What is FCBGA Package Substrate?
FCBGA Package Substrate,FCBGA Package Substrate (Fine-pitch Ball Grid Array) is an advanced packaging technology used for connecting and encapsulating integrated circuits. It employs a fine-pitch array of solder balls to connect the chip to the Printed Circuit Board (PCB), providing high-density signal transmission and power distribution. Typically comprising multiple layers of thin films, including insulating, metal, and conductor layers, FCBGA Package Substrate ensures reliable electrical connections and effective thermal management. Its compact design enables electronic devices to achieve higher component density and smaller form factors while maintaining performance and reliability.
FCBGA, or Flip-Chip Ball Grid Array, represents a pioneering advancement in the realm of integrated circuit (IC) packaging. Let’s explore the intricate layers and components that constitute this technology, unveiling the fundamental elements crucial for seamlessly integrating semiconductor advancements.
Innovative Flip-Chip Design: FCBGA distinguishes itself through the application of flip-chip technology. Departing from traditional methods that orient the semiconductor die in an upright position, FCBGA flips the chip, attaching it directly to the packaging substrate.
Precision in Ball Grid Array Formation: On the underside of the package, a meticulously arranged Ball Grid Array configuration takes shape. Solder balls are strategically placed in a grid pattern, forming critical contact points that establish a robust connection between the IC and the printed circuit board (PCB).
Central Role of the Package Substrate: At the heart of FCBGA lies the package substrate, providing essential support for the semiconductor die and facilitating efficient electrical connections. Crafted from high-performance materials, the substrate ensures optimal thermal and electrical properties.
Layered Complexity: The substrate unfolds as a complex, multi-layered structure, with each layer serving a specific purpose. Signal layers intricately route electrical connections, power and ground planes efficiently distribute energy, and additional layers contribute to advanced thermal management.
Diversity in Material Composition: FCBGA substrates boast a diverse material composition, spanning from organic substrates like FR-4 to advanced choices such as high-temperature laminates or ceramics. Material selection hinges on factors such as thermal efficiency, cost-effectiveness, and the specific requirements of the application.
Meticulous Routing and Interconnects: Within the substrate, a carefully designed network of traces facilitates the routing of electrical signals between the semiconductor die and the solder balls. Precision in this routing is paramount to ensuring optimal electrical performance and upholding signal integrity.
Strategic Thermal Management: Recognizing the importance of effective heat dissipation, FCBGA substrates often integrate features like thermal vias. These elements play a pivotal role in efficiently transferring heat away from the semiconductor die to the PCB.
In essence, FCBGA embodies the sophistication of IC packaging, establishing a robust foundation for electrical connections, thermal control, and structural integrity. With its innovative flip-chip approach and precise ball grid array configuration, FCBGA stands as the preferred choice across a diverse range of semiconductor applications.
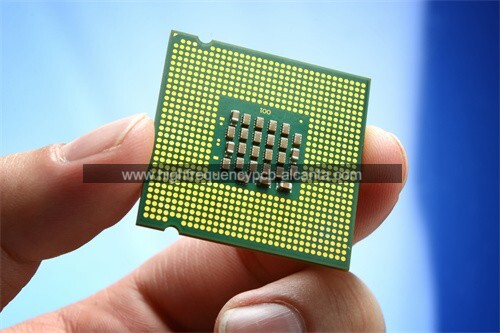
FCBGA Package Substrate
What Roles Does FCBGA Package Substrate Play?
The FCBGA (Flip-Chip Ball Grid Array) package substrate assumes a multifaceted role in the intricate world of integrated circuits, wielding its influence across various facets of packaging and functionality. Let’s dissect the diverse functions that the FCBGA package substrate fulfills, illuminating its integral contributions:
Foundational Guardian: Acting as a steadfast guardian, the package substrate provides a robust foundation for the delicate semiconductor die. Its structural support becomes paramount during critical stages such as handling, assembly, and the rigors of operational use.
Electrical Nexus: The substrate emerges as a pivotal nexus for electrical connections, seamlessly linking the semiconductor die to external components like the printed circuit board (PCB). Through a labyrinth of traces, it orchestrates the intricate dance of signals, ensuring smooth communication.
Temperature Maestro: Acknowledging the temperature sensitivity of integrated circuits, the substrate takes on the role of a maestro in thermal regulation. Features like thermal vias conduct a symphony of heat away from the semiconductor die, preserving optimal operating conditions.
Signal Choreographer: The substrate assumes the role of a meticulous choreographer, directing the flow of electrical signals within the integrated circuit. This precision is akin to orchestrating a symphony, safeguarding signal integrity and harmonizing overall performance.
Power Distribution Conductor: Within its layered structure, the substrate transforms into a conductor, efficiently directing the distribution of electrical power throughout the integrated circuit. This orchestrated power delivery is fundamental for the reliable performance of diverse semiconductor components.
Isolation Guardian: Layers within the substrate play the role of a guardian, providing dielectric isolation. This shield mitigates electrical interference, preserving the sanctity of individual signals and preventing undesirable cross-talk between different segments of the integrated circuit.
BGA Artisan: Positioned strategically on the substrate’s underbelly, the solder balls form an artful arrangement in the Ball Grid Array (BGA). These solder balls serve as adept artisans, creating secure connection points that underpin a robust electrical interface with the PCB.
Material Alchemist: The substrate’s material selection transforms it into an alchemist, blending and refining materials for optimal performance. From organic substrates like FR-4 to advanced alternatives, material choices are tailored to meet the specific demands of diverse applications.
In summation, the FCBGA package substrate emerges not just as a passive support structure but as an active participant, orchestrating a symphony of functions. Its intricate design and material nuances collectively elevate the reliability and performance of integrated circuits across a spectrum of applications.
What Are the Different Variants of FCBGA Package Substrate?
The FCBGA (Flip-Chip Ball Grid Array) package substrate manifests in a variety of renditions, each finely tuned to cater to distinct necessities and applications. Let’s explore the panorama of different variants:
Standard FR-4 Substrate:
Description: Crafted from the ubiquitous FR-4 material, an epoxy-based glass-reinforced laminate.
Application: Suited for applications where a balance of moderate electrical performance and thermal characteristics aligns with cost considerations.
High-Temperature Laminate Substrate:
Description: Leverages high-temperature laminates engineered to endure higher operational temperatures compared to the standard FR-4.
Application: Tailored for environments with demanding thermal prerequisites, such as realms in high-performance computing or automotive electronics.
Ceramic Substrate:
Description: Comprised of ceramics like alumina or aluminum nitride, boasting stellar thermal conductivity and reliability.
Application: Excelling in high-power applications that necessitate efficient heat dissipation, like power amplifiers or RF components.
Metal Core Substrate:
Description: Flaunts a metal core, often aluminum or copper, to amplify thermal conductivity and bolster heat dissipation.
Application: Ubiquitous in LED applications and other power electronics domains where adept heat management stands paramount.
Flexible Substrate:
Description: Harnesses flexible materials like polyimide, empowering the substrate to conform to non-planar surfaces.
Application: Tailor-made for scenarios with spatial constraints or those mandating flexibility, including wearable devices or flexible electronics.
Integrated Heat Spreader (IHS) Substrate:
Description: Integrates a heat spreader, typically forged from copper, intensifying thermal dissipation capabilities.
Application: Finds its niche in high-performance computing landscapes where effective cooling is of the essence.
Thin Substrate:
Description: Showcases a svelte profile, reducing the overall thickness of the package.
Application: Ideal for applications where spatial constraints dictate, such as in mobile devices or sleek electronic apparatuses.
Embedded Passive Components Substrate:
Description: Seamlessly embeds passive components directly into substrate layers, mitigating the need for standalone discrete components.
Application: Strives in applications where space economy and heightened electrical performance take precedence, as seen in RF and high-frequency designs.
Multilayer Substrate:
Description: Embraces multiple layers to amplify routing capabilities and elevate electrical performance.
Application: Frequently deployed in intricate ICs boasting a high pin count or in arenas where meticulous signal integrity is paramount, such as high-speed data communication.
Opting for the most fitting FCBGA substrate variant pivots on considerations like cost, thermal requisites, electrical performance, and the unique demands of the given application. Each variant unveils a bespoke solution tailored to navigate the diverse challenges inherent in electronic design landscapes.
How Does FCBGA Package Substrate Interact with IC Packaging?
The synergy between the FCBGA (Flip-Chip Ball Grid Array) package substrate and IC (Integrated Circuit) packaging is a dynamic interplay that profoundly shapes various facets of the packaging process and performance. Let’s delve into the nuanced interactions:
Harmony of Flip-Chip Integration:
Description: FCBGA employs flip-chip technology, inverting the semiconductor die to expose its active side, featuring electrical connections.
Interaction: The substrate acts as a steadfast support, facilitating the seamless integration of the flip-chip configuration and ensuring the secure connection of the chip’s solder bumps to the substrate.
Electrical Ballet:
Description: Within the substrate lies a intricate dance of traces, intricately routing electrical signals between the semiconductor die and the external environment, typically the PCB.
Interaction: The substrate emerges as the stage for this ballet, serving as the conduit for efficient and reliable transmission of signals, thereby fostering seamless electrical connectivity.
BGA Choreography:
Description: Solder balls, meticulously arranged in a grid on the substrate’s underside, compose the Ball Grid Array (BGA).
Interaction: This BGA choreography orchestrates a symphony of secure electrical connections and robust mechanical support during the assembly process, establishing a cohesive interface between the IC and the PCB.
Thermal Maestro:
Description: The substrate’s design is engineered to master the art of thermal management, efficiently handling the heat generated by the operational semiconductor die.
Interaction: Features like thermal vias and dedicated thermal layers conduct a ballet of heat dissipation, ensuring the IC operates harmoniously within specified temperature thresholds.
Dielectric Ballet:
Description: Layers within the substrate perform a ballet of dielectric isolation, mitigating electrical interference between different segments of the integrated circuit.
Interaction: This dance of dielectric isolation preserves signal integrity, minimizing crosstalk and interference, thus elevating the overall performance of the IC.
Architectural Support:
Description: Beyond its electrical prowess, the substrate extends structural support to the semiconductor die, shielding it from physical stresses and external factors.
Interaction: This architectural support is a silent guardian throughout the IC’s lifecycle, contributing to its robustness and reliability.
Material Symphony:
Description: The substrate’s material composition, whether it be FR-4, high-temperature laminates, ceramics, or a metal core, influences the IC’s electrical, thermal, and mechanical characteristics.
Interaction: Material selection orchestrates a symphony of properties, directly impacting the IC’s suitability and performance for specific applications.
Innovative Flourishes:
Description: Some FCBGA substrates boast innovative features, such as embedded passive components or integrated heat spreaders.
Interaction: These creative flourishes enhance the IC’s functionality, introducing capabilities like improved electrical performance, compact form factors, or enhanced thermal dissipation.
In essence, the FCBGA package substrate is not just a passive participant but a choreographer, orchestrating a multidimensional performance that shapes the functionality, reliability, and adaptability of the integrated circuit within a diverse array of applications.
What Sets FCBGA Package Substrate Apart from PCB?
The FCBGA (Flip-Chip Ball Grid Array) package substrate and a conventional PCB (Printed Circuit Board) stand apart in their roles and characteristics within the landscape of electronic components. Distinctive features differentiate the FCBGA substrate, tailored for flip-chip integrated circuits, from the broader functionality of a standard PCB:
Specialized Integration Dynamics:
FCBGA Substrate: Purposefully crafted for the integration of semiconductor dies using flip-chip technology, facilitating direct electrical connections through solder bumps.
PCB: Primarily functions as a universal support structure for various electronic components, employing conventional mounting methods like wire bonding.
Distinctive Flip-Chip Configuration:
FCBGA Substrate: Embraces the flip-chip configuration, positioning the active side of the semiconductor die toward the substrate for direct electrical connections.
PCB: Adheres to conventional mounting practices, with the active side of the semiconductor die facing away from the PCB surface.
Emphasis on Ball Grid Array (BGA):
FCBGA Substrate: Showcases a dedicated BGA configuration on its underside, featuring solder balls arranged in a grid pattern as the primary connection points to the external PCB.
PCB: May incorporate Ball Grid Arrays for certain components but doesn’t center its design around the comprehensive BGA configuration seen in the FCBGA substrate.
Tailored Thermal Management:
FCBGA Substrate: Engineered with specific thermal management features, such as thermal vias or additional layers, strategically addressing the heat dissipation requirements unique to flip-chip technology.
PCB: While incorporating general cooling features like thermal vias, the focus is dispersed across the board and isn’t as specialized for managing heat from a specific semiconductor die.
Material Composition Considerations:
FCBGA Substrate: Material selection is finely tuned to meet the specific demands of semiconductor packaging, accounting for factors such as thermal conductivity, electrical properties, and compatibility with flip-chip configurations.
PCB: Material considerations encompass a broader spectrum, factoring in mechanical strength, dielectric properties, and cost-effectiveness for the comprehensive needs of electronic assemblies.
Role in IC Packaging:
FCBGA Substrate: Plays a critical role in the packaging of flip-chip integrated circuits, providing a dedicated platform for support, electrical connectivity, and thermal regulation.
PCB: Assumes a versatile role as a central platform for mounting and interconnecting various electronic components within a broader electronic system.
Size and Specialization:
FCBGA Substrate: Typically smaller and more specialized, tailored to accommodate a specific semiconductor die with a flip-chip configuration.
PCB: Exhibits greater size variability, accommodating diverse components and serving as a comprehensive platform for electronic systems of varying complexities.
In essence, the FCBGA package substrate stands as a specialized and finely tuned component, purpose-built for the intricacies of flip-chip integrated circuits. In contrast, a PCB offers a more universal platform, addressing the broader requirements of electronic assemblies across different configurations.
Can We Unravel the Structures and Production Technologies of FCBGA Package Substrate?
Let’s unravel the intricacies of FCBGA (Flip-Chip Ball Grid Array) package substrate structures and explore the technologies employed in its production:
Structures of FCBGA Package Substrate:
Foundational Material:
Overview: The substrate begins with a foundational material, often a laminate or specialized material such as high-temperature laminates, ceramics, or metal core, selected based on the specific application requirements.
Layered Dielectrics:
Overview: Multiple dielectric layers are meticulously stacked on the foundational material, forming the substrate’s core structure. These layers provide electrical insulation and contribute to the substrate’s overall structural resilience.
Intricate Signal Pathways:
Overview: Woven within the dielectric layers are intricate patterns of signal traces, serving as the conduit for electrical signals between the semiconductor die and external components.
Thermal Management Solutions:
Overview: To address thermal challenges, the substrate may incorporate features like thermal vias, additional copper layers, or integrated heat spreaders. These elements play a crucial role in efficiently dissipating heat generated by the semiconductor die.
Protective Solder Mask:
Overview: A solder mask layer envelops the substrate’s surface, offering insulation and protection. It delineates areas where solder connections will be established and safeguards the substrate during subsequent processes.
Ball Grid Array (BGA) Configuration:
Overview: On the substrate’s underside, a meticulously arranged grid pattern of solder balls forms the BGA configuration. This configuration acts as the interface, establishing connections between the FCBGA and the external printed circuit board (PCB) or other components.
Strategic Pad Areas:
Overview: The substrate features pad areas strategically positioned to align with solder bumps on the semiconductor die. These pads facilitate precise placement during the flip-chip bonding process.
Production Technologies of FCBGA Package Substrate:
Precision Lamination:
Overview: The base material and dielectric layers undergo precision lamination processes. Layers are intricately pressed together and cured, yielding a unified substrate structure.
Copper Deposition Techniques:
Overview: Copper layers, encompassing signal traces and additional thermal layers, are deposited onto the substrate using methods such as sputtering or electroplating.
Photoengraving Mastery:
Overview: The creation of intricate patterns, including signal traces, involves photoengraving or photolithography. Photoresist application, exposure through a mask, and subsequent development define the desired patterns.
Strategic Drilling:
Overview: Precision drilling is employed to create holes for thermal vias or other purposes. These holes are vital for facilitating heat flow or establishing pathways for through-hole connections.
Solder Ball Attachment Precision:
Overview: Solder balls are meticulously attached to the substrate using solder paste or other bonding methods. Precise placement and uniformity are paramount for the subsequent flip-chip bonding process.
Solder Mask Application Expertise:
Overview: A solder mask is expertly applied to cover areas not requiring solder connections, ensuring insulation and protection during subsequent manufacturing steps.
Flip-Chip Bonding Artistry:
Overview: The pinnacle of the process involves the flip-chip bonding phase. The semiconductor die, flipped and aligned with precision, establishes contact between its solder bumps and the corresponding pads on the substrate. This assembly undergoes reflow soldering or a similar bonding technique.
Thorough Quality Control and Testing:
Overview: Post-production, the FCBGA package substrate undergoes meticulous quality control and testing procedures. These measures are implemented to verify adherence to specifications for electrical performance, thermal characteristics, and overall reliability.
In essence, the synthesis of these structures and production technologies results in a sophisticated FCBGA package substrate, a linchpin in providing a robust foundation for integrating flip-chip integrated circuits across diverse electronic applications.
FAQs About FCBGA Package Substrates
What are the key components of an FCBGA package substrate?
The main components include the base material, dielectric layers, signal traces, thermal management features, solder mask, ball grid array (BGA) configuration, and pad areas for flip-chip bonding.
How is the quality of FCBGA package substrates ensured?
Quality control measures involve thorough testing for electrical performance, thermal characteristics, and overall reliability. The substrates undergo stringent checks to meet specified standards and ensure they can withstand the demands of various electronic applications.
Can FCBGA package substrates accommodate different semiconductor die sizes?
Yes, FCBGA package substrates can be designed to accommodate various semiconductor die sizes. The pad areas on the substrate are strategically arranged to align with the solder bumps on the specific semiconductor die intended for use.
What factors should be considered when selecting an FCBGA substrate for a specific application?
Factors to consider include cost, thermal requirements, electrical performance, and the unique demands of the application. The choice of substrate material, thermal management features, and additional functionalities like embedded components should align with the specific needs of the electronic design.
What Materials are Typically Used in FCBGA Package Substrates?
FCBGA substrates can be fashioned from diverse materials, ranging from FR-4 for standard applications to high-temperature laminates for scenarios with rigorous thermal demands, ceramics for high-power applications, and metal core for improved thermal conductivity.
Which Applications Are Well-Suited for FCBGA Technology?
FCBGA technology finds application in various domains, such as high-performance computing, automotive electronics, power amplifiers, RF components, LED applications, and other scenarios where efficient heat dissipation, compact form factors, and heightened electrical performance are critical.
In Conclusion
In summary, the FCBGA (Flip-Chip Ball Grid Array) package substrate emerges as a sophisticated and adaptable technology within the domain of integrated circuit packaging. Its unique flip-chip configuration, establishing direct connections between the semiconductor die and substrate, coupled with specialized thermal management features, distinguishes FCBGA from conventional packaging methodologies.
The intricate composition of an FCBGA package substrate, encompassing elements like the base material, dielectric layers, signal traces, thermal solutions, solder mask, and ball grid array, collaboratively constructs a resilient foundation for seamless semiconductor integration. Its applicability spans a broad spectrum, extending from high-performance computing to automotive electronics, where the imperative for efficient heat dissipation, compact form factors, and heightened electrical performance takes precedence.
The production methodologies involved in shaping FCBGA substrates, employing precision lamination, copper deposition, photoengraving, and flip-chip bonding, underscore a meticulous and forward-looking approach. Rigorous quality control measures underscore the commitment to meeting stringent standards in electrical performance, thermal dynamics, and overall reliability.
In essence, FCBGA package substrates stand as pivotal facilitators in propelling the advancement of electronic systems, offering a fusion of streamlined design, effective thermal regulation, and elevated electrical connectivity. The ongoing evolution of FCBGA technology remains at the forefront of integrated circuit packaging, continually addressing the diverse and evolving requisites of contemporary electronic applications.