FC-CSP Substrates Manufacturer
FC-CSP Substrates Manufacturer,FC-CSP Substrates (Flip Chip Chip Scale Package) are integral to semiconductor packaging, combining flip chip and chip scale technologies. These substrates enable direct chip-to-board connections, enhancing electrical performance and miniaturization. Comprising multiple layers including insulating, metal, and conductor layers, FC-CSP Substrates ensure reliable connections and efficient heat dissipation. They are crucial for compact electronic devices, such as smartphones and wearables, optimizing space utilization while maintaining reliability. FC-CSP Substrates drive advancements in semiconductor packaging, offering high performance and compactness in various consumer electronics and industrial applications, where space-saving and performance are paramount.
FC-CSP, Flip Chip Chip Scale Package, represents a cutting-edge approach to chip packaging, particularly favored in high-performance and densely integrated circuits. This innovative method involves flipping the chip and directly attaching it to the packaging substrate, bypassing traditional wire bonding. Widely employed in processors, graphics chips, and other sophisticated integrated circuits, FC-CSP offers a compact vertical footprint, allowing for enhanced component integration even in constrained spaces. Substrates for FC-CSP are typically composed of organic or ceramic materials, prized for their excellent thermal conductivity and mechanical robustness, crucial for effective chip cooling and stability. By embracing FC-CSP packaging technology, electronics manufacturers can develop sleeker, lighter, and more powerful product designs, meeting the growing demand for portable gadgets and high-performance computing solutions.
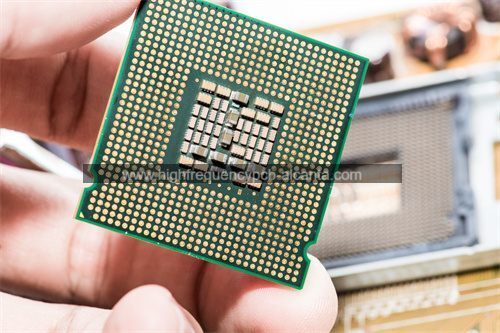
FC-CSP Substrates Manufacturer
What are the functions of FC-CSP Substrate?
The FC-CSP (Flip Chip Chip Scale Package) substrate stands as an indispensable component in electronic packaging, executing several pivotal functions:
Structural Fortification: Acting as a solid base, the substrate ensures the chip’s steadfastness and shields it from physical harm during handling and operation.
Electrical Bridging: Serving as a conduit, the substrate facilitates seamless electrical connections between the chip and external components, facilitating efficient signal transmission and smooth integration into the electronic system.
Heat Dissipation: Leveraging materials with high thermal conductivity, the substrate efficiently disperses the heat generated by the chip during operation, preserving optimal temperatures and bolstering long-term reliability.
Signal Preservation: By upholding the integrity of electrical signals, the substrate curtails signal distortion and interference, ensuring dependable communication between the chip and external circuitry.
Mechanical Reinforcement: Offering robust mechanical support, the substrate forestalls excessive stress or deformation on the chip, safeguarding its operational functionality and extending its lifespan.
In essence, the FC-CSP substrate plays a pivotal role in electronic packaging, underpinning the stability, functionality, and endurance of integrated circuit chips across a diverse array of electronic applications.
What are the different types of FC-CSP Substrates?
A variety of FC-CSP (Flip Chip Chip Scale Package) substrates are available, each meticulously designed to cater to specific requirements and applications:
Organic substrates, made from materials such as epoxy resin or polyimide, are highly valued for their lightweight design, affordability, and effective electrical insulation. They are extensively utilized in consumer electronics and mobile gadgets due to these advantageous properties.
Ceramic substrates, made from materials like alumina (Al2O3) or aluminum nitride (AlN), boast exceptional thermal conductivity and mechanical stability. They are highly favored for rigorous applications such as automotive electronics and power modules.
Flexible substrates are highly esteemed for their capacity to adapt to non-planar surfaces, making them well-suited for scenarios necessitating flexibility during operation or in environments constrained by space. Widely utilized in wearable technology and medical devices, these substrates offer versatility and resilience in various applications.
Silicon substrates boast remarkable thermal conductivity, making them ideal for seamless integration with silicon-based semiconductor devices. They play a pivotal role in high-performance computing and telecommunications equipment.
Glass Substrates: Recognized for their outstanding dimensional stability and electrical insulation properties, glass substrates are favored for high-frequency applications such as RF devices and mmWave antennas.
These diverse FC-CSP substrate options offer tailored solutions to meet a wide array of electronic device and system requirements, effectively addressing varied industry needs and specifications
What is the relationship between FC-CSP Substrate and IC packaging?
The relationship between FC-CSP substrates and IC packaging is tightly intertwined. FC-CSP substrates serve as a pivotal element within integrated circuit (IC) packaging, facilitating the mounting and connection of IC chips. Specifically engineered for flip chip bonding, these substrates enable IC chips to be directly affixed onto them with their active surfaces facing downward.
FC-CSP substrates play a crucial role in enhancing the performance, reliability, and size efficiency of IC packaging. They provide a compact and efficient platform for IC chip mounting, promoting high-density interconnections and enabling rapid signal transmission with minimal loss. Additionally, these substrates aid in effective thermal management by dissipating heat away from the IC chips, thereby ensuring their optimal functionality and durability.
In essence, FC-CSP substrates are essential components in modern IC packaging technology, enabling the development of compact, high-performance electronic devices across various industries, including mobile communication, automotive electronics, and advanced computing.
How does FC-CSP Substrate differ from traditional PCBs?
FC-CSP substrates and traditional PCBs vary significantly across several dimensions:
Physical Size and Configuration: FC-CSP substrates are notably smaller and more compact compared to traditional PCBs, reflecting their specialized role in integrated circuit (IC) packaging. They are meticulously crafted to meet stringent space constraints while optimizing performance.
Mounting Methodology: FC-CSP substrates employ flip chip bonding as the primary means of affixing IC chips. Conversely, traditional PCBs commonly utilize surface-mount or through-hole techniques for component attachment.
Interconnection Approach: FC-CSP substrates leverage flip chip technology to establish dense, direct connections between IC chips, resulting in shorter signal paths. In contrast, traditional PCBs often rely on wire bonding or soldering for component interconnection, which may entail longer signal routes.
Thermal Regulation: FC-CSP substrates are purposefully engineered to efficiently dissipate heat generated by IC chips, typically integrating advanced thermal management features like metal core or ceramic substrates. While traditional PCBs may incorporate heat dissipation methods such as heat sinks or thermal vias, they generally lack the same level of thermal optimization.
Application Emphasis: FC-CSP substrates are predominantly employed in high-performance applications where space efficiency, speed, and thermal considerations are critical, including mobile devices, high-speed communication systems, and advanced computing. In contrast, traditional PCBs are more versatile and find widespread use across various electronic devices, spanning consumer electronics, industrial machinery, and automotive electronics.
In essence, FC-CSP substrates are specialized platforms tailored specifically for demanding IC packaging requirements, offering distinct advantages over traditional PCBs in terms of compactness, performance, and thermal management capabilities.
What is the structure and manufacturing technology of FC-CSP Substrate?
The structure and production methods of FC-CSP substrates are characterized by their intricate design and specialized manufacturing processes:
Structure:
FC-CSP substrates typically comprise multiple layers of materials, including a base layer (often composed of a dielectric material like FR-4 or a more thermally conductive material such as copper or ceramic), intermediate layers for routing electrical connections, and a top layer for mounting the IC chips. These substrates are engineered to accommodate flip chip bonding, featuring solder balls or bumps arranged on the surface for direct connections with the IC chips.
Manufacturing Process:
The manufacturing of FC-CSP substrates involves several key stages:
Substrate Fabrication: The base layer material is prepared and processed to form the substrate’s foundation. This may entail cutting, drilling, and laminating to achieve the desired dimensions and layering.
Circuit Formation: Thin layers of conductive material, such as copper, are applied to the substrate to create circuit patterns and interconnections. This is typically accomplished through techniques like photolithography and etching.
Via Creation: Vias, small holes drilled or etched through the substrate layers, are established to facilitate connections between different circuit layers. This process may utilize methods like laser drilling or chemical etching.
Surface Treatment: The substrate surface undergoes treatments such as solder mask application and surface planarization to ensure a smooth, uniform surface for IC chip mounting.
Solder Ball/Bump Placement: Solder balls or bumps are precisely deposited onto the substrate surface, often using techniques like solder paste printing or specialized attachment equipment. These solder connections serve to bond the IC chips to the substrate.
Testing and Inspection: Finished FC-CSP substrates undergo thorough testing and inspection to verify quality and reliability. This involves electrical testing, visual examination, and other quality assurance measures.
In summary, the production of FC-CSP substrates entails a combination of precision machining, material deposition, patterning, and assembly processes to create substrates that meet the exacting standards of modern IC packaging requirements.
Conclusion
In conclusion, FC-CSP substrates stand out as crucial components in modern integrated circuit (IC) packaging, offering advantages in size efficiency, performance, and thermal management. Compared to traditional PCBs, FC-CSP substrates are smaller, employ flip chip bonding for IC chip attachment, feature dense interconnections, and are optimized for effective heat dissipation. Their structure involves multiple layers of materials and specialized manufacturing processes including substrate fabrication, circuit formation, via creation, surface treatment, solder ball/bump placement, and rigorous testing. Through these processes, FC-CSP substrates are meticulously crafted to meet the demanding requirements of high-performance electronic devices across various industries.