Flip Chip CSP Package Substrate Manufacturer
Flip Chip CSP Package Substrate Manufacturer,The Flip Chip CSP (Chip-Scale Package) Package Substrate is a cutting-edge technology used in semiconductor packaging. It combines the benefits of flip chip technology and chip-scale packaging to achieve a compact and high-performance solution. The substrate provides a platform for direct chip-to-board connections through solder bumps, enhancing electrical performance by reducing signal path lengths and improving heat dissipation. This design is ideal for applications requiring miniaturization, such as smartphones, wearables, and IoT devices. By offering increased component density and reliability, Flip Chip CSP Package Substrates play a crucial role in the advancement of modern electronic devices.
A Flip Chip Chip-Scale Package Substrate stands as a transformative semiconductor packaging technology, altering the traditional dynamics of connecting semiconductor dies to substrates or printed circuit boards (PCBs). Departing from the conventional approach of mounting chips upright, the Flip Chip CSP involves an unconventional flip, placing the semiconductor die upside down and directly adhering it to the substrate or PCB. This distinctive method employs small solder bumps or balls for electrical connections, resulting in a package that is not only compact but also boasts a low-profile design.
Key to this chip-scale packaging is its size, deliberately aligned with that of the semiconductor chip itself. This innovation brings forth several notable advantages:
Compact Form Factor: The package is compact and characterized by a low profile, making it a preferred choice for applications where spatial constraints are a critical consideration.
Performance Boost: Flip Chip connections introduce heightened electrical and thermal performance, surpassing the capabilities of traditional packaging methods.
Minimized Interconnection Lengths: Establishing a direct connection between the chip and substrate reduces interconnection lengths, contributing to an overall enhancement in electrical performance.
Effective Thermal Control: The direct attachment mechanism facilitates efficient dissipation of heat from the chip to the substrate.
Widely adopted in diverse electronic devices, from microprocessors to memory chips and various integrated circuits, Flip Chip CSP addresses challenges related to spatial efficiency, performance elevation, and adept thermal regulation.
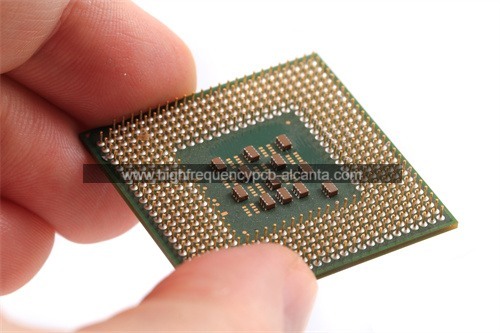
Flip Chip CSP Package Substrate Manufacturer
What Functions Does Flip Chip CSP Package Substrate Have?
Enter the realm of semiconductor orchestration with the Flip Chip Chip-Scale Package (CSP) Substrate, a versatile performer donning many hats in the intricate dance of packaging technology:
Electrical Maestro: At its core, the substrate conducts the symphony of electrical connectivity. Through the artful use of solder bumps or balls, it creates a seamless connection, allowing the semiconductor die to harmonize with the substrate or printed circuit board (PCB).
Signal Navigator: Beyond mere connection, the substrate takes on the role of a signal conductor, guiding electrical signals with finesse between the semiconductor die and other components within the electronic ensemble.
Heat Choreographer: Unveiling its prowess in thermal management, the substrate conducts a ballet of heat dissipation. By anchoring the chip directly, it orchestrates a delicate dance, ensuring optimal temperatures and shielding against thermal stress.
Structural Guardian: In the grand performance, the substrate stands as a stalwart guardian, offering mechanical support to the semiconductor die. It shields against the percussions of external forces, be it vibrations or physical impacts, preserving the integrity of the packaged spectacle.
Space Whisperer: A silent participant in the pursuit of compactness, the substrate plays a pivotal role in crafting a low-profile package. The direct attachment method reduces the footprint, contributing to the symphony of spatial efficiency.
Precision Partner: Not a mere spectator, the substrate actively engages in the packaging ballet. It facilitates the exact alignment and positioning of the semiconductor die, a crucial act in ensuring the precision of electrical connections and the structural harmony of the entire composition.
Integration Virtuoso: In the grand symphony of electronic devices, the substrate seamlessly integrates the packaged semiconductor device with external components on the printed circuit board. It ensures a harmonious collaboration within the broader system.
Performance Alchemist: Through its alchemical touch, the Flip Chip CSP substrate transforms the mundane into brilliance. By optimizing interconnection lengths and mastering thermal nuances, it contributes to an alchemical enhancement of both electrical and thermal performance.
In the intricate choreography of semiconductor packaging, the Flip Chip CSP Package Substrate emerges as a versatile virtuoso, conducting a symphony of functions that transcend mere connectivity, encompassing thermal finesse, structural resilience, and spatial grace.
What are the Different Types of Package Substrate?
Embark on an illuminating exploration of semiconductor packaging substrates, each meticulously tailored to meet specific needs and applications. Here’s a glimpse into this diverse spectrum:
Printed Circuit Board (PCB): PCBs, meticulously shaped using materials such as FR-4, act as dynamic foundations for the mounting and interconnection of electronic components, including semiconductor devices. With a layered structure, they offer a versatile base that accommodates a myriad of functionalities.
Leadframe:In the realm of packaging configurations such as Dual In-Line Packages (DIP) and Quad Flat Packages (QFP), leadframes stand as stalwart contributors. Crafted from resilient metals like copper, they assume a crucial role in facilitating indispensable electrical connections for semiconductor devices via their leads.
Ceramic Substrates: Ceramic substrates, hailed for their remarkable thermal conductivity, whether crafted from alumina or aluminum nitride, find a specialized role in high-power applications by facilitating efficient heat dissipation.
Organic Substrates: Embracing materials like BT or epoxy, organic substrates serve as the backbone of cutting-edge packaging technologies. Configurations like Ball Grid Array (BGA) and Chip-on-Board (COB) thrive on their commendable electrical performance.
Flexible Substrates: Delving into flexibility, polyimide-based flexible substrates gracefully cater to applications like wearable devices and flexible displays, where adaptability takes center stage.
Metal Core PCB (MCPCB): Elevating thermal conductivity, MCPCBs, adorned with robust aluminum cores, shine in applications demanding efficient heat dissipation, such as high-power LED modules.
Glass Substrates: Stepping into the realm of advanced semiconductor packaging, glass substrates captivate attention, particularly in applications like microelectromechanical systems (MEMS), offering a harmonious blend of dimensional stability and transparency.
Copper Substrates: With an unwavering focus on high thermal conductivity, copper substrates find their calling in applications requiring superior heat dissipation, notably in power modules.
The selection of a package substrate unfolds against the backdrop of factors such as thermal requirements, electrical specifications, form factor, and the unique needs of the electronic device. Various packaging technologies adeptly leverage different substrate types, creating a nuanced tapestry of performance optimization and reliability.
What is the Relationship Between Flip Chip CSP Package Substrate and IC Packaging?
The intricate dance between Flip Chip Chip Scale Package (CSP) substrates and Integrated Circuit (IC) packaging is a cornerstone in the realm of semiconductor device assembly. Let’s unravel the nuances of this relationship:
Connection Choreography: Flip Chip CSP steps onto the stage as a distinctive IC packaging technology. Here, the semiconductor die takes a bold flip, connecting directly to the substrate or package. This departure from traditional wire bonding brings a fresh rhythm to the packaging process.
Spatial Symphony: Flip Chip CSP takes center stage for its choreography of space efficiency. By eschewing the need for additional bonding wires, it orchestrates a harmonious reduction in package size, a crucial note in the symphony of modern electronics where miniaturization is a defining movement.
Electrical Harmony: The direct connection in Flip Chip CSP orchestrates a symphony of enhanced electrical performance. The shortened interconnection lengths and minimized parasitic elements create a composition conducive to improved signal integrity and accelerated data transfer rates, making it a fitting overture for high-performance applications.
Thermal Ballet: In this performance, the choice of substrate material is a pivotal dancer in the thermal ballet. The substrate pirouettes as it manages the heat choreography, playing a crucial role in effective thermal dissipation. The material, whether organic, ceramic, or metal core PCB, must match the thermal conductivity demands of the act.
Package Sonata: Flip Chip CSP harmonizes with various substrate types, each lending its unique melody. Organic substrates, akin to FR-4, lend their notes to cost-effective compositions, while ceramic substrates, like alumina or aluminum nitride, contribute their thermal prowess to high-power symphonies.
Assembly Waltz: The assembly process of Flip Chip CSP is a well-choreographed waltz. The chip gracefully takes its place on the substrate, the dance precision executed through advanced packaging technologies such as solder bumping and underfill encapsulation.
Application Serenade: The melodic tones of Flip Chip CSP resonate across diverse applications. From the handheld sonatas of smartphones and tablets to the grand symphonies of high-performance computing, its composition of compact size, high-speed prowess, and thermal finesse strikes the right chords.
In essence, the relationship between Flip Chip CSP package substrates and IC packaging is a symphony of symbiosis. Flip Chip CSP, as a distinct IC packaging maestro, twirls and tangoes with a well-designed substrate to compose a sonnet of space efficiency, high-performance crescendos, and thermal mastery. The choice of substrate material and design, akin to musical notes, orchestrates the cadence and resonance of the integrated circuit package.
What are the Differences Between Package Substrate and PCB?
Embark on an exploration of the nuanced disparities between package substrates and Printed Circuit Boards (PCBs), integral players in the symphony of electronic systems. Let’s uncover the distinctive features that set them apart:
Function and Purpose:
Package Substrate: Positioned as the cornerstone for mounting and connecting semiconductor devices, the package substrate takes center stage in facilitating electrical connections and, on occasion, contributing to the thermal management of the embedded chip.
PCB: Assumes the central role as a versatile platform for hosting a myriad of electronic components. Beyond semiconductor devices, PCBs weave a comprehensive network of electrical connections, allowing signals and power to gracefully traverse the entire electronic ensemble.
Mounting Ensemble:
Package Substrate: Sculpted with precision for the mounting of semiconductor chips, the substrate is a canvas optimized for the attachment and interconnection of the chip’s bonding pads with the external landscape.
PCB: A sprawling canvas that accommodates an eclectic ensemble of electronic components—from resistors to capacitors and transistors. PCBs provide an expansive stage for the mounting and interconnection of a diverse cast of elements.
Material Tapestry:
Package Substrate: Adaptable to a tapestry of materials, be it the organic resonance of substrates like FR-4, the ceramic allure of alumina or aluminum nitride, or the sturdy foundation of metal core PCBs. Material selection dances to the rhythms of thermal needs, electrical properties, and cost considerations.
PCB: Traditionally attuned to materials like FR-4, PCBs are equally receptive to alternative notes, such as ceramics or metal cores, harmonizing with the unique demands of diverse applications.
Design Choreography:
Package Substrate: A dance of specialization, the design of the package substrate is finely tuned to the specific demands of the semiconductor device it cradles. Its choreography leans towards precision, tailored to the chip’s unique requirements.
PCB: Unveiling a symphony of versatility, PCBs flaunt a more intricate layout. Their canvas accommodates a complex arrangement of components and intricate electronic circuits, embodying the versatility needed to support the multifaceted requirements of electronic systems.
Integration Harmony:
Package Substrate: A maestro in the integration of a singular semiconductor chip, conducting a symphony at the component level.
PCB: The virtuoso of system-level integration, orchestrating the integration of multiple components and chips, weaving a tapestry that resonates across the entire electronic spectrum.
In unraveling these distinctions, one can navigate the intricate choices between package substrates and PCBs, selecting the most fitting component based on the unique requirements and aspirations of the electronic design.
What are the Main Structures and Production Technologies of Flip Chip CSP Package Substrate?
Embark on a captivating exploration into the realm of Flip Chip Chip Scale Package (CSP) package substrates, where structures and production technologies converge to shape the backbone of cutting-edge electronics. Let’s navigate the intricate features:
Structural Composition:
Core Substrate:
Foundational Base: The core substrate, hewn from materials like FR-4 or flexible polyimide, establishes the bedrock for the substrate’s architectural elegance.
Bump or Solder Ball Array:
Connective Choreography: The semiconductor die’s active side boasts an array of bumps or solder balls, engaged in a sophisticated dance as part of the flip chip bonding spectacle.
Dielectric Layers:
Insulating Symphony: Interspersed dielectric layers weave a symphony of insulation, safeguarding the substrate’s structural integrity while harmonizing with its electrical performance.
Routing and Signal Layers:
Conductive Pathway Ballet: Layers dedicated to routing signals choreograph a ballet of conductive pathways, orchestrating an exquisite symphony of electrical connectivity.
Cavity for Die Placement:
Strategic Stage: A meticulously designed cavity or recessed area becomes the stage for the semiconductor die, adding an element of sophistication to the overall compactness of the package.
Underfill Material:
Protective Embrace: Post flip chip bonding, an underfill material embraces the structure, fortifying its stability and shielding against external influences.
Technological Tapestry:
Photolithography:
Artistic Patterning: Photolithography, akin to an artist’s brushstroke, intricately patterns the substrate layers, crafting visually captivating and functionally precise designs.
Electroplating:
Conductive Alchemy: Electroplating, a touch of alchemical prowess, deposits thin layers of conductive materials like copper, infusing the substrate with an enchanting blend of conductivity.
Die Attach and Flip Chip Bonding:
Bonding Ballet: The die attach and flip chip bonding processes unfold a ballet of attachment, seamlessly connecting the semiconductor die to the substrate in a meticulously choreographed sequence.
Laser Drilling:
Precision Sculpting: Laser drilling, a tool of precision sculpting, etches out cavities in the substrate, providing a canvas for the artful placement of the semiconductor die.
Underfill Encapsulation:
Encapsulation Sonata: Post flip chip bonding, the underfill material is dispensed and cured, conducting a sonata of encapsulation that fortifies the chip, ensuring resilience and longevity.
Quality Control and Testing:
Verification Waltz: Rigorous quality control measures and testing protocols engage in a waltz of verification, ensuring that each Flip Chip CSP substrate is a masterpiece of reliability and functionality.
In this symphony of structures and technologies, Flip Chip CSP package substrates emerge as the unspoken architects, composing a harmonious blend of form and function in the grand tapestry of electronic innovation.
Frequently Asked Questions (FAQs)
Can You Outline the Manufacturing Process for Flip Chip CSP Package Substrates?
The manufacturing process involves intricate steps such as photolithography for precision patterning, electroplating for depositing conductive layers, die attach for affixing the semiconductor die, flip chip bonding for interconnecting the die and substrate, laser drilling for creating cavities, and underfill encapsulation for protective shielding. Quality control and testing are integral throughout.
What Advantages Do Flip Chip CSP Package Substrates Offer?
Flip Chip CSP Package Substrates provide advantages like a reduced footprint, enhanced electrical performance with shorter interconnections, effective thermal management, and suitability for high-density applications.
Can Manufacturers Customize Flip Chip CSP Package Substrates for Specific Applications?
Yes, manufacturers offer customization options, tailoring Flip Chip CSP Package Substrates to specific applications by selecting suitable substrate materials, designing specialized structures, and meeting unique project requirements.
What Quality Assurance Measures Are Employed by Manufacturers?
Manufacturers implement robust quality assurance measures, conducting rigorous testing to ensure substrates adhere to electrical performance standards, reliability benchmarks, and specifications.
Is the Presence of Flip Chip CSP Package Substrate Manufacturers Global?
Yes, Flip Chip CSP Package Substrate manufacturers often have a global presence with production facilities, sales offices, or distribution networks spanning different regions to cater to the global semiconductor industry.
How Can I Select the Right Flip Chip CSP Package Substrate Manufacturer for My Project?
The selection process involves evaluating factors such as the manufacturer’s experience, expertise in substrate materials, customization capabilities, quality control practices, and industry reputation. Direct discussions about project requirements ensure alignment with the chosen manufacturer.
Conclusion
In conclusion, the realm of Flip Chip CSP Package Substrates unfolds as a symphony of innovation, where manufacturers play a pivotal role in crafting the building blocks of advanced semiconductor technologies. These FAQs shed light on the intricacies of Flip Chip CSP Package Substrates and the expertise required in their production. From material versatility to the dance of fabrication processes, manufacturers orchestrate a harmonious blend of form and function.
The core substrate, adorned with bump arrays and intricate layers, becomes a canvas for the delicate artistry of flip chip bonding. This technique, intimately linked to CSP Package Substrates, enhances electrical performance and minimizes footprint, unleashing a new era of compact and high-performance electronic devices.
Manufacturers navigate a meticulous process, from photolithography’s artful patterning to laser drilling’s precision sculpting, ensuring each substrate meets stringent quality standards. The advantages of Flip Chip CSP Package Substrates, including reduced footprint and superior thermal management, position them as frontrunners in the semiconductor packaging landscape.
Customization emerges as a key theme, with manufacturers tailoring substrates to specific applications. The global presence of these manufacturers reflects the expansive reach of semiconductor technologies, bridging regions to meet the dynamic demands of the industry.
In the journey of selecting the right manufacturer, project planners are encouraged to consider experience, material expertise, customization options, and quality assurance measures. Direct communication with manufacturers ensures a nuanced understanding of project requirements and paves the way for collaborative innovation.
As the curtain falls on these FAQs, the Flip Chip CSP Package Substrate manufacturers continue to be the unsung architects, crafting the foundation for the electronic marvels that shape our interconnected world.