Flip Chip Package Substrate Manufacturer
Flip Chip Package Substrate Manufacturer,Flip Chip Package Substrate Manufacturers specialize in producing critical components for semiconductor packaging. These companies employ advanced techniques to fabricate substrates that facilitate direct chip-to-board connections, enhancing performance and reliability in electronic devices. With expertise in materials science and manufacturing processes, they ensure precise alignment, high-density interconnections, and efficient heat dissipation in Flip Chip Package Substrates. These manufacturers play a vital role in the semiconductor industry, supplying substrates tailored to meet the stringent requirements of modern electronics, enabling innovations in communication, computing, and consumer electronics sectors.
Enter the Flip Chip Package Substrate, an avant-garde packaging marvel dominating the semiconductor arena. Picture this: a semiconductor chip mounted in a topsy-turvy fashion on the substrate, with its active side boldly facing the ground. How do they connect, you ask? Through the wizardry of solder bumps.
Now, let’s unravel the quirks of this packaging wizardry:
Spatial Wizardry: Bid farewell to the space-hogging norms. Flip chip packaging dances to its own tune, creating a sleeker design by nixing the need for excess space. It’s like minimalism for semiconductors.
Speedy Sorcery: Ever heard of interconnect lengths casting spells on performance? Flip chip packaging sure has. Shorter lengths mean quicker electrical prowess, reduced signal hesitation, and an overall uptick in operational speed. Abracadabra!
Heat Hocus-Pocus: Chip heat can be a bother, but not for the flip chip maestro. The direct chip-to-substrate fusion becomes a heat-dissipating waltz, ensuring a cool vibe on the substrate dance floor.
Density Enchantment: Flip chip technology isn’t shy about showing off its I/O prowess. It pulls off a high-density act, cramming more connections into its magical spatial realm.
Signal Charm: Long interconnects be gone! The flip chip’s direct connections weave a spell of enhanced signal integrity, with distortion taking a backseat in this mystical performance.
Reliability Magic: Solder bumps take center stage, forging a reliable and enduring connection. It’s the kind of magic that ensures the chip and substrate stay bonded through thick and thin.
In summation, the Flip Chip Package Substrate isn’t your run-of-the-mill packaging tale. It’s a saga of spatial finesse, speed enchantments, heat-defying dances, density wizardry, signal charm, and reliability magic. This tech luminary graces applications like microprocessors, integrated circuits, and electronic components, adding a touch of magic to the semiconductor spectacle.
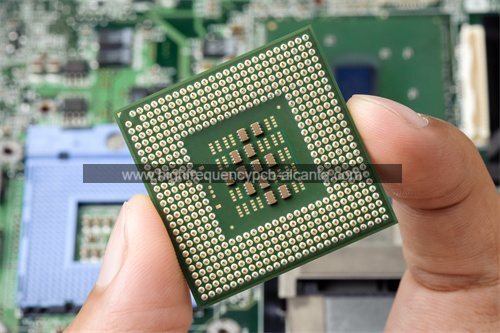
Flip Chip Package Substrate Manufacturer
What Functions Does Flip Chip Package Substrate Serve?
The Flip Chip Package Substrate wears many hats in the semiconductor world, embodying a versatile role that shapes the performance of electronic devices. Let’s unveil the myriad functions it gracefully undertakes:
Electrical Nexus: At its core, the substrate acts as a conduit for electrical wizardry, forging connections between the semiconductor chip and the external circuitry. Solder bumps become the enchanting bridges, conducting the symphony of currents.
Spatial Magician: Picture the substrate as a spatial illusionist. By hosting the semiconductor chip in a downward-facing stance, it conjures a spell of spatial optimization. This is a game-changer for devices where the art of space utilization is as critical as the device’s prowess.
Thermal Harmonizer: Playing the role of a thermal maestro, the substrate orchestrates the graceful dissipation of heat emanating from the semiconductor chip. This is a crucial act, especially in applications where high performance and heat management perform a delicate duet.
Signal Custodian: The substrate becomes the custodian of signal sanctity. Through the crafty use of shortened interconnect lengths, it ensures that electronic signals traverse their paths with minimal turbulence. This is essential in preserving signal fidelity, particularly in the swift rhythms of high-speed applications.
I/O Choreographer: In the grand dance of inputs and outputs, the flip chip substrate takes on the role of a choreographer. It conducts a dance of high input/output (I/O) density, allowing a plethora of connections to pirouette within a confined space. A true conductor of connectivity.
Reliability Guardian: Armed with solder bumps, the substrate stands as a guardian of reliability. These bumps forge sturdy connections, weathering the storms of operational demands and ensuring an enduring alliance between chip and substrate.
Performance Artisan: The substrate becomes a key artisan in crafting performance. Short interconnect lengths and direct connections weave an artistic tapestry of improved electrical performance, reduced signal delay, and an overall acceleration in operational tempo.
Structural Composer: In the architectural composition of semiconductor packages, the substrate takes center stage. It ensures the integrity of the package, composing a symphony that keeps the semiconductor chip securely anchored under a myriad of operational scenarios.
In essence, the Flip Chip Package Substrate is not a mere participant but a versatile artist in the semiconductor narrative. Its functions extend beyond mere electrical connections, embracing roles as a spatial illusionist, thermal maestro, signal custodian, connectivity choreographer, reliability guardian, performance artisan, and structural composer. It’s a dynamic artist conducting the symphony of electronic functionality.
What are the Different Types of Flip Chip Package Substrate?
Diverse Flip Chip Package Substrates cater to specific needs and applications within the semiconductor realm. Here’s a glimpse into the various types available:
Versatile Organics:
Flexible PCBs (Flex): When flexibility is paramount, flexible substrates enable the semiconductor device to bend or adapt to specific shapes.
Rigid PCBs: Stability and support are the hallmarks of rigid substrates, ideal for applications where flexibility takes a back seat.
Inorganic Powerhouses:
Ceramic Wonders: Materials like alumina or aluminum nitride dominate when exceptional thermal conductivity is non-negotiable. These are favored in high-power applications.
Interposer Innovations:
Silicon Interposers: Elevating the game with high-density integration, silicon interposers excel in advanced packaging technologies.
Glass Interposers: Offering a blend of cost-effectiveness and scalability, glass interposers find their place in diverse integrated setups.
Laminates of Density:
HDI Laminates: Paving the way for high-density interconnects, these laminates are the go-to for applications demanding a multitude of connections in a confined space.
Metallic Guardians:
Metal Core Champions (MCPCB): With a metal core—aluminum, copper, or a fusion—these substrates shine in thermal performance. LED applications and power electronics are their common stomping grounds.
Composite Blends:
Polymer-Ceramic Fusion: Marrying the strengths of polymers and ceramics, these substrates strike a balance, finding their place where flexibility and thermal performance converge.
System Harmony:
SiP Substrates: In System-in-Package applications, where multiple components unite, the substrate orchestrates connectivity and support for a harmonious integration.
Traditional Faves:
Leadframe-Based Gems (FCoL): The trusty leadframe makes its mark in Flip Chip on Leadframe scenarios. A cost-effective choice with a broad reach in semiconductor applications.
Selecting the ideal flip chip package substrate hinges on factors like thermal demands, flexibility prerequisites, budget constraints, and the unique demands of the application at hand. Each substrate type brings its own set of advantages, tailored to diverse semiconductor packaging needs.
How Does Flip Chip Package Substrate Differ from PCBs?
Flip Chip Package Substrates and Printed Circuit Boards (PCBs) may dwell in the same electronic universe, but their cosmic roles and characteristics set them apart. Let’s embark on a celestial journey to explore the galaxies of their disparities:
Celestial Functions:
Flip Chip Package Substrate: Imagine it as the cosmic stage for semiconductor chips, orchestrating a dance of flip chip bonding. Its mission: to weave electrical connections, dissipate heat like a stellar breeze, and provide a sturdy foundation for the semiconductor device.
PCBs: The unsung heroes of electronic constellations, serving as the cosmic canvas for myriad components like resistors and integrated circuits. They navigate the vast expanse, enabling interstellar connections and ensuring the harmony of the electronic cosmos.
Galactic Mounting Tactics:
Flip Chip Package Substrate: Crafted for the delicate art of mounting flip-chip-bonded semiconductor chips. Picture chips aligned like celestial bodies, their solder bumps creating direct electrical connections.
PCBs: Versatility is their cosmic trait, accommodating various components through soldering or surface mount technology. They welcome an array of components, each finding its celestial niche.
Quantum Connection Technologies:
Flip Chip Package Substrate: Ventures into the quantum realm of flip chip bonding, where solder bumps forge connections with the finesse of subatomic particles.
PCBs: Navigate the electronic continuum with traces, pads, and vias—pathways akin to cosmic threads weaving through the fabric of the board.
Flexibility Nebula:
Flip Chip Package Substrate: Adaptable like a nebula, it can manifest in rigidity, flexibility, or semi-flexibility, morphing to suit the cosmic dance of its application.
PCBs: Explore the nebulous realms of rigidity to flexibility, even embracing the hybrid existence of rigid-flex boards, embodying the adaptability of celestial bodies.
Universal Applications:
Flip Chip Package Substrate: Thrives in the cosmic realms of advanced semiconductors, high-performance integrated circuits, and applications where the space-time continuum demands efficiency and high-density interconnects.
PCBs: Ubiquitous cosmic travelers, finding their place in the cosmic tapestry of computers, smartphones, consumer electronics, and the far reaches of industrial and automotive applications.
Design Constellations:
Flip Chip Package Substrate: Crafted with precision, envision it as a constellation with stars aligning in the intricate dance of flip chip bonding—a cosmic masterpiece.
PCBs: Navigate the cosmic canvas with complex constellations—multiple layers, intricate routing, and a myriad of components—a celestial spectacle in versatile circuit designs.
In the grand cosmic ballet of electronics, Flip Chip Package Substrates and PCBs twirl as celestial partners, each with its cosmic role, creating harmonies and orchestrating dances across the vast expanse of the electronic universe.
What are the Main Structures and Technologies in Manufacturing Flip Chip Package Substrate?
Embarking on the manufacturing journey of Flip Chip Package Substrates unravels a narrative interwoven with intricate structures and cutting-edge technologies. Let’s delve into the pivotal components that shape this manufacturing odyssey:
Versatile Substrate Materials:
Organic Marvels: Forged from the essence of epoxy-based laminates or the resilience of polyimide, organic substrates emerge as flexible artisans, fitting seamlessly into applications that demand adaptability.
Inorganic Pioneers: Harnessing the thermal prowess of ceramics such as alumina or aluminum nitride, inorganic substrates stand as stalwart pioneers, addressing the power-hungry needs of specific applications.
Architectural Symphony:
Layered Elegance: Flip Chip Package Substrates unfurl layers of elegance, providing a canvas for intricate routing and a playground for incorporating a diverse ensemble of components.
Through-Hole Intricacies: Adding a touch of structural complexity, through-hole structures grace the stage, facilitating vertical connections—a symphony of architectural intricacies.
Flip Chip Bonding Ballet:
Solder Bump Ballet: The semiconductor chip takes center stage, adorned with solder bumps crafted through the precision of electroplating or the finesse of solder paste deposition.
Graceful Bonding Performance: The flip chip bonding process takes center stage—a delicate dance of alignment and attachment, orchestrating a perfect harmony between solder bumps and substrate pads.
Underfill Artistry:
Underfill Application Choreography: Post-bonding, an underfill material steps into the spotlight, filling the void between chip and substrate. It becomes a virtuoso, enhancing mechanical strength, providing stress relief, and orchestrating improved thermal properties.
Curing Ritual: The underfill undergoes a transformative ritual—curing initiated by heat or the illuminating touch of ultraviolet (UV) light.
Surface Finish Grandeur:
Sublime Substrate Pads: Substrate pads receive a regal touch with surface finishes, ensuring impeccable solderability and standing guard against the audacity of oxidation. Gold, tin, or an alloyed spectacle—diverse finishes grace the stage.
Quality Control Ballet:
AOI Performance: Automated Optical Inspection (AOI) systems gracefully take the spotlight, scrutinizing the flip chip assembly for any anomalies—a performance of meticulous scrutiny.
X-ray Symphony: The X-ray technology orchestrates a backstage symphony, delving into the inner sanctum to ensure the integrity of solder joints and the even distribution of underfill.
Advanced Packaging Epics:
SiP Saga: Flip Chip Package Substrates take center stage in the grand System-in-Package (SiP) saga, where multiple chips unite in a harmonious ensemble.
3D Prowess: Venture into the realm of 3D packaging—a narrative of stacking where semiconductor dies ascend vertically, potentially featuring through-silicon vias (TSVs) for vertical connections.
Interposer Enigma:
Silicon or Glass Charm: Interposer technologies weave an enigmatic tale, employing silicon or glass to create a high-density platform, a captivating platform for integrating diverse semiconductor components.
In the symphony of Flip Chip Package Substrate manufacturing, materials, technologies, and processes converge in a choreographed performance, crafting the foundation for reliable and high-performance semiconductor devices across a myriad of applications.
Frequently Asked Questions (FAQs)
What are the diverse design options available for Flip Chip Package Substrates?
Designs can vary, featuring layered structures for intricate routing, through-hole configurations enabling vertical connections, and flexibility variations (rigid, flexible, or semi-flexible) tailored to the unique demands of different applications.
How does the underfill material contribute to the assembly process in Flip Chip Package Substrates?
The underfill material is applied post flip chip bonding, filling the void between the chip and substrate. It enhances mechanical strength, relieves stress, and improves thermal conductivity for optimal performance.
What surface finishes are commonly applied to substrate pads for Flip Chip Package Substrates?
Substrate pads receive refined coatings such as gold, tin, or a combination of metals, ensuring impeccable solderability and safeguarding against oxidation.
What measures are in place for quality control during Flip Chip Package Substrate manufacturing?
Quality control involves the meticulous scrutiny of Automated Optical Inspection (AOI) systems, checking for defects, and the insightful gaze of X-ray technology, ensuring solder joint integrity and uniform underfill distribution.
Are there advanced packaging technologies associated with Flip Chip Package Substrates?
Absolutely! Technologies like System-in-Package (SiP) and 3D packaging may incorporate Flip Chip Package Substrates. SiP unites multiple chips in a single package, while 3D packaging elevates the game by stacking semiconductor dies vertically.
What role do interposers play in the realm of Flip Chip Package Substrate technology?
Interposers, crafted from silicon or glass, can be enlisted to create a high-density platform, adding a layer of sophistication for integrating multiple semiconductor components in specific applications.
Conclusion
In conclusion, the world of Flip Chip Package Substrates unfolds as a dynamic realm where precision and innovation converge. As a pivotal component in semiconductor packaging, Flip Chip Package Substrates play a multifaceted role, providing a robust platform for semiconductor chips through the artistry of flip chip bonding.
The manufacturing journey reveals a tapestry of materials, from organic wonders like epoxy-based laminates to the thermal prowess of inorganic ceramics. Designs vary, offering layered elegance, through-hole intricacies, and flexibility adaptations to meet the diverse needs of applications.
Flip chip bonding takes center stage, delicately aligning semiconductor chips and substrate with solder bumps orchestrating a symphony of direct electrical connections. The application of underfill material post-bonding enhances mechanical strength and thermal conductivity, ensuring a harmonious integration.
Surface finishes add a touch of refinement to substrate pads, safeguarding against oxidation and ensuring impeccable solderability. Quality control measures, from Automated Optical Inspection (AOI) systems to X-ray scrutiny, ensure the integrity of each assembly, providing a stage for reliable and high-performance semiconductor devices.
The narrative extends to advanced packaging technologies, where Flip Chip Package Substrates seamlessly integrate into System-in-Package (SiP) sagas and elevate experiences with 3D packaging, stacking semiconductor dies in vertical harmony. Interposers, like enigmatic companions, enhance the landscape with high-density platforms for multiple semiconductor components.
In this symphony of manufacturing intricacies, Flip Chip Package Substrates emerge as protagonists, crafting the foundation for electronic devices across diverse applications. Their story continues to evolve, guided by the pursuit of efficiency, reliability, and the ever-expanding horizons of technological innovation. As we navigate this landscape, the dance between precision and creativity propels us forward into the future of semiconductor packaging.