What are FCBGA Substrates?
FCBGA Substrates,FCBGA Substrates (Fine-pitch Ball Grid Array) are advanced packaging solutions for integrated circuits, facilitating high-density connections and efficient signal transmission. Utilizing a fine-pitch array of solder balls, FCBGA Substrates enable direct chip-to-board connections, enhancing performance and reliability in electronic devices. Composed of multiple layers including insulating, metal, and conductor layers, these substrates ensure robust electrical connectivity and effective thermal dissipation. Their compact design enables smaller form factors and higher component density, meeting the demands of modern electronics while maintaining optimal functionality and reliability.
FCBGA, or Flip-Chip Ball Grid Array, represents a packaging technology integral to the world of integrated circuits (ICs) and microprocessors. The linchpin of this packaging approach lies in the FCBGA substrates.
Let’s break down the essential terms:
Inverted Chip Technique: Unlike conventional packaging where ICs perch on a substrate with their active side facing upward, flip-chip packaging flips the IC, enabling its active side to directly engage with the substrate. This innovation paves the way for abbreviated interconnection paths and superior heat dissipation.
Spherical Grid Array (BGA): A species of surface-mount packaging for integrated circuits, BGAs discard conventional leads in favor of an array of petite solder balls beneath the package, establishing electrical connections with the circuit board.
Foundation Board: The substrate, often a laminate, acts as the material underpinning the installation and interconnection of various components in an integrated circuit. It provides a stable base for the chip and facilitates electrical connections between the chip and the circuit board.
Within the realm of FCBGA substrates, the term denotes the specific substrate tailored for flip-chip ball grid array packaging technology. These substrates are meticulously crafted to accommodate the flip-chip configuration and the solder balls facilitating electrical connections.
Given its prowess in electrical performance, adept thermal management, and an overall streamlined design, FCBGA packaging finds its niche in high-performance domains like microprocessors and other cutting-edge integrated circuits.
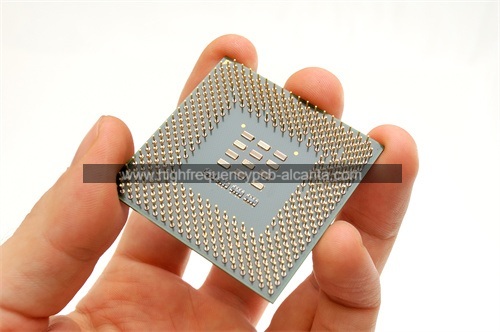
FCBGA Substrates
How do FCBGA Substrates Operate?
The operational intricacies of FCBGA substrates are intricately tied to the innovative flip-chip ball grid array (FCBGA) packaging methodology. Let’s unravel the mechanics of this process:
Inverted Chip Dynamics: FCBGA diverges from tradition by adopting an inverted mounting approach for the integrated circuit (IC). The active side of the IC intimately engages with the substrate, in contrast to the conventional orientation where the active side faces upward. This inverted configuration streamlines interconnection pathways and bolsters effective heat dissipation.
Substrate Foundation: The linchpin of FCBGA operation is the substrate, typically fashioned from materials like laminate. Serving as a robust underpinning for the IC, the substrate boasts a labyrinth of traces and vias facilitating essential electrical connections between the IC and the broader circuit.
Solder Ball Linkages: Positioned on the underside of the IC, an array of diminutive solder balls acts as conduits for electrical connections. As the IC is affixed onto the substrate, these solder balls establish contact with corresponding pads on the substrate, forging dependable electrical conduits.
Formation of Electrical Pathways: The intricate network of traces and vias on the substrate weaves a tapestry of electrical pathways, ensuring the seamless flow of signals between the IC and the larger circuit. The concise interconnection paths contribute to heightened signal integrity and minimized signal delay.
Thermal Dynamics: The flip-chip orientation plays a pivotal role in thermal management. With the active side of the IC directly interfacing with the substrate, heat generated during operation dissipates efficiently through the substrate and into the surrounding environment.
In essence, FCBGA substrates orchestrate their operation by embracing the flip-chip paradigm, providing a steadfast foundation for the IC, establishing electrical connections via solder balls, and orchestrating seamless signal transmission and effective heat dissipation. This packaging technology finds resonance in high-performance domains where precision in electrical functions and adept thermal control are paramount.
What Types of FCBGA Substrates Exist?
A spectrum of FCBGA substrate variants caters to diverse applications, each with its distinct attributes and advantages:
Organic Substrates: Crafted from materials like laminates or epoxy-based compounds, organic FCBGA substrates offer a cost-effective solution. Embraced in consumer electronics, they deliver robust electrical insulation properties, adapting seamlessly to a variety of applications.
Ceramic Substrates: Forged from materials such as alumina or aluminum nitride, ceramic FCBGA substrates stand out in thermal conductivity. Ideal for high-power scenarios where efficient heat dissipation is paramount, ceramic substrates find homes in aerospace, automotive, and high-performance computing.
Build-Up Substrates: Introducing layered complexity, build-up FCBGA substrates integrate additional insulating layers onto the base substrate. This design streamlines intricate routing of traces and vias, enabling higher density and sophisticated circuit designs. They are the go-to in applications requiring miniaturization and advanced packaging.
Low-Temperature Co-Fired Ceramic (LTCC) Substrates: A subset of ceramic substrates, LTCC substrates undergo firing at lower temperatures. This unique characteristic seamlessly integrates passive components, such as resistors and capacitors, directly into the substrate. LTCC FCBGA substrates find niches in RF scenarios.
High-Temperature Substrates: Tailored for applications navigating elevated operating temperatures, high-temperature FCBGA substrates exhibit resilience in demanding environments. These substrates maintain both structural integrity and electrical performance under extreme thermal conditions.
Selecting the optimal FCBGA substrate type hinges on specific application requirements, factoring in considerations like thermal dynamics, budget constraints, and the intricacy of the circuit design. Manufacturers meticulously navigate these considerations to pinpoint the substrate that aligns seamlessly with the performance and reliability prerequisites of the end product.
How do FCBGA Substrates Differ from Traditional PCBs?
FCBGA substrates and traditional PCBs diverge in several fundamental aspects, mainly due to the distinctive flip-chip packaging technology employed in FCBGA. Let’s delve into the key distinctions:
Chip Orientation:
FCBGA Substrates: Embrace an inverted approach where the integrated circuit (IC) is mounted upside down, presenting its active side to the substrate. This flip-chip configuration facilitates shorter interconnection paths and enhanced heat dissipation.
Traditional PCBs: Typically employ a conventional configuration with ICs mounted in a face-up or wire-bonded orientation, showcasing their active side.
Interconnection Method:
FCBGA Substrates: Utilize an array of small solder balls beneath the IC for direct electrical connections with the substrate. These solder balls establish contact with corresponding pads on the substrate.
Traditional PCBs: Often rely on through-hole or surface-mount technology, incorporating leads or pins for electrical connections.
Package Design:
FCBGA Substrates: Feature a distinct ball grid array on the IC’s bottom side, streamlining the soldering process and contributing to a more compact overall design.
Traditional PCBs: Exhibit diverse package designs, including configurations like dual in-line packages (DIP), surface-mount devices (SMD), and other variations depending on the application.
Thermal Performance:
FCBGA Substrates: Excel in thermal management due to the direct contact between the active side of the IC and the substrate, facilitating efficient heat dissipation.
Traditional PCBs: May require additional thermal considerations, such as heat sinks or cooling solutions, depending on the design and application.
Complexity and Miniaturization:
FCBGA Substrates: Enable a more compact design, shorter interconnections, and higher component density, making them well-suited for high-performance and miniaturized applications.
Traditional PCBs: Present a range of sizes and complexities, accommodating various interconnection methods and configurations to suit diverse applications.
In summary, FCBGA substrates leverage flip-chip technology, providing advantages in electrical performance, thermal management, and compact design, particularly suitable for high-performance applications when compared to the more traditional configurations of PCBs.
What is the Structure and Production Technologies of FCBGA Substrates?
The makeup of FCBGA (Flip-Chip Ball Grid Array) substrates involves a strategic assembly of key components, and its production encompasses specialized technologies tailored to the nuances of flip-chip packaging. Here’s a reimagined exploration of the structure and manufacturing processes:
Composition of FCBGA Substrates:
Fundamental Base Material:
Commencing with a base material, often a laminate or a purpose-selected substance chosen to establish a sturdy foundation for the integrated circuit (IC).
Traces and Vias Network:
Weaving a network of traces and vias within the substrate, crafting conductive pathways that play a pivotal role in establishing electrical connections between the IC and other integral components.
Strategic Solder Mask Application:
Applying a solder mask layer strategically, leaving apertures for the placement of solder balls. This layer serves the dual purpose of insulation and delineation of specific regions for soldering.
Solder Balls Array:
Arranging an array of diminutive solder balls on the underside of the IC, acting as conduits to facilitate robust electrical connections between the IC and the substrate.
Incorporation of Dielectric Layers:
In certain configurations, build-up substrates introduce additional layers of dielectric material. These supplementary layers, added atop the base substrate, often consist of insulating materials, enabling more intricate routing of traces and vias.
Manufacturing Technologies:
Precision Flip-Chip Bonding:
Employing flip-chip bonding methodologies with precision, entailing the attachment of the IC to the substrate with the active side strategically facing downward. Techniques like controlled collapse chip connection (C4) or solder bump technology find application.
Delicate Solder Ball Attachment:
Meticulous placement and attachment of solder balls to the IC’s underside, demanding attention to detail to ensure uniformity and reliability in the established connections.
Solder Reflow Mastery:
Subjecting the assembled components to solder reflow, a meticulous process involving controlled heating to melt the solder balls. This process culminates in the formation of sturdy solder joints between the IC and the substrate.
Comprehensive Testing and Inspection:
Rigorous post-assembly phase involving comprehensive testing procedures, including electrical assessments for connection integrity and optical inspections to identify any visual defects.
Harnessing Advanced Packaging Technologies:
Leveraging cutting-edge packaging technologies, encompassing equipment for precise component placement, automated soldering techniques, and inspection systems to uphold uncompromising quality standards.
Persistent Materials Innovation:
Continual research endeavors focused on the development of innovative substrate materials, with the aim of augmenting electrical performance, refining thermal management, and enhancing overall reliability.
The production narrative of FCBGA substrates unfolds as a meticulous dance between precision assembly, specialized soldering techniques, and stringent quality assurance measures, all orchestrated to ensure the end product’s integrity. Advances in materials and manufacturing technologies persist as driving forces behind continual enhancements in the realm of FCBGA substrate production.
Where do FCBGA Substrates Fit in Chip Package Technology Classification?
FCBGA (Flip-Chip Ball Grid Array) substrates are situated within the domain of advanced chip packaging technologies, specifically as a subset of flip-chip packaging. This innovative approach to mounting and connecting integrated circuits (ICs) distinguishes itself in the broader classification of chip package technology.
As a variant of Ball Grid Array (BGA) packaging, FCBGA leverages an array of solder balls for electrical connections, arranged in a grid-like pattern to streamline the soldering process and bolster overall reliability.
The hallmark of flip-chip packaging, exemplified by FCBGA, lies in the unconventional inversion of the IC. Unlike conventional methods where the active side faces upward, flip-chip technology orients the active side downward. This inversion introduces advantages such as shortened interconnection paths, heightened electrical performance, and more efficient thermal management.
As an integral component of advanced packaging technologies, FCBGA substrates respond to the escalating demands for heightened performance, compact design, and superior thermal regulation in the realm of electronic devices. This overarching category encompasses diverse strategies, including 3D packaging, System-in-Package (SiP), and other innovative methodologies extending beyond traditional packaging norms.
FCBGA substrates play a pivotal role in high-performance applications spanning sectors like computing, telecommunications, and automotive electronics. Their significance lies in contributing to miniaturization goals, facilitated by a compact design and reduced interconnection lengths, ultimately culminating in improved signal integrity.
To encapsulate, FCBGA substrates form a crucial component of advanced chip packaging technologies, embodying the flip-chip configuration within the broader landscape of Ball Grid Array packaging. Their strategic role addresses the evolving requirements of contemporary electronics, particularly in applications where heightened performance, miniaturization, and advanced packaging solutions are paramount.
FAQs
How does FCBGA differ from traditional chip packaging?
FCBGA deviates from traditional chip packaging with its flip-chip configuration. In this setup, the inverted IC utilizes solder balls for direct electrical connections, offering advantages such as shortened interconnection paths and enhanced thermal management.
What role do solder balls play in FCBGA substrates?
Solder balls in FCBGA substrates act as pathways for electrical connections between the IC and the substrate. Strategically placed on the IC’s bottom side, they form a grid-like pattern.
In which applications are FCBGA substrates commonly employed?
FCBGA substrates are prevalent in high-performance applications like computing, telecommunications, and automotive electronics. Their design suits scenarios where efficient heat dissipation and compact packaging are pivotal.
How does FCBGA contribute to the drive for miniaturization?
FCBGA’s flip-chip configuration and the use of solder balls facilitate a more compact design with shorter interconnection paths. This contributes significantly to the pursuit of miniaturization in electronic devices.
What are some key advantages of FCBGA substrates?
Advantages include shortened interconnection paths, enhanced electrical performance, efficient heat dissipation, and a compact design. These features make FCBGA substrates well-suited for high-performance and miniaturized applications.
Why is flip-chip bonding significant in FCBGA production?
Flip-chip bonding is pivotal in FCBGA production as it involves attaching the IC to the substrate with the active side facing downward. This bonding method ensures efficient electrical connections and enhances overall substrate reliability.
Conclusion
In summary, FCBGA (Flip-Chip Ball Grid Array) substrates stand as a pivotal advancement in chip packaging, offering distinct features to meet the evolving requirements of contemporary electronics. Utilizing a flip-chip configuration, where the integrated circuit is inverted and connected through an array of solder balls, FCBGA substrates bring benefits such as reduced interconnection paths, enhanced electrical performance, and effective heat dissipation.
These substrates have found extensive applications in high-performance sectors like computing, telecommunications, and automotive electronics, owing to their compact design and superior thermal management capabilities. The varied types of FCBGA substrates, including organic, ceramic, and build-up substrates, underscore their versatility in addressing diverse application needs.
The importance of flip-chip bonding in FCBGA production cannot be overstressed, as it ensures reliable electrical connections and bolsters the overall substrate reliability. Ongoing trends in FCBGA substrate technology highlight a commitment to continuous innovation in materials, manufacturing processes, and advanced packaging techniques. Research endeavors are focused on improving electrical performance, refining thermal management, and optimizing reliability across a spectrum of applications.
As FCBGA substrates continue to shape the chip packaging landscape, their role in driving miniaturization efforts and meeting the demands of high-performance electronic devices remains significant. In essence, FCBGA substrates emerge as leaders in advanced chip packaging technologies, embodying precision, efficiency, and adaptability to seamlessly align with the dynamic needs of the electronics industry.