Flip Chip Packaging Substrate Manufacturer
Flip Chip Packaging Substrate Manufacturer,Flip Chip Packaging Substrate is a critical component in semiconductor packaging, facilitating direct connections between the chip and the Printed Circuit Board (PCB). Utilizing flip-chip bonding, it enables the chip’s connections to directly interface with solder pads on the substrate, enhancing electrical performance and miniaturization. Comprising multiple layers including insulating, metal, and conductor layers, Flip Chip Packaging Substrate ensures reliable electrical connections and efficient heat dissipation. Its design supports high-density integration, enabling faster signal transmission and higher power density in electronic devices while maintaining reliability. This substrate technology is pivotal in advancing semiconductor packaging for various applications.
Enter Flip Chip Packaging Substrate, a trailblazing semiconductor packaging technology reshaping how integrated circuits (ICs) connect with their packages or substrates. In this avant-garde methodology, the active side of the IC, home to the semiconductor die, takes a daring flip to establish a direct bond with the substrate or package, breaking free from the traditional vertical IC mounting on substrates.
Distinguishing features that define the essence of Flip Chip Packaging Substrate include:
Minute Marvels – Bump Connections: The utilization of diminutive solder bumps intricately orchestrates connections between the IC’s bond pads and their counterparts on the substrate. These bumps wear the dual hats of electrical and mechanical connectors.
Trimming the Connectivity Fat – Compact Interconnections: The direct tethering of the IC and substrate results in abbreviated interconnections, departing from the drawn-out paths of traditional wire bonding. This paves the way for a boost in electrical prowess and accelerated signal hustle.
Density on Steroids – Amplified I/O Density: Flip chip technology steps up to the plate by accommodating a more intense density of Input/Output (I/O) connections. A boon for high-performance applications craving a plethora of connections.
Thermal Tango at Its Best – Heightened Thermal Performance: Direct hitching of the IC to the substrate sets the stage for a ballet of efficient heat dissipation. The generated heat pirouettes its way directly to the substrate.
Downsizing Elegance – Streamlined Package Dimensions: Opting for flip chip packaging is synonymous with embracing more petite package sizes, a bespoke advantage in domains where spatial frugality is non-negotiable.
Harmony in Signal Symphony – Advancements in Signal Integrity: The fusion of truncated interconnections and direct links orchestrates a symphony of signal integrity enhancements, orchestrating a diminished risk of signal discord.
Flip Chip Packaging Substrate’s ubiquity extends its influence across a myriad of sectors, from high-performance computing to telecommunications and consumer electronics. Its allure lies in its prowess to satiate the escalating appetite for chic form factors, elevated performance benchmarks, and a choreography of efficient heat dissipation.
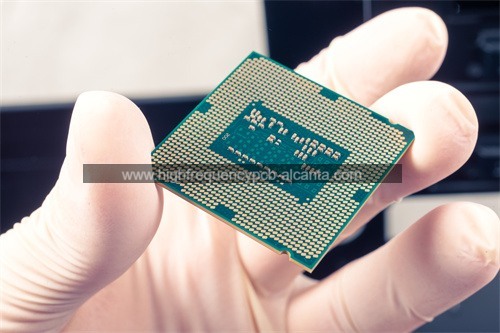
Flip Chip Packaging Substrate Manufacturer
What Functions Does Flip Chip Packaging Substrate Serve?
Flip Chip Packaging Substrate assumes a pivotal role at the nexus of semiconductor packaging and integrated circuit (IC) assembly, executing an array of indispensable functions. Let’s unravel the diverse tapestry of its roles:
Electrical Nexus: At its fundamental essence, Flip Chip Packaging Substrate functions as a nexus for electrical connections. It orchestrates the intricate dance of conductive links between the bond pads on the semiconductor die (IC) and their counterparts on the substrate, choreographing this intricate ballet with solder bumps as the conductive maestros.
Mechanical Sentinel: Beyond its electrical choreography, the substrate transforms into a steadfast mechanical sentinel. The solder bumps, besides their role in electrical connectivity, serve as stalwart sentinels, ensuring the secure mooring of the IC to the substrate.
Streamlined Signal Pathways: Embracing efficiency as its guiding principle, the direct bonding of the IC to the substrate trims the proverbial fat off signal pathways. This deliberate act of streamlining translates into reduced signal propagation delays and an elevation in the overall electrical performance.
Density Dynamo: Flip chip technology flexes its muscles in accommodating a heightened density of input/output (I/O) connections. This attribute proves invaluable in high-performance scenarios where a profusion of connections is a prerequisite for seamless data transfer.
Thermal Maestro: The union of the IC and substrate under the banner of Flip Chip Packaging serves as a maestro in orchestrating efficient heat dissipation. Heat emanating from the IC pirouettes gracefully to the substrate, contributing to a more harmonious thermal management composition.
Spatial Alchemy: Flip chip packaging, with its efficiency ethos, often conjures smaller package sizes compared to conventional methods. This spatial alchemy is a strategic maneuver in applications where spatial considerations wield considerable influence, allowing for more nimble and resourceful device designs.
Guardian of Signal Fidelity: The synergy of truncated interconnections and direct links acts as a vigilant guardian for signal integrity. This concerted effort minimizes the risk of signal degradation, a critical aspect for maintaining the fidelity and reliability of signals in high-speed applications.
Tech Symphony: Flip Chip Packaging Substrate seamlessly harmonizes with advanced technologies such as multi-chip modules and three-dimensional integrated circuits (3D ICs). This adaptability facilitates the symphonic integration of multiple ICs within a confined space.
Swift Conductor for High Frequencies: The intricacies of Flip Chip Packaging Substrate’s design position it as a swift conductor for high-frequency applications. This makes it a preferred choice in domains like telecommunications and high-performance computing, where the tempo of rapid signal transmission is imperative.
In essence, Flip Chip Packaging Substrate emerges as an agile orchestrator, providing a stage for electrical, mechanical, and thermal performances in semiconductor devices. Its prowess in streamlining signal pathways, accommodating high I/O density, and conducting the symphony of thermal efficiency positions it as a cornerstone in the landscape of advanced and spatially constrained applications.
What Are the Different Types of Flip Chip Packaging Substrate?
Flip Chip Packaging Substrate comes in a diverse array of types, each meticulously tailored to meet specific demands and applications within the intricate landscape of semiconductor packaging. Let’s navigate through this spectrum of variants:
FCBGA (Flip Chip Ball Grid Array): FCBGA introduces us to the balletic artistry of a semiconductor die gracefully flipping and securing itself to a substrate using an array of solder balls. These spherical connectors play a dual role, functioning as both electrical conductors and steadfast anchors.
FC-COB (Flip Chip Chip-on-Board): FC-COB takes a minimalist stance as the flipped IC elegantly sidesteps a traditional package, opting for a direct mount onto a printed circuit board (PCB) or substrate. This approach results in a sleek and compact assembly.
FC-CSP (Flip Chip Chip Scale Package): FC-CSP emerges as a compact virtuoso, with the flipped IC delicately attaching directly to a substrate, offering a smaller footprint compared to conventional packaging methods.
FC-POP (Flip Chip Package-on-Package): FC-POP engages in a stacking choreography, with multiple IC packages gracefully layered atop one another. This arrangement caters to diverse functionalities and optimizes spatial utilization on the PCB.
FC-QFP (Flip Chip Quad Flat Package): FC-QFP is a symphony of flatness, where the flipped IC adheres to a flat substrate, extending leads from all four sides. This type adds a visual flair for applications favoring a sleek and flat packaging aesthetic.
FC-LGA (Flip Chip Land Grid Array): FC-LGA takes a departure by attaching the flipped IC to a substrate with an array of lands, providing a distinctive form of electrical connection that adds a touch of uniqueness to the packaging landscape.
FC-DIP (Flip Chip Dual In-Line Package): FC-DIP introduces an alternative visual appeal by flipping the IC and securing it to a dual in-line package substrate. This variant caters to applications seeking a different aesthetic.
FC-PIP (Flip Chip Package-in-Package): FC-PIP orchestrates a dance of packages, with one IC package gracefully nested atop another within the same ensemble. This configuration offers a compact solution for applications requiring multiple functionalities.
FC-SiP (Flip Chip System-in-Package): FC-SiP dons the role of an integrator, seamlessly blending multiple ICs, passive components, and potentially more elements into a cohesive package. This type emerges as a holistic solution for comprehensive system integration.
In the intricate tapestry of semiconductor packaging, the choice of Flip Chip Packaging Substrate becomes a nuanced decision, finely tuned to the specific needs of the application. From size constraints to thermal considerations, each type unfurls its unique advantages, allowing designers to compose a bespoke packaging symphony that harmonizes seamlessly with the intricacies of the electronic device or system at hand.
How is Flip Chip Packaging Substrate Related to IC Packaging?
Delving into the realm of semiconductor intricacies, Flip Chip Packaging Substrate emerges as a pivotal protagonist in the ballet of Integrated Circuit (IC) packaging. Let’s pirouette through the nuances of its relationship with IC packaging:
Artful Mounting: Flip Chip Packaging Substrate introduces a distinctive choreography in mounting ICs. Departing from the conventional wire bonding routine, it opts for a daring flip, directly entwining the IC with the substrate. This avant-garde move creates a more intimate and streamlined connection.
Electrical Symphony: At its core, the substrate orchestrates a symphony of electrical connections. Solder bumps take center stage, conducting a harmonious flow of electrons between the IC’s bond pads and the substrate. This electric ballet forms the backbone of reliable connectivity.
Mechanical Ballet: Beyond the realm of electrons, the substrate transforms into a ballet of mechanical support. The solder bumps, akin to steadfast partners, not only conduct electricity but also anchor the IC securely on the substrate, ensuring a poised performance.
Interconnections Waltz: The allure of Flip Chip Packaging Substrate lies in its ability to lead a waltz of shorter interconnections. The direct attachment of the IC to the substrate creates a dance of reduced signal propagation delays, harmonizing with an elegant improvement in electrical performance.
Thermal Harmony: The substrate takes on the role of a thermal maestro, orchestrating a symphony of heat dissipation. The direct union of the IC and substrate allows for a graceful transfer of heat, enabling it to pirouette away from the IC and dissipate into the surroundings.
Package Variations: Flip Chip Packaging Substrate offers a diverse repertoire of package types, each with its own unique form and function. From the grandeur of Flip Chip Ball Grid Array (FCBGA) to the simplicity of Flip Chip Chip-on-Board (FC-COB), designers can choreograph a packaging performance tailored to the specific IC and its application.
Advanced Technology Waltz: In a dance with progress, Flip Chip Packaging Substrate seamlessly embraces advanced technologies. It becomes a dance partner in the realm of multi-chip modules and three-dimensional integrated circuits (3D ICs), facilitating a fusion of multiple ICs and components within a compact stage.
In essence, Flip Chip Packaging Substrate takes center stage, not merely as a connector of ICs and substrates but as a choreographer orchestrating the ballet of electrical, mechanical, and thermal harmony. It offers a stage for the dance of advanced technologies, a canvas for miniaturization marvels, and a partner in the ever-evolving symphony of semiconductor packaging.
How Does Flip Chip Packaging Substrate Differ from PCB?
Within the intricate dance of electronic components, Flip Chip Packaging Substrate and Printed Circuit Board (PCB) emerge as distinct performers, each contributing its unique choreography to the symphony of electronic packaging. Let’s navigate the nuances of their differences:
Functional Ballet:
Flip Chip Packaging Substrate: This skilled performer takes center stage, orchestrating the intricate mounting and direct connection of a flipped Integrated Circuit (IC). Beyond mere support, it weaves a narrative of electrical connectivity, robust mechanical support, and adept heat management.
PCB: A foundational ensemble member, the PCB provides the canvas for a diverse array of components, forming an interconnected network. Its role transcends individual components, acting as the central hub for signal routing and system cohesion.
Mounting Choreography:
Flip Chip Packaging Substrate: The mounting technique here is a captivating dance, with the IC taking a dynamic flip and embracing a direct connection to the substrate. Solder bumps or balls become the graceful partners in this intricate performance, resulting in reduced interconnection lengths and heightened electrical performance.
PCB: The mounting techniques on a PCB are diverse, accommodating components through a symphony of surface-mount technology (SMT) or through-hole technology (THT) dances. The choreography adapts to the nature of the component and the design melody.
Directness of Connections:
Flip Chip Packaging Substrate: It radiates an aura of directness, forging electrical connections between the IC and the substrate with minimal detours. This direct path contributes to concise signal pathways and diminished signal propagation delays.
PCB: The connections on a PCB follow a more nuanced route, employing traces, vias, and pads. The interconnections traverse the board’s surface or navigate through internal layers, creating an intricate dance of connectivity.
Applications and Integration Showcase:
Flip Chip Packaging Substrate: Takes the spotlight in the avant-garde realm of advanced IC packaging, showcasing prowess in high-performance applications, compact designs, and an elegant ballet of heat dissipation. It seamlessly integrates into the grand theater of technologies like multi-chip modules and 3D ICs.
PCB: Assumes a versatile role as the supporting artist in electronic systems, catering to a spectrum of applications. PCBs don different costumes, ranging from the simplicity of single-layer acts to the complexity of multi-layer performances, supporting diverse electronic devices.
Size and Complexity Ensemble:
Flip Chip Packaging Substrate: Often seen in smaller ensembles, perfectly suited for applications where spatial considerations take the lead. The design choreography can be intricate, especially in scenarios demanding an advanced IC integration showcase.
PCB: Takes on roles of varying sizes and complexities, fitting into electronic devices of different scales. From the elegance of simplicity in single-layer acts to the intricacy of multi-layer performances, PCBs adapt to diverse scenarios.
Component Support Symphony:
Flip Chip Packaging Substrate: Specializes in providing a stage for ICs, particularly those embracing the avant-garde flip chip technology. The ensemble may include additional components, contributing to specific functionalities.
PCB: Showcases versatility in supporting a diverse cast of electronic components. From ICs and resistors to capacitors and connectors, PCBs create an inclusive environment for a wide array of elements.
In essence, Flip Chip Packaging Substrate and PCB, though sharing the electronic stage, bring their own unique performances to the symphony of electronic packaging. Flip Chip Packaging Substrate takes on a specialized and direct role in the art of IC mounting, while PCB forms the foundational canvas for a diverse cast of components to harmonize within the comprehensive orchestration of an electronic system. Each plays a vital role, contributing its unique melody to the grand performance.
What is the Main Structure and Production Technology of Flip Chip Packaging Substrate?
The world of Flip Chip Packaging Substrate unfolds with a symphony of structures and production technologies, meticulously orchestrated to meet the demands of diverse applications. Let’s embark on a journey through the key elements of its architecture and the intricate dance of production technologies:
Architectural Ensemble:
Substrate’s Elemental Foundation:
Flip Chip Packaging Substrates find their essence in materials of exceptional thermal conductivity. Options range from the grace of ceramics, such as alumina or aluminum nitride, to the flexibility of organic substrates like high-performance laminates and polyimide films.
Layered Complexity:
The substrate often unveils a multi-layered composition, allowing for an intricate tapestry of traces and interconnections. High-Density Interconnects (HDI) technology takes center stage, enabling finer pitch and heightened wiring density.
Metallic Crescendo:
Layers of metal bring conductivity to the composition, shaping the electric pathways with precision. The metal layers, artfully patterned, form the intricate circuitry and connection points.
Dielectric Harmony:
Dielectric layers play a role akin to harmony, residing between metal layers to offer insulation and safeguard against short circuits. The choice of dielectric materials adds nuances to the overall electrical performance.
Solder Mask Elegance:
A layer of solder mask is gracefully applied, defining spaces for solder connections and ensuring a flawless backdrop during subsequent processes. This layer safeguards against solder bridges, contributing to the precision of the performance.
Solder Ballet:
Solder bumps or balls take the stage, strategically positioned to create connection points for the flipped IC. These solder connections not only conduct electricity but also serve as the graceful anchors for the mechanical attachment.
Underfill Crescendo:
Post flip chip attachment, an underfill material enters the scene. This material gracefully fills the void between the IC and the substrate, enhancing mechanical strength and providing a protective layer against stresses and thermal cycles.
Production Symphony:
Substrate Crafting Prelude:
The production overture begins with the crafting of the substrate. For ceramics, it involves the poetic dance of tape casting, green sheet lamination, and firing. Organic substrates take shape through the ballet of lamination and etching.
HDI Choreography:
High-Density Interconnects (HDI) technology takes the lead, crafting build-up layers with finesse. Laser drilling, electroplating, and photoimaging weave a dance of intricate traces and high wiring density.
Metallic Harmonization:
Metal layers gracefully descend onto the substrate, whether through the rhythmic beats of sputtering or the electroplating melody. These layers form the conductive pathways, bringing the composition to life.
Solder Mask Artistry:
Solder mask application involves a delicate brushstroke, defining areas for solder connections and bestowing protection upon the substrate. Photoimaging and curing are the steps in this artistic application.
Solder Ballet Choreography:
The solder bumps or balls take shape, whether through the precision of solder paste printing, solder ball placement, or the electroplating ballet.
Flip Chip Attachment Pas de Deux:
The climactic moment arrives as the IC takes center stage, flipping and attaching itself to the substrate with the grace of solder bumps. Reflow soldering or other bonding techniques contribute to this captivating pas de deux.
Underfill Embrace:
An underfill material enters, embracing the assembly and solidifying the connection between the IC and the substrate. This step adds a layer of resilience and thermal stability to the performance.
Finale: Testing and Inspection:
The grand finale unfolds with testing and inspection, ensuring the seamless harmony of electrical connections, precise alignment, and the overall functionality of the completed assembly.
In this grand performance, Flip Chip Packaging Substrate takes its place as a masterpiece, intricately woven with a blend of materials, precision processes, and artistic assembly techniques. The choice of materials and production methodologies, like notes in a symphony, harmonizes to create a platform that elegantly supports advanced semiconductor packaging requirements.
Frequently Asked Questions (FAQs)
In Which Applications Are Flip Chip Packaging Substrates Widely Utilized?
Flip Chip Packaging Substrates find extensive use in high-performance electronic devices such as smartphones, tablets, data centers, and automotive electronics. They excel in scenarios where compact size and superior electrical performance are crucial.
What Testing and Inspection Processes Are Employed During Flip Chip Packaging Substrate Manufacturing?
Rigorous testing and inspection processes are integral to Flip Chip Packaging Substrate manufacturing. These include electrical tests, visual inspections, and other quality control measures to ensure the reliability of electrical connections, precise alignment, and overall functionality.
Can Flip Chip Packaging Substrates Be Customized for Specific Applications?
Absolutely, Flip Chip Packaging Substrates are highly customizable to meet the specific requirements of diverse applications. This customization may involve adjustments in substrate materials, design configurations, and other parameters to align with the unique needs of the application.
How Does the Choice of Flip Chip Packaging Substrate Impact Overall System Performance?
The selection of Flip Chip Packaging Substrate plays a pivotal role in overall system performance. Factors such as material choice, design intricacies, and thermal considerations collectively influence the substrate’s impact on the electrical, mechanical, and thermal aspects of the entire system.
What Noteworthy Trends Are Emerging in the Flip Chip Packaging Substrate Industry?
A: Emerging trends in the Flip Chip Packaging Substrate industry include the adoption of advanced materials, integration of heterogeneous integration technologies, and a concerted effort towards achieving higher levels of miniaturization and performance efficiency.
Conclusion
In summary, Flip Chip Packaging Substrate emerges as a pivotal element in semiconductor packaging, fusing cutting-edge design with advanced manufacturing processes. Leading manufacturers like Amkor Technology, ASE Group, JCET, Samsung Electro-Mechanics, and STATS ChipPAC collectively define excellence in this dynamic domain.
Crafted from materials such as ceramics or organic substrates, Flip Chip Packaging Substrates provide a distinctive platform for the direct attachment of flipped Integrated Circuits. The manufacturing journey unfolds through intricate stages, encompassing substrate fabrication, High-Density Interconnects (HDI), solder bump formation, and stringent testing protocols.
The allure of Flip Chip Packaging Substrates lies in their capacity to deliver streamlined interconnections, elevated electrical performance, and compatibility with avant-garde packaging technologies like multi-chip modules and 3D ICs. Widely embraced in applications ranging from smartphones to data centers, these substrates shine in scenarios prioritizing compact size and superior electrical performance.
The customization flexibility of Flip Chip Packaging Substrates allows tailored adaptations for diverse applications, facilitating adjustments in materials and design configurations. As a pivotal component shaping system performance, careful substrate selection reverberates across electrical, mechanical, and thermal dimensions, crafting a symphony of functionality.
Looking ahead, industry trends signal the adoption of advanced materials and the integration of heterogeneous technologies, steering towards heightened levels of miniaturization and performance efficiency. This collective drive propels Flip Chip Packaging Substrate technology into new realms of innovation.
In essence, the realm of Flip Chip Packaging Substrate epitomizes a fusion of precision, adaptability, and forward-thinking trends, underscoring a commitment to advancing semiconductor packaging and redefining the frontiers of electronic device performance.