FCCSP Flip Chip Package Substrate Manufacturer
FCCSP Flip Chip Package Substrate Manufacturer,FCCSP (Flip Chip Chip Scale Package) Substrate combines flip chip and chip scale packaging technologies, offering compact design and high performance. This substrate facilitates direct chip-to-board connections, reducing signal path lengths and enhancing electrical performance. Comprising multiple layers including insulating, metal, and conductor layers, FCCSP Substrate ensures reliable connections and efficient heat dissipation. It finds applications in portable electronics, IoT devices, and automotive electronics, optimizing space utilization while maintaining reliability. FCCSP Substrate enables sleek designs and improved functionality in various electronic products, meeting the demands of modern technology-driven markets.
FCCSP (Flip Chip Package Substrate) is an integrated circuit packaging technology specifically designed for flip-chip assembly. In traditional packaging, chips are connected to the package substrate through solder balls or wires, but in FCCSP, the chip is directly flipped and mounted on the substrate, connected through micro-scale solder joints or other interconnect structures.
The main advantages of FCCSP technology include shorter signal transmission paths, smaller package sizes, lower inductance and resistance, and improved thermal performance. These features make FCCSP widely used in high-performance and high-density applications, such as mobile devices, communication equipment, and computer chips.
The basic construction of this technology includes the substrate, chip, interconnect points, and possibly heat dissipation structures. The substrate typically employs a multilayer structure to provide channels for electrical connections and signal transmission. Interconnect points can be solder balls, electrodes, or other small contact points used to connect the chip and substrate. In the design, FCCSP must consider requirements related to thermal management, electrical performance, and mechanical stability.
In summary, FCCSP is an advanced integrated circuit packaging technology that enhances the performance and reliability of electronic devices by optimizing the layout of chips and substrates.
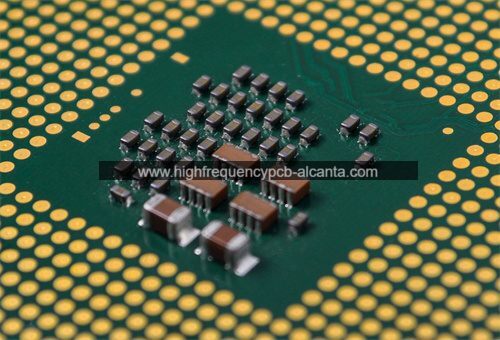
FCCSP Flip Chip Package Substrate Manufacturer
What are the Functions of FCCSP Flip Chip Package Substrate?
The FCCSP (Flip Chip Package Substrate) assumes a pivotal role in the packaging dynamics of flip-chip assemblies within integrated circuits, manifesting diverse functionalities:
Electrical Conduit:
The substrate functions as an electrical conduit, establishing seamless connectivity between the flip-chip and the broader electronic framework. It ensures the unimpeded flow of signals and facilitates the even distribution of power to the flip-chip.
Structural Pillar:
Operating as a foundational element, the substrate provides indispensable structural support. It upholds the positional stability and structural integrity of the flip-chip within the packaging framework.
Heat Dispersion Hub:
The substrate actively contributes to efficient heat dissipation, a critical consideration given the thermal output from the flip-chip during operational phases. This is further augmented by features such as thermal vias and specialized layers.
Guardian of Signal Integrity:
Through intentional design and material nuances, the substrate becomes a guardian of signal integrity. It mitigates issues such as signal loss and crosstalk, ensuring the fidelity of transmitted signals.
Compact Package Maestro:
FCCSP, with its innate design attributes, facilitates the creation of more compact packages, offering a departure from traditional bulkier packaging methods. This aligns with the ongoing trend of miniaturization in electronic devices.
Performance Augmenter:
By curtailing signal path lengths and minimizing parasitic effects, FCCSP actively contributes to the augmentation of electrical performance. This translates to expedited signal propagation and a reduction in undesirable electrical noise.
Champion of High-Density Integration:
The compact design inherent in FCCSP positions it as a champion for high-density integration of electronic components. This makes it an apt choice in scenarios where spatial considerations are paramount.
Economical Manufacturing Facilitator:
The adoption of flip-chip assembly and FCCSP technology often streamlines manufacturing processes, optimizing material utilization and assembly procedures for enhanced cost-effectiveness.
In essence, FCCSP emerges as a versatile linchpin, addressing vital aspects of electrical connectivity, structural robustness, thermal management, and overall system proficiency. Its design intricacies and functional repertoire significantly propel the evolution of electronic devices in terms of size, efficiency, and dependability.
What are the Different Types of FCCSP Flip Chip Package Substrate?
FCCSP (Flip Chip Package Substrate) manifests itself in an array of types, each meticulously tailored to address specific applications and requisites. Let’s explore some key categorizations:
Organic Substrates:
FR-4 (Flame Retardant-4): A widely embraced and budget-friendly substrate crafted from woven glass-reinforced epoxy. While versatile, FR-4 might encounter constraints in environments characterized by high frequency and temperature.
High-Performance Organic Substrates: Harnessing advanced materials like liquid crystal polymer (LCP) or polyimide, these substrates ascend to a realm of heightened thermal and electrical prowess, rendering them apt for demanding high-speed and high-frequency applications.
Ceramic Substrates:
Alumina (Al2O3): Acclaimed for its stellar thermal conductivity and mechanical fortitude, alumina substrates shine in arenas where efficient heat dissipation is non-negotiable.
Aluminum Nitride (AlN): As a ceramic counterpart with commendable thermal conductivity, AlN substrates prove invaluable in scenarios that demand superior thermal performance, particularly in power electronics.
Flexible Substrates:
Polyimide Films: Nimble and lightweight, polyimide films carve a niche in applications craving adaptability, such as in wearable devices or the realm of flexible electronics.
Heterogeneous Integration Substrates:
Silicon Interposers: Silicon substrates adorned with through-silicon vias (TSVs) pave the way for the integration of diverse technologies, offering a tapestry of possibilities, like the harmonious fusion of a logic chip with a memory chip.
Glass Interposers: Bestowing an alternative to silicon, glass-based interposers contribute to achieving goals in heterogeneous integration.
Metal Core Substrates:
Aluminum or Copper Metal Core: Showcasing a metal layer for amplified thermal conductivity, these substrates prove their mettle in applications where the efficient dissipation of heat takes center stage, such as in the radiant domain of high-power LED applications.
Advanced Packaging Technologies:
Fan-Out Wafer-Level Packaging (FOWLP): Pioneering a progressive path, this packaging technique bids farewell to the conventional substrate. The redistribution layer (RDL) choreographs a direct connection between the flip-chip and a molded underfill, giving rise to a package that is both compact and slender.
System-in-Package (SiP): Assembling multiple circuits or functional blocks within a single package, SiP orchestrates a ballet of substrates, harmonizing the unique attributes of each to optimize performance for every constituent.
This rich tapestry of FCCSP substrate options caters to nuanced considerations, ranging from thermal dynamics and flexibility to signal fidelity and cost-effectiveness. The selection of a specific substrate type becomes an art, finely tuned to the distinctive demands of the electronic device or system in question.
What is the Relationship Between FCCSP Flip Chip Package Substrate and IC Packaging?
The alliance between FCCSP (Flip Chip Package Substrate) and IC (Integrated Circuit) packaging is deeply rooted in their collaborative role in advancing semiconductor packaging technology. FCCSP serves as a specialized approach within the realm of IC packaging, primarily tailored for the unique demands of flip-chip assemblies. Let’s unravel the nuances of this relationship:
Packaging Synergy:
FCCSP emerges as a distinctive packaging technology, intricately woven into the broader tapestry of IC packaging methodologies.
Flip-Chip Dynamics:
At its core, FCCSP excels in facilitating flip-chip assembly, a departure from conventional packaging approaches where the chip is traditionally oriented with its front side facing up.
Direct Kinship:
The essence of FCCSP lies in the direct interconnection between the flip-chip and the substrate, utilizing micro-scale solder joints or alternative interconnect structures. This direct link is pivotal, leading to reduced signal path lengths and heightened electrical performance.
Signal Symphony:
FCCSP orchestrates a symphony of benefits, offering shorter signal transmission paths, compact package sizes, and superior thermal management compared to traditional IC packaging methods. The amalgamation of these features enhances signal integrity and overall performance.
Multilayer Tapestry:
The substrate within FCCSP unfolds as a multilayered canvas, intricately designed to carve channels for electrical connections and signal transmission. This substrate intricacy is instrumental in optimizing electrical efficiency and ensuring the structural robustness of the assembly.
Density Dance:
FCCSP takes center stage in applications where high-density integration is paramount, such as in the domains of mobile devices, communication equipment, and high-performance computing chips.
Thermal Ballet:
The choreography of thermal management is elegantly executed by FCCSP, strategically addressing the dissipation of heat. This thermal consideration is crucial for bolstering the reliability and endurance of integrated circuits.
Customization Canvas:
The diverse array of FCCSP substrates serves as a customizable canvas, allowing for tailoring based on specific needs like flexibility, thermal conductivity, and cost considerations.
In essence, FCCSP and IC packaging engage in a collaborative dance, with FCCSP offering a specialized and refined solution within the intricate landscape of semiconductor packaging technologies. Together, they propel the evolution of integrated circuits, enhancing their performance, reliability, and adaptability in the ever-evolving landscape of electronic devices.
How Does FCCSP Flip Chip Package Substrate Differ from Traditional PCBs?
FCCSP (Flip Chip Package Substrate) emerges as a divergent force when juxtaposed with the conventional landscape of traditional PCBs (Printed Circuit Boards). The divergence is conspicuous in the realms of design philosophy, assembly intricacies, and performance attributes. Let’s embark on a journey to delineate the distinguishing features that set FCCSP apart from its conventional counterpart:
Choreography of Flip-Chip Elevation:
FCCSP: Imbued with the essence of flip-chip assembly, FCCSP orchestrates the elegant inversion of the semiconductor chip, delicately placing it directly onto the substrate. This inversion lends itself to a unique dance, fostering a direct and efficient interplay between the chip and the substrate.
Traditional PCBs: In the traditional ballet of PCBs, components adhere to a conventional pose, with their leads gracefully facing upward. The notion of flip-chip assembly remains an unconventional divergence in this classical setting.
Direct Interlacing Threads:
FCCSP: Micro-scale solder joints or alternative interconnect structures weave an intricate tapestry within FCCSP, forming a direct connection that shortens signal paths. This artistic interplay mitigates parasitic effects and accentuates the symphony of electrical performance.
Traditional PCBs: The traditional PCB script includes a repertoire of interconnection techniques such as through-hole vias and surface mount technology. However, the direct interconnection elegance of flip-chip assembly is not a standard motif.
Gracefully Compact Ensemble:
FCCSP: Celebrated for its compact design, FCCSP takes center stage in applications where spatial constraints dictate the choreography. The streamlined design is particularly appealing in scenarios where a diminutive footprint becomes a performance imperative.
Traditional PCBs: While traditional PCBs traverse a spectrum of sizes, the pursuit of the same level of miniaturization as FCCSP is not an inherent feature, owing to divergent assembly methodologies.
Thermal Ballet Extravaganza:
FCCSP: A maestro in thermal dynamics, FCCSP elegantly dissipates the heat emanating from the flip-chip. The intricacies of the substrate and packaging orchestrate a thermal ballet that adds to the performance finesse.
Traditional PCBs: Thermal management in traditional PCBs unfolds through methods like heat sinks and thermal vias. Effective in its own right, it unfurls a different act compared to the thermal symphony directed by FCCSP.
Integration Waltz:
FCCSP: Leading the waltz in high-density integration, FCCSP seamlessly integrates its compact design and direct interconnection in a dance tailored for applications that demand heightened performance.
Traditional PCBs: The integration dance in traditional PCBs involves intricate choreography, often requiring multiple layers, but it may not mirror the same finesse in high-density integration as the FCCSP waltz.
Versatile Performance on the Stage:
FCCSP: The limelight often bathes FCCSP in applications like mobile devices, high-performance computing, and communication equipment. Its unique choreography aligns with the critical demands of space, performance, and miniaturization.
Traditional PCBs: Versatility is the hallmark of traditional PCBs, featuring prominently across diverse industries, from consumer electronics to automotive and industrial realms.
In essence, FCCSP and traditional PCBs engage in a dialogue of divergence and distinction. FCCSP’s emphasis on flip-chip assembly, direct interconnection, compact design, and thermal finesse positions it as a virtuoso in the grand theater of semiconductor packaging. The choice between FCCSP and traditional PCBs becomes a matter of selecting the right performance for the specific needs of the electronic device or system at the center stage.
What are the Main Structure and Production Technologies of FCCSP Flip Chip Package Substrate?
The FCCSP (Flip Chip Package Substrate) is a marvel of intricacy, blending a nuanced structure with advanced production technologies. Let’s navigate through the facets of its composition and the sophisticated methods that breathe life into this high-performance substrate:
Composition Symphony of FCCSP:
Material Palette for Substrates:
FCCSP substrates boast a diverse material palette, spanning organic choices like FR-4 and advanced polymers (liquid crystal polymer, polyimide) to ceramic stalwarts such as alumina or aluminum nitride. The inclusion of flexible substrates like polyimide films adds a layer of adaptability.
Precision Circuitry and Wiring Choreography:
The substrate hosts a tapestry of intricate circuitry and wiring patterns meticulously designed to optimize electrical connectivity between the flip-chip and external components. This choreography prioritizes the minimization of signal path lengths, elevating overall performance.
Bump Pads: Precision Dance Partners:
Strategically positioned bump pads serve as the dance partners for the flip-chip, providing a stage for direct and precise connections. Materials like solder or conductive polymers choreograph this connection, ensuring a flawless interplay.
Dielectric Layers: Insulating Maestros:
Seamlessly integrated dielectric layers act as maestros, orchestrating insulation between different conductive layers. This harmonious addition contributes to the structural integrity and electrical isolation of the FCCSP.
Vias: Vertical Connectivity Artistry:
Vias, whether through-hole or microvias, contribute to the vertical connectivity masterpiece. These conduits facilitate electrical connections between different substrate layers, adding a layer of connectivity finesse.
Redistribution Layers (RDL): Layout Symphony:
The optimization of redistribution layers (RDL) plays a pivotal role in orchestrating the symmetrical layout of signals and power distribution. RDL contributes to the compact design and efficient arrangement of the FCCSP ensemble.
Underfill Material: Supporting Act:
Carefully selected underfill material takes on a supporting role beneath the flip-chip, enhancing mechanical stability, promoting thermal conductivity, and mitigating the impact of thermal disparities. This supporting act adds an extra layer of reliability to the assembly.
Production Ballet of FCCSP:
Substrate Manufacturing Prowess:
Substrate manufacturing unfolds with finesse, involving a series of steps such as lamination, patterning, and etching tailored to the specific substrate material. The approach is guided by considerations of thermal performance and flexibility.
Bump Formation Precision Ballet:
Bumps take shape on the substrate with precision, employing techniques like solder deposition, plating, or conductive polymer application. The aim is a synchronized dance of accurate and reliable connections with the flip-chip.
Flip-Chip Assembly Elegance:
The flip-chip is delicately placed onto the substrate using advanced assembly methods—whether it’s the nimble moves of pick-and-place machines or the graceful flow of solder reflow. This step ensures a flawless alignment and secure attachment.
Underfill Application Artistry:
Underfill material is applied strategically, optimizing the spatial relationship between the flip-chip and the substrate. This artistry enhances mechanical stability, facilitates effective thermal management, and provides a protective shield against environmental elements.
Integration of Advanced Packaging Technologies: Techno Waltz:
FCCSP often engages in a waltz with advanced packaging technologies, such as fan-out wafer-level packaging (FOWLP) or the intricate moves of system-in-package (SiP) techniques. This techno dance contributes to the art of miniaturization and optimizes the overall package aesthetics.
Quality Control Symphony:
Rigorous quality control measures, including the discerning eyes of visual inspection, the precise ears of electrical testing, and the calibrated instruments of thermal testing, come together in a symphony to ensure the FCCSP assembly meets the highest standards of reliability and functionality.
In essence, the FCCSP emerges as a symphony of materials and technologies, a masterpiece carefully crafted to meet the dynamic demands of contemporary electronic devices. The choice of substrate materials and production techniques reflects a meticulous harmony, tailored to the unique needs of each electronic system.
Frequently Asked Questions (FAQs)
How does FCCSP differ from traditional PCBs?
FCCSP distinguishes itself by its specialized design for flip-chip assembly. This involves directly mounting the flipped semiconductor chip onto the substrate, resulting in shorter signal paths, heightened electrical performance, and a more compact design compared to traditional PCBs.
What standout features define FCCSP substrates?
FCCSP substrates boast distinctive features, including bump pads for direct chip connections, intricate circuitry, dielectric layers for insulation, through-hole vias or microvias for vertical connections, redistribution layers (RDL) optimizing signal routing, and the use of underfill material for mechanical support and thermal management.
Can you elaborate on the manufacturing process of FCCSP substrates?
The manufacturing process involves meticulous steps, from selecting substrate materials to lamination, patterning, and etching for intricate circuitry. Bump formation, often using solder or conductive polymers, is crucial. Advanced technologies like fan-out wafer-level packaging (FOWLP) or system-in-package (SiP) may also be incorporated.
How do manufacturers ensure the quality of FCCSP substrates during production?
Quality control is paramount. Manufacturers conduct visual inspections, rigorous electrical testing for connectivity validation, and thermal testing to assess performance under varying temperatures. Stringent measures are taken to meet and surpass industry standards.
Where are FCCSP substrates commonly applied?
FCCSP substrates find versatile applications across electronic devices, including mobile devices, high-performance computing systems, communication equipment, and scenarios demanding a blend of miniaturization, improved electrical performance, and effective thermal management.
Conclusion
To encapsulate our exploration, FCCSP (Flip Chip Package Substrate) emerges as a trailblazer in the realm of semiconductor packaging, particularly renowned for its prowess in facilitating flip-chip assembly. The role of Flip Chip Package Substrate Manufacturers is nothing short of orchestrating a symphony, intricately designing, meticulously crafting, and seamlessly delivering substrates tailored for this specialized assembly technique.
The diverse selection of materials, spanning organic choices, high-performance polymers, ceramics, and flexible substrates, underscores FCCSP’s adaptability across various applications. Its distinctive features, from bump pads to intricate circuitry, usher in a new era of improved electrical performance and compact design, outshining conventional PCBs.
The manufacturing process unfolds like a meticulously choreographed dance, involving material selection, lamination, patterning, and the integration of cutting-edge technologies like FOWLP or SiP. Quality control measures, akin to a watchful guardian, ensure that FCCSP substrates meet and exceed the stringent standards set for electronic devices.
FCCSP’s versatility finds expression in an array of applications, from mobile devices to high-performance computing systems, where the trifecta of miniaturization, enhanced electrical performance, and efficient thermal management takes center stage.
Choosing the right FCCSP substrate manufacturer becomes a discerning task, demanding an evaluation of expertise, commitment to standards, and a proven track record. The industry’s trajectory, marked by trends like advanced packaging technologies and an unwavering focus on miniaturization, shapes the narrative, emphasizing the importance of staying attuned to the unfolding developments.
In essence, FCCSP emerges not just as a technological innovation but as a testament to precision engineering, steering the course of semiconductor packaging and meeting the dynamic demands of our electronic landscape. As we journey forward, the narrative of FCCSP unfolds, promising further breakthroughs and applications in the ever-evolving domain of electronic devices.