where necessary. These vias allow for inter-layer connections. Plate the vias with a conductive material, typically copper, to ensure electrical connectivity between different layers of the substrate.
- Additional Layering: For multi-layer substrates, apply additional layers of dielectric material and copper foil. Repeat the photolithography, etching, and via plating steps for each layer. Ensure alignment between layers to maintain circuit integrity.
- Solder Mask Application: Apply a solder mask to the substrate to protect the circuitry and define areas where solder will be applied. Pattern the solder mask to expose the pads where the flip chip will be mounted.
- Surface Finish: Apply a surface finish to the exposed pads to enhance solderability and protect against oxidation. Common finishes include electroplated gold, immersion silver, or other suitable options based on the application requirements.
- Flip Chip Placement: Align and place the flip chip (IC) onto the substrate. The flip chip is equipped with solder bumps or balls that will form electrical connections when reflowed.
- Reflow Soldering: Heat the assembly to reflow the solder bumps or balls, establishing reliable electrical and mechanical connections between the flip chip and the substrate. Carefully control the temperature to avoid damage to sensitive components.
- Inspection and Testing:Conduct thorough inspections and testing of the substrate and assembled flip chip. This includes visual inspection, electrical testing for continuity and performance, and thermal testing to ensure the substrate can handle operating conditions.
- Final Processing: Complete any additional processes such as encapsulation or packaging to protect the substrate and flip chip assembly. Ensure that the final product meets all design specifications and reliability standards.
By following these steps, manufacturers can produce high-quality Flip Chip RF Substrates that meet the demanding requirements of high-frequency applications.
How Much Should a Flip Chip RF Substrate Cost?
The cost of a Flip Chip RF Substrate can vary significantly based on several factors. Here’s a breakdown of key factors influencing the cost:
- Material: High-frequency materials such as advanced laminates (e.g., Rogers, Arlon) or ceramics typically cost more than standard materials. The choice of material affects both performance and cost.
- Complexity: The complexity of the substrate design, including the number of layers, trace patterns, and via configurations, impacts the cost. More complex designs require more intricate manufacturing processes.
- Size and Thickness:Larger and thicker substrates generally cost more due to increased material usage and manufacturing time.
- Quantity: Production volume affects cost. Higher quantities usually lead to lower per-unit costs due to economies of scale. Low-volume or prototype runs are typically more expensive per unit.
- Manufacturing Technology: Advanced manufacturing techniques, such as high-precision photolithography, laser drilling, and fine-pitch plating, can increase costs. The use of state-of-the-art equipment and processes adds to the overall expense.
- Surface Finish: The type of surface finish applied (e.g., gold plating, immersion silver) affects cost. More expensive finishes provide better performance and durability but increase the substrate’s price.
- Lead Time: Shorter lead times for manufacturing can lead to higher costs. Rush orders or expedited production often incur additional charges.
- Testing and Inspection: Comprehensive testing and quality control procedures add to the overall cost. High-performance substrates for critical applications require extensive testing to ensure reliability.
As a rough estimate, the cost for a standard Flip Chip RF Substrate might range from $50 to $500 per unit, depending on the above factors. For high-complexity or high-performance designs, costs can exceed this range. For specific quotes, it’s best to consult with manufacturers who can provide detailed pricing based on the exact requirements and specifications of the substrate.
What is Flip Chip RF Substrate Base Material?
The base material for Flip Chip RF Substrates is crucial to their performance, particularly in high-frequency applications. Here’s an overview of common base materials used:
- High-Frequency Laminates: These are specialized materials designed to handle high-frequency signals with minimal loss. Common types include:
– Rogers Materials: Known for their low dielectric loss and stable electrical properties, Rogers laminates (like RO4000 and RO3000 series) are widely used in RF applications.
– Arlon Materials: Arlon offers high-frequency laminates such as ARlon 25N and ARlon 4000 series, which provide low loss and excellent thermal stability.
- Ceramic Substrates: Ceramic materials offer high dielectric constants and low loss, making them suitable for high-frequency applications. Common ceramics used include:
– Alumina (Al2O3): Provides high thermal conductivity and electrical performance.
– Barium Titanate (BaTiO3): Offers high dielectric constant and low loss.
- Polyimide Films: These are used for flexible RF substrates or in combination with other materials. Polyimide films are known for their high thermal stability and mechanical properties.
- Composite Materials: These materials combine different substances to achieve desired electrical and mechanical properties. They can be tailored to specific needs by adjusting the composition of the base material.
- PTFE-Based Materials: Polytetrafluoroethylene (PTFE) and its composites (such as Teflon) are used for their low dielectric loss and high-frequency performance.
The choice of base material impacts the substrate’s electrical performance, thermal management, and overall reliability. For RF applications, materials with low dielectric loss, high thermal conductivity, and stable electrical properties are essential to ensure signal integrity and efficient performance.
Which Company Makes Flip Chip RF Substrates?
Several companies manufacture Flip Chip RF Substrates, including:
- Rogers Corporation: Rogers is a leader in high-frequency materials, offering various high-performance RF substrate materials such as the RO4000 and RO3000 series. These materials are known for their low dielectric loss and high stability, widely used in high-frequency and high-power electronic devices.
- Arlon Electronic Materials: Arlon provides a range of high-frequency substrate materials, such as the ARlon 25N and ARlon 4000 series. These materials are renowned for their excellent electrical performance and thermal stability, suitable for high-frequency applications and high-power circuits.
- Taconic: Taconic manufactures high-frequency materials, including the TLY and TSM series, known for their low dielectric loss and excellent electrical performance, ideal for high-frequency communications and RF applications.
- Isola Group: Isola offers various high-performance substrate materials suitable for high-frequency applications, such as the IS680, IS550, and IS400 series. They exhibit outstanding performance in high-frequency signal transmission.
- Mitsubishi Materials: Mitsubishi’s high-frequency materials, including the MU-10 and MU-1000 series, focus on low dielectric loss and high thermal conductivity, suitable for high-frequency and RF applications.
- DuPont: DuPont provides high-frequency materials such as the Pyralux and Kapton series, offering good performance and stability in high-frequency electronic applications.
Our company also manufactures Flip Chip RF Substrates. We are committed to delivering high-quality RF substrates that meet the needs of customers in high-frequency and high-power applications. Our Flip Chip RF Substrates are made using advanced manufacturing processes and high-performance materials, ensuring signal integrity and reliability. We offer customized solutions to meet specific customer requirements, including material choices, layer counts, circuit complexity, and surface finishes.
With precise process control and stringent quality management, our products excel in high-frequency communications, radar systems, satellite communications, and other high-performance applications. If you have any requirements or want to learn more about our Flip Chip RF Substrates, please feel free to contact us. We will provide professional technical support and solutions tailored to your needs.
What Are the 7 Qualities of Good Customer Service?
Good customer service is crucial for building strong relationships with clients and ensuring their satisfaction. Here are seven key qualities that define excellent customer service:
- Responsiveness: Quick and efficient responses to customer inquiries and issues are essential. Customers appreciate timely feedback and solutions to their problems, whether through phone, email, or chat.
- Empathy: Understanding and sharing the feelings of customers helps build rapport and trust. Empathetic service providers acknowledge customer concerns, show genuine care, and strive to address their needs effectively.
- Knowledgeability: Well-informed customer service representatives possess a deep understanding of the products or services they support. They can provide accurate information, answer questions, and resolve issues confidently.
- Patience: Patience is vital, especially when dealing with frustrated or confused customers. Taking the time to listen and explain things clearly without rushing helps ensure a positive customer experience.
- Communication Skills: Clear and effective communication is crucial. This includes using simple language, avoiding jargon, and ensuring that the customer fully understands the information or instructions provided.
- Reliability: Consistency in service quality and follow-through on promises are key to building trust. Reliable customer service means delivering on commitments and resolving issues as promised.
- Personalization:Tailoring interactions to meet individual customer needs and preferences enhances the customer experience. Personalizing service shows that you value each customer and understand their unique requirements.
These qualities collectively contribute to a positive and memorable customer experience, fostering loyalty and encouraging repeat business.
FAQs
What is a Flip Chip RF Substrate?
A Flip Chip RF Substrate is a specialized base material used to mount flip chip integrated circuits (ICs) for high-frequency applications. It provides a platform for the IC and ensures efficient signal transmission and thermal management.
What materials are used for Flip Chip RF Substrates?
Common materials include high-frequency laminates (like Rogers and Arlon), ceramics (such as alumina), and PTFE-based materials. These materials are chosen for their low dielectric loss and high thermal conductivity.
What are the benefits of using Flip Chip RF Substrates?
Benefits include reduced signal loss, improved thermal performance, and higher reliability in high-frequency applications. The flip chip technology allows for a compact and efficient design with reduced parasitic inductance and capacitance.
How are Flip Chip RF Substrates manufactured?
The manufacturing process involves material preparation, copper lamination, photolithography, etching, via drilling, plating, solder mask application, surface finishing, and assembly of the flip chip IC.
What industries use Flip Chip RF Substrates?
They are used in industries such as telecommunications, aerospace, defense, satellite communications, and advanced radar systems where high-frequency performance is critical.
What factors affect the cost of Flip Chip RF Substrates?
Cost factors include the choice of base material, complexity of the design, size and thickness of the substrate, production volume, and additional features like surface finishes and testing requirements.
How do I choose the right Flip Chip RF Substrate?
Selecting the right substrate involves considering the application’s frequency requirements, thermal management needs, electrical performance, and material compatibility with the flip chip IC.