Extra Small Pitch PCB Manufacturing
Extra Small Pitch PCB Manufacturing,Extra Small Pitch PCBs are printed circuit boards characterized by their exceptionally narrow spacing between adjacent electrical components or solder points. These PCBs are designed to accommodate miniaturized electronic devices where space is at a premium. With pitch sizes ranging from as small as 0.2mm or even less, they enable the integration of intricate circuitry into compact assemblies, facilitating the development of smaller, lighter, and more portable electronics. Extra Small Pitch PCBs demand precise manufacturing techniques to ensure accurate alignment and soldering of components, making them suitable for high-density applications in industries such as consumer electronics, wearables, and medical devices.
What is an Extra Small Pitch PCB?
Professional Extra small pitch PCB manufacturing. high frequency packaging substrates with ultra-small trace width and pitch, we produce high quality substrates (PCB) from 2 to 50 layers.
An Extra Small Pitch PCB refers to a printed circuit board (PCB) with very tight or narrow spacing between the electrical contacts or pads. “Pitch” in this context refers to the distance between the centers of adjacent contacts or pads on the PCB.
Typically, PCBs have standard pitch sizes, such as 0.1 inches (2.54 mm) or 0.05 inches (1.27 mm). However, in certain applications where space is limited or where high-density interconnection is required, extra small pitch PCBs are used. These PCBs have smaller distances between the pads, allowing for more compact designs and higher component density.
Extra small pitch PCBs are commonly used in various electronic devices, including smartphones, tablets, wearables, and other miniaturized electronic gadgets where space optimization is critical. They often require specialized manufacturing techniques and assembly processes to ensure accurate placement of components and reliable electrical connections despite the reduced spacing.
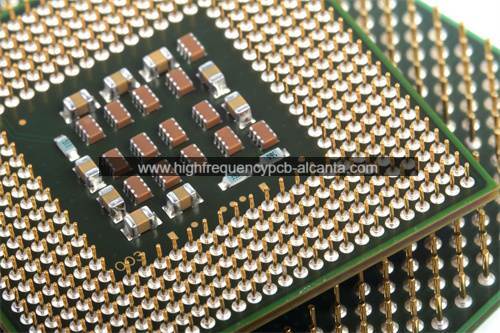
Extra Small Pitch PCB Manufacturing
What are the Design Guidelines for Extra Small Pitch PCBs?
Designing PCBs with extra small pitch requires careful consideration and adherence to specific guidelines to ensure successful manufacturing and reliable performance. Here are some design guidelines for extra small pitch PCBs:
- Minimum Trace and Space Width: Ensure that the traces and spaces on the PCB are designed to meet the minimum width requirements specified by your PCB manufacturer. These widths are often smaller than those used for standard pitch PCBs due to the tighter spacing.
- Via Design: Use smaller vias with appropriate aspect ratios to accommodate the smaller pitch. Ensure that the vias are properly placed to avoid routing conflicts and impedance issues.
- Pad and Land Design: Design pads and lands with appropriate dimensions to accommodate the smaller pitch while still providing sufficient solder fillet and electrical contact area. Pay attention to pad shapes (round, rectangular, etc.) to optimize soldering and reduce the risk of solder bridging.
- Component Placement: Optimize component placement to maximize space utilization while maintaining adequate clearance between components. Consider the orientation of components and their corresponding pads to facilitate routing and soldering.
- Routing Considerations: Plan routing carefully to avoid signal integrity issues, such as crosstalk and impedance mismatches. Use controlled impedance traces for high-speed signals and ensure proper signal integrity simulation.
- Layer Stackup: Choose an appropriate layer stackup to accommodate the routing requirements of the PCB while minimizing signal degradation and interference. Consider using microvia technology for HDI (High-Density Interconnect) PCBs to further reduce trace lengths and increase routing density.
- Manufacturability: Collaborate closely with your PCB manufacturer to ensure that the design is manufacturable with the chosen fabrication processes. Consider factors such as solder mask registration, copper plating thickness, and manufacturing tolerances.
- Testing and Inspection: Develop testing and inspection procedures tailored to the specific challenges posed by extra small pitch PCBs. Use automated optical inspection (AOI) and X-ray inspection to detect defects and ensure quality control.
- Thermal Management: Pay attention to thermal management considerations, especially in densely populated areas of the PCB. Ensure adequate spacing between components to facilitate heat dissipation and prevent overheating.
- Documentation: Maintain comprehensive documentation of the PCB design, including detailed specifications, layer stackup, component placement, and routing guidelines. This documentation is essential for collaboration with manufacturers and troubleshooting any issues that may arise during fabrication or assembly.
By following these design guidelines, you can increase the likelihood of success when designing extra small pitch PCBs, minimizing the risk of manufacturing defects and ensuring reliable performance in the final product.
What is the Extra Small Pitch PCB Fabrication Process?
The fabrication process for Extra Small Pitch PCBs (printed circuit boards) is similar to that of standard PCBs but requires more precision due to the tighter spacing between components and traces. Here’s an overview of the fabrication process for Extra Small Pitch PCBs:
- Design: The process starts with the PCB design using specialized PCB design software. Designers must pay close attention to component placement, trace routing, and spacing to accommodate the extra small pitch requirements.
- Preparation of Gerber Files: Once the design is complete, the PCB layout is converted into Gerber files, which contain all the necessary information for the fabrication process, including copper traces, solder mask, silkscreen, and drill holes.
- Material Selection: High-quality laminate materials are selected based on the specific requirements of the PCB, including factors such as dielectric constant, thermal properties, and signal integrity considerations.
- Panelization: Multiple PCB designs are often combined into a single panel to optimize manufacturing efficiency. Panelization involves arranging individual PCB designs within a larger panel, taking into account factors such as board size, orientation, and fiducial markings.
- Inner Layer Processing: For multilayer PCBs, inner layers are fabricated first. This involves laminating copper foil onto both sides of the substrate material, then etching away excess copper to create the desired traces and interconnections.
- Drilling: Precision drilling machines are used to create holes for through-hole components and vias. Extra care must be taken to ensure that the drill holes are accurately positioned and aligned with the corresponding pads and traces.
- Through-Hole Plating: After drilling, the holes are plated with metal (typically copper) to provide electrical conductivity between layers. This process, known as through-hole plating, ensures reliable electrical connections throughout the PCB.
- Outer Layer Processing: The outer layers of the PCB are processed similarly to the inner layers, with copper foil laminated onto the substrate and then etched to create the desired traces and features.
- Solder Mask Application: A solder mask is applied to the surface of the PCB to protect the copper traces from oxidation and to provide insulation between conductive elements. The solder mask is selectively applied to expose areas where soldering is required.
- Silkscreen Printing: Identifying information, such as component labels, logos, and reference designators, is printed onto the PCB surface using a silkscreen printing process. This information helps assembly technicians identify components and ensure correct placement during assembly.
- Surface Finish: The PCB surface is finished with a coating or plating to improve solderability and protect against corrosion. Common surface finishes for Extra Small Pitch PCBs include HASL (hot air solder leveling), ENIG (electroless nickel immersion gold), and OSP (organic solderability preservative).
- Quality Control: Throughout the fabrication process, rigorous quality control measures are implemented to ensure that the finished PCBs meet the specified design requirements. This may include visual inspection, electrical testing, and dimensional verification.
- Separation: After fabrication is complete, the individual PCBs are separated from the panel using mechanical or laser cutting methods.
- Packaging and Shipping: The finished PCBs are packaged according to customer specifications and shipped to the assembly facility for component placement and soldering.
By following these steps and paying close attention to detail, manufacturers can produce Extra Small Pitch PCBs with the precision and reliability required for modern electronic devices.
How do you Manufacture an Extra Small Pitch PCB?
Manufacturing an Extra Small Pitch PCB (printed circuit board) requires specialized equipment and processes to achieve the tight spacing and high component density required. Here’s an overview of the manufacturing process for Extra Small Pitch PCBs:
- Design Preparation: The process begins with the PCB design, where designers use specialized PCB design software to create layouts optimized for extra small pitch components. Designers must pay close attention to component placement, trace routing, and spacing to accommodate the tight pitch requirements.
- Material Selection: High-quality laminate materials are selected based on the specific requirements of the PCB, including factors such as dielectric constant, thermal properties, and signal integrity considerations. The choice of materials plays a crucial role in achieving the desired electrical performance and reliability.
- Panelization: Multiple PCB designs are often combined into a single panel to optimize manufacturing efficiency. Panelization involves arranging individual PCB designs within a larger panel, taking into account factors such as board size, orientation, and fiducial markings.
- Photoresist Application: A layer of photoresist material is applied to the surface of the copper-clad laminate. The photoresist acts as a protective layer during the subsequent etching process and allows for the transfer of the PCB design onto the copper surface.
- Exposure and Development: The panel is exposed to ultraviolet (UV) light through a photomask that contains the PCB design. The UV light cures the photoresist in areas not covered by the design, while the exposed areas remain uncured. The panel is then developed to remove the uncured photoresist, leaving behind the desired pattern for the copper traces.
- Etching: The panel is immersed in an etchant solution, typically containing chemicals such as ferric chloride or ammonium persulfate, which selectively removes the exposed copper from the panel. The etching process creates the desired traces and interconnections on the PCB, with the remaining photoresist acting as a mask to protect the areas where traces are needed.
- Drilling: Precision drilling machines are used to create holes for through-hole components and vias. Extra care must be taken to ensure that the drill holes are accurately positioned and aligned with the corresponding pads and traces.
- Through-Hole Plating: After drilling, the holes are plated with metal (typically copper) to provide electrical conductivity between layers. This process, known as through-hole plating, ensures reliable electrical connections throughout the PCB.
- Outer Layer Processing: The outer layers of the PCB are processed similarly to the inner layers, with copper foil laminated onto the substrate and then etched to create the desired traces and features.
- Solder Mask Application: A solder mask is applied to the surface of the PCB to protect the copper traces from oxidation and to provide insulation between conductive elements. The solder mask is selectively applied to expose areas where soldering is required.
- Silkscreen Printing: Identifying information, such as component labels, logos, and reference designators, is printed onto the PCB surface using a silkscreen printing process. This information helps assembly technicians identify components and ensure correct placement during assembly.
- Surface Finish: The PCB surface is finished with a coating or plating to improve solderability and protect against corrosion. Common surface finishes for Extra Small Pitch PCBs include HASL (hot air solder leveling), ENIG (electroless nickel immersion gold), and OSP (organic solderability preservative).
- Quality Control: Throughout the manufacturing process, rigorous quality control measures are implemented to ensure that the finished PCBs meet the specified design requirements. This may include visual inspection, electrical testing, and dimensional verification.
- Separation: After manufacturing is complete, the individual PCBs are separated from the panel using mechanical or laser cutting methods.
- Packaging and Shipping: The finished PCBs are packaged according to customer specifications and shipped to the assembly facility for component placement and soldering.
By following these steps and utilizing specialized equipment and processes, manufacturers can produce Extra Small Pitch PCBs with the precision and reliability required for modern electronic devices.
How much should an Extra Small Pitch PCB cost?
The cost of an Extra Small Pitch PCB (printed circuit board) can vary widely depending on several factors, including the complexity of the design, the number of layers, the size of the PCB, the materials used, the manufacturing processes required, and the quantity ordered. Here are some key factors that influence the cost:
- Complexity of Design: PCBs with extra small pitch often involve more intricate designs with tighter tolerances, which can increase manufacturing costs.
- Number of Layers: Extra Small Pitch PCBs can be single-sided, double-sided, or multilayered. Multilayer PCBs typically cost more due to the additional manufacturing steps and materials required.
- Size of the PCB: Larger PCBs generally cost more to manufacture than smaller ones due to the increased material and production time.
- Materials Used: The choice of laminate materials, copper thickness, surface finish, and other materials can impact the overall cost of the PCB.
- Manufacturing Processes: Specialized manufacturing processes, such as laser drilling, microvia technology, and HDI (High-Density Interconnect) techniques, may be required for Extra Small Pitch PCBs, adding to the cost.
- Quantity Ordered: Economies of scale typically apply, meaning that larger quantities of PCBs ordered will result in lower unit costs. However, prototype or low-volume orders may incur higher per-unit costs.
- Turnaround Time: Expedited or quick-turn PCB fabrication services may involve additional fees, whereas standard lead times may offer lower costs.
It’s essential to request quotes from multiple PCB manufacturers and compare their pricing, capabilities, and lead times to find the best option for your specific requirements. Additionally, consider factors such as quality, reliability, and customer service when selecting a PCB manufacturer.
What is the Base Material for Extra Small Pitch PCBs?
The base material for Extra Small Pitch PCBs (printed circuit boards) is typically a high-quality laminate composed of layers of substrate and copper foil. The choice of base material is critical as it directly affects the performance, reliability, and manufacturability of the PCB. Some common base materials used for Extra Small Pitch PCBs include:
- FR-4: FR-4 (Flame Retardant 4) is the most commonly used substrate material for PCBs due to its excellent electrical properties, mechanical strength, and cost-effectiveness. It consists of woven fiberglass cloth impregnated with epoxy resin and clad with copper foil on both sides. FR-4 is suitable for a wide range of applications, including Extra Small Pitch PCBs.
- High-Frequency Laminates: For Extra Small Pitch PCBs operating at high frequencies, such as RF (radio frequency) and microwave applications, specialized high-frequency laminates are used. These laminates offer low dielectric constant (Dk) and low loss tangent (Df) to minimize signal attenuation and maintain signal integrity.
- Rogers and Taconic Laminates: Brands like Rogers Corporation and Taconic offer a range of high-performance laminates specifically designed for high-frequency applications. These laminates provide superior electrical properties, thermal stability, and dimensional accuracy required for Extra Small Pitch PCBs in demanding RF and microwave environments.
- Polyimide (PI): Polyimide is a flexible substrate material suitable for applications requiring bendability or high-temperature resistance. It is often used in Extra Small Pitch PCBs for flexible circuits or applications where space constraints or thermal considerations are critical.
- Metal Core (MCPCB): Metal Core PCBs feature a metal core, typically aluminum or copper, sandwiched between layers of substrate material. They offer enhanced thermal conductivity, making them suitable for applications requiring efficient heat dissipation, such as LED lighting and power electronics.
- Specialized Dielectric Materials: Depending on the specific requirements of the Extra Small Pitch PCB, other specialized dielectric materials may be used, such as ceramic-filled PTFE (polytetrafluoroethylene) or liquid crystal polymer (LCP), to achieve desired electrical performance and reliability.
When selecting the base material for Extra Small Pitch PCBs, designers must consider factors such as electrical properties, thermal characteristics, mechanical strength, dimensional stability, cost, and compatibility with the manufacturing processes involved. Collaborating with a trusted PCB manufacturer can help ensure the selection of the most suitable base material for the intended application.
Which company makes Extra Small Pitch PCBs?
Manufacturing Extra Small Pitch PCBs is typically undertaken by specialized PCB manufacturing companies. These companies possess advanced technology and equipment, as well as experienced engineers and technical teams, capable of meeting customers’ demands for high-precision, high-density PCBs. Some of these companies may specialize specifically in producing Extra Small Pitch PCBs, having expertise and experience in this area.
As a specialized PCB manufacturing company, our company is capable of producing various types of PCBs, including Extra Small Pitch PCBs. We have advanced production equipment and a skilled technical team capable of meeting customers’ demands for high-precision, high-density PCBs. Our engineers and technical staff undergo professional training and possess rich experience and skills, enabling us to provide customized solutions to customers and ensure the production of high-quality PCBs that meet their requirements.
Furthermore, our company is also capable of manufacturing Mixed Dielectric Rogers PCBs. Rogers PCBs are manufactured using Rogers high-frequency dielectric materials, which offer excellent high-frequency performance and thermal stability, making them suitable for various high-frequency applications such as communication equipment, radar systems, satellite communication, and more. Our engineering team has extensive experience and professional knowledge, allowing us to produce Mixed Dielectric Rogers PCBs that meet customers’ specifications and requirements.
In summary, as a specialized PCB manufacturing company, our company possesses the technology, equipment, and experience required to produce Extra Small Pitch PCBs and Mixed Dielectric Rogers PCBs. We are committed to meeting customers’ needs and providing high-quality, customized PCB solutions. We strive to grow and develop together with our customers by offering quality products and services.
What are the 7 Qualities of Good Customer Service?
Good customer service is essential for building strong relationships with customers and ensuring satisfaction. Here are seven qualities of good customer service:
- Empathy: Empathy involves understanding and sharing the feelings of customers. Good customer service representatives listen actively to customers’ concerns, acknowledge their emotions, and demonstrate understanding and compassion. Empathetic interactions can help build trust and rapport with customers.
- Responsiveness: Responsiveness refers to the ability to address customers’ needs promptly and efficiently. Good customer service involves timely responses to inquiries, requests, and complaints. Whether it’s answering phone calls, replying to emails, or resolving issues, being responsive demonstrates a commitment to customer satisfaction.
- Professionalism: Professionalism encompasses behaviors and attitudes that reflect competence, integrity, and respect for customers. Good customer service representatives maintain a courteous and polite demeanor, communicate clearly and effectively, and handle challenging situations calmly and professionally.
- Knowledgeability: Knowledgeability refers to having a deep understanding of products, services, policies, and processes. Good customer service representatives are well-trained and informed, allowing them to provide accurate information, answer questions confidently, and offer helpful recommendations or solutions.
- Flexibility: Flexibility involves adapting to the unique needs and preferences of each customer. Good customer service representatives are flexible and resourceful, willing to accommodate special requests, negotiate solutions, and go the extra mile to ensure customer satisfaction. Being flexible can help build loyalty and goodwill with customers.
- Problem-Solving Skills: Problem-solving skills are essential for resolving issues and addressing customer concerns effectively. Good customer service representatives are proactive in identifying and solving problems, taking ownership of issues, and finding creative solutions to meet customers’ needs. Effective problem-solving builds confidence and trust in the company’s ability to deliver quality service.
- Consistency: Consistency is key to maintaining high standards of customer service over time. Good customer service is consistent across all channels and interactions, ensuring that customers receive the same level of care and attention regardless of the situation or the representative they encounter. Consistency builds reliability and fosters positive customer experiences.
By embodying these qualities, businesses can provide exceptional customer service that not only meets but exceeds customer expectations, leading to increased satisfaction, loyalty, and positive word-of-mouth recommendations.
FAQs (Frequently Asked Questions)
What are Mixed Dielectric Rogers PCBs?
Mixed Dielectric Rogers PCBs are printed circuit boards (PCBs) that incorporate different types of dielectric materials from the Rogers Corporation. These PCBs are designed to offer optimized electrical performance and thermal management for high-frequency applications.
What are the advantages of Mixed Dielectric Rogers PCBs?
Mixed Dielectric Rogers PCBs offer several advantages, including excellent high-frequency performance, low signal loss, high thermal conductivity, and dimensional stability. These properties make them ideal for applications such as communication systems, radar systems, satellite communication, and more.
How are Mixed Dielectric Rogers PCBs different from standard PCBs?
Mixed Dielectric Rogers PCBs utilize specialized dielectric materials from the Rogers Corporation, which offer superior electrical properties compared to standard PCB materials. These materials are engineered specifically for high-frequency applications and provide enhanced signal integrity and thermal management.
What are the applications of Mixed Dielectric Rogers PCBs?
Mixed Dielectric Rogers PCBs are used in a wide range of high-frequency applications, including wireless communication devices, microwave equipment, RF (radio frequency) modules, aerospace and defense systems, and medical devices. They are suitable for any application that requires reliable high-frequency performance and thermal stability.
How do Mixed Dielectric Rogers PCBs improve signal integrity?
Mixed Dielectric Rogers PCBs feature low-loss dielectric materials that minimize signal attenuation and distortion, resulting in improved signal integrity and reliability. These PCBs also offer controlled impedance, reducing signal reflections and ensuring consistent performance across different frequencies.
What factors should be considered when designing Mixed Dielectric Rogers PCBs?
When designing Mixed Dielectric Rogers PCBs, factors such as dielectric constant (Dk), dissipation factor (Df), thermal conductivity, dimensional stability, and compatibility with manufacturing processes should be taken into account. Close collaboration with experienced PCB designers and manufacturers is essential to ensure optimal design and performance.
Can Mixed Dielectric Rogers PCBs be manufactured in different layer configurations?
Yes, Mixed Dielectric Rogers PCBs can be manufactured in various layer configurations, including single-sided, double-sided, and multilayer designs. The choice of layer configuration depends on the specific requirements of the application, such as signal routing, component density, and thermal management needs.
Are Mixed Dielectric Rogers PCBs more expensive than standard PCBs?
Mixed Dielectric Rogers PCBs may have a higher cost compared to standard PCBs due to the specialized materials and manufacturing processes involved. However, the performance benefits and reliability they offer often justify the investment, especially for high-frequency applications where signal integrity is critical.