What Is Flip Chip Packaging Substrate?
Flip Chip Packaging Substrate ,The Flip Chip Packaging Substrate is a critical component for integrated circuit packaging. It serves as a bridge between the chip and the Printed Circuit Board (PCB), enabling direct connections between the chip’s pins and the solder pads on the substrate through flip-chip bonding. This packaging technology offers high density and performance, facilitating faster signal transmission speeds and higher power densities. Typically composed of multiple thin layers including insulating layers, metal layers, and conductor layers, the Flip Chip Packaging Substrate ensures reliable electrical connections and effective thermal management.
Flip chip packaging substrate is a cutting-edge approach in semiconductor packaging. Here, the active side of a microchip or integrated circuit (IC) takes a different orientation by being flipped and directly affixed to a substrate or another packaging element. This contrasts with the conventional method, where the chip’s active side faces upwards, and connection is established through wire bonding.
In flip chip packaging, the chip is inverted, positioning its active side with solder bumps or copper pillars facing downward. The substrate plays a pivotal role as a supportive foundation, fostering electrical connections between the chip and the broader system. Materials for the substrate vary, encompassing options like organic printed circuit boards (PCBs) or ceramic substrates, chosen based on considerations like thermal performance, electrical characteristics, and cost-effectiveness.
The connectivity between the flip chip and the substrate is established via solder bumps or copper pillars, forming the crucial “flip chip interconnect.” This methodology offers multiple advantages, including reduced signal path lengths, heightened electrical efficiency, superior thermal control, and the capacity for achieving heightened packaging density.
Embraced extensively in the semiconductor industry, flip chip packaging finds its niche in applications where top-tier performance, compact designs, and efficient thermal attributes are paramount. Examples include its application in mobile devices, high-performance computing setups, and advanced electronic systems.
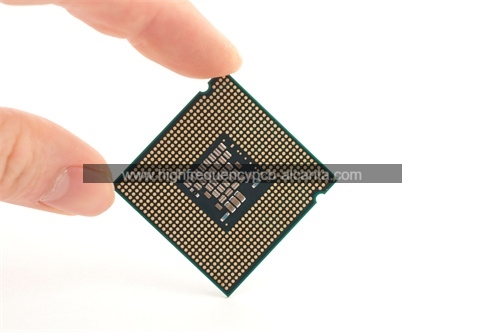
Flip Chip Packaging Substrate
How Does Flip Chip Packaging Substrate Enhance Functionality?
Flip chip packaging substrates revolutionize the landscape of semiconductor devices, imparting a host of benefits that elevate their performance:
Efficient Signal Transmission: Through the innovative method of flipping the chip and establishing direct connections with the substrate, flip chip packaging shortens interconnect paths. This not only reduces signal propagation delays but also enhances overall performance, enabling swift and efficient data transfer.
Optimized Electrical Output: The utilization of solder bumps or copper pillars for direct electrical connections enhances the electrical performance of flip chip packaging. This results in improved signal integrity, reduced parasitic capacitance, and superior characteristics at higher frequencies.
Maximized Packaging Density: The flipped chip orientation, combined with the compact arrangement of solder bumps or copper pillars, allows for a higher packaging density. This proves especially advantageous in situations where space is a premium, as seen in compact electronic systems and mobile devices.
Effective Heat Management: Flip chip packaging excels in its capacity to efficiently distribute the heat produced by the integrated circuit. The direct bonding of the chip to the substrate enhances thermal conductivity, resulting in a more effective dissipation of heat compared to traditional packaging methods. This aspect becomes especially critical in high-performance applications where strict thermal considerations are paramount.
Minimized Inductance: The departure from wire bonds in favor of direct connections translates to reduced inductance. Lower inductance is advantageous for high-frequency applications, mitigating signal distortion and loss.
Enhanced Device Reliability: Flip chip packaging contributes to the overall reliability of semiconductor devices. The robust nature of the direct connections between the chip and substrate helps mitigate risks associated with potential failures linked to wire bonds.
Adaptable Design Integration: With its inherent design flexibility, flip chip packaging allows for the seamless integration of diverse components on the same substrate. This adaptability proves invaluable in crafting sophisticated electronic systems with multifaceted functionalities.
In conclusion, flip chip packaging substrates play a pivotal role in optimizing functionality by addressing challenges related to signal integrity, thermal management, packaging density, and reliability. These attributes make them exceedingly well-suited for advanced semiconductor applications across a spectrum of industries.
What Are the Different Types of Flip Chip Packaging Substrate?
Embarking on a journey through the realm of flip chip packaging substrates unveils a pivotal dimension in the intricate orchestration of assembling flip chip integrated circuits (ICs). These substrates, adorned with a diverse array of materials and properties, are fastidiously selected to align with the nuanced demands across various applications.Let’s traverse the kaleidoscope of substrate types:
Organic Substrates:
FPCB (Flexible Printed Circuit Board): Showcasing versatility, it adeptly integrates pliable materials such as polyimide, skillfully maneuvering through the complexities of tailored applications.
PCB (Printed Circuit Board): Embraces rigidity, utilizing substrates such as FR-4 or high-speed materials to elevate the cadence of electrical performance.
Ceramic Substrates:
Alumina (Aluminum Oxide): Renowned for its mastery in thermal conductivity, taking the lead in orchestrating efficient heat dissipation.
Aluminum Nitride (AlN): Commands attention for its dual virtues of excellent thermal conductivity and electrical insulation, especially favored in the domain of high-power applications.
Silicon Substrates:
Silicon Interposer: Conducts a harmonious symphony with a silicon substrate, fostering high-density interconnects and elevating the melody of electrical performance.
Silicon Carrier: Takes on the role of a vessel, carrying multiple dice within its composition, choreographing an intricate dance of integration and functionality.
Laminates:
Liquid Crystal Polymer (LCP): Takes center stage with a solo in electrical performance, tailor-made for applications with demanding high-frequency requirements.
Polyimide Laminate: Strikes a chord that resonates with both flexibility and thermal stability, crafting a perfect composition for applications that demand mechanical flexibility.
Glass Interposers:
Glass-Ceramic Interposer: Blends the elegance of glass and the resilience of ceramic materials, offering a composition that conducts both thermal efficiency and electrical insulation in harmony.
Metal Substrates:
Copper Substrate: Leads the ensemble with the brilliance of copper, orchestrating commendable thermal conductivity and electrical performance.
Copper-Clad Laminates: Weaves a tapestry that integrates a copper layer into laminates, achieving a delicate equilibrium between electrical and thermal properties.
Thick Film Substrates:
Thick Film Ceramic Substrate: Takes the spotlight in a performance where ceramic materials, enriched with the finesse of thick film technology, steal the show by enabling the effortless assimilation of passive components.
High-Density Interconnect (HDI) Substrates:
Build-Up HDI Substrate: Embodies a crescendo of multiple layers of conductive and insulating materials, crafting a symphony of high-density interconnects.
Through-Silicon Via (TSV) Substrate: Engages in a dance of connectivity, utilizing vertical vias to minimize signal delay and enhance the overall composition.
The choice of a flip chip packaging substrate, akin to a conductor selecting instruments for an orchestra, hinges on a nuanced understanding of application requirements, thermal intricacies, electrical nuances, and the art of cost-effectiveness. Each substrate type unveils a unique set of advantages, empowering engineers to compose their selection in harmony with the specific needs of the electronic device in development.
How Does Flip Chip Packaging Substrate Differ from Conventional PCBs?
Diverging paths in design philosophy set flip chip packaging substrates and conventional PCBs apart in the realm of electronic systems. These differences manifest across various dimensions, outlining the unique roles and configurations of each:
Bump Placement:
Flip Chip Packaging Substrates: A distinctive feature involves the direct mounting of the semiconductor chip onto the substrate, with solder bumps facilitating a direct and immediate electrical connection.
Conventional PCBs: Components on conventional PCBs find their place on the surface, forming connections through through-hole or surface-mount technology, with leads extending outward.
Chip Orientation:
Flip Chip Packaging Substrates: Embraces an inverted orientation, positioning the chip with its active side facing the substrate. This arrangement minimizes signal delays with more direct connections.
Conventional PCBs: Components are conventionally oriented with their active sides facing upward, and interconnections occur through leads or soldered joints on the PCB surface.
Interconnect Method:
Flip Chip Packaging Substrates: Solder bumps take center stage, crafting a concise and immediate path for electrical signals between the chip and the substrate, optimizing electrical performance.
Conventional PCBs: Interconnections unfold through traces on the PCB surface, potentially introducing longer signal paths and heightened inductance.
Size and Weight:
Flip Chip Packaging Substrates: Tends to favor a more compact design as the direct chip-substrate attachment reduces overall size and weight.
Conventional PCBs: Components on the surface may contribute to a larger and heavier system.
Thermal Performance:
Flip Chip Packaging Substrates: Leverages the direct chip-substrate link for efficient heat dissipation, rendering it apt for high-power applications.
Conventional PCBs: Heat dissipation may rely on alternative methods, such as heat sinks, and might not be as direct as in flip chip packaging.
Complexity and Cost:
Flip Chip Packaging Substrates: Tends towards complexity, often involving advanced manufacturing processes that may translate to higher initial costs.
Conventional PCBs: Typically more straightforward in manufacturing, presenting a potentially more cost-effective solution for diverse applications.
In essence, the choice between flip chip packaging substrates and conventional PCBs hinges on specific design requirements and performance criteria. Flip chip packaging excels in scenarios demanding compactness, superior electrical performance, and efficient heat dissipation, especially in high-performance and miniaturized electronic devices. Conversely, conventional PCBs offer versatility and cost-effectiveness across a broader spectrum of applications.
How Does Flip Chip Packaging Substrate Distinguish Itself Across Various Electronic Components?
In the intricate dance of electronic components, flip chip packaging substrates take on diverse roles, adapting their performance to the unique needs of each player in the technological ensemble:
Microprocessors and CPUs:
Distinctive Feature: The spotlight shines on flip chip packaging’s direct chip-to-substrate connection, orchestrating concise signal paths that reduce delays and elevate electrical performance, particularly in the fast-paced realm of high-speed computing.
Memory Modules (DRAM, NAND, etc.):
Distinctive Feature: Within the collective harmony of memory modules, flip chip packaging’s direct bump-to-substrate connection emerges as a virtuoso, conducting a symphony of accelerated data transmission, diminished inductance, and enhanced memory capabilities.
Graphics Processing Units (GPUs):
Distinctive Feature: Adapting to the computational crescendo and thermal ballet of GPUs, flip chip packaging stands out as a virtuoso of efficient heat dissipation—a crucial note for sustaining peak performance in graphics-intensive applications.
RF and Microwave Components:
Distinctive Feature: For components traversing the high-frequency spectrum, such as RF and microwave components, flip chip packaging orchestrates a melody of minimized signal loss and heightened high-frequency prowess. Its shorter interconnects contribute to a composition of reduced parasitic effects and refined signal integrity.
Power Amplifiers and High-Power Components:
Distinctive Feature: In the powerful symphony of amplifiers, flip chip packaging takes on the role of a thermal virtuoso, ensuring the graceful dissipation of heat—an instrumental harmony in maintaining reliability and preventing the risk of overheating.
Sensors and MEMS Devices:
Distinctive Feature: Tailored for a sonnet of compactness, flip chip packaging resonates with sensors and MEMS devices, navigating the spatial constraints of applications like consumer electronics and IoT with finesse.
System-on-Chip (SoC) Integration:
Distinctive Feature: In the symphonic integration of multiple functions within integrated circuits (SoC), flip chip packaging orchestrates a dance of dense integration. Shorter interconnects contribute to a harmonious reduction of parasitic effects and crosstalk, enhancing the efficiency of the overall system composition.
Optoelectronic Components (LEDs, Photodetectors):
Distinctive Feature: Stepping onto the stage of optoelectronics, flip chip packaging’s compact design takes a leading role, ensuring a precise alignment of optical elements—an exquisite movement enhancing the performance of optoelectronic compositions.
In essence, flip chip packaging substrates embody a versatile artistry, seamlessly adapting to the distinctive needs and rhythms of diverse electronic components. Whether it’s orchestrating signal precision, choreographing efficient heat dissipation, or navigating spatial constraints, flip chip packaging emerges as a flexible conductor in the intricate symphony of electronic components.
What Constitutes the Structure and Production Technologies of Flip Chip Packaging Substrate?
Crafting the structural framework and implementing cutting-edge production methodologies for flip chip packaging substrates is an intricate symphony of elements and processes. Let’s delve into the composition and manufacturing techniques that define these sophisticated electronic components:
Architecture of Flip Chip Packaging Substrate:
Base Material Elegance:
Ceramic or Organic Canvas: The substrate sets the tone, offering the elegance of ceramics like alumina or aluminum nitride or the flexible canvas of organics like FR-4 and high-speed materials.
Dielectric Layers Ballet:
Insulating Choreography: Intertwined within the substrate, dielectric layers perform a ballet, providing insulation to preserve the purity of the circuit.
Conductor Traces Rhythm:
Copper Rhythms: Copper conductor traces orchestrate a rhythm, guiding the flow of electrical signals and composing the intricate connectivity of the integrated circuit.
Solder Mask Shield:
Guardians of Integrity: A solder mask stands guard, shielding conductor traces from environmental elements and ensuring the sanctity of the electrical connections.
Bump Pad Platforms:
Elevated Platforms: Bump pads rise as elevated platforms, awaiting the solder bumps that will create a seamless link between the flip chip and the substrate.
Underfill Serenade:
Structural Serenade: An underfill material takes center stage, serenading structural support and facilitating heat dissipation beneath the flip chip.
Production Symphony of Flip Chip Packaging Substrate:
Wafer Artistry:
Semiconductor Prelude: The chip, the virtuoso, undergoes wafer fabrication—a masterpiece of lithography, etching, and material deposition.
Bumping Harmony:
Solder Bump Harmony: Solder bumps are meticulously arranged, creating a harmonious connection through processes like electroplating or precise solder ball placement.
Wafer Dicing Crescendo:
Chip Separation Crescendo: The wafer transitions to a crescendo, with each chip emerging individually, ready for its pivotal role in the ensemble.
Substrate Composition Waltz:
Layered Waltz: The substrate takes form in a waltz of layered dielectric materials, conductive traces, and protective layers—a composition poised to support the flip chip.
Bump Transfer Pas de Deux:
Alignment Pas de Deux: The solder bumps on the chip engage in a pas de deux with corresponding bump pads on the substrate. The bonding process, a dance of controlled heat, seals their connection.
Underfill Dispensing Opera:
Encapsulation Opera: Underfill material takes the stage in an operatic dispense, enveloping the flip chip with a protective embrace, creating an opera of structural integrity.
Curing and Testing Finale:
Solidification Finale: The underfill undergoes a finale, solidifying its contribution to stability. A comprehensive testing finale unfolds, ensuring the electronic masterpiece meets rigorous quality standards.
Integration Grand Coda:
Incorporation Coda: The completed flip chip package gracefully enters the grand coda, seamlessly integrating into the final electronic production—a crescendo of technological brilliance.
This orchestrated symphony of materials and processes harmonizes to deliver flip chip packaging substrates, each playing a unique role in the grand composition of electronic components. The choice of materials and manufacturing techniques reflects a delicate balance, tailored to the specific needs and performance criteria of diverse applications.
What Are the Frequently Asked Questions (FAQs) Surrounding Flip Chip Packaging Substrate?
What defines a flip chip packaging substrate?
Insight: A flip chip packaging substrate stands as a cornerstone in semiconductor engineering, offering a platform for the attachment and interconnection of a flip chip. Comprising materials like ceramic or organics, it orchestrates a symphony of conductor traces, solder bumps, and protective layers.
How does the flip chip approach differ from traditional chip packaging?
Insight: In the dance of flip chip packaging, the semiconductor chip elegantly presents its active side facing downward. Solder bumps then form direct electrical connections with the substrate—an approach distinct from traditional packaging methods.
Which materials grace the canvas of flip chip packaging substrates?
Insight: The stage is set with materials like ceramic (aluminum oxide or aluminum nitride) or organic companions such as FR-4. The choice is a delicate balance, considering factors like thermal conductivity, flexibility, and application nuances.
Unraveling the mystery of solder bumps: What role do they play?
Insight: Solder bumps, akin to tiny protagonists, emerge on the flip chip, creating pivotal connection points. They engage in a dance with corresponding bump pads on the substrate, forming a direct and reliable electrical alliance.
What advantages does the flip chip performance bring to the stage?
Insight: The flip chip takes a bow with advantages like shortened interconnect paths, heightened electrical performance, efficient heat dissipation, and a sleek, compact form—an ensemble ideal for high-performance and miniaturized electronic productions.
How is the delicate alignment of solder bumps and bump pads orchestrated?
Insight: Precision choreography unfolds through advanced manufacturing processes, featuring automated tools and visionary techniques. These ensure the harmonious alignment of solder bumps and bump pads.
Underfill material steps into the limelight: What role does it play?
Insight: Underfill material graces the scene after flip chip attachment, offering structural support and weaving a narrative of reliability. Its presence aids in minimizing thermal stresses and contributes to the graceful dissipation of heat.
Can flip chip packaging substrates take the center stage in high-frequency performances?
Insight: Indeed, the flip chip graces high-frequency stages with its shorter interconnects, minimizing parasitic effects. This makes it a virtuoso in applications like RF and microwave devices, where precision is paramount.
Consumer electronics: Is the flip chip a sought-after performer?
Insight: The flip chip commands attention in the consumer electronics spotlight, showcasing a compact design, efficient heat dissipation, and stellar electrical performance. It earns applause in devices like smartphones, tablets, and wearables.
Testing the reliability: What processes ensure the flip chip’s endurance?
Insight: The flip chip undergoes a series of tests—a choreography of electrical examinations, thermal evaluations, and reliability assessments. These ensure its mettle, guaranteeing sustained performance across diverse conditions.
In Conclusion
As we draw the curtain on our exploration of flip chip packaging substrates, it’s worth reflecting on the significance of these technological protagonists. In the ever-evolving landscape of electronic engineering, flip chip packaging substrates emerge as versatile performers, seamlessly integrating into the orchestra of semiconductor innovation.
Their role as a foundational platform for flip chips, with their downward-facing elegance and direct electrical connections, underscores a paradigm shift in packaging methodologies. This shift brings with it a symphony of advantages—shorter interconnect paths, enhanced electrical performance, and efficient heat dissipation—that resonate across a spectrum of high-performance applications.
Whether in the limelight of consumer electronics, where their compact design finds a perfect stage, or in the precision-demanding realms of high-frequency devices, flip chip packaging substrates command attention. The collaborative dance of materials—ceramics or organics—alongside advanced manufacturing processes orchestrates a production symphony that ensures structural integrity and reliability.
As the final movement unfolds and flip chip packaging substrates take their place in the grand finale of electronic production, their significance echoes. They are not just components; they are key players in shaping the future of miniaturized, high-performance devices that define our connected world.
In conclusion, let us acknowledge the nuanced choreography of flip chip packaging substrates—a technological ballet where each element plays a crucial role. Their contribution to the harmony of electronics is a testament to the constant evolution and innovation that propels the industry forward. The stage is set, the players are in position, and the encore of possibilities awaits in the ongoing saga of semiconductor excellence.