Embedded IC PCB Manufacturing
Embedded IC PCB Manufacturing,Embedded IC PCBs, or Embedded Integrated Circuit Printed Circuit Boards, represent a cutting-edge approach to electronic circuit design. In these PCBs, integrated circuits (ICs) are directly embedded within the layers of the board, rather than being mounted on the surface. This innovative technique offers several advantages, including significant space savings, improved signal integrity, enhanced thermal management, and increased reliability. By embedding ICs within the PCB, the need for additional space for separate IC packages is eliminated, allowing for the creation of smaller and lighter electronic devices. Moreover, the shorter signal traces in Embedded IC PCBs minimize signal degradation and electromagnetic interference, leading to better overall performance. Additionally, the close proximity of ICs to heat-dissipating elements within the PCB facilitates more efficient heat dissipation, ensuring optimal functioning of the components. Overall, Embedded IC PCBs represent a sophisticated solution for applications where space, performance, and reliability are paramount.
What is an Embedded IC PCB?
An Embedded IC (Integrated Circuit) PCB (Printed Circuit Board) refers to a design approach where integrated circuits are directly embedded within the layers of a PCB rather than being mounted onto the surface of the board. This approach offers several advantages:
- Miniaturization: By embedding ICs within the PCB, the overall size of the electronic device can be reduced since there’s no need for additional space for separate IC packages.
- Improved Signal Integrity: Embedding ICs can reduce the length of signal traces, which minimizes signal degradation and interference, leading to better signal integrity.
- Reduced Interconnects: With ICs embedded within the PCB, the number of interconnects (e.g., wires, traces) required between the IC and the PCB is reduced, which can enhance reliability and reduce manufacturing complexity.
- Enhanced Thermal Management: Embedding ICs within the PCB can facilitate more efficient heat dissipation since the ICs can be in closer contact with heat-dissipating elements within the board.
- Protection: Embedded ICs may be less susceptible to physical damage or environmental factors since they are encased within the PCB layers, providing a degree of protection against external elements.
This approach is often used in applications where space, reliability, and performance are critical considerations, such as in portable electronic devices, medical devices, aerospace applications, and automotive electronics. However, it also poses challenges in terms of manufacturing complexity and repairability, as accessing and replacing embedded components can be more difficult compared to traditional surface-mounted components.
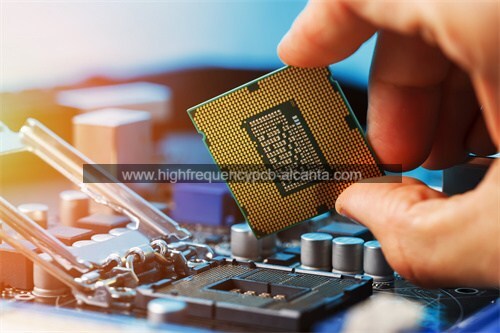
Embedded IC PCB Manufacturing
What are the Embedded IC PCB Design Guidelines?
Here are some general design guidelines for Embedded IC PCBs:
- Thermal Considerations: Since embedded ICs are enclosed within the PCB layers, thermal management is crucial. Ensure that there are adequate thermal vias and heat dissipation mechanisms within the PCB design to prevent overheating of the embedded ICs.
- Signal Integrity: Pay attention to signal routing to minimize signal degradation and electromagnetic interference. Keep signal traces short and use proper impedance control techniques. Consider using ground and power planes to reduce noise.
- Component Placement: Plan the placement of embedded ICs carefully to optimize signal paths and minimize signal distortion. Consider the proximity of other components that may affect signal integrity or thermal management.
- Manufacturability: Ensure that the PCB design is manufacturable with embedded ICs. Consider the capabilities of your PCB manufacturer and any special processes or materials required for embedding ICs.
- Reliability: Design the PCB to withstand environmental factors such as temperature fluctuations, humidity, and mechanical stress. Choose materials and construction techniques that enhance the reliability of the embedded IC PCB.
- Repairability and Accessibility: While embedding ICs can offer advantages, consider the implications for repair and maintenance. Ensure that embedded components can be accessed and replaced if necessary, even if it requires more complex disassembly.
- Testing and Debugging: Plan for testing and debugging of the embedded IC PCB. Consider test points and access to embedded components for troubleshooting during the development and production phases.
- Documentation: Document the design thoroughly, including the placement of embedded ICs, routing guidelines, thermal management strategies, and any special considerations for manufacturing or assembly.
By following these guidelines, you can design embedded IC PCBs that meet performance, reliability, and manufacturability requirements for your specific application. However, it’s essential to consider the unique challenges and constraints of embedding ICs within a PCB and adjust your design approach accordingly.
What is the Embedded IC PCB Fabrication Process?
The fabrication process for an Embedded IC PCB involves several steps, which may vary depending on the specific requirements of the design and the manufacturing capabilities of the PCB manufacturer. Here’s a general overview of the process:
- Design Preparation: The process begins with the preparation of the PCB design, including the placement of embedded ICs, routing of signal traces, creation of power and ground planes, and implementation of thermal management strategies. This design is typically done using PCB design software.
- Substrate Selection: Choose a suitable substrate material for the PCB based on factors such as thermal conductivity, dielectric properties, and mechanical strength. Common substrate materials include FR-4, FR-408, and Rogers laminates.
- Embedding Process: The embedding process involves placing the integrated circuits directly onto the substrate material before the layers of the PCB are laminated together. This can be done using techniques such as flip-chip bonding, wire bonding, or direct placement of bare die.
- Lamination: Once the ICs are in place, the layers of the PCB are laminated together using heat and pressure. This process typically involves stacking multiple layers of copper-clad substrate material and insulating layers, then applying heat and pressure to bond them together.
- Drilling and Plating: After lamination, holes are drilled through the PCB at specific locations for vias and component mounting. These holes are then plated with conductive material to provide electrical connections between different layers of the PCB.
- Copper Etching: Copper is typically applied to the surface of the PCB using a process called electroplating. The excess copper is then etched away using chemical etchants, leaving behind the desired copper traces and pads for soldering components.
- Component Assembly: Once the PCB has been fabricated, components such as resistors, capacitors, and connectors are soldered onto the surface using surface-mount technology (SMT) or through-hole technology (THT).
- Testing and Inspection: After assembly, the PCB undergoes testing to ensure that all components are functioning correctly and that there are no manufacturing defects. This may include electrical testing, visual inspection, and functional testing.
- Finishing: Finally, the PCB may undergo finishing processes such as coating with solder mask and silkscreen printing of component labels and markings.
- Packaging and Shipping: Once the PCBs have been fabricated and tested, they are packaged and shipped to the customer or assembly facility for integration into the final product.
Throughout the fabrication process, quality control measures are implemented to ensure that the finished PCB meets the required specifications for performance, reliability, and manufacturability. Collaboration between the PCB designer and the manufacturer is essential to address any design considerations specific to embedded ICs and to optimize the fabrication process accordingly.
How do you manufacture an Embedded IC PCB?
Manufacturing an Embedded IC PCB involves several specialized steps compared to traditional PCB manufacturing. Here’s a detailed overview of the process:
- Design Preparation:
– Develop a detailed PCB design including the placement of embedded ICs, routing of signal traces, and consideration of thermal management.
– Use PCB design software to create the design, ensuring adherence to manufacturing constraints and guidelines.
- Substrate Selection:
– Choose a suitable substrate material based on thermal conductivity, dielectric properties, and mechanical strength.
– Common substrate materials include FR-4, FR-408, and high-frequency laminates like Rogers materials.
- Embedding Process:
– Place integrated circuits directly onto the substrate material before laminating the layers together.
– Techniques for embedding ICs may include flip-chip bonding, wire bonding, or direct placement of bare die onto the substrate.
- Lamination:
– Stack multiple layers of copper-clad substrate material and insulating layers according to the PCB design.
– Apply heat and pressure to bond the layers together, forming a solid composite structure.
- Drilling and Plating:
– Drill holes through the PCB at specified locations for vias and component mounting.
– Plate the holes with conductive material to provide electrical connections between different layers.
- Copper Etching:
– Apply copper to the surface of the PCB using electroplating.
– Use chemical etchants to remove excess copper, leaving behind the desired traces and pads.
- Component Assembly:
– Solder components onto the surface of the PCB using surface-mount technology (SMT) or through-hole technology (THT).
– Carefully handle the embedded ICs to avoid damage during assembly.
- Testing and Inspection:
– Perform electrical testing to ensure that all components are functioning correctly and that there are no manufacturing defects.
– Conduct visual inspection and functional testing to verify the integrity of the PCB.
- Finishing:
– Apply solder mask to protect the copper traces and pads from oxidation and environmental damage.
– Print component labels and markings onto the PCB surface using silkscreen printing.
- Packaging and Shipping:
– Package the finished PCBs and prepare them for shipping to the customer or assembly facility.
– Ensure proper handling and packaging to prevent damage during transit.
Throughout the manufacturing process, quality control measures are implemented to ensure that the finished Embedded IC PCBs meet the required specifications for performance, reliability, and manufacturability. Collaboration between the PCB designer and the manufacturer is crucial to address any design considerations specific to embedded ICs and to optimize the manufacturing process accordingly.
How much should an Embedded IC PCB cost?
The cost of manufacturing an Embedded IC PCB can vary significantly depending on various factors, including:
- Complexity of the Design: The complexity of the PCB design, including the number of layers, size, and density of components, will influence the manufacturing cost. More complex designs with intricate routing and embedded ICs may require specialized manufacturing processes, resulting in higher costs.
- Materials Used: The choice of substrate material, copper thickness, and any special materials required for embedding ICs will impact the cost. High-quality materials or specialized laminates may increase manufacturing costs.
- Manufacturing Process: The specific manufacturing processes required for embedding ICs, such as flip-chip bonding or wire bonding, can affect the overall cost. Some processes may require additional equipment or expertise, contributing to higher manufacturing costs.
- Volume of Production: The volume of PCBs being produced will also affect the cost per unit. Larger production volumes typically result in lower per-unit costs due to economies of scale, while smaller production runs may incur higher costs per unit.
- Additional Services: Additional services such as testing, inspection, and finishing processes (e.g., solder mask application, silkscreen printing) will add to the overall cost of manufacturing.
- Supplier and Location: The choice of PCB manufacturer and their location can impact costs. Manufacturers with advanced capabilities or located in regions with higher labor costs may charge more for their services.
- Customization and Lead Time: Any customization requirements or expedited lead times may incur additional costs.
It’s essential to work closely with the PCB manufacturer to understand the specific requirements of your Embedded IC PCB design and obtain a detailed quote based on these factors. Prices can vary widely depending on the unique specifications of each project.
What is the Embedded IC PCB base material?
The choice of base material for an Embedded IC PCB depends on various factors, including thermal conductivity, dielectric properties, mechanical strength, and cost considerations. Here are some commonly used base materials for Embedded IC PCBs:
- FR-4: FR-4 (Flame Retardant 4) is the most widely used substrate material for PCBs due to its affordability, availability, and good overall performance. It offers decent thermal conductivity and dielectric properties suitable for many applications.
- FR-408: FR-408 is an enhanced version of FR-4 with improved electrical performance, particularly in terms of signal integrity and lower dielectric loss. It is often chosen for high-speed and high-frequency applications.
- Rogers Laminates: Rogers Corporation manufactures a range of high-performance laminates specifically designed for RF/microwave applications. These laminates offer excellent dielectric properties, low loss, and high thermal conductivity, making them suitable for demanding applications where signal integrity is critical.
- Polyimide: Polyimide substrates, such as Kapton, offer excellent thermal stability and mechanical flexibility, making them suitable for applications requiring a flexible PCB. They are commonly used in aerospace, automotive, and medical devices.
- Metal Core PCBs: Metal core PCBs, also known as MCPCBs, feature a metal core (typically aluminum or copper) for enhanced thermal conductivity. They are often used in applications requiring efficient heat dissipation, such as LED lighting and power electronics.
- Ceramic Substrates: Ceramic substrates, such as alumina (Al2O3) and aluminum nitride (AlN), offer high thermal conductivity and excellent electrical insulation properties. They are commonly used in high-power and high-temperature applications, such as power modules and RF amplifiers.
The choice of base material depends on the specific requirements of the Embedded IC PCB design, including thermal management, signal integrity, and mechanical considerations. It’s essential to select a base material that meets the performance requirements of the application while considering factors such as cost and manufacturability.
Which company makes Embedded IC PCBs?
Embedded IC PCBs are a technologically advanced PCB design widely used in various electronic devices such as portable devices, medical equipment, automotive electronics, communication devices, and more. Currently, many PCB manufacturing companies have the capability to produce Embedded IC PCBs, including well-known companies like Foxconn, OSEIA, Ericsson, and others.
As for our company, we have advanced PCB manufacturing equipment and a professional technical team capable of producing Embedded IC PCBs. We utilize the latest manufacturing technology and high-quality materials to ensure the stable and reliable performance of our products. With our experienced team, we can provide customized solutions tailored to the specific needs of our customers, ensuring that our products meet or exceed industry standards.
We are committed to providing excellent service and high-quality products to our customers. We understand the requirements for Embedded IC PCBs and continuously invest in technology and equipment to enhance our production capabilities and standards. Our goal is to become a trusted partner for our customers, providing reliable support for their business development.
If you require production services for Embedded IC PCBs, our company is the ideal choice. We will provide you with high-quality products and professional service, working closely with you to ensure the successful realization of your projects.
What are the 7 qualities of good customer service?
Good customer service is essential for building positive relationships with customers and fostering loyalty. Here are seven qualities that contribute to excellent customer service:
- Empathy: A good customer service representative empathizes with customers, understanding their needs, concerns, and emotions. They listen actively, demonstrate compassion, and show genuine concern for the customer’s situation.
- Patience: Patience is crucial in customer service, especially when dealing with frustrated or confused customers. A patient representative remains calm and composed, taking the time to address customer inquiries or resolve issues effectively.
- Communication Skills: Effective communication is key to providing good customer service. Representatives should be clear, concise, and articulate in their interactions with customers, whether it’s through verbal communication, written messages, or non-verbal cues.
- Product Knowledge: A good customer service representative has a deep understanding of the products or services offered by the company. They can answer customer questions accurately, provide relevant information, and offer helpful recommendations or solutions.
- Problem-Solving Skills: Customers often reach out to customer service when they encounter problems or issues. A skilled representative can identify and analyze problems, explore possible solutions, and take proactive steps to resolve issues in a timely manner.
- Positive Attitude: Maintaining a positive attitude is essential in customer service, even in challenging situations. A positive representative remains optimistic, approachable, and enthusiastic, which can help to alleviate customer concerns and leave a lasting impression.
- Reliability: Customers value reliability and consistency in their interactions with a company. A reliable customer service team delivers on promises, follows through with commitments, and ensures that customer needs are met promptly and effectively.
By embodying these qualities, companies can deliver exceptional customer service experiences that leave customers satisfied and loyal to the brand.
FAQs (Frequently Asked Questions)
What are Embedded IC PCBs?
Embedded IC PCBs refer to printed circuit boards where integrated circuits (ICs) are directly embedded within the layers of the PCB, rather than being mounted onto the surface of the board. This design approach offers advantages such as miniaturization, improved signal integrity, and enhanced thermal management.
What are the benefits of using Embedded IC PCBs?
Embedded IC PCBs offer several benefits, including reduced size and weight of electronic devices, improved signal integrity due to shorter signal traces, enhanced thermal management, and increased reliability due to fewer interconnects.
What applications are suitable for Embedded IC PCBs?
Embedded IC PCBs are suitable for various applications where space, performance, and reliability are critical factors. Common applications include portable electronic devices, medical equipment, aerospace systems, automotive electronics, and communication devices.
How are ICs embedded within the PCB layers?
ICs can be embedded within the PCB layers using various techniques, such as flip-chip bonding, wire bonding, or direct placement of bare die onto the substrate. Each technique has its advantages and is chosen based on factors like cost, performance, and manufacturability.
What materials are used for Embedded IC PCBs?
Common substrate materials for Embedded IC PCBs include FR-4, FR-408, Rogers laminates, polyimide, metal core PCBs, and ceramic substrates. The choice of material depends on factors such as thermal conductivity, dielectric properties, and mechanical strength.
Are Embedded IC PCBs more expensive to manufacture?
The cost of manufacturing Embedded IC PCBs can vary depending on factors such as design complexity, materials used, manufacturing processes, and volume of production. While they may incur additional costs compared to traditional PCBs, the benefits they offer often justify the investment.
What considerations should be taken into account when designing Embedded IC PCBs?
Design considerations for Embedded IC PCBs include thermal management, signal integrity, component placement, manufacturability, reliability, and repairability. Collaboration between the PCB designer and manufacturer is essential to address these considerations effectively.
Can existing PCB designs be converted into Embedded IC PCBs?
In some cases, existing PCB designs can be modified to incorporate embedded ICs. However, this may require redesigning certain aspects of the board to accommodate the embedded components and ensure proper performance and reliability.