What is FCBGA Packaging Substrate?
FCBGA Packaging Substrate,FCBGA Packaging Substrate,FCBGA Package Substrate (Fine-pitch Ball Grid Array) is an advanced packaging technology used for connecting and encapsulating integrated circuits. It employs a fine-pitch array of solder balls to connect the chip to the Printed Circuit Board (PCB), providing high-density signal transmission and power distribution. Typically comprising multiple layers of thin films, including insulating, metal, and conductor layers, FCBGA Package Substrate ensures reliable electrical connections and effective thermal management. Its compact design enables electronic devices to achieve higher component density and smaller form factors while maintaining performance and reliability.
FCBGA Packaging Substrate stands as a notable technological leap in the realm of electronic components, significantly influencing the architecture of integrated circuits (ICs). This innovative packaging methodology melds flip-chip technology with a ball grid array (BGA) configuration, reshaping the landscape of electronic device construction.
In essence, FCBGA involves an unconventional approach where the semiconductor die is inverted, placing its active side facing downward, directly affixing it to the packaging substrate. Departing from traditional methods, this design incorporates solder balls organized in a grid pattern on the package’s underside, forming what is termed as a Ball Grid Array.
The packaging substrate, acting as the fundamental material, offers a dual function: providing the necessary mechanical support for the IC and establishing crucial electrical connections.
Distinctive Characteristics and Benefits of FCBGA Packaging Substrate:
Performance Augmentation: The flip-chip design drastically reduces the distance between the IC and the substrate, resulting in shorter interconnect lengths. This translates to diminished electrical resistance and inductance, thereby elevating signal integrity and overall performance.
Efficient Thermal Regulation: Directly attaching the active side of the IC to the substrate optimizes heat dissipation. This proves particularly advantageous for high-performance ICs that tend to generate significant heat during their operational lifespan, ensuring a more effective thermal regulation mechanism.
Compact Design Efficiency: The BGA configuration’s grid layout allows for a high concentration of connections within a confined space. This compactness renders FCBGA well-suited for applications where spatial considerations are paramount.
The widespread adoption of FCBGA Packaging Substrate spans various electronic devices, including microprocessors and graphic processors. Its appeal lies in the ability to deliver heightened electrical performance, adept thermal management, and an overall boost in efficiency within electronic systems.
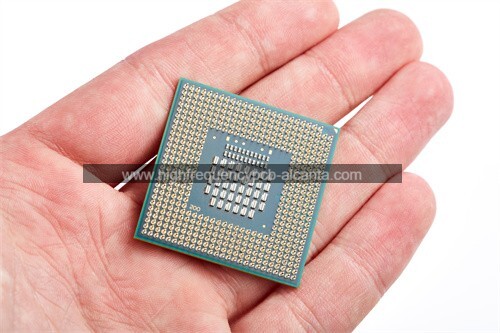
FCBGA Packaging Substrate
What Functions Does FCBGA Packaging Substrate Serve?
FCBGA (Flip-Chip Ball Grid Array) Packaging Substrate stands as a linchpin in the world of integrated circuits (ICs) and electronic devices, playing a diverse and integral role:
Sturdy Foundation: The packaging substrate is the backbone, providing essential mechanical support to the integrated circuit (IC). Its robust structure shields the IC from physical damage, ensuring the overall durability and reliability of the electronic component.
Electrical Pathway: As an electrical conduit, the substrate intricately weaves a network of conductive traces. This network facilitates the seamless transmission of electrical signals between the IC and external components or the circuit board, forming the nerve center of electronic connectivity.
Inventive Flip-Chip Arrangement: FCBGA introduces a paradigm shift with its flip-chip design, where the active side of the semiconductor die is ingeniously flipped and directly bonded to the packaging substrate. This innovative configuration minimizes interconnect distances, slashes resistance, and diminishes inductance, ultimately elevating the electrical performance of the IC.
Solder Ball Grid Choreography: Underneath the substrate lies a choreographed array of solder balls, crafting a Ball Grid Array (BGA). These solder balls are the unsung heroes, facilitating a reliable and efficient union between the IC and the circuit board, akin to the well-orchestrated steps of a dance.
Heat Harmony: FCBGA’s approach to thermal management is noteworthy. By directly linking the active side of the IC to the substrate, it orchestrates an efficient dissipation of heat. This feature proves invaluable for high-performance ICs that generate substantial heat during their operational symphony.
Compact Choreography: Embracing the grid layout philosophy, FCBGA choreographs a dance of connections within a confined space. This spatial efficiency is particularly advantageous for applications where real estate is a premium, making it a maestro in designing for compactness.
Symphony of Signal Integrity: The amalgamation of reduced interconnect lengths, lowered resistance, and minimized inductance, a result of the flip-chip ballet, creates a symphony that enhances signal integrity. This is the melody that ensures the harmonious transmission of electrical signals within the IC and across the circuit.
In essence, FCBGA Packaging Substrate emerges as a versatile artist, painting a canvas of structural resilience, electrical dexterity, and thermal efficiency for integrated circuits. Its avant-garde features cater to the nuanced demands of applications where spatial efficiency and high-performance standards are part of the grand composition.
What Are the Different Types of FCBGA Packaging Substrate?
FCBGA (Flip-Chip Ball Grid Array) Packaging Substrate exhibits a rich tapestry of variations, each crafted to address specific considerations such as material composition, design intricacies, and targeted applications. Let’s delve into the distinctive facets that characterize these diverse types:
Material Dynamics:
Organic Expressions: Composed of materials like epoxy resins or polyimide, organic substrates take center stage, valued for their cost-efficiency and manufacturing simplicity.
Inorganic Impressions: Embracing ceramics or glass, inorganic substrates step into the spotlight, particularly in applications where superior thermal conductivity is a critical attribute.
Layered Symphonies:
Solo Performances: Traditional FCBGA substrates follow a minimalist approach with a single layer of interconnects.
Orchestrated Layers: Advancing in complexity, certain FCBGA iterations weave intricate layers of interconnects, enabling sophisticated routing and fortifying signal integrity.
Performance Choreography:
High-Density Overtures: Tailored for applications demanding a profusion of connections in confined spaces, like the realm of high-performance computing or graphic processors.
High-Speed Rhythms: Engineered for accelerated data transfer, these FCBGA variants prioritize features such as signal integrity and meticulous impedance control.
Application Stories:
Consumer Electronics Saga: FCBGA substrates find resonance in the consumer electronics narrative, seamlessly integrating into devices like smartphones, tablets, and laptops.
Computing Systems Odyssey: Protagonists in the domain of processors and critical ICs within high-performance computing systems, servers, and data centers, FCBGA packaging takes on pivotal roles.
Tailored Artistry:
Application-Specific FCBGA: An exquisite craft tailored for specific industries or use cases, these substrates incorporate bespoke features aligning with the unique demands of particular applications.
In recognizing the versatile nature of FCBGA, it’s imperative to appreciate the nuanced design choices that may vary among manufacturers and applications. Engineers and designers, akin to skilled conductors, carefully navigate these variations when selecting FCBGA packaging substrates, considering factors such as thermal exigencies, electrical performance, cost dynamics, and the distinctive needs defining the electronic device’s intended narrative.
How Does FCBGA Packaging Substrate Differ from Traditional PCB?
FCBGA (Flip-Chip Ball Grid Array) Packaging Substrate and traditional PCB (Printed Circuit Board) represent distinct methodologies in the realm of electronic component integration. These methodologies diverge in design philosophies, interconnection strategies, approaches to heat dissipation, considerations of size, and overarching performance characteristics:
Mounting Perspectives:
FCBGA: A trailblazer in design, FCBGA adopts a flip-chip paradigm, positioning the semiconductor die with its active side facing downward, forming a direct bond with the substrate. This departure from conventional practices minimizes interconnect distances, ushering in superior electrical performance.
Traditional PCB: Adhering to a more established norm, ICs in traditional PCBs generally adopt a face-up orientation, relying on wire bonding or similar methods for electrical connections.
Interconnection Strategies:
FCBGA: Marked by the utilization of a Ball Grid Array (BGA) configuration, FCBGA orchestrates a grid pattern of solder balls beneath the package. This intricate arrangement not only ensures robust connections but also facilitates a compact and densely packed layout.
Traditional PCB: In contrast, traditional PCBs leverage diverse interconnection methods, encompassing through-hole or surface-mount technologies, utilizing solder joints or pins to establish connections.
Thermal Dynamics:
FCBGA: The direct tethering of the IC’s active side to the substrate in FCBGA strategically addresses heat dissipation, particularly advantageous in applications where thermal considerations take precedence.
Traditional PCB: Heat dissipation in traditional PCBs hinges on factors such as layout intricacies, material choices, and the potential incorporation of supplementary heat sinks.
Dimensions and Density:
FCBGA: Celebrated for its compact design, FCBGA finds a niche in applications defined by spatial constraints. The BGA configuration enables a high density of connections.
Traditional PCB: PCBs showcase a broad spectrum of sizes and complexities, serving a diverse array of applications with varying spatial demands.
Performance Dynamics:
FCBGA: The distinctive features encapsulated in FCBGA, including the flip-chip design and BGA configuration, contribute to heightened electrical performance, shortened interconnect lengths, and an enhanced semblance of signal integrity.
Traditional PCB: Performance nuances in traditional PCBs are nuanced, shaped by factors such as trace layout intricacies, judicious material choices, and considerations to maintain signal integrity.
In essence, while both FCBGA Packaging Substrate and traditional PCBs are integral to electronic systems, FCBGA stands out for its innovative design choices, compact form factor, and focus on optimized electrical and thermal performance—particularly pertinent in applications where spatial efficiency and high performance are critical. Traditional PCBs, meanwhile, embody versatility to cater to a broad spectrum of applications with diverse design requisites.
Where Does the Distinction Lie Between FCBGA Packaging Substrate and PCB?
The distinction between FCBGA (Flip-Chip Ball Grid Array) Packaging Substrate and PCB (Printed Circuit Board) manifests across multiple dimensions, delineating their unique approaches to electronic component integration. This demarcation encompasses fundamental design principles, chip mounting orientations, interconnection methodologies, heat dissipation strategies, considerations of size, and overarching performance attributes:
Chip Mounting Orientation:
FCBGA: Diverges from convention with a flip-chip design, where the semiconductor die is inverted and directly affixed to the substrate’s active side. This innovative orientation minimizes interconnect lengths, fostering heightened electrical performance.
PCB: Adheres to a standard face-up orientation for ICs, relying on wire bonding or similar methods for electrical connections.
Interconnection Modalities:
FCBGA: Showcases a sophisticated Ball Grid Array (BGA) configuration, orchestrating a grid pattern of solder balls beneath the package. This intricate layout not only ensures robust connections but also enables a compact and densely packed arrangement.
PCB: Embraces diverse interconnection methods, encompassing through-hole or surface-mount technologies, utilizing solder joints or pins to establish connections.
Thermal Dynamics:
FCBGA: Pioneers efficient heat dissipation by directly linking the IC’s active side to the substrate, particularly advantageous in applications prioritizing thermal considerations.
PCB: Navigates heat dissipation complexities through factors like layout intricacies, material selections, and the potential integration of supplementary heat sinks.
Size and Density:
FCBGA: Celebrated for its compact design, FCBGA carves a niche in applications defined by spatial constraints, boasting a high density of connections.
PCB: Projects versatility in size and complexity, accommodating diverse applications with varying spatial demands.
Performance Dynamics:
FCBGA: The distinctive features, including the flip-chip design and BGA configuration, contribute to heightened electrical performance, truncated interconnect lengths, and an amplified semblance of signal integrity.
PCB: Performance nuances in traditional PCBs are nuanced, shaped by factors such as trace layout intricacies, judicious material choices, and considerations for sustaining signal integrity.
Application Landscape:
FCBGA: Frequently enlisted in applications where spatial efficiency, high density, and optimized electrical and thermal performance take precedence, as seen in microprocessors and graphic processors.
PCB: Embodies adaptability, catering to a myriad of electronic devices and systems with diverse design requisites.
In essence, while both FCBGA Packaging Substrate and PCB are integral to electronic systems, FCBGA distinguishes itself with its avant-garde design choices, compact form factor, and a focus on optimized electrical and thermal performance—especially pertinent in applications where spatial efficiency and high performance are paramount. Traditional PCBs, in contrast, exemplify versatility, addressing a broad spectrum of applications with diverse design needs.
What is the Main Structure and Production Technology of FCBGA Packaging Substrate?
The FCBGA (Flip-Chip Ball Grid Array) packaging substrate boasts a sophisticated structure crafted through meticulous production processes. Let’s delve into the core components and manufacturing techniques that define its form:
Core Structure of FCBGA Packaging Substrate:
Substrate Material:
Primarily composed of organic materials like epoxy resins or polyimide, the substrate may also feature inorganic counterparts such as ceramics or glass for heightened thermal performance.
Layered Complexity:
Employing advanced sequential build-up (SBU) technology, FCBGA substrates often incorporate multiple layers. This three-dimensional structure allows intricate routing of traces, optimizing electrical pathways.
Conductive Pathways:
Copper or other conductive materials shape the intricate network of traces on the substrate. These paths serve as the essential conduits connecting various components within the FCBGA package.
Insulating Layers:
Dielectric materials provide insulation between conductive traces, influencing the substrate’s electrical characteristics.
Protective Solder Mask:
A solder mask layer shields and insulates the substrate, defining areas for solder connections and safeguarding the underlying elements.
Solder Balls Array:
Strategically positioned solder balls on the substrate’s underside form a precise grid. These solder balls serve as pivotal connection points linking the FCBGA package to the printed circuit board (PCB).
Via Structures:
Vias, whether through-hole or filled, create vertical connections between different substrate layers, ensuring seamless integration.
Pad Areas for Die Attachment:
Exposed metal pads provide direct attachment points for the flip-chip die, establishing crucial electrical connections.
Production Techniques:
Substrate Fabrication:
Employing methods like lamination, etching, and deposition, the substrate takes shape with multiple layers for structural complexity.
Formation of Copper Traces:
Precision techniques such as photolithography and etching are employed to form intricate copper traces, defining the conductive pathways.
Dielectric Layer Integration:
Application of dielectric layers ensures proper insulation and separation between conductive elements.
Solder Mask Application:
A meticulous process applies a solder mask layer, leaving apertures for solder connections while safeguarding the substrate.
Creation of Vias:
Vias, essential for vertical connections, are formed through drilling or laser ablation techniques.
Placement of Solder Balls:
Advanced equipment precisely places solder balls on the substrate’s underside, adhering to the defined grid pattern.
Flip-Chip Attachment:
The semiconductor die undergoes a flip-chip process, attaching directly to the substrate and establishing vital electrical connections.
Comprehensive Testing:
Rigorous testing protocols ensure the FCBGA package’s functionality, verifying electrical connections, reliability, and performance.
Encapsulation for Durability:
The entire package may undergo encapsulation with a protective molding compound, enhancing durability and providing mechanical support.
The production technology behind FCBGA packaging substrates represents a pinnacle of precision and sophistication. Through a synergy of material deposition, patterning techniques, and assembly processes, these substrates emerge with a meticulously crafted structure, ensuring reliability and optimal performance across diverse electronic applications.
Frequently Asked Questions (FAQs) about FCBGA Packaging Substrate
What does FCBGA stand for?
FCBGA stands for Flip-Chip Ball Grid Array, a type of packaging substrate used in electronic components.
How is FCBGA different from traditional packaging substrates?
FCBGA utilizes a flip-chip design where the semiconductor die is flipped and directly attached to the substrate. This differs from traditional packaging substrates where the die is typically mounted in a face-up orientation.
What is the main function of FCBGA packaging substrate?
The main function of FCBGA packaging substrate is to provide a platform for mounting and connecting the semiconductor die in electronic components. It facilitates electrical connections, heat dissipation, and integration into printed circuit boards (PCBs).
What materials are commonly used in FCBGA substrates?
FCBGA substrates are often made from organic materials like epoxy resins or polyimide. In some cases, inorganic materials such as ceramics or glass may be used for enhanced thermal performance.
How are connections made in FCBGA packaging substrate?
Connections in FCBGA are made through a Ball Grid Array (BGA) configuration. Solder balls are strategically placed beneath the package, forming a grid that serves as the interface for connecting to the printed circuit board (PCB).
What is the significance of the flip-chip design in FCBGA?
The flip-chip design in FCBGA involves attaching the active side of the semiconductor die directly to the substrate. This design reduces interconnect lengths, enhances electrical performance, and improves heat dissipation.
What role do solder balls play in FCBGA?
Solder balls in FCBGA serve as the connection points between the package and the PCB. They provide a reliable and compact interface for electrical connections.
Conclusion
In conclusion, FCBGA (Flip-Chip Ball Grid Array) packaging substrate stands as a transformative force in the domain of electronic components, showcasing innovation in design and functionality. The flip-chip paradigm, where the semiconductor die is inverted and directly attached to the substrate, distinguishes FCBGA from traditional packaging substrates. This design choice, coupled with a Ball Grid Array (BGA) configuration of solder balls, contributes to its compact form, high-density interconnects, and optimized electrical and thermal performance.
The main structure of FCBGA involves layers of substrate material, conductive traces, dielectric layers, solder masks, solder balls, via structures, and pad areas for die attachment. The production technology behind FCBGA is a symphony of sophisticated processes, including substrate manufacturing, copper trace formation, dielectric layer application, solder mask deposition, via formation, solder ball placement, flip-chip attachment, comprehensive testing, and encapsulation for durability.
Frequently Asked Questions (FAQs) shed light on common queries related to FCBGA, covering its significance, materials used, connection methods, applications, and reliability assurance.
In essence, FCBGA packaging substrate emerges as a pivotal player in electronic systems, particularly in applications demanding spatial efficiency, high density, and superior electrical and thermal performance. Its unique design and manufacturing intricacies position it as a crucial component driving advancements in the electronic industry.